Papers by Azwan Iskandar Azmi

Hybrid composites of carbon/glass fibre have gained wide application in various facets of enginee... more Hybrid composites of carbon/glass fibre have gained wide application in various facets of engineering fields due to material property enhancements. In common practices, hybrid composite are manufactured to near-net shapes; however, finishing operation that involves machining operation such as drilling is essential for assembly with other components. In this paper, the parametric effects of controlled parameters on delamination during drilling carbon/glass hybrid polymer composite are presented. Taguchi design of experiment is employed to statistically analyze the drilling performance of carbon/glass hybrid composite. The experiments were conducted to elucidate the effects of spindle speed, feed rate and tool geometry on delamination using uncoated cement carbide (K20) tool of 8 mm diameter. The results showed that the delamination values are greatly influenced by the feed rate and tool geometry rather than spindle speed. This is likely due to the higher thrust force exerts on the workpiece during drilling operation.
Advanced Materials Research, 2016

The feasibility of four vegetable oils was studied in drilling AISI 316 stainless steel using HSS... more The feasibility of four vegetable oils was studied in drilling AISI 316 stainless steel using HSS drill tool through assessment of surface integrity and surface roughness. In particular, the performance of palm, sesame, olive and coconut oils were compared under minimum quantity lubrication (MQL) technique. Temperature of the cutting zones as well as their surface roughness and surface integrity using these vegetable oils were compared for the same spindle speed (rev/min), feed rate (mm/rev) and depth of cut (mm). The results reported that the use of coconut oil in this experiment has achieved better surface roughness and surface integrity. This was followed by palm, olive and sesame oil. Viscosities of the fluids also have been analyzed, and the coconut oil has the lowest average viscosity value. This shows that coconut oil possesses better fluidity and faster cooling capacity than the other oils tested. Based on these results, coconut oil are recommended as viable alternative lubricants during machining of AISI 316 stainless steel.

Advances in Engineering Software, 2015
ANFIS based tool wear/condition monitoring is demonstrated for end milling GFRP composites.Grid p... more ANFIS based tool wear/condition monitoring is demonstrated for end milling GFRP composites.Grid portioning and subtractive clustering are used to partition the experimental data.Using feed force produces better prediction capability compared to cutting force.Statistical analyses are used to evaluate the predictive capability.The challenges of machining, particularly milling, glass fibre-reinforced polymer (GFRP) composites are their abrasiveness (which lead to excessive tool wear) and susceptible to workpiece damage when improper machining parameters are used. It is imperative that the condition of cutting tool being monitored during the machining process of GFRP composites so as to re-compensating the effect of tool wear on the machined components. Until recently, empirical data on tool wear monitoring of this material during end milling process is still limited in existing literature. Thus, this paper presents the development and evaluation of tool condition monitoring technique using measured machining force data and Adaptive Network-Based Fuzzy Inference Systems during end milling of the GFRP composites. The proposed modelling approaches employ two different data partitioning techniques in improving the predictability of machinability response. Results show that superior predictability of tool wear was observed when using feed force data for both data partitioning techniques. In particular, the ANFIS models were able to match the nonlinear relationship of tool wear and feed force highly effective compared to that of the simple power law of regression trend. This was confirmed through two statistical indices, namely r2 and root mean square error (RMSE), performed on training as well as checking datasets.
Applied Mechanics and Materials, 2015
Advanced Materials Research, 2015
Advanced Materials Research, 2015
International Review of Mechanical Engineering (IREME), 2014
This paper is to compare the performance of machining characteristic of two types of composite bl... more This paper is to compare the performance of machining characteristic of two types of composite blends: Palm Oil-based wax/ LLDPE/ Palm oil fiber and Palm Oil-based wax/ HDPE/ Palm oil fiber to industrial blue wax. Palm oil-based wax is a waste material produced from palm oil refining process. Current prototyping activities use industrial blue wax to produce part prototypes for machining processes. The results show that palm oil-based wax blends produced better machining characteristics than the existing industrial blue wax. The machinability study covered surface roughness, chip formation characteristic, dimensional consistency and cutting tool wear. The new palm oil-based wax will be an attractive alternative to the existing industrial blue wax for prototyping application due to lower cost of production.
Advanced Materials Research, 2014
Applied Mechanics and Materials, 2014
This paper studies the effect of minimum quantity lubricant of SiO 2 nanoparticle with surfactant... more This paper studies the effect of minimum quantity lubricant of SiO 2 nanoparticle with surfactant, PEG on surface roughness during machining of mild steel. The application of conventional cutting fluid leads to techno-environmental issue such as environmental pollution. Nanolubricant consists of suspended nanoparticles in base fluid. Nanolubricant with surfactant creates stability of the particles in the base fluid. The results indicate the application of minimum quantity lubricant of nanolubricant with surfactant during machining process lead to minimum usage of cutting fluid and better surface finish.
Applied Mechanics and Materials, 2014

International Journal of Materials and Product Technology, 2013
The use of end milling process for machining of fibre reinforced polymer composites has been wide... more The use of end milling process for machining of fibre reinforced polymer composites has been widespread in various industries. Until recently, very little work has been reported with regard to characterisation of chip formation mechanisms while end milling these composite materials. This paper reports such study which was accomplished via high speed photography and quick stop procedure. It is apparent that the heterogeneity and insufficient ductility of the composites have produced discontinuous and fracturing chips. Information disclosed by the high-speed photography footages has shown that a layer of delaminated chip was formed as the tool cutting edge fractured the workpiece along the fibre orientation at the lowest cutting speed. The increased cutting speed accelerates the fracture of chips into smaller segments, which make it difficult to denote any chip formation processes. Similarly, shorter chip fragments were created as the tool cut at different fibre orientation (45° and 90° with respect to tool feed direction).
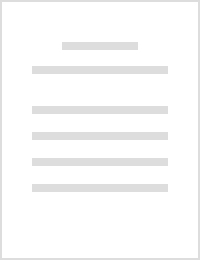
Machining of composite materials is usually performed to achieve required geometrical shapes and ... more Machining of composite materials is usually performed to achieve required geometrical shapes and dimensional tolerances. However, machinability evaluation of glass fibre-reinforced polymer (GFRP) composites in end milling has not yet received its due attention in the research community despite the extensive industrial use of this process. This work aims to elucidate the end milling machinability of GFRP composites with respect to surface roughness, tool life and machining forces. Experiments were conducted under different experimental parameters and their levels according to the Taguchi design of experiment method. Taguchi analysis combined with statistical analysis of variance (ANOVA) was performed to quantify the effects of spindle speed, feed rate and depth of cut on those characteristics. Multiple regression analysis (MRA) was also employed to establish parametric relationships between the experimental parameters and the machinability outputs. Results from ANOVA and MRA reveal that feed rate is the governing factor affecting all the machinability outputs. The calculated values from MRA have been found to be fairly close to experimental values in almost all cases. Validation tests under randomly selected machining conditions have further demonstrated the feasibility of the developed mathematical models with 8–12% error for tool life and machining forces predictions while >19% error for calculating the surface roughness.
Complexity of the machining process, the nonlinear relationship between parameters, and the rando... more Complexity of the machining process, the nonlinear relationship between parameters, and the random variations of material properties make the prediction of tool life during machining of composite material a challenge. Therefore, this article reports on the application of fuzzy logic technique for modelling of the useful life of the end mill cutter while machining under the aforesaid process. Dry end milling experiments were conducted to gather experimental data, followed by the design of Mamdani fuzzy inference system (FIS) so as to perform fuzzy logic correlation between the employed machining conditions with the tool life. Results showed remarkable prediction of tool life when compared to the experimentally determined values. Confirmation tests of randomly selected conditions were also undertaken to further demonstrate the effectiveness of the proposed model.
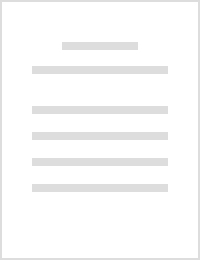
Composite products are often subjected to secondary machining processes as integral part of compo... more Composite products are often subjected to secondary machining processes as integral part of component manufacture. However, rapid tool wear becomes the limiting factor in maintaining consistent machining quality of the composite materials. Hence, this study demonstrates the development of an indirect approach in predicting and monitoring the wear on carbide tool during end milling using multiple regression analysis (MRA) and neuro-fuzzy modelling. Although the results have indicated that acceptable predictive capability can be well achieved using MRA, the application of neuro-fuzzy yields a significant improvement in the prediction accuracy. It is apparent that the accuracies are pronounced as a result of nonlinear membership function and hybrid learning algorithms. Using the developed models, a timely decision for tool re-conditioning or tool replacement can be achieved effectively.

Materials and Manufacturing …, Jan 1, 2012
This article describes an experimental investigation on end milling of glass fiber reinforced pol... more This article describes an experimental investigation on end milling of glass fiber reinforced polymer (GFRP) composites using uncoated tungsten carbide tool. A series of experiments were carried out to evaluate the machinability of GFRP composites in terms of tool wear, tool useful life, machining quality, and machining forces. Machinability data were evaluated in the form of Taylor's equation in order to predict the tool performance while machining this composite material. The useful life of the cutting tool was found to be well described by the Taylor's equations. The cutting speed was identified as the key parameter in influencing the tool life followed by feed rate and fiber orientation. Machining force variations were constantly monitored during end milling tests, which are mainly attributed to the growth of tool wear and fiber orientation.
Uploads
Papers by Azwan Iskandar Azmi