Papers by mohd amri sulaiman
Sekkei Kogaku, Shisutemu Bumon Koenkai koen ronbunshu, 2014
This paper study the effect of three Clifferent numcrical cutting parameters on surface roughncss... more This paper study the effect of three Clifferent numcrical cutting parameters on surface roughncss using during high speed machining . This experiment was carr 董 ed out to investigate the effbct machining parameters of AISI D2 tool steel us 孟 ng an insert end milL The experimont work p 且 an was carried out using Box −Behken techniques , a part of response surfaoe methodology (RSM) approach . The effect of variable milling cutting parameters were studied to evaluate their effects on surface roughness . In this study , the cutting speed , feed rate , depth ofcut and width of cut were in the range of lOO − 200 m 〆 min ,0. 1 − 0. 3 mm / tooth, 0. 2mm and 2. 0 − 8. O mm respectively . The effect of input factors that on the rcsponds wcrc identi 且ed by using me 跏 ofANOVA

This paper presents the tool life of the end milled Inconel 718, which is part of a material that... more This paper presents the tool life of the end milled Inconel 718, which is part of a material that is difficult to be machined. Previous researchers found that tool life in machining aged Inconel 718 is shorter compared with other materials. However, this observation required further investigation. Thus, a raw grade Inconel was proposed in this experiment. The experiments were performed using TiAlN-coated carbide. The studied milling parameters were the cutting speed, V c , from 90 to 150 m/min; feed rate, f z , from 0.15 to 0.25 mm/rev; depth of cut, a p , from 0.3 to 0.5 mm; and radial depth of cut, a e =1 mm. The application of the cutting fluid used in this experiment was a minimum quantity lubricant, which had the advantage of cooling effectiveness and low consumption of cutting fluid. The results showed that the feed rate, f z , was the primary factor controlling the tool life. The combination of V c =115 m/min, f z =0.15 mm/tooth, as well as a p =0.5 mm and a e =0.15 mm gave the longest tool life that served 95.38 min in operation.
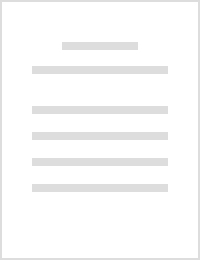
Lecture Notes in Mechanical Engineering, 2019
Flow analysis of three plate family injection mould using pin point gate that consist of four cav... more Flow analysis of three plate family injection mould using pin point gate that consist of four cavities was studied. The responses investigated were volumetric shrinkage, in-cavity residual stress and deflection. The experiment was conducted using Taguchi method with L9 orthogonal array. The parameters involved in this study were mould temperature, melt temperature, injection time and cooling time. The plastic specimens were designed using CATIA V5 and the drawing was imported to Autodesk Moldflow Insight (AMI) simulation software environment. The feed system such as sprue, runner, pin-point gate and cooling system of three plate mould were designed inside the simulation software. Flow analysis was conducted under cool + fill + pack + warp analysis. From the flow analysis using Taguchi method, the lowest volumetric shrinkage obtained is 7.907%. For other responses, the lowest in-cavity residual stress and deflection found are 27.69 MPa and 0.9203 mm respectively. After optimization using optimized parameters, the value of volumetric shrinkage is reduced about 2.88% to 7.678%. In-cavity residual stress is reduced about 0.14% to 27.41 MPa, while deflection of plastic parts is reduced about 0.30% to 0.9176 mm. From ANOVA results, it is found that melt temperature is the most important factors affecting volumetric shrinkage, in-cavity residual stress and deflection of plastic parts.
The Proceedings of Design & Systems Conference, 2014

The Proceedings of Design & Systems Conference, 2014
Minami ・ Jos 刎 ima 2 ・ 1, To shima ・ shi, To shima , 770 ・ 8506 Japan This papcr fbcuses on the i... more Minami ・ Jos 刎 ima 2 ・ 1, To shima ・ shi, To shima , 770 ・ 8506 Japan This papcr fbcuses on the investigation of cutting parameter on Kerf width using wiro electrical discharge machining (WEDM) ofInconel 718 . The effect ofthree numerical parameters , na ely the voltage gap, feed rate , and current are being studied in this experiment . Response sur 飴 ce me 出 odology was selected as designs of experiment (DOE) . ANOVA shows that feed rate significantly affects the size of Kerf width oompared to other pararneters . The optimization is done aftcr the experimcnt has bccn va [ idated by using the random parameter and optimized parameteL The error obtained when using random parameter is 5% and 4 % fbr血 e optimized parameteL The best combination ofoptimized parameter ofminimum Kerf width is fz ≡ 0. 86 mm 〆 min , V ≡ 41 V and I ≡ 7A in as to obtain a Kerfwidth of325 . 12 pm .

Journal of Materials Research, 2015
A carbide cutting tool is widely used in machining process due to its availability and being chea... more A carbide cutting tool is widely used in machining process due to its availability and being cheaper than a better performance cutting tool, such as cubic boron nitride. The carbide cutting tool also has substantial hardness and toughness that is suitable to be applied in intermittent cutting. This paper presents the case study of a wear mechanism experienced on the cutting edge of the coated and uncoated carbide tools in turning and milling processes. The wear mechanisms of carbide cutting tools were investigated in machining Inconel 718, titanium alloy Ti-6Al-4V extra-low interstitial, and aluminum metal matrix composite (AlSi/AlN MMC) at their high cutting speed regime. The tools failed primarily due to wear on the flank and rake faces. The failure mode of the carbide cutting tools was similar regardless of the machining operations and coating is believed to enhance the tool life, but once removed, the tool fails similar to that with the uncoated tool.
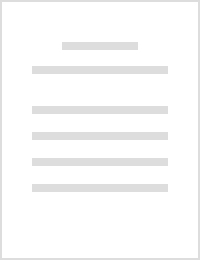
This paper presents the mould design analysis of casted natural fibre-metal matrix composites mat... more This paper presents the mould design analysis of casted natural fibre-metal matrix composites material. The natural fibre composites were introduced to the metal matrix as reinforced material for emerging new material. The pattern for sand casting was made from LM6 as metal matrix alloy, titanium carbide as reinforced material, and empty fruit bunch as natural fibre composites. Open mould was designed for producing the metal matrix composites and allowed the natural fibre composites introduce to metal matrix composite during the solidification stage. There were four design concepts were generated and simulated. The simulation shows the velocity, internal energy, pressure, turbulence kinetic energy; wall shear stress and cell Reynolds number lead the defect of casting product. Based on the design analysis, the mould design was proposed for casted natural fibre-metal matrix composites.
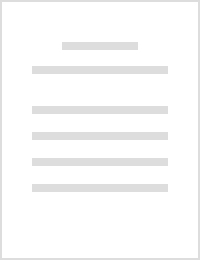
This research aims to promote environmentally friendly manufacturing areas without sacrificing pr... more This research aims to promote environmentally friendly manufacturing areas without sacrificing productivity, by the application of biodegradable minimum quantity lubricant (MQL) coolant in end-milling Inconel 718. This study is carried out by comparing a machining cost and method of lubrication applied in the end-milling process. High-speed cutting of Inconel 718 was performed, according to response surface methodology (RSM). Later, the optimization condition of the end mill cutting tool consumption and minimum quantity lubrication (MQL) are evaluated, based on the tool performance; i.e. machining time and material removed. In addition, the number of cutting tool edges is taken into consideration in the machining cost calculation. Machining performance at optimum condition is compared with other research, and the results show that the application of MQL and using ball-nose end mill are competitive, since this type of tool has a high index number which reduces the number of cutting tools required drastically, when compared to other types of cutting tools. The optimization of cutting parameters, with regard to criteria of the maximum material removed (9.03 cm3) and the lowest total cost ($23.55/100 cm3), gives the combination parameter that meets the requirement for green manufacturing; i.e. by reducing the usage of cutting tools and the amount of lubrication consumption.

This paper presents the tool life of the end milled Inconel 718, which is part of a material that... more This paper presents the tool life of the end milled Inconel 718, which is part of a material that is difficult to be machined. Previous researchers found that tool life in machining aged Inconel 718 is shorter compared with other materials. However, this observation required further investigation. Thus, a raw grade Inconel was proposed in this experiment. The experiments were performed using TiAlN-coated carbide. The studied milling parameters were the cutting speed, V c , from 90 to 150 m/min; feed rate, f z , from 0.15 to 0.25 mm/rev; depth of cut, a p , from 0.3 to 0.5 mm; and radial depth of cut, a e =1 mm. The application of the cutting fluid used in this experiment was a minimum quantity lubricant, which had the advantage of cooling effectiveness and low consumption of cutting fluid. The results showed that the feed rate, f z , was the primary factor controlling the tool life. The combination of V c =115 m/min, f z =0.15 mm/tooth, as well as a p =0.5 mm and a e =0.15 mm gave the longest tool life that served 95.38 min in operation.
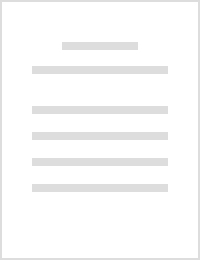
This paper investigates the effect of minimum quantity lubricant (MQL) on the surface roughness o... more This paper investigates the effect of minimum quantity lubricant (MQL) on the surface roughness of titanium alloy Ti-6Al-4V ELI when turning using uncoated tungsten carbide tool. The response surface method (RSM) design of experiment using Box-behnken was used to accomodate the turning experiment factors and levels. Turning parameters studied were cutting speed (100, 135, 170 m/min), feed rate (0.15, 0.2, 0.25 mm/rev) and depth of cut (0.6, 0.8, 1.0 mm). The results show that the feed rate was the most influence factor controlling the surface roughness produced. The feed rate (F) was found directly proportional with the surface roughness value (Ra) but inversely proportional to the cutting speed (Vc). MINITAB software was used to develop a surface roughness model, and the optimum condition was at 160 m/min of cutting speed, 0.18 mm/rev of feed rate and 1 mm of depth of cut. At the optimum condition low value of 1.54 μm surface roughness was obtained.

This paper investigates the effect of cutting speed, feed rate and depth of cut on the surface ro... more This paper investigates the effect of cutting speed, feed rate and depth of cut on the surface roughness of Inconel 718 when milled under minimum quantity lubrication. The response surface methodology (RSM) was employed in the experiment and a Box-Behnken design was used to determine the cause and effect of the relationship between the control variables and the response. The investigated milling parameters were cutting speed (100, 135 and 170 m/min), feed rate (0.15, 0.2 and 0.25 mm/rev) and depth of cut (0.6, 0.8 and 1.0 mm). The results showed that the interaction between the feed rate, f and the radial depth of cut, a , was the z e primary factor controlling surface roughness. The responses of various factors were plotted using a three-dimensional surface graph. The quadratic empirical models were developed with a 95% confidence level. The optimum condition required for minimum surface roughness include cutting speed of 136 m/min, feed rate of 0.1 mm/rev, axial depth of cut of 0.5 mm and radial depth of cut of 1.38 mm. With this optimum condition, a surface roughness of 0.117 µm was obtained.
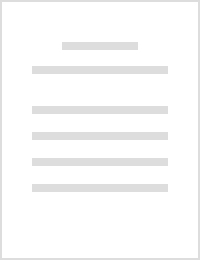
Inconel 718 is a material exhibiting characteristic that are able to maintain strength and integr... more Inconel 718 is a material exhibiting characteristic that are able to maintain strength and integrity at elevated temperatures, but it is well known as a material with poor machinability. This paper presents a study of the performance in high speed machining of TiAlN/AlCrN nanomultilayer PVD coated Inconel 718 with minimum lubrication. Investigations have been made into the effects of cutting speed, feed rate and depth of cut (DOC) on the tool life. A toolmakers microscope and a scanning electron microscope (SEM) were used to examine the tool wear and chemical attrition, respectively, on the cutting tool during machining. In the machining of aged Inconel 718, the cutting tool experienced attrition, abrasion and notch wear throughout the experiment. Notch wear was found to be the dominant failure mode during milling; this wear appeared severe when localized flank wear reached the critical zone. The influence of radial depth despite the cutting speed, well known as having the most significant effect on tool life, is also discussed.

JOURNAL OF MECHANICAL ENGINEERING AND SCIENCES, 2014
When polyetheretherketone is used in structural applications it generally undergoes additional ma... more When polyetheretherketone is used in structural applications it generally undergoes additional machining operations in order to form components. Machining PEEK can be a challenging task for manufacturers, however, especially when using a conventional cutting tool. This paper deals with the influence of a cutter's geometrical features when machining polyetheretherketones engineering plastic on their machining performances. Three categories of end mills were designed and fabricated with varying rake angles, clearance angles and helix angles to investigate effects on machining surface roughness and burr formation. From the investigations conducted, it is evident that end mill geometrical features (rake angle, clearance angle and helix angle) have significant effects on machining surface roughness and burr formation. Increasing the rake angle and helix angle value will improved the machining surface roughness, however, in the case of varying clearance angles, there are no significant results for the surface roughness produced. It could be observed, however, that a 12° clearance angle produced better surface roughness compared to other angles. The findings from the deliberately conducted experiments can be used for the development of high performance cutting tools, especially for machining polyetheretherketones engineering plastic material.
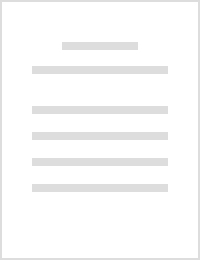
Applied Mechanics and Materials, 2014
The thin-walled component is mostly used in the aerospace industry. During machining the thin-wal... more The thin-walled component is mostly used in the aerospace industry. During machining the thin-walled components, deflection of wall occurs and causes the surface dimensional error. This paper focuses on the effect of end mill helix angle on the surface dimensional error and surface roughness when machining thin wall structure. End mills uncoated carbide were fabricated with a difference helix angle which are 25°, 30°, 35°, 40° and 45°. The results show, helix angle 35° produce smaller surface dimensional error and smoothest followed by 40°, 45°, 30° and 25°. The smaller helix angle provided high cutting force that causes more surface dimensional error due to chatter and reduction of contact time when then end mill engage with the workpiece material. Results from this research help to guide the machinist to machine thin-wall component with the right cutting tool.
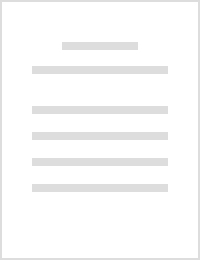
Advanced Materials Research, 2010
The purpose of this study is to investigate the effect of turning parameters on the surface integ... more The purpose of this study is to investigate the effect of turning parameters on the surface integrity of Inconel 718. The turning parameters studied were cutting speed of 90, 120, 150 m/min, feed rate of 0.15, 0.25, 0.25mm/rev and depth of cut of 0.3, 0.4, 0.5 mm under minimum quantity lubricant (MQL) using coated carbide tool. surface response methodology (RSM) design of experiment using Box-Behnken approach has been employed consisting of various combination of turning parameters Surface roughness, surface topography, microstructure and the micro hardness of the machined surface were studied after the machining process. Feed rate was found to be the most significant parameter affecting the surface roughness. The optimum parameter was obtained with Ra equal to 0.243 µm at cutting speed of 150 m/min, feed rate of 0.25 mm/rev and depth of cut of 0.3mm. A mathematical model for surface roughness was developed using Response Surface Methodology. The effect of turning parameters and fac...

JOURNAL OF MECHANICAL ENGINEERING AND SCIENCES, 2014
Metal matrix composite (MMC) is a combination of two or more materials in a metal matrix, and is ... more Metal matrix composite (MMC) is a combination of two or more materials in a metal matrix, and is being widely used nowadays due to its excellent properties. This paper presents the surface integrity of LM6 aluminum MMC when machined with two different cutting tools; high speed steel (HSS) and uncoated carbide. The experiments were carried out with a constant cutting speed, feed rate and axial depth of cut, but differ in the radial depth of cut under dry cutting conditions. Results indicated that machining LM6 with uncoated carbide cutting tools provides a lower surface roughness and fine surface profile compared to HSS cutting tools, due to its edge stability. A lower radial depth of cut produced a fine surface finish and vice versa. Most of the machined surface was dominated by the feed mark effect due to path overlap from the cutting tool. This study is expected to provide a database of suitable cutting tools and cutting parameters for machining MMC based materials.

Applied Mechanics and Materials, 2014
The effect of maleated polypropylene (MAPP) as binder on the mechanical properties of kenaf fibre... more The effect of maleated polypropylene (MAPP) as binder on the mechanical properties of kenaf fibre/polypropylene (KF/PP) composites is studied. Ratios between kenaf fibre and PP having 10:90, 30:70 and 50:50 in weight ratio were selected. Further, MAPP having 1, 3 and 5 percent in percentage of weight ratio was mixed in KF/PP composites. Hot press machine was used to produce tensile test samples of KF/PP composites. The mechanical properties that are tensile strength, tensile modulus and elongation at break of KF-PP composites were obtained from tensile test result. It is found that the tensile strength and tensile modulus increase with increasing the kenaf fibre loading and higher percentage of MAPP. Further, the elongation at break for KF/PP composites shows lower result when increasing of kenaf fibre loading. However, when percentage of MAPP added in KF/PP composites increases, the elongation at break increased slightly. Thus, result shows that kenaf fibre/PP composites with binde...

Applied Mechanics and Materials, 2014
Carbon Fiber Reinforced Plastics (CFRP) exhibit superior characteristics such as high specific st... more Carbon Fiber Reinforced Plastics (CFRP) exhibit superior characteristics such as high specific strength, high specific modulus, fatigue strength and endurance. During the manufacture of components from CFRP, it is usually necessary to carry out a post-machining step. Generally, after curing process, the parts will be trimmed in order to meet the required tolerances. Due to the heterogeneous composition and anisotropy of composite materials, machining procedures can damage the material in ways that directly affect its mechanical properties. Currently a costly try and error approach is employed to determine the optimal process conditions. Thus, this study focused on numerical modelling of machining CFRP composites using cross-nick router. A set of machining tests were performed in order to validate the accuracy of the model. Good agreement between simulation and experimental results show the validity of the model in handling real-field problems. The proposed numerical modeling techniq...
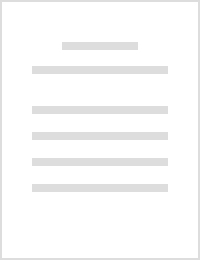
Advanced Materials Research, 2014
The optimization of processing parameters on warpage of polypropylene (PP) in the application of ... more The optimization of processing parameters on warpage of polypropylene (PP) in the application of injection moulding machine was studied. The appropriate parameters were adjusted to reduce the warpage defect on the tensile test specimen of dumbbell. The type of injection moulding machine used in this research is Arburg 420C 800-250C. Four parameters that have been investigated; injection pressure, clamping pressure, back pressure and holding pressure. A concept of design of experiment (DOE) has been applied using Taguchi method to determine the suitable parameters. To measure the warpage of the dumbbell, digital height gauge was used to measure the flatness of the part surface. According the analysis of variance (ANOVA), the most significant factor that effect the warpage was holding pressure by 57.82%, followed with back pressure by 25.75%, clamping pressure by 16.27% and injection pressure by 0.16%. It is found that the optimum parameters setting that have been obtained were inject...

Wear, 2013
This study is an investigation of tool wear using a ball-type end mill. The primary purpose of th... more This study is an investigation of tool wear using a ball-type end mill. The primary purpose of this work is to examine the tool life and wear mechanism when machining Inconel 718 with a physical vapor deposition (PVD)-coated carbide tool and varying the cutting parameters. Notch wear and flaking near the depth of the cut zone were the predominant types of tool failure for the four round cutting tools and were initiated by pitting caused by the repetitive cyclic load. The major factor identified was the large radial depth of the cut. Further examination indicated that the dominant wear was located near the depth of the cut line. On the flank face, smooth and coarse wear types, from abrasion and attrition, occurred at low and high cutting speeds, respectively. A maximum temperature of 521 1C was recorded, which is less than the critical temperature of 650 1C for Inconel 718. A mathematical model was developed to predict the location of the pitting, which was responsible for notching and flaking. This location could then be used to calculate the location associated with the maximum load exerted during the cutting. The error between the predictive model of pitting and the actual notching/flaking was less than 6%.
Uploads
Papers by mohd amri sulaiman