Papers by Ernesto Solanes

IFAC Proceedings Volumes, 1993
This work p;c~cnls. nu robust cuntrol IDcthodolon ror hybrid positiuntrofl:c control. Ttlc I.:ont... more This work p;c~cnls. nu robust cuntrol IDcthodolon ror hybrid positiuntrofl:c control. Ttlc I.:ontrol input of tnis IIcthodu JOR' consists of I nnnlincar lnd a linear part. The DUDlincar control part lIi'fes I DCW coordinate system. Using this coordinate system. robot dynamics is dcrouplcd and input !paf:Cs ale difidcd into 1.0 orlhogoul spaces of pflsition lOd force control. The lincar (oalrul pan illPro,cs robuslness properties of the DonlinClr h1bri4 coulro! sr.bc.e. A ..odel feedback control sctlc.e is lPplied to the linear put of positi(Jn [Dolral aDd jnt~RrlJ r.oDlrol is used ill ttlc lioClr part or rorr.c control. The robustness properties ur the nonlinear robust hybrid cODtrol llRnrilh. &rc d.caoastrlled. throulItI si.vluiOD or I (fJJ1strlincd two degrees or rrecdoll robot llIuipulator. lef words: Robot lIIa.nipu.lator; hyhrid pnsitllJn.!rorr.e (oftlral; robut coatrol;.udcl reed.blck caatrul where I/> (q) is the m by I vector rcpresenting the constraints. i. e.• I/> (q)'" [I/> ".... I/>~]"'.), denotes the mby 1 vector of reaction forces. Let 7/ he the new coordi na te system. where 7/ is the n by I vector denoted by 7/ c.

Applied Sciences
This work proposes a new interface for the teleoperation of mobile robots based on virtual realit... more This work proposes a new interface for the teleoperation of mobile robots based on virtual reality that allows a natural and intuitive interaction and cooperation between the human and the robot, which is useful for many situations, such as inspection tasks, the mapping of complex environments, etc. Contrary to previous works, the proposed interface does not seek the realism of the virtual environment but provides all the minimum necessary elements that allow the user to carry out the teleoperation task in a more natural and intuitive way. The teleoperation is carried out in such a way that the human user and the mobile robot cooperate in a synergistic way to properly accomplish the task: the user guides the robot through the environment in order to benefit from the intelligence and adaptability of the human, whereas the robot is able to automatically avoid collisions with the objects in the environment in order to benefit from its fast response. The latter is carried out using the ...

Libro de Actas IN-RED 2020: VI Congreso de Innovación Edicativa y Docencia en Red, 2020
Es bien sabido que las modalidades pedagógicas que fomentan que el alumno sea protagonista de su ... more Es bien sabido que las modalidades pedagógicas que fomentan que el alumno sea protagonista de su proceso de aprendizaje son más eficaces. Sin embargo, el arraigo hacia la modalidad de clase magistral hace que tanto alumnos como profesores sean muy reacios a cambiar drásticamente a un modelo activo, sobretodo en asignaturas con alto grado teórico y de primeros cursos de grado. Es por ello que este artículo propone combinar la modalidad de clase magistral con metodologías activas de cara a mejorar el proceso de enseñanza-aprendizaje en alumnos de primeros cursos de grado. El artículo describe con detalle un caso de aplicación en la asignatura de Electrónica y Automática de segundo curso de Grado de Ingeniería Mecánica. Además, se muestra una comparativa de los resultados académicos obtenidos con el mismo profesorado en los cursos 2018/2019, con la modalidad tradicional de clase magistral, y el 2019/2020, con la propuesta de este trabajo. Por último, el artículo expone la opinión que h...
CIRP Journal of Manufacturing Science and Technology, 2020
This research develops a new mixed reality-based worker interface for industrial camera 3D positi... more This research develops a new mixed reality-based worker interface for industrial camera 3D positioning, which is intuitive and easy to manage, in order to enhance the worker safety, ergonomics and productivity. An experimental prototype to be used in the car body quality control is developed in the paper. The benefits and drawbacks of the proposed interface are discussed along the paper and sustained through several usability tests conducted with users familiar and not-familiar with mixed reality devices. Furthermore, the feasibility of the proposed approach is demonstrated by tests made in an industrial environment with skilled workers from Alfatec Sistemas company.

Advances in Autonomous Robotics, 2012
This paper introduces a novel concept of dual-rate non-linear high order holds, based on artifici... more This paper introduces a novel concept of dual-rate non-linear high order holds, based on artificial neuronal networks, in order to improve control, robustness and stability margin of non-linear processes. The main idea is that artificial networks provide accurate inter-sampling data estimation in dual-rate systems, allowing controlling the process at the fastest possible rate. In addition to this, the paper compares the performance with other approaches taking into account the ideal but non-feasible closed loop at high frequency. For that purpose, the paper considers metrics such as mean square error and settling time to measure the overall performance. The proposed dual-rate non-linear holds have been tested in both, simulation and real processes, and particularly, in an industrial robot within an image-based visual servoing application. The new approach improves with respect to the conventional single-rate behavior and showing higher stability margin than conventional dual-rate holds.
Applied Sciences
Teleoperation of bimanual robots is being used to carry out complex tasks such as surgeries in me... more Teleoperation of bimanual robots is being used to carry out complex tasks such as surgeries in medicine. Despite the technological advances, current interfaces are not natural to the users, who spend long periods of time in learning how to use these interfaces. In order to mitigate this issue, this work proposes a novel augmented reality-based interface for teleoperating bimanual robots. The proposed interface is more natural to the user and reduces the interface learning process. A full description of the proposed interface is detailed in the paper, whereas its effectiveness is shown experimentally using two industrial robot manipulators. Moreover, the drawbacks and limitations of the classic teleoperation interface using joysticks are analyzed in order to highlight the benefits of the proposed augmented reality-based interface approach.
International Journal of Computer Integrated Manufacturing, 2021

Journal on Multimodal User Interfaces, 2022
High dexterity is required in tasks in which there is contact between objects, such as surface co... more High dexterity is required in tasks in which there is contact between objects, such as surface conditioning (wiping, polishing, scuffing, sanding, etc.), specially when the location of the objects involved is unknown or highly inaccurate because they are moving, like a car body in automotive industry lines. These applications require the human adaptability and the robot accuracy. However, sharing the same workspace is not possible in most cases due to safety issues. Hence, a multi-modal teleoperation system combining haptics and an inertial motion capture system is introduced in this work. The human operator gets the sense of touch thanks to haptic feedback, whereas using the motion capture device allows more naturalistic movements. Visual feedback assistance is also introduced to enhance immersion. A Baxter dual-arm robot is used to offer more flexibility and manoeuvrability, allowing to perform two independent operations simultaneously. Several tests have been carried out to asses...

Electronics, 2021
In recent years, the use of technology in the museum context has changed radically. It has switch... more In recent years, the use of technology in the museum context has changed radically. It has switched from the display of information to offering emotive, immersive, and rich experiences with heritage. Virtual interactive media have the potential to put museums back into a relevant place in our increasingly digital society. The emergence of augmented-reality glasses offers the possibility to test and implement new methodologies compatible with this aim. However, most of the first examples developed in recent years did not take advantage of the possibilities of this new medium. This paper presents a novel methodology for producing mixed-reality applications for museums and heritage sites, with an intuitive, immersive, and natural way of operating. An experimental prototype designed for the archaeological museum of the Almoina is shown in the paper to demonstrate the benefits of the proposed system and methodology of production. In addition, the paper shows the results of several tests.

2018 IEEE/RSJ International Conference on Intelligent Robots and Systems (IROS), 2018
This paper presents a control architecture readily suitable for surface treatment tasks such as p... more This paper presents a control architecture readily suitable for surface treatment tasks such as polishing, grinding, finishing or deburring as carried out by a human operator, with the added benefit of accuracy, recurrence and physical strength as administered by a robotic manipulator partner. The shared strategy effectively couples the human operator propioceptive abilities and fine skills through his interactions with the autonomous physical agent. The novel proposed control scheme is based on task prioritization and a non-conventional sliding mode control, which is considered to benefit from its inherent robustness and low computational cost. The system relies on two force sensors, one located between the last link of the robot and the surface treatment tool, and the other located in some place of the robot end-effector: the former is used to suitably accomplish the conditioning task, while the latter is used by the operator to manually guide the robotic tool. When the operator chooses to cease guiding the tool, the robot motion safely switches back to an automatic reference tracking. The paper presents the theories for the novel collaborative controller, whilst its effectiveness for robotic surface treatment is substantiated by experimental results using a redundant 7R manipulator and a mock-up conditioning tool.

IEEE Access, 2020
This article develops a human-robot cooperation to carry out treatments such as sanding, polishin... more This article develops a human-robot cooperation to carry out treatments such as sanding, polishing, etc. on the surface of a known rigid object. For this purpose, a vision system is considered to get the object location to ensure not only the perpendicularity of the robot tool to the object surface but also a smooth approach of the tool to the surface. In order to add flexibility, the proposal includes the simultaneous combination of automatic and manual modes of operation. Thus, the human user can guide the robot tool to treat arbitrary areas (manual mode) and, when the operator releases the tool, the robot goes into the automatic mode to treat prior established areas. The method uses a task prioritization framework and three types of controllers: an admittance controller for the tool guidance; a hybrid controller to modify the tool orientation and, in the automatic mode, the tool position; and a sliding mode controller to limit the velocity at which the tool approaches the object surface. The applicability and efficacy of the proposed method is demonstrated experimentally using a conventional 6R robot arm.
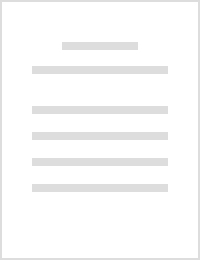
International Journal of Systems Science, 2021
This work develops a method to perform surface treatment tasks using a bimanual robotic system, i... more This work develops a method to perform surface treatment tasks using a bimanual robotic system, i.e. two robot arms cooperatively performing the task. In particular, one robot arm holds the workpiece while the other robot arm has the treatment tool attached to its end-effector. Moreover, the human user teleoperates all the six coordinates of the former robot arm and two coordinates of the latter robot arm, i.e. the teleoperator can move the treatment tool on the plane given by the workpiece surface. Furthermore, a force sensor attached to the treatment tool is used to automatically attain the desired pressure between the tool and the workpiece and to automatically keep the tool orientation orthogonal to the workpiece surface. In addition, to assist the human user during the teleoperation, several constraints are defined for both robot arms in order to avoid exceeding the allowed workspace, e.g. to avoid collisions with other objects in the environment. The theory used in this work to develop the bimanual robot control relies on sliding mode control and task prioritisation. Finally, the feasibility and effectiveness of the method are shown through experimental results using two robot arms.
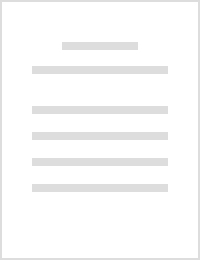
Computers & Industrial Engineering, 2021
Abstract Surface treatment operations, such as sanding, deburring, finishing, grinding, polishing... more Abstract Surface treatment operations, such as sanding, deburring, finishing, grinding, polishing, etc. are progressively becoming more automated using robotic systems. However, previous research in this field used a completely automatic operation of the robot system or considered a low degree of human-robot interaction. Therefore, to overcome this issue, this work develops a truly synergistic cooperation between the human operator and the robot system to get the best from both. In particular, in the application developed in this work the human operator provides flexibility, guiding the tool of the robot system to treat arbitrary regions of the workpiece surface; while the robot system provides strength, accuracy and security, not only holding the tool and keeping the right tool orientation, but also guaranteeing a smooth approach to the workpiece and confining the tool within the allowed area close to the workpiece. Moreover, to add more flexibility to the proposed method, when the user is not guiding the robot tool, a robot automatic operation is activated to perform the treatment in prior established regions. Furthermore, a camera network is used to get a global view of the robot workspace in order to obtain the workpiece location accurately and in real-time. The effectiveness of the proposed approach is shown with several experiments using a 6R robotic arm.

Journal of Manufacturing Systems, 2021
There are some industrial tasks that are still mainly performed manually by human workers due to ... more There are some industrial tasks that are still mainly performed manually by human workers due to their complexity, which is the case of surface treatment operations (such as sanding, deburring, finishing, grinding, polishing, etc.) used to repair defects. This work develops an advanced teleoperation and control system for industrial robots in order to assist the human operator to perform the mentioned tasks. On the one hand, the controlled robotic system provides strength and accuracy, holding the tool, keeping the right tool orientation and guaranteeing a smooth approach to the workpiece. On the other hand, the advanced teleoperation provides security and comfort to the user when performing the task. In particular, the proposed teleoperation uses augmented virtuality (i.e., a virtual world that includes non-modeled real-world data) and haptic feedback to provide the user an immersive virtual experience when remotely teleoperating the tool of the robot system to treat arbitrary regions of the workpiece surface. The method is illustrated with a car body surface treatment operation, although it can be easily extended to other surface treatment applications or even to other industrial tasks where the human operator may benefit from robotic assistance. The effectiveness of the proposed approach is shown with several experiments using a 6R robotic arm.

The International Journal of Advanced Manufacturing Technology, 2020
This research develops a novel teleoperation for robot manipulators based on augmented reality. T... more This research develops a novel teleoperation for robot manipulators based on augmented reality. The proposed interface is equipped with full capabilities in order to replace the classical teach pendant of the robot for carrying out teleoperation tasks. The proposed interface is based on an augmented reality headset for projecting computer-generated graphics onto the real environment and a gamepad to interact with the computer-generated graphics and provide robot commands. In order to demonstrate the benefits of the proposed method, several usability tests were conducted using a 6R industrial robot manipulator in order to compare the proposed interface and the conventional teach pendant interface for teleoperation tasks. In particular, the results of these usability tests show that the proposed approach is more intuitive, ergonomic and easy-to-use. Furthermore, the comparison results also show that the proposed method clearly improves the velocity of the teleoperation task, regardless of the user's previous experience in robotics and augmented reality technology.
International Journal of Robust and Nonlinear Control, 2017
An approach based on sliding mode is proposed in this work for reference tracking in robot visual... more An approach based on sliding mode is proposed in this work for reference tracking in robot visual servoing. In particular, 2 sliding mode controls are obtained depending on whether joint accelerations or joint jerks are considered as the discontinuous control action. Both sliding mode controls are extensively compared in a 3D-simulated environment with their equivalent well-known continuous controls, which can be found in the literature, to highlight their similarities and differences. The main advantages of the proposed method are smoothness, robustness, and low computational cost. The applicability and robustness of the proposed approach are substantiated by experimental results using a conventional 6R industrial manipulator (KUKA KR 6 R900 sixx [AGILUS]) for positioning and tracking tasks.
ISA Transactions, 2018
This work presents a human-robot closely collaborative solution to cooperatively perform surface ... more This work presents a human-robot closely collaborative solution to cooperatively perform surface treatment tasks such as polishing, grinding, deburring, etc. The method considers two force sensors attached to the manipulator end-effector and tool: one sensor is used to properly accomplish the surface treatment task, while the second one is used by the operator to guide the robot tool. The proposed scheme is based on task priority and adaptive non-conventional sliding mode control. The applicability of the proposed approach is substantiated by experimental results using a redundant 7R manipulator: the Sawyer cobot.

Control Engineering Practice, 2018
This work presents a hybrid position/force control of robots aimed at handling applications using... more This work presents a hybrid position/force control of robots aimed at handling applications using multi-task and sliding mode ideas. The proposed robot control is based on a novel adaptive non-conventional sliding mode control used to robustly satisfy a set of inequality constraints defined to accomplish the cooperative transport task. In particular, these constraints are used to guarantee the reference parameters imposed by the task (e.g., keeping the load at a desired orientation) and to guide the robot using the human operator's forces detected by a force sensor located at the robot tool. Another feature of the proposal is the multi-layered nature of the strategy, where a set of four tasks are defined with different priorities. The effectiveness of the proposed adaptive non-conventional sliding mode control is illustrated by simulation results. Furthermore, the applicability and feasibility of the proposed robot control for transport tasks are substantiated by experimental results using a redundant 7R manipulator.

Journal of Manufacturing Systems, 2019
In recent years, the quality control of car body surfaces production lines have been put in the c... more In recent years, the quality control of car body surfaces production lines have been put in the context of Industry 4.0. The emergence of automatic defect detection systems have helped to standardize the brand quality and gather information about all quality control tasks performed by workers. However, current worker interfaces used to indicate the location and other characteristics of the defects found by these systems have overcome the ergonomics of workers and increased their stress at work. This paper presents a novel mixed reality-based user interface for quality control inspection which is more intuitive, in order to improve the ergonomics of workers, reduce their stress at work and improve the productivity of current quality control production lines. An experimental prototype is shown in the paper in order to demonstrate the benefits of the proposed interface. In addition, the paper shows the results of several usability tests that compare the proposed mixed reality-based user interface with current interfaces used in important factories such as Mercedes-Benz, analyzing the benefits and drawbacks of each interface.

Robotics and Autonomous Systems, 2018
This work presents an approach based on multi-task, non-conventional sliding mode control and adm... more This work presents an approach based on multi-task, non-conventional sliding mode control and admittance control for human-robot collaboration aimed at handling applications using force feedback. The proposed robot controller is based on three tasks with different priority levels in order to cooperatively perform the safe transportation of an object with a human operator. In particular, a high-priority task is developed using non-conventional sliding mode control to guarantee safe reference parameters imposed by the task, e.g., keeping a load at a desired orientation (to prevent spill out in the case of liquids, or to reduce undue stresses that may compromise fragile items). Moreover, a second task based on a hybrid admittance control algorithm is used for the human operator to guide the robot by means of a force sensor located at the robot tool. Finally, a third low-priority task is considered for redundant robots in order to use the remaining degrees of freedom of the robot to achieve a pre-set secondary goal (e.g., singularity avoidance, remaining close to a homing configuration for increased safety, etc.) by means of the gradient projection method. The main advantages of the proposed method are robustness and low computational cost. The applicability and effectiveness of the proposed approach is substantiated by experimental results using a redundant 7R manipulator: the Sawyer collaborative robot.
Uploads
Papers by Ernesto Solanes