Papers by Evren Ozbayoglu

Journal of Petroleum Exploration and Production Technology, 2016
Slurry transport has become a subject of interest in several industries, including oil and gas. T... more Slurry transport has become a subject of interest in several industries, including oil and gas. The importance of slurry/solid transport in the oil and gas industry is evident in areas of cuttings transport, sand transport and, lately, hydrates. There is therefore a great need to develop instrumentation capable of characterizing fluids with high solid content. Presence of solids in fluids makes the rheological characterization of these systems difficult. This is because available rheometers are designed with a narrow gap and cannot prevent solids from settling. The main aim of this paper is to present a step-by-step procedure of converting torque and shaft speed into viscosity information by applying the Couette analogy, equivalent diameter and inverse line concepts. The use of traditional impeller geometries such as cone and plate may be challenging due to their narrow gap and inability to prevent settling. Therefore, the use of nonconventional impeller geometry is imperative when dealing with settling slurries and suspensions. The most challenging task using complex geometry impeller is data interpretation especially when dealing with complex rheology fluids. In this work, an autoclave is transformed into a mixer-type viscometer by modifying its mixing, cooling and data acquisition systems. Mathematical models relating the measured torque to shear stress and the measured shaft speed to shear rate were developed and expressed in terms of the equivalent diameter. The shear rate and shear stress constants were expressed in terms of equivalent diameter and measureable parameters such as impeller speed and torque. The mixer-type viscometer was calibrated using four Newtonian and four Power-Law fluids to determine the rheological constants (equivalent diameter, shear rate and shear stress constants). The concept of inverse line was used to identify the laminar flow regime. The calibrated instrument was used to characterize two Power-Law fluids. This procedure can be extended to any rheological model. Methods developed in this work can be used to characterize fluids with high solid content. This is particularly important when dealing with complex rheology slurries such as those encountered in food processing, oil and gas and pharmaceuticals.
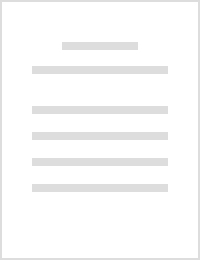
Time Series Data Analysis with Recurrent Neural Network for Early Kick Detection
Day 2 Tue, May 02, 2023
Fast and accurate kick detection during drilling operations is critical to ensure drilling safety... more Fast and accurate kick detection during drilling operations is critical to ensure drilling safety and reduce non-productive time. Over the years, the industry has taken various approaches to address this problem. However, due to the complexity of the influx process, the problem of slow detection speed and high false detection rate still exists. While many recent works of literature have attempted to solve the influx detection problem with machine learning algorithms, only a few of them have considered the time series information in real-time drilling data. Since there may be lags of unknown duration between different drilling parameters, a properly designed time series analysis model may be able to capture their relationships and make reasonable predictions. Recurrent Neural Network with long short-term memory (RNN-LSTM) architecture is a deep learning algorithm capable of making predictions based on historical time series data. Previous studies have shown that the RNN-LSTM algorith...
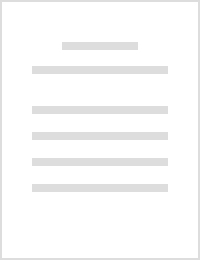
Gas Migration Model for Non-Newtonian Fluids Under Shut-In Well Conditions
Day 1 Tue, March 07, 2023
Addressing gas migration in a static mud column during the shut-in period is a major concern in P... more Addressing gas migration in a static mud column during the shut-in period is a major concern in Pressurized Mud Cap Drilling (PMCD). Significant discrepancies have been found between the field data and existing correlations for gas migration velocity, since the latter are based on either small-scale experiments or overly simplified assumptions, resulting in overly conservative estimations. To meet the Light Annular Mud (LAM) requirement for managing gas migration and to monitor the transient pressure experienced throughout the PMCD operation, an improved gas migration velocity model was developed by combining the equation of motion (bubble flow) and Taylor-bubble correlation (slug flow). In the bubble flow model, the effects of non-Newtonian fluid properties and drill pipe rotation are considered through a modified drag coefficient (CD) that incorporates the bubble Reynolds number (Reb) and dimensionless shear rate (Sr). The effect of bubble swarm is taken into account through a voi...
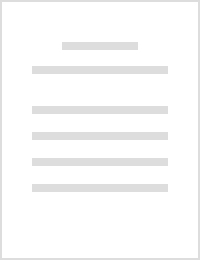
Design and Calculation of Process Parameters in Bullheading and Pressurized Mud Cap Drilling
Day 1 Tue, March 07, 2023
This study aims to provide the design and calculation method of key parameters in bullheading/PMC... more This study aims to provide the design and calculation method of key parameters in bullheading/PMCD operations. An improved gas migration velocity model in closed well conditions was developed based on the combination of the equation of motion (bubble flow) and Taylor bubble correlation (slug flow). A detailed derivation of the model can be found in our companion work (Liu et al. 2023). Experiments of Taylor bubble countercurrent behavior in an eccentric 6 in. × 4 in. annulus were conducted. Fluid rheology, annulus inclination, and internal pipe rotational speed were varied to provide a clearer understanding of Taylor bubble physics under non-Newtonian countercurrent flow and its implications for effectively managing upward gas migration that can occur in a wellbore during drilling operations in fractured or vugular rock formations. Computational Fluid Dynamics (CFD) simulations were performed to estimate the velocity of Taylor bubble in vertical annuli with downward fluid flow and a...
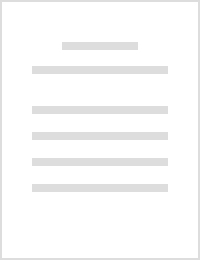
Cement Sheath Fatigue Failure Prediction by Support Vector Machine Based Model
Day 2 Wed, October 19, 2022
Zonal isolation is significant for safety operation of the well. Failure to keep wellbore integri... more Zonal isolation is significant for safety operation of the well. Failure to keep wellbore integrity can lead to sustained annulus pressure (SAP), and gas migration (GM), which may cause long non-productive time. Losing zonal isolation can cause severe environmental issue, which is irreversible and detrimental. However, cement sheath is exposed to temperature and pressure changes from the beginning of the drilling process to the whole life of the well. These cyclic changes can lead to fatigue failure of the cement. The objective of this study is to investigate the fatigue failure that caused by cyclic changing of temperature and pressure during life of the well. The scope of the study is based on the laboratory fatigue failure cases in previous literatures. Instead of using mechanical failure models, support vector machine (SVM) model is used to predict the fatigue failure of the cement sheath. The data is gathered from six papers of One-Petro, which includes 325 laboratory cement fa...
Experimental and Theoretical Studies on Taylor Bubbles Rising in Stagnant Non-Newtonian Fluids in Inclined Non-Concentric Annuli
International Journal of Multiphase Flow, 2021

Energies, 2021
An experimental investigation of single Taylor bubbles rising in stagnant and downward flowing no... more An experimental investigation of single Taylor bubbles rising in stagnant and downward flowing non-Newtonian fluids was carried out in an 80 ft long inclined pipe (4°, 15°, 30°, 45° from vertical) of 6 in. inner diameter. Water and four concentrations of bentonite–water mixtures were applied as the liquid phase, with Reynolds numbers in the range 118 < Re < 105,227 in countercurrent flow conditions. The velocity and length of Taylor bubbles were determined by differential pressure measurements. The experimental results indicate that for all fluids tested, the bubble velocity increases as the inclination angle increases, and decreases as liquid viscosity increases. The length of Taylor bubbles decreases as the downward flow liquid velocity and viscosity increase. The bubble velocity was found to be independent of the bubble length. A new drift velocity correlation that incorporates inclination angle and apparent viscosity was developed, which is applicable for non-Newtonian flu...
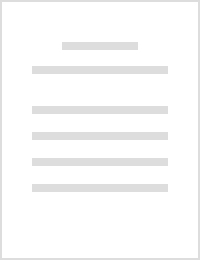
Mud/Cement Displacement in Vertical Eccentric Annuli
SPE Drilling & Completion, 2020
Summary A successful cement placement can provide zonal isolation and environmental safety. Effec... more Summary A successful cement placement can provide zonal isolation and environmental safety. Effective design of cement placement and mud removal affects all the stages of the wellbore life, from drilling ahead to production. Accurate predictions of fluid displacement in the wellbore are vital to design fluid properties and plan the cementing job. In this work, an analytical model is developed to simulate the displacement of fluids in eccentric annuli. This paper presents an analytical method for the solution of cement/mud displacement and evaluation of interfluid contamination during displacement in vertical eccentric annuli. This new approach starts by addressing the problem of single-fluid flow in eccentric annuli by analytically solving the governing transport equations for a flow inside an unwrapped annulus. The solution is then extended to a system of two fluids in a vertical annulus by adjusting the boundary conditions for displacement. The model is completed by adding the tim...

SPE Journal, 2019
Summary Loadings acting on a wellbore are more realistically regarded as dynamic rather than stat... more Summary Loadings acting on a wellbore are more realistically regarded as dynamic rather than static, and the wellbore response under dynamic loading can be different from that under static loading. Under dynamic loading, the inertia term should be considered and the changing rate of loading could induce a change in the mechanical properties of the wellbore, which might compromise wellbore stability and integrity. In this paper, a fully coupled poroelastodynamic model is proposed to study wellbore behavior. This model not only considers fully coupled deformation/diffusion effects, but also includes both solid and fluid inertia terms. The implicit finite-difference method was applied to solve the governing equations, which allows this model to handle all kinds of dynamic loading conditions. After modifying the existing code only slightly, our numerical solution can neglect inertia terms. The numerical results were validated by comparing them to the analytical solution with a simulated...

Energies, 2021
Effectively transporting drilled cuttings to the surface is a vital part of the well construction... more Effectively transporting drilled cuttings to the surface is a vital part of the well construction process. Usually, mechanistic models are used to estimate the cuttings concentration during drilling. Based on the results from these model, operational parameters are adjusted to mitigate any nonproductive time events such as pack-off or lost circulation. However, these models do not capture the underlying complex physics completely and frequently require updating the input parameters, which is usually performed manually. To address this, in this study, a data-driven modeling approach is taken and evaluated together with widely used mechanistic models. Artificial neural networks are selected after several trials. The experimental data collected at The University of Tulsa–Drilling Research Projects (in the last 40 years) are used to train and validate the model, which includes a wide range of wellbore and pipe sizes, inclinations, rate-of-penetration values, pipe rotation speeds, flow r...
Carbon nanotubes reinforced lightweight cement testing under tri-axial loading conditions
Journal of Petroleum Science and Engineering, 2018

Journal of Petroleum Science and Engineering, 2018
The low density enables lightweight cement to be an ideal candidate for petroleum drilling in dep... more The low density enables lightweight cement to be an ideal candidate for petroleum drilling in depleted formations. Lightweight cement is able to tolerate more deformation due to its high strain capacity. The major challenge, however, is its relatively low strength properties. Carbon nanotubes (CNTs) have been used in multiple industries to improve the strength, strain capacity, and durability of materials. In this study, the effect of CNTs on the mechanical properties of lightweight cement under triaxial loading conditions was analyzed. Two different lightweight cement systems, foam and microsphere cements, mixed with multi-walled carbon nanotubes at the concentration of 0.5%wt. were investigated and compared to conventional cement. Young's modulus, compressive strength, brittleness and strain capacity were measured under elevated confining pressures. Permeability and splitting tensile strength were calculated based on test
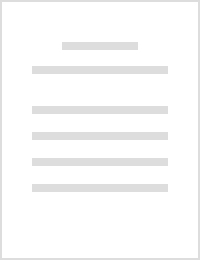
Fluid flow and heat transfer modeling in the event of lost circulation and its application in locating loss zones
Journal of Petroleum Science and Engineering, 2017
Abstract Lost circulation is one of the most persistent and costly drilling problems that drillin... more Abstract Lost circulation is one of the most persistent and costly drilling problems that drilling engineers have been struggling with for decades. The pinpointing of the zones of loss allows the treatments to be applied directly to the points of loss rather than to the entire open hole. This paper presents an approach to predict the location of single loss zone in a vertical well by interpreting the transient mud circulating temperature profiles altered by mud loss. The fluid flow and heat transfer numerical model in estimating the transient mud circulating temperature profiles during a lost circulation event was developed. The temperature profile in both the flow conduits (drillpipe and annulus) were modeled using mass and energy balances. The flow rate of drilling mud decreases in the annulus above the loss zone as part of the fluids lost into the fractures, which in turn alters the heat transmission status between the drillpipe, annulus, and near-wellbore formation. The wellbore is divided into two sections, which accounts for single loss zone. Case studies were performed and numerical solution results were presented and analyzed. According to the results, alterations induced by mud loss include: 1) Declines in both annular mud temperature and drillpipe mud temperature over time, and 2) Discontinuity in the first order derivative of annular mud temperature with respect to depth at the location of loss. By matching the simulated results with the distributed temperature measurements at different time stamps, the depth of the loss zone can be identified.
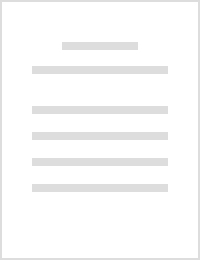
Fluid flow and heat transfer modeling in the event of lost circulation and its application in locating loss zones
Journal of Petroleum Science and Engineering, 2017
Abstract Lost circulation is one of the most persistent and costly drilling problems that drillin... more Abstract Lost circulation is one of the most persistent and costly drilling problems that drilling engineers have been struggling with for decades. The pinpointing of the zones of loss allows the treatments to be applied directly to the points of loss rather than to the entire open hole. This paper presents an approach to predict the location of single loss zone in a vertical well by interpreting the transient mud circulating temperature profiles altered by mud loss. The fluid flow and heat transfer numerical model in estimating the transient mud circulating temperature profiles during a lost circulation event was developed. The temperature profile in both the flow conduits (drillpipe and annulus) were modeled using mass and energy balances. The flow rate of drilling mud decreases in the annulus above the loss zone as part of the fluids lost into the fractures, which in turn alters the heat transmission status between the drillpipe, annulus, and near-wellbore formation. The wellbore is divided into two sections, which accounts for single loss zone. Case studies were performed and numerical solution results were presented and analyzed. According to the results, alterations induced by mud loss include: 1) Declines in both annular mud temperature and drillpipe mud temperature over time, and 2) Discontinuity in the first order derivative of annular mud temperature with respect to depth at the location of loss. By matching the simulated results with the distributed temperature measurements at different time stamps, the depth of the loss zone can be identified.
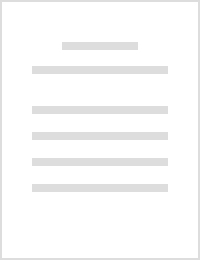
Estimation of Very-Difficult-to-Identify Data for Hole Cleaning, Cuttings Transport and Pressure Drop Estimation in Directional and Horizontal Drilling
IADC/SPE Asia Pacific Drilling Technology Conference and Exhibition, 2010
As the inclination of a wellbore increases, cuttings start having a tendency to accumulate in the... more As the inclination of a wellbore increases, cuttings start having a tendency to accumulate in the lower section of the wellbore, and develop a cuttings bed. This developed bed causes a reduction in the flow area, an increase in the friction between the drillstring and the wellbore, leading to an increase in torque, decrease in force transfer to the bit, and lose control on the bottomhole pressure. Finally, drilling rate decreases. Estimation of total concentration inside the wellbore is not an easy task. Moreover, moving cuttings and fluid dragging them to move have different relative velocities inside the wellbore, causing variations in pressure drop. Although there are many attempts to estimate the cuttings concentration and slip between the cuttings and the fluid using mechanistic models and empirical correlations, the performances are limited either with the strong assumptions made, or the experimental facility capabilities. This study aims to determine some of the very-difficul...

Journal of Energy and Power Engineering, 2016
Failure to manage and minimize lost circulation can greatly increase the cost of drilling and the... more Failure to manage and minimize lost circulation can greatly increase the cost of drilling and the risk of well abandonment. Many lost circulation remedial procedures are not working as planned because the locations of loss zones are incorrectly estimated. The lack of this critical piece of information prevents treatments from being applied directly to the points of losses and, thus, resulting in low efficiency and extended NPT (non-productive time). This paper presents an integrated method for identifying the locations of loss zones with continuous temperature measurement data enabled by drilling microchip technology. A transient thermal model in predicting the temperature profiles in the wellbore and formation during mud loss is developed as a forward calculation procedure of the loss zone mapping method. For a deep well with moderate to severe loss, there are significant changes in the mud circulating temperature profiles as mud loss persists. Certain characteristics of wellbore thermal behavior are evaluated and identified as good indicators of loss zones. Case studies are conducted to demonstrate the practical applications of the method in both onshore and offshore drilling applications. The results from these case studies are important in setting cement plugs, applying expandable tubular systems, and spotting LCM (lost circulation material) pills. Additional uses of this method include identifying highly permeable zones for reservoir or formation evaluation purposes. This method can be used as a routine monitoring process performed regularly without any interference of the drilling operations at the time.

Journal of Petroleum Exploration and Production Technology, 2016
Transportation of solids in form of slurries has become one of the most important unit operations... more Transportation of solids in form of slurries has become one of the most important unit operations in industries across several disciplines. In fact, the need is more pronounced in industries that are very important for human survival such as food processing, pharmaceuticals and energy (coal, oil and gas). A lot of work has been done in the past 30 years in understanding the factors affecting the deposition velocity of solids in slurries. Experimental observation and theoretical predictions pointed to mixture velocity and solid/fluid properties especially rheology of the resulting slurry to be the most important factors that dramatically affect particle motion and patterning. This paper presents a critical deposition velocity model and a ''stability flow map'' for complex rheology slurries. The critical deposition model utilizes a more robust generalized two-parameter rheology model to account for any given slurry rheology. The ''stability flow map'' demarcates the different flow patterns that may be observed at different mixture velocities and rheologies. On this map, the homogeneous slurries are predicted at low rheology and high mixture velocity, whereas heterogeneous slurries (with a concentration gradient) predicted at high rheology (yield stress effects). Sensitivity analysis was conducted on critical Reynolds number, particle density, carrier fluid density, generalized flow behavior index and pipe diameter. It was observed that increase in shear thinning behavior, particle density, pipe diameter and particle diameter led to a decrease in the laminar region and an increased unstable region. The model showed good performance when tested on glass and stainless steel beads test data available in open literature. Preliminary simulation with this map may help engineers select flowline size and carrier fluid rheology for a given type of solid particle. Keywords Rheology Á Particulate flow Á Slurry Á Flow regime Á Flow assurance Á Stability map List of symbols 1-C s Liquid volume fraction (-) C s Solid particle volume fraction (-) D Pipe inner diameter (m) d Particle diameter (micron) g Gravity (ms-2) K Viscosity consistency coefficient (mPa s N) n Flow behavior index/power law exponent (-) N Generalized flow behavior index (-) Re G Generalized Reynolds number (-) Re G,t Generalized transitional Reynolds number (-) S Ratio of solid density to carrier fluid density, q s =q f (-) V Velocity (ms-1) V c Critical deposition velocity (ms-1) V l Laminar deposition velocity (ms-1) V t Transitional deposition velocity (ms-1) x c Ratio of yield stress to wall shear stress, s y /s w (-) a Ratio of wall shear stress to surficial particle shear stress, s w /s p (-) g m Viscosity function (mPa s N) l Viscosity (mPa s) l B Plastic viscosity (mPa s) l m Mixture fluid viscosity (mPa s) l w Carrier fluid viscosity (mPa s) q Density (kg m-3
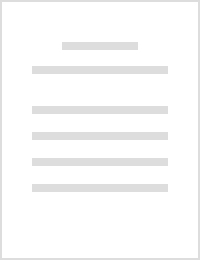
Frictional pressure loss of drilling fluids in a fully eccentric annulus
Journal of Natural Gas Science and Engineering, 2015
Abstract It is common practice when drilling oil and gas wells to assume that the drillstring is ... more Abstract It is common practice when drilling oil and gas wells to assume that the drillstring is placed concentrically in the annular space with either the open hole or previous casing strings in order to predict annular frictional pressure losses. The assumption of such a concentric annulus is, however, a considerable simplification that may not properly reflect the majority of drilling applications in the field. In fact, with an increasing number of deviated/horizontal and extended reach wells being drilled, a fully eccentric annulus is actually present in a large section of the wellbore. In this study, we apply experimental, analytical, and numerical approaches to investigate the impact of drillpipe eccentricity on the annular pressure loss while circulating non-Newtonian drilling fluids. The length of the experimental section of a flow loop was 27.74 m (91′) and it consisted of 0.0245 m (1″) steel drillpipe and 0.0571 m (2.25″) acrylic casing with the inner diameter of 0.0508 m (2″). Drillpipe was placed at the bottom of the casing, thereby simulating a fully eccentric annulus. Four Yield Power Law (YPL) drilling fluids were tested in this flow loop. Annular pressure loss for a wide range of laminar flow rates was recorded for each fluid. A numerical model based on a finite difference approach was developed to estimate the annular pressure loss. Subsequently, the experimental data was compared with the proposed model and also with several other widely used analytical and numerical approaches previously reported in the literature. The obtained results show that in the laminar flow regime, the annular frictional pressure loss in a fully eccentric annulus is considerably less than a concentric annulus, on occasions by less than 50%. In general, all the applied models under-estimated the effect of eccentricity on pressure loss. However, the novel proposed model showed the least discrepancy with the experimental data. Furthermore, it was found that the difference between the estimated and experimental results increases with increasing fluid yield stress. This suggests that models and/or correlations that are developed to correct for the eccentricity effect for fluids with negligible yield stress (for instance Power Law fluids) are not suitable to estimate the pressure loss for YPL fluids with elevated yield stress.
Real-Time Drilling Rate Of Penetration Performance Monitoring
Uploads
Papers by Evren Ozbayoglu