Papers by Stefania Bruschi
International Journal of Material Forming, 2008
International Journal of Material Forming, 2009
The paper presents the mechanical characterization of the magnesium alloy AZ31B at elevated tempe... more The paper presents the mechanical characterization of the magnesium alloy AZ31B at elevated temperature carried out on a dedicated uni-axial tensile set-up. The samples are heated in-situ through induction heating and their deformation recorded in-line through the Aramis™ system. Results from the tests in terms of plastic properties, anisotropic coefficients, hardening and strain rate sensitivity exponents are presented and commented.

International Journal of Material Forming, 2009
A number of scientists are currently involved in Incremental Forming investigation, in order to b... more A number of scientists are currently involved in Incremental Forming investigation, in order to better understand the process and to extend its applicability to industrial practice. If flexibility is probably the main advantage deriving from Incremental Forming use, today a new point of view is given by the possibility to use the process instead of a sequence of operations, allowing also a better sustainability. Formability enhancing is one of the keyfactors of this success and for this reason it is widely investigated, also on lightweight materials, for which the use of a preliminary heating is required. In the paper the formability of Magnesium AZ31 is investigated in warm Incremental Forming, focusing the attention on the tools currently utilised for describing material formability. It is shown that Forming Limit Curves fail in this goal while a study of fracture, exploiting results of conventional tensile tests, supplies more appreciable results.
International Journal of Material Forming, 2008
International Journal of Material Forming, 2008
Key Engineering Materials, 2014
ABSTRACT
Key Engineering Materials, 2010
ABSTRACT The paper presents results obtained at two labs, on in Germany and one in Italy, in term... more ABSTRACT The paper presents results obtained at two labs, on in Germany and one in Italy, in terms of friction coefficient as function of hot stamping process parameters. Even if the testing procedures and analysis tools to evaluate tribological conditions are different for the two labs, both the approaches show a similar trend as regards the friction coefficient dependence from the process parameters.
International Journal of Material Forming, 2008
Production Engineering, 2010
The paper deals with the correlations that can be established in the numerical simulation of manu... more The paper deals with the correlations that can be established in the numerical simulation of manufacturing process chains among the process parameters, microstructure evolution, and properties of the final product. With the focus on process chains applied to bulk and sheet metal parts where deformation is carried out in hot working conditions, the paper illustrates through three application cases the role that the analysis of the microstructure evolution plays in the process chains simulations and, in particular, in enhancing the capabilities of the models that are currently implemented in commercial FE codes for predicting the properties of the final part.

International Journal of Material Forming, 2011
The paper presents the mechanical and microstructural characterization of the magnesium alloy AZ3... more The paper presents the mechanical and microstructural characterization of the magnesium alloy AZ31B through tests conducted at elevated temperature on a dedicated uni-axial tensile set-up. The samples are heated in-situ through induction heating and their actual deformation is recorded in-line through the Aramis™ system. Results from the tests in terms of flow stress, plastic properties and anisotropic coefficients are presented and commented. Additionally, the microstructural analysis on deformed samples in terms of grain size and recrystallized fraction is shown, in order to identify the fundamental mechanisms of dynamic recrystallization and grain growth and to correlate them with the testing parameters. The study provides the best combination of process parameters that can assure, at the same time, good formability and sound microstructure in the warm forming temperature range.
Key Engineering Materials, 2009
D. Pellegrini 1, a , J. Lechler 2,b , A. Ghiotti 1,c , S. Bruschi 3,d and M. Merklein 2,e ... 1DI... more D. Pellegrini 1, a , J. Lechler 2,b , A. Ghiotti 1,c , S. Bruschi 3,d and M. Merklein 2,e ... 1DIMEG, Univ. of Padova, Via Venezia 1, 35131, Padova, Italy ... 2 Chair of Manufacturing Technology (LFT), University of Erlangen-Nuremberg, Egerlandstr. 13, 91058 Erlangen, Germany ...

International Journal of Material Forming, 2010
Hot forging of large ingots made of high temperature resistant steels is gaining renewed attentio... more Hot forging of large ingots made of high temperature resistant steels is gaining renewed attention due to the increasing demand of large products mostly for the power industry. Hot forging is chosen among different manufacturing processes thanks to its potentialities in producing sound components characterized by excellent mechanical properties. Nevertheless, one of the most critical issues lies in the presence of shrinkage cavities and porosities inside the ingot that must be closed and healed completely during forging in order to avoid catastrophic failure of the component during its service life. The paper presents the FE modeling of the cogging process applied to a large component made of a duplex steel. An accurate calibration of the model in terms of material rheology and microstructure helps in quantifying the ranges of variables that are recognized to affect the closure and bonding of internal voids. A procedure is proposed to evaluate the recrystallized fraction of duplex steels which is likely to affect the goodness of such closure and bonding.

Research on data integration has provided a set of rich and well understood schema mediation lang... more Research on data integration has provided a set of rich and well understood schema mediation languages and systems that provide a meta-data representation of the modeled real world, while, in general, they do not deal with data instances. Such meta-data are necessary for querying classes result of an integration process: the end user typically does not know the contents of such classes, he simply defines his queries on the basis of the names of classes and attributes. In this paper we introduce an approach enriching the description of selected attributes specifying as meta-data a list of the "relevant values" for such attributes. Furthermore relevant values may be hierarchically collected in a taxonomy. In this way, the user may exploit new meta-data in the interactive process of creating/refining a query. The same meta-data are also exploited by the system in the query rewriting/unfolding process in order to filter the results showed to the user. We conducted an evaluation of the strategy in an e-business context within the EU-IST SEWASIE project. The evaluation proved the practicability of the approach for large value instances.
International Journal of Forming Processes, 2001
Key Engineering Materials, 2007
ABSTRACT
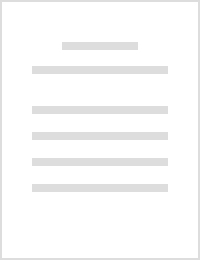
Advanced Materials Research, 2014
ABSTRACT Hot stamping of quenchenable high strength steels represents the most promising forming ... more ABSTRACT Hot stamping of quenchenable high strength steels represents the most promising forming technology for the manufacturing of safety and crash relevant car parts. In such process, the manganese-boron steel 22MnB5 is homogeneously austenitized, formed and subsequently quenched in one process step, so that complex geometric structural components can be formed with an ultimate tensile strength up to 1500 MPa. Due to the high temperature, no lubrication is used during the process with consequent high wear and reduced service-life of the dies. Commercial available steel blanks usually present an Al-Si coating that has been specifically developed as a protection from oxidation and decarburization and, at the same time, has proved positive influence also on the decreasing the friction at interface between the blank and the dies during the forming. Although such coating is generally accepted as the only lubrication medium in hot stamping, its performances are considered not appropriate for a good lubrication. The paper presents the comparison of the standard Al-Si coating and a new Zn coating when applied to metal sheets in hot stamping. A novel apparatus to investigate the tribological conditions during sheet metal working processes is presented. In addition to the control of mechanical (i.e. normal pressure) and kinematic parameters (i.e. sliding speed, sliding length), the developed testing machine permits to reproduce the thermal fields and monitor the thermal conditions of the sheet and tool materials. Experiments were carried out on Zn coated 22MnB5 sheets in the range between 700° and 950°C and compared with the performances of the commercial Al-Si coating. The coating performances are investigated for different heating temperatures and soaking times.
Key Engineering Materials, 2009
ABSTRACT
Key Engineering Materials, 2007
ABSTRACT
Advanced Materials Research, 2006

Wear, 2011
Sheet metal forming processes usually involve a sliding contact between the blank and tool surfac... more Sheet metal forming processes usually involve a sliding contact between the blank and tool surfaces, thus requiring the use of lubricants to prevent severe tribological conditions at the tool-workpiece interface. However, improper lubrication policies may have a negative impact on the environment, due to the use of unhealthy degreasing agents to wash the formed parts. In recent years, the introduction of the diamond like carbon (DLC) coatings has represented an attractive solution for the development of dry or nearly-dry forming processes. To be effective, these coatings must strongly bond to the dies substrate in order to grant resistance to the abrasive and adhesive wear. Although many approaches for evaluating the tribological performances of such coatings can be found in the existing literature, they often suffer from limitations in reproducing the interface conditions typical of the industrial processes. The objective of the present research work is to investigate the tribological behaviour of DLC coatings applied to sheetforming tools under process conditions compared to the ones experienced by the traditional coatings used in industry. Experimental values of the friction coefficient have been determined by means of strip drawing tests and the coatings wear and adhesion to the substrate have been investigated by means of pin-on-disk and scratch tests.
Uploads
Papers by Stefania Bruschi