Papers by José Angel Diosdado De la Peña

Proceedings of the 8th International Conference on Fluid Flow, Heat and Mass Transfer (FFHMT'21), 2021
Metal additive manufacturing (MAM) has gained interest due to its capability to produce metallic ... more Metal additive manufacturing (MAM) has gained interest due to its capability to produce metallic components with complex geometry by depositing consecutives layers of material that will shape said geometry through Direct Energy Deposition (DED) [1-3]. DED processes employ a high energy source, commonly a laser, to melt and laid metals [4]. Different DED technologies are commercially available such as Laser cladding (LC), Direct metal deposition (DMD), Laser engineer net shaping (LENS), Laser powder fusion (LPF), to name a few; these have been used to process various titanium, steel, nickel and aluminium alloys, among others [5]. It has been identified that DED processes are mainly influenced by the heat source power, scanning speed, feeding rate, and scanning strategy, and the exploration of these parameters with numerical simulation reduces experimental efforts [5, 6]. Numerical modeling by using finite element method (FEM) software has been used to explore the effect of the process parameters in the temperature distribution, either heating, cooling or both, as well as residual stresses, residual deformation and grain formation; commercial and selfdeveloped code was reported in literature with good agreement to reference data [2, 6-12]. FEM cases are also employed to validate new methods such as the modified inherent strain method and the invasion model in MAM [1, 13], as well as to evaluate diverse heat source models applicable to laser heating [14]. Based on this, a thermal-transient model in ANSYS® is proposed to reproduce a reference case [15]. The model considers a single-straight wall (12.6 x 38.1 mm x 3.0 mm) on a rectangular substrate (6.35 mm x 76.2 mm x 38.1 mm). The geometry is meshed with 20-nodes hexahedral elements, limited to a minimum element size of 0.75mm but forced to 62 divisions for the wall height. Sets of elements in each layer were created independently to allow for element birth/death commands and each set would be deposited as the heat source scans the geometry. A moving heating source is defined and travels at 8.47 mm/s, heating the top surface of the deposited elements; the parameters of the heat source were fitted to a laser with power of 425 W, 1.5 mm beam radius and process efficiency of 0.45. The initial temperature of the wall and substrate geometries and the surrounding temperature are defined as 30.5°C. Free convection boundary condition is assumed on every surface of the model and set to 10 W/mm 2 /°C. Wall and substrate are both assumed as Ti-6Al-4V with temperature dependent material properties [1-3, 15]. The proposed model agrees qualitatively with the reference case for the temperature profile from the first deposited layer down to the bottom of the substrate. Nonetheless, there are some significant differences quantitatively, while temperature at the surface and almost 0.1 mm below are only 5% different that the reference case and at the substrate bottom around 10%, the temperature in the midsection decreases rapidly and around 2.4 mm below the first layer the temperature difference is almost 50%. These results indicate that the proposed model behaves as expected, but improvements are required on the boundary condition and the heat source definition perhaps.
IEEE Access, 2020
This work studies the suitability of using 3D printed PLA wedges made through additive manufactur... more This work studies the suitability of using 3D printed PLA wedges made through additive manufacturing to propagate Lamb waves in plate structures instead of using rather more expensive commercial wedges. Ultrasonic waves were propagated in test samples printed at different densities to determine the optimal printing features of ultrasonic wedges based on signal attenuation. Results show barely any difference in Lamb wave filtered effect between 3D printed PLA and commercial wedges, which supports its usage as a suitable and cheaper option for Lamb wave propagation. INDEX TERMS Layered manufacturing, acoustic waves, ultrasonic transducers.

Polymers
Additive manufacturing is catalyzing a new class of volumetrically varying lattice structures in ... more Additive manufacturing is catalyzing a new class of volumetrically varying lattice structures in which the dynamic mechanical response can be tailored for a specific application. Simultaneously, a diversity of materials is now available as feedstock including elastomers, which provide high viscoelasticity and increased durability. The combined benefits of complex lattices coupled with elastomers is particularly appealing for anatomy-specific wearable applications such as in athletic or safety equipment. In this study, Siemens’ DARPA TRADES-funded design and geometry-generation software, Mithril, was leveraged to design vertically-graded and uniform lattices, the configurations of which offer varying degrees of stiffness. The designed lattices were fabricated in two elastomers using different additive manufacturing processes: (a) vat photopolymerization (with compliant SIL30 elastomer from Carbon) and (b) thermoplastic material extrusion (with Ultimaker™ TPU filament providing increa...
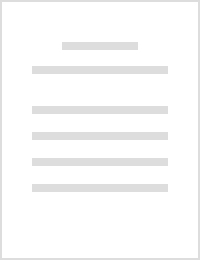
Journal of Manufacturing Processes, 2020
Abstract The present work focuses on the optimization of geometric parameters for Roll Hemming pr... more Abstract The present work focuses on the optimization of geometric parameters for Roll Hemming process, considering linear and nonlinear trajectories on two oblique planes (3D). Here, the optimization parameters of interest are the roller radius, pre-hemming angle, fillet radius, and fillet height. The main aim of this work is to improve the quality parameters of the 3D process: roll-in, roll-out and wrinkle. Furthermore, a comparison is presented between numerical (Finite Element Method) and experimental data with optimal and non-optimal parameters for four different rollers (10, 15, 20 and 25 mm in radius). The experimental testing was performed using a 6 degree° of freedom (DoF) NACHI® SRA210 industrial manipulator, with a self-developed end effector. The parameters estimated through simulations were used to build the four rollers for experimental testing. Multiple roll hemming tests were performed on several U-shaped aluminum 6011 sheets (31,194 mm2), with a thickness of 0.9 mm. After a detailed analysis of numerical and experimental data, it was observed that the optimum parameters for the roller with 15 mm in radius generated the best quality in hemmed samples.
Ingeniería Investigación y Tecnología, 2019
This work presents an analytical and numerical methodology that allows determining stress distrib... more This work presents an analytical and numerical methodology that allows determining stress distribution during the functioning of a screw conveyor utilized for conveying granular material. Different operating conditions were studied analytically and numerically. Initially, the reactions generated when the mechanism was fully braced with four supports along the longitudinal axis of the shaft were estimated. In addition, the system was analyzed with a typical fault in one of the central supports. The faults studied occur primarily due to the empirical modifications that companies make to these kinds of mechanisms and to the continuous operation of the conveyor system. Finally, a comparative analysis is presented between the analytical and the numerical results in order to validate the proposed methodology.

Polymers
This work provides a structural analysis of small-scale 3D-printed wind turbine ribs subjected to... more This work provides a structural analysis of small-scale 3D-printed wind turbine ribs subjected to compression. The ribs were manufactured according to NACA 23015 and NACA 633618 geometries, with polylactic acid (PLA) and polylactic acid with carbon fiber additives (CF-PLA). In addition, holes were manufactured into the sample bodies by either 3D printing or drilling for being compared with solid samples. The compression testing was performed by following the ASTM 695D standard, whereas the beginning and propagation of delamination were assessed with the ASTM 5528 standard. Experimental results revealed that 3D-printed built-in holes provided higher compression strength, hence higher structural efficiency, than the drilled samples. Significant improvement by adding carbon fiber additives into the PLA resin system in comparison to raw PLA was detected for at least one of the studied airfoil profiles. NACA geometries also represented a key parameter for avoiding stress concentration ar...

Energies
Linear Friction Welding (LFW) is a unique welding process which enables dissimilar materials to b... more Linear Friction Welding (LFW) is a unique welding process which enables dissimilar materials to be welded without filler material. In this study, bi-metallic Ti-64-CCM joints were manufactured utilizing LFW and subsequently analyzed. A coupled thermal-deformation model was created to accurately model both thermal and deformation profiles along the weld interface. Ti-64 and CCM stock were machined in accordance with ASTM standards for tensile testing. Temperature distribution of the two material surfaces were measured using an IR camera. Tensile testing was then performed to analyze weldability and bonding strength. A transient decoupled thermomechanical simulation model was generated to simulate the LFW process. The simulation model produced results within 5% error of both experimental results. The tensile testing results indicate that successful bonding of Ti-64 to CCM is possible for an oscillation amplitude of 2 mm under large forging pressure. The results also show that paramete...
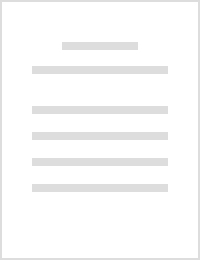
NED University Journal of Research
This paper proposes a numerical assessment of the after-test failure of a retractable jointed-cra... more This paper proposes a numerical assessment of the after-test failure of a retractable jointed-crane by using finite element analysis (FEA). The original design of the equipment involves a jointed section of coplanar arms and a telescopic section of collinear arms, which complies with the prevalent design standard, applicable for this kind of machinery in Mexico. A prototype of this design was built and was damaged during a beta test, presumably due to a crane misuse. The suggested numerical analysis was carried out in a FEA commercial software by assembling the component by kinematic pairs method, and considering dynamic loads and their resulting reactions at each element. The numerically obtained failure in the components was compared with the observed damage which indicated a difference less than ten percent in the permanent deformation results. Some modifications are recommended on the damaged components to increase the minimum safety factor, reaching up to sixty percent incremen...
International Journal of Materials and Product Technology, 2019
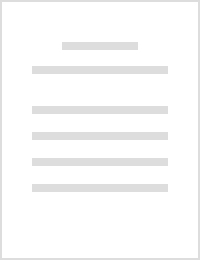
Volume 2: Advanced Manufacturing, 2018
A comparative experimental analysis of three common hemming processes used in the automotive indu... more A comparative experimental analysis of three common hemming processes used in the automotive industry is presented. These processes are die hemming, table hemming, and roll hemming. We aim to determine which one of the three processes provides the better quality hemming. The die hemming and table hemming used in this study were performed with custom made tooling and a 35 tonne hydraulic press. Similarly, roll hemming was performed using a custom made workbench with a three-degree of freedom system of rolls. The material used for testing was aluminum sheet (6011); three rolling directions were taken in account: 0°, 45°, and 90° for the manufacture of the samples. Hemming quality was determined from the geometric variables such as: lip high, pre-hemming angle, tool position, roll radius (roll hemming only). As a result, the comparison of roll in/out and wrinkle defects are reported and compared.
The behavior of composite materials reveals a material that is different from common heterogeneou... more The behavior of composite materials reveals a material that is different from common heterogeneous materials (isotropic: the same mechanical properties in all directions). A composite material is a combination of two or more materials that results in better properties than those of the individual components used alone. When a structure is made of a composite material, this effect should be considered in a mechanical study and a structural analysis. In this work be compared experimental results with theoretical results obtained by a numerical analysis (finite element). First we did a calculate the normal strain and the loads transmitted to specimens and then three different mechanical test simulations were made with simulation software ANSYS. Palabras Clave Materiales compuestos; Propiedades mecánicas; elemento finito.

Se plantea el modelado y manufactura de un prototipo didactico reductor de velocidad de un sistem... more Se plantea el modelado y manufactura de un prototipo didactico reductor de velocidad de un sistema de engranaje de tipo tren compuesto, con el uso de la manufactura aditiva a traves de una computadora y una impresora 3D Prusa i3 XL. Este Equipo aplica la tecnica de prototipado rapido modelado por deposicion fundida, la cual fabrica piezas disenadas en el ordenador a escala real por medio de extrusion de plastico por capas y el posicionamiento de una herramienta en tres dimensiones. En los resultados obtenidos se identificaron los factores imprevistos y condiciones necesarias para la respuesta del prototipo en lo concerniente al tiempo de impresion, paradas de emergencia, entre otras. Se describen algunas de las ventajas de usar este metodo de prototipado. La impresion que se muestra logro satisfacer las caracteristicas de movimiento determinado por la respuesta observada en el programa CAD. Se concluye con un comparativo de la animacion del modelo CAD y el movimiento obtenido en el ...
In this work the measurement of strain generated by impact loads is proposed. Some impact tests a... more In this work the measurement of strain generated by impact loads is proposed. Some impact tests are listed, from which the Hopkinson Split Pressure Bar (SHPB) is selected. We present the design of the equipment manufactured and used in this work. The materials and equipment needed to carry out the impact test are proposed, as well as how the strain measurement system should be installed. In the test performed, it is identified that the elements of the SHPB are similarly deformed when tested independently. Thus, there is evidence on the feasibility of measuring strain and that the system shown can be improved in future developments for impact load.
El siguiente trabajo evalua la factibilidad de medir microdeformaciones en intervalos de milisegu... more El siguiente trabajo evalua la factibilidad de medir microdeformaciones en intervalos de milisegundos. Las microdeformaciones ocurren cuando una masa choca con la celda de carga; para medir las deformaciones en cuestion de milisegundos se utilizo la tarjeta NI 9237 que tiene la capacidad de leer cincuenta mil muestras por segundo. Fue realizado un trabajo experimental que consistia en la ejecucion de siete pruebas con diferente rango de masa, los resultados obtenidos fueron satisfactorios porque se cumplio con los objetivos del proyecto.

Strength of Materials, 2017
Íàâåäåíî ÷èñåëüíèé ðîçðàõóíîê ï³äéîìíîãî êðàíà äëÿ ï³äíÿòòÿ ïåðñîíàëó íà îñíîâ³ ñê³í÷åííîåëåìåíòí... more Íàâåäåíî ÷èñåëüíèé ðîçðàõóíîê ï³äéîìíîãî êðàíà äëÿ ï³äíÿòòÿ ïåðñîíàëó íà îñíîâ³ ñê³í÷åííîåëåìåíòíîãî àíàë³çó, ï³äòâåðäaeåíèé åêñïåðèìåíòàëüíèìè äàíèìè ïî ñêëàäîâèõ éîãî êîìïîíåíòàõ. Îðèã³íàëüíà ìîäåëü ï³äéîìíîãî êðàíà âêëþ÷ຠç÷ëåíîâàí³ ñåêö³¿ êîìïëàíàðíèõ ñòð³ë ³ òåëåñêîï³÷íî¿ ñåêö³¿ êîë³íåàðíèõ ñòð³ë. Ìàêñèìàëüí³ íàâàíòàaeåííÿ òà ³õ âïëèâ íà ñêëàäîâ³ êîìïîíåíòè ï³äéîìíîãî êðàíà âèçíà÷åíî çã³äíî ç³ ñòàíäàðòîì ANSI/SIA 92.9, ùî âèêîðèñòîâóºòüñÿ äëÿ ìîäåëåé ï³äéîìíîãî êðàíà, ðîçïîâñþäaeåíèõ ³ êîìåðö³àë³çîâàíèõ ó Ìåêñèö³. Ñê³í÷åííîåëåìåíòíèé àíàë³ç áàçóºòüñÿ íà ìåòîä³ ñêëàäàííÿ ê³íåìàòè÷íèõ ïàð ç óðàõóâàííÿì äèíàì³÷íîãî íàâàíòàaeåííÿ òà ¿õ ðåçóëüòóþ÷î¿ ðåàêö³¿ íà êîaeåí åëåìåíò. Ìåõàí³÷í³ õàðàêòåðèñòèêè êîaeíîãî êîìïîíåíòà îö³íþþòüñÿ çà ïàðàìåòðîì ì³í³ìàëüíîãî ôàêòîðà áåçïåêè. Îäíàê ó òèõ êîìïîíåíòàõ, äå öåé ôàêòîð íå â³äïîâ³äຠñòàíäàðòó, ïðîïîíóºòüñÿ áåçë³÷ ìîäèô³êàö³é äëÿ ïåðåïðîåêòóâàííÿ äàíîãî êîìïîíåíòà. Ïðîâåäåíî äåòàëüíèé ñòðóêòóðíèé àíàë³ç çàïðîïîíîâàíî¿ ¿õ ìîäåðí³çàö³¿ é îòðèìàíî á³ëüø âèñîê³ ôàêòîðè áåçïåêè ïîð³âíÿíî ç îðèã³íàëüíîþ ìîäåëëþ. ×èñåëüí³ ðåçóëüòàòè çàïðîïîíîâàíî¿ ìîäåðí³çàö³¿ ï³äòâåðäaeåíî åêñïåðèìåíòàëüíèìè âèì³ðþâàííÿìè äåôîðìàö³é ïðè âèêîðèñòàíí³ òåíçîäàò÷èê³â, óñòàíîâëåíèõ íà ïðîòîòèï³ ï³äéîìíîãî êðàíà, ÿêèé âèãîòîâëåíî çã³äíî ³ç çàïðîïîíîâàíîþ ïåðåïðîåêòîâàíîþ ìîäåëëþ. Êëþ÷îâ³ ñëîâà: ï³äéîìíèé êðàí äëÿ ï³äíÿòòÿ ïåðñîíàëó, ñê³í÷åííîåëåìåíòíèé àíàë³ç, êîíñòðóêòèâíå ïåðåïðîåêòóâàííÿ, ìåòîä ñêëàäàííÿ ê³íåìàòè÷íèõ ïàð, àíàë³ç ³ç óðàõóâàííÿì äèíàì³÷íîãî íàâàíòàaeåííÿ. Commonly, the design of cranes is carried out in accordance with the manufacturer's experience or applying reverse engineering on existing designs . These development processes result in frequent repairs to the constituent components of the crane, without any numerical validation of their mechanical performance to any standard . In order to avoid such inconveniences, a variety of support technologies and analysis methods have been used on the design of this kind of machinery. Among the methods commonly used for the analysis of the constituent mechanisms of a crane, the synthesis of kinematics and its solution through numerical methods [5-9] and the analytic models for optimization are highlighted. Nevertheless, the most frequently used technologies include computer-aided design and engineering software (CAD and CAE), which are used for modeling a given three-dimensional geometry and its subsequent simulation under different working conditions . Some of these

Acta Universitaria, 2018
El engargolado es un proceso de manufactura que consiste en doblar una lámina metálica sobre si m... more El engargolado es un proceso de manufactura que consiste en doblar una lámina metálica sobre si misma o sobre otra. En este trabajo, se implementó el Ruido Magnético de Barkhausen (RMB) para identificar los esfuerzos residuales y su variación durante el proceso de engargolado por rodillo conducido. Inicialmente se detalla el proceso de inspección sobre especímenes de acero ASTM A36 engargolados. Para el estudio, se seleccionó el sensor S6519 para realizar mediciones en 5 puntos del borde de las piezas, obteniendo valores promedio de intensidad de RMB para cada etapa de engargolado. Se incluye una discusión de las variaciones identificadas en los resultados. Finalmente, se presenta un análisis de la ausencia o presencia de los esfuerzos residuales sobre la pieza y su efecto sobre el comportamiento magnético del material. Los resultados obtenidos permiten determinar la factibilidad de implementar el RMB para la inspección de piezas engargoladas en líneas de producción.

Metallurgical Research & Technology, 2018
The development and testing of protective coatings against corrosion for magnesium is reported. T... more The development and testing of protective coatings against corrosion for magnesium is reported. The coatings were based on the MgOx–TiOx composite and for their fabrication the reactive RF-sputtering technique in the co-deposition mode was employed. MgOx–TiOx coatings with chemical composition ranging from pure Mg oxides to pure Ti oxides, including its mixture, were obtained through the variation of the rate of the sputtering powers applied to the Mg and Ti targets. Characterization (XRD and XPS) showed changes in the crystalline structure according to the rate of the sputtering powers and confirmed the presence of MgO2, MgO, Ti2O3 and TiO2 in different proportions. Electrochemical polarization measurements (Tafel) made by employing the Hank's solution showed that both Vcorr and Icorr depend on the chemical composition of the coatings, having better corrosion resistance when the content of Ti oxides is higher. Results showed that corrosion resistance of Mg could be modulated by...
Experimental Techniques, 2018
sample is small, the propensity of low thiamine in female patients is intriguing and merits follo... more sample is small, the propensity of low thiamine in female patients is intriguing and merits follow up.
Materials Today: Proceedings, 2017
Abstract A new design for a biaxial tensile testing module or fixture was developed to characteri... more Abstract A new design for a biaxial tensile testing module or fixture was developed to characterize a sheet metal specimen with a level of anisotropy. The main advantage of this fixture is the capability to perform tests in standard testing machines, besides its low-cost and easy mounting of the test specimen in comparison with other fixtures. The design was developed according to different fixture from the literature. These were analyzed by using Finite Element Analysis (FEA) software in order to identify their advantages and disadvantages as well as their behavior under loading. To validate the results from the FEA, 3D printed models were carried out, and their kinetic functionality was observed. With the resulting data new design was proposed, this was analyzed using FEA and 3D printed in order to evaluate its functionality.
Surface and Coatings Technology, 2018
Station de Recherches de Virologie et d'immunologie (l.N.RA.), route de Thi verval -78850 Thiverv... more Station de Recherches de Virologie et d'immunologie (l.N.RA.), route de Thi verval -78850 Thiverval-Grignon (France).
Uploads
Papers by José Angel Diosdado De la Peña