Papers by Francesca LIONETTO
Journal of Marine Science and Engineering, Apr 19, 2021
This article is an open access article distributed under the terms and conditions of the Creative... more This article is an open access article distributed under the terms and conditions of the Creative Commons Attribution (CC BY

Polymer Composites, Jan 17, 2015
The engineering aspects, which are associated with the development of nanocomposites, involve in ... more The engineering aspects, which are associated with the development of nanocomposites, involve in either final properties or processability of nanocomposites. Both are affected by the distribution of nanofiller in the matrix and by the aspect ratio of the nanofiller. A nanofilled thermosetting resin can be exploited as a matrix for continuous fibers when the alignment of a high aspect ratio nanofiller is achieved, and in this case, a hierarchical composite is obtained. In this study, a new procedure for the alignment of nanofillers in a thermosetting matrix is proposed. The two-step approach is based on (i) the alignment of nanofillers (carbon nanotubes, graphene, etc.) in thermoplastic fibers by a fiber spinning process and (ii) the use of these nanocomposite fibers as a carrier to bring aligned nanofillers into a reactive thermosetting resin. These fibers, soluble in the thermosetting resin, release the nanofillers orientated according to the direction in which fibers are positioned, even after the curing of the matrix. The proof of concept is demonstrated by producing melt spun polyethylene terephtalate (PETg) fibers filled with graphene nanoplatelets (GNP) and multiwall carbon nanotubes (MWCNT) with a very high filler content (up to 10 wt%) in view of producing a hierarchical composite.
Journal of Materials Processing Technology, Sep 1, 2017
Hybrid ultrasonic spot welding of aluminum to carbon fiber reinforced epoxy composites.
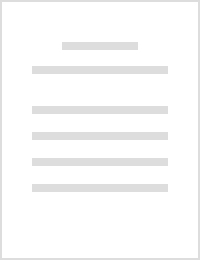
Smart Materials and Structures, Jan 29, 2021
Carbon fiber-epoxy thin laminates, manufactured adopting a [0/90] non-symmetric lay-up, are chara... more Carbon fiber-epoxy thin laminates, manufactured adopting a [0/90] non-symmetric lay-up, are characterized by two stable curved shapes, so being bistable. These composite thin laminates are attracting great interest for their potential application as novel morphing structures and power harvesting devices in many engineering fields. The curvature changes of rectangular bistable plates were monitored at room temperature by a laser scanner system over a time span of 10 d. These changes were ascribed to the relaxation of thermal stresses over time. Anisotropic stress relaxation behavior was then studied looking at the matrix dominated properties, such as the transverse modulus in accelerated high temperature experiments and the moisture absorption. Then, a simple viscoelastic model was proposed together with a finite element analysis of the distortion arising from laminate cooling at the end of high temperature cure process. The experimental and numerical results showed that the transverse elastic modulus and the hygroscopic effect are the main factors affecting the shape relaxation of bistable laminates.
Polymers, Jul 16, 2021
This article is an open access article distributed under the terms and conditions of the Creative... more This article is an open access article distributed under the terms and conditions of the Creative Commons Attribution (CC BY
Composites Part B-engineering, Jul 1, 2018
The mechanical and electrochemical behavior of ultrasonic spot welded hybrid joints, made of AA57... more The mechanical and electrochemical behavior of ultrasonic spot welded hybrid joints, made of AA5754 aluminum and carbon fiber reinforced epoxy with a co-cured thermoplastic surface layer, was studied. The effect of the welding parameters (energy and force) and the thickness of a thermoplastic film, applied as an upper ply in the composite lay-up, on the development of adhesion strength, was investigated. The best mechanical results were obtained when the welding parameters were able to achieve a large bonding area of mechanical interlocking between naked carbon fibers and aluminum and a better load distribution. The electrochemical results excluded the possibility of galvanic corrosion between aluminum and composite adherends thanks to the insulating action provided by the thermoplastic film.
Polymers, Jan 31, 2023
This article is an open access article distributed under the terms and conditions of the Creative... more This article is an open access article distributed under the terms and conditions of the Creative Commons Attribution (CC BY

Polymer Engineering and Science, Mar 27, 2017
During autoclave processing of composites for high performance applications, it is mandatory to l... more During autoclave processing of composites for high performance applications, it is mandatory to limit the porosities, which mainly depend on the hydrostatic pressure in the resin. This pressure, which is not constant during heating being affected either by resin flow either by elastic stress in the fiber stack, can be significantly different from the autoclave pressure. Modeling of resin flow and stress in the fiber stack is a key issue for prediction of the resin hydrostatic pressure, which can be related to void development. Also, the viscosity of the thermosetting matrix is a relevant parameter since it is not constant but evolves during curing going through a minimum and then increasing to an infinite value at gel point. In this work, a viscoelastic model is adopted to calculate the evolution of resin pressure during an autoclave cycle up to gelation, accounting for viscosity and degree of reaction changes. Therefore, the model includes a kinetic and rheological model whose input parameters have been experimentally determined by Differential Scanning Calorimetry and rheological analysis. The predicted resin pressure for three case studies associated to different composite and bleeder thicknesses and reinforcement materials have been discussed.
Energies, Nov 26, 2021
This article is an open access article distributed under the terms and conditions of the Creative... more This article is an open access article distributed under the terms and conditions of the Creative Commons Attribution (CC BY
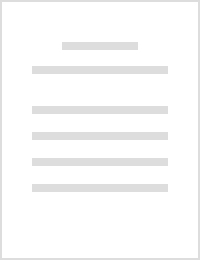
Polymer Engineering and Science, Jun 1, 2009
The aim of this work is to study the mechanical behavior of flexible polyurethane foams used in c... more The aim of this work is to study the mechanical behavior of flexible polyurethane foams used in cushioning applications. In particular, the differences between slow recovery (SR) and fast recovery (FR) foams are highlighted. To characterize the flexible polyurethane foams, creep and hysteresis tests were performed at different strain rate, stress levels, and temperatures. Significant differences were observed between the SR and FR foams, particularly in terms of residual deformation after unloading, hysteresis area, and creep behavior at different stress levels. Creep compliance at different stress levels was compared with a Voigt‐Kelvin model. Stress–strain loading curves were compared with a phenomenological model originally modified to account for the strain rate dependence. In both cases, it is possible to show that the main differences observed in the behavior of the foams are due to the different relaxation and recovery times of the foams. POLYM. ENG. SCI., 2009. © 2009 Society of Plastics Engineers

Composites Part B: Engineering
Porosity represents a critical issue in composite manufacturing often leading to parts rejection.... more Porosity represents a critical issue in composite manufacturing often leading to parts rejection. The aim of this work was to develop a multiphysic model capable to predict the conditions leading to porosity generated by water in composite parts processed by autoclave lamination. The developed model does not aim to assess the void growth phenomenon, as other models in the literature, but it enables the prediction of the thermodynamic conditions for water-generated porosity, where they could occur and how to prevent their presence by suitably modifying the process parameters. The potential of this multiphysic model was proved on epoxy matrix carbon fiber reinforced laminates cured after their exposition to a moist environment. The model was also applied to modify the curing cycle suggested by the prepreg provider in order to avoid favorable conditions for porosity development.
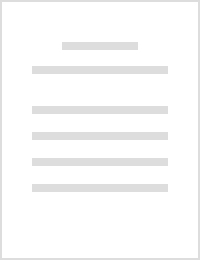
Stress relaxation behavior of unidirectional AS4/8852 carbon/epoxy composites at high temperature... more Stress relaxation behavior of unidirectional AS4/8852 carbon/epoxy composites at high temperatures has been investigated. Specimens with an off axis angle of 90° and ±45° have been exposed to constant strain and high temperature. The mechanical results have been modeled by Standard Linear Solid model. The obtained parameters have been implemented in a finite element (FEM) model able to predict the residual stresses in carbon fiber reinforced composites, both in the elastic and in the viscoelastic field.Stress relaxation behavior of unidirectional AS4/8852 carbon/epoxy composites at high temperatures has been investigated. Specimens with an off axis angle of 90° and ±45° have been exposed to constant strain and high temperature. The mechanical results have been modeled by Standard Linear Solid model. The obtained parameters have been implemented in a finite element (FEM) model able to predict the residual stresses in carbon fiber reinforced composites, both in the elastic and in the ...

Composites Part A: Applied Science and Manufacturing, 2021
In this work the architectural anisotropy of short fiber reinforced polymers (SFRPs) has been cha... more In this work the architectural anisotropy of short fiber reinforced polymers (SFRPs) has been characterized using X-ray computed micro-tomography (micro-CT) with four different morphometric methods: Mean Intercept Length (MIL), Volume Orientation (VO), Star Length Distribution (SLD) and Star Volume Distribution (SVD). The fabric tensor obtained from micro-CT analysis provided information on the fiber orientation, indicating that fibers were partially aligned in the injection direction. The fiber length and orientation obtained from optical microscopy and from the morphometric analysis in 3D, respectively, has been used to determine the mechanical properties of the composite sample, using a model based on micro and macromechanics. This approach leads to the prediction of the elastic constants of the component for any possible composite morphology resulting from injection, representing a key need for the design of SFRP components.
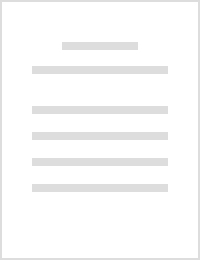
Construction and Building Materials, 2019
Abstract Heritage buildings worldwide are primarily masonry construction. Over the centuries, the... more Abstract Heritage buildings worldwide are primarily masonry construction. Over the centuries, these structures have demonstrated a high vulnerability in seismic events. The seismic protection and retrofitting of these historical structures require an effective structural solution, without compromise, cover or loss of architectural and artistic value. For these scenarios, the use of Fiber Reinforced Polymers (FRPs) is discouraged since removability of the intervention is often a mandatory requirement, and the polymeric adhesives bond the fiber to the masonry substrate, eliminating the possibility of preserving the underlying material during a replacement operation. In FRP-strengthening, the force transfer from the substrate to the FRP occurs by means of bond stresses. However, in the case of column confinement, while full bond is nevertheless developed through the adhesive, it is not necessary for the effectiveness of the confinement. Instead, the confining pressure is applied by the FRP when transversal dilatation of the column is mobilized. Thus, with the exception of the overlapping regions, an FRP retrofit for column confinement works due to a contact phenomenon instead of bond. In this context, new FRP-confinement techniques, based on contact rather than adhesion, can be developed. This paper presents research on fully-reversible contact-based techniques for FRP-confinement. Three different techniques were developed and demonstrated by the authors. Each technique was experimentally evaluated through compression tests of small-scale limestone cylinders. The reversibility of each technique was verified through comparison of the substrates before the FRP-confinement and after the testing. The effectiveness of each technique was evaluated by comparing the compressive strength and the deformability with those obtained for unconfined specimens. The concepts show promise as effective and reversible strengthening techniques.

Materials & Design, 2017
Continuous induction welding for thermoplastic matrix composites requires an accurate modeling of... more Continuous induction welding for thermoplastic matrix composites requires an accurate modeling of the temperature distribution in the laminates, depending on the electromagnetic field. In this work, a transient three-dimensional finite element (FE) model was developed in order to study the heat transfer phenomena, and melting and crystallization in the welding area during the continuous induction welding of carbon fiber reinforced Poly(ether ether ketone) (CF/PEEK) laminates. The multiphysics problem was solved by coupling electromagnetic and heat transfer equations considering matrix melting and crystallization behavior. The model was able to simulate the continuous process along a linear path at a constant speed. The computed temperatures were in good agreement with experimental measurements. Several numerical simulation were used for selecting a processing window as a function of coil speed and current, for the welding of CF/PEEK joints. The results of welding experiments were evaluated by single lap shear tests and morphology characterization of the welded interfaces and fracture surfaces.
A finite element (FE) model able to evaluate both the evolution of resin flow, degree of reaction... more A finite element (FE) model able to evaluate both the evolution of resin flow, degree of reaction and void formation during autoclave cure cycles was developed. The model was implemented using a commercial epoxy matrix widely used in aeronautic field. The FE model also included a kinetic and rheological model whose input parameters were experimentally determined by Differential Scanning Calorimetry and rheological analysis. The FE model was able to predict the evolution of degree of reaction with very good agreement with the experimental data. Moreover, the predicted resin losses were lower than 3% of the overall composite resin content.
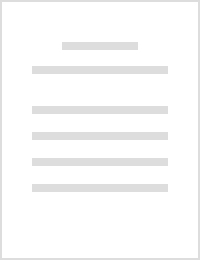
The work is addressed to investigating the potentiality of calcination of organic-inorganic (O-I)... more The work is addressed to investigating the potentiality of calcination of organic-inorganic (O-I) hybrids as a feasible approach to produce silica particles, at mild temperature conditions and with tailored morphology. Two different innovative hybrid systems were obtained through sol-gel process with a siloxane content ranging from 6 to 26wt%. The two O-I hybrids differed for i) the organic matrix (methacrylic or epoxy), ii) its crosslinking mechanism (photopolymerization for methacrylic systems or thermal cold-cure for epoxy systems) and iii) the rate ratio between sol-gel and crosslinking reactions. Different characterization techniques were used to understand the effect of composition and curing method on the morphology of the silica obtained from O-I hybrids after calcination in air. The results confirm the morphology and properties of silica particles in terms of surface and porosity may be tailored over a wide range by varying the composition and nature of organic and inorganic precursors of hybrids.

Composites Part A: Applied Science and Manufacturing, 2016
Ultrasonic propagation was used to provide heat and pressure in order to perform impregnation and... more Ultrasonic propagation was used to provide heat and pressure in order to perform impregnation and consolidation during production of thermoplastic matrix composites. For this purpose, a new experimental setup , integrating a laboratory filament winding machine with a horn and a compaction roller, was developed. The heat transfer phenomena occurring during continuous impregnation and consolidation were simulated solving by finite element (FE) analysis the energy balance equations in 2D accounting for the heat generated by ultrasonic waves, the melting characteristics of the matrix and the movement of the thermoplastic commingled roving. The temperature distribution in the composite, predicted by the numerical simulations, was validated by temperature measurements during the production of E-glass/polypropylene cylinders, with the optimized parameters obtained by the FE analysis. The ultrasonic consolidated composite cylinders were characterized by low void content and a shear modulus comparable with that obtained by the micromechanical analysis.

Polymers
Liquid composite molding (LCM) is a class of fast and cheap processes suitable for the fabricatio... more Liquid composite molding (LCM) is a class of fast and cheap processes suitable for the fabrication of large parts with good geometrical and mechanical properties. One of the main steps in an LCM process is represented by the filling stage, during which a reinforcing fiber preform is impregnated with a low-viscosity resin. Darcy’s permeability is the key property for the filling stage, not usually available and depending on several factors. Permeability is also essential in computational modeling to reduce costly trial-and-error procedures during composite manufacturing. This review aims to present the most used and recent methods for permeability measurement. Several solutions, introduced to monitor resin flow within the preform and to calculate the in-plane and out-of-plane permeability, will be presented. Finally, the new trends toward reliable methods based mainly on non-invasive and possibly integrated sensors will be described.
Journal of Polymers and the Environment
Uploads
Papers by Francesca LIONETTO