Papers by Steven Bervoets

SAE Technical Paper Series, 2010
In 2007 Punch Powertrain started the development of a full hybrid powertrain concept based on its... more In 2007 Punch Powertrain started the development of a full hybrid powertrain concept based on its CVT. A performance and efficiency analysis proved that a post-configuration offered the best solution. In parallel to the mechanical and electrical development an advanced, Matlab/Simulink® simulation system was established. A robust powertrain strategy was developed and implemented into the simulation system. Results show a potential of 30% to 70% fuel efficiency improvement depending on the cycle (type approval and real world cycles). A higher saving potential is possible as a plug-in. The fuel efficiency improvement is reached while meeting other important targets. First of all, the powertrain cost premium needs to match the saving. Next to keeping the transmission cost under control the electric drive technology and the batteries are cornerstones of the powertrain development. A dedicated switched reluctance electric motor/generator is developed at a partner. Switched reluctance combines high efficiency and dynamic behaviour with a low cost potential. Special care has been taken to iron out some drawbacks like torque ripple and noise. LiFePO 4 is the preferred battery chemistry. It offers the best combination of performance and cost without the safety risk of classic lithium ion or polymer cells. Additionally, the powertrain size is very restricted. The development team at Punch Powertrain managed to keep the powertrain length, width and height within the size of the conventional counterpart. This enables a straightforward integration into most engine bays. As such, Punch Powertrain offers a fairly easy hybridization path for conventional cars. During the development project the search for auxiliary components was a continuous effort to find affordable components that do not jeopardize the development targets for mass, space and efficiency. For most components a "hybrid compatible" solution was found. The hydraulic pump for the transmission was one exception. A parallel development was initiated during the project. A demonstrator vehicle was built to drive as EV mid 2009 and as full hybrid by the end of 2009. In parallel a second powertrain is built to undergo a series of tests on bench to validate and optimize the powertrain strategy. By exchanging powertrain control modifications between the demonstrator and the test bench driveability will be guaranteed while further optimizing the fuel economy. Experience from both test platforms will be used in

World Electric Vehicle Journal, Sep 24, 2010
The parallel hybrid powertrain developed by Punch Powertrain provides also a nice solution for ra... more The parallel hybrid powertrain developed by Punch Powertrain provides also a nice solution for range extender and boosted range extender vehicles. While most range extender solutions like the GM Volt or the Jaguar XJ Limo Green Hybrid Concept have a series hybrid topology Punch's uses a parallel hybrid topology. A parallel topology offers a higher efficiency when the vehicle is driven in hybrid mode. This is even more the case by applying the strategy developed at Punch for this powertrain. This strategy can narrow down the combined engine and CVT operation to peak efficiency. This parallel topology does not only offer the possibility to extend the EV-range of the vehicle, it also allows extending the power in cases the vehicle is used in high power situations its EV powertrain is not designed for. By applying this powertrain in vehicles used for urban and suburban deliveries the electric powertrain can be sized for the majority of its use, i.e. low to medium speed driving using low to medium power. The engine can kick in when more power is required, e.g. high speed driving or accelerating with high payloads. Consequently this concept allows using a lower power rating for the electric powertrain (motor/generator and battery). Due to its parallel topology also one electric machine is required. These cost advantages come with the necessity to use a CVT transmission. Most parts of this transmission are already made in high volume while the other parts are carried over from the other hybrid powertrains from Punch. Consequently this CVT transmission can be produced at low cost. As such Punch Powertrain offers a valid alternative to equip electric vehicles with a cost and fuel efficient range extender or boosted range extender powertrain.

The parallel hybrid powertrain developed by Punch Powertrain provides also a nice solution for ra... more The parallel hybrid powertrain developed by Punch Powertrain provides also a nice solution for range extender and boosted range extender vehicles. While most range extender solutions like the GM Volt or the Jaguar XJ Limo Green Hybrid Concept have a series hybrid topology Punch‘s uses a parallel hybrid topology. A parallel topology offers a higher efficiency when the vehicle is driven in hybrid mode. This is even more the case by applying the strategy developed at Punch for this powertrain. This strategy can narrow down the combined engine and CVT operation to peak efficiency. This parallel topology does not only offer the possibility to extend the EV-range of the vehicle, it also allows extending the power in cases the vehicle is used in high power situations its EV powertrain is not designed for. By applying this powertrain in vehicles used for urban and suburban deliveries the electric powertrain can be sized for the majority of its use, i.e. low to medium speed driving using low...
Late 2006 Punch Powertrain started the development of a hybrid powertrain. To meet the next gener... more Late 2006 Punch Powertrain started the development of a hybrid powertrain. To meet the next generation of hybrids head on Punch Powertrain defined ambitious targets with respect to fuel saving, total cost and vehicle implications. To supply hybrid powertrains to OEMs a minimal impact on the vehicle side is
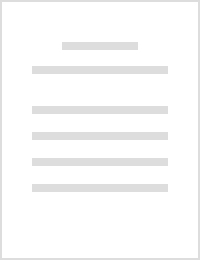
This paper presents an advanced development of a switched reluctance motor/generator for automoti... more This paper presents an advanced development of a switched reluctance motor/generator for automotive traction applications. The performance, efficiency and peak torque characteristics of switched reluctance machines, combined with its typical robust, low cost construction make this technology an attractive alternative to other motor types typically chosen for traction applications. In this research, a combined optimization was conducted on the design and control for a compact high torque assist motor/generator aimed at application in full hybrid vehicles. From the early design stage, known challenges related to switched reluctance motors such as torque ripple, vibrations and acoustic noise were addressed by a combined approach of innovative mechanical design features and state of the art control of the motor excitation. The motor was manufactured and characterized, with resulting characteristics covering the application requirements and matching simulated performance and efficiency. ...
Late 2006 Punch Powertrain started the development of a hybrid powertrain. To meet the next gener... more Late 2006 Punch Powertrain started the development of a hybrid powertrain. To meet the next generation of hybrids head on Punch Powertrain defined ambitious targets with respect to fuel saving, total cost and vehicle implications. To supply hybrid powertrains to OEMs a minimal impact on the vehicle side is required. This paper focuses on the chosen parallel topology, the general system optimisation strategy, the technology and components selection and the control system development. Simulations for different target vehicles are performed with detailed component maps. The fuel consumption target is well within reach. Actual hardware tests are planned for 2009.
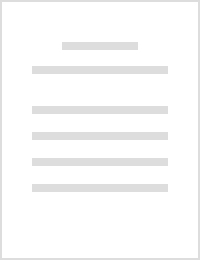
2013 Eighth International Conference and Exhibition on Ecological Vehicles and Renewable Energies (EVER), 2013
ABSTRACT This paper describes a control approach to reduce the torque ripple of the switched relu... more ABSTRACT This paper describes a control approach to reduce the torque ripple of the switched reluctance motor (SRM) employed as a prime mover in a full electric vehicle (FEV). The SRM drive, which was originally installed in the prototype electric vehicle was facing significant torque ripple at low speeds. The implemented control solution allowed to overcome this problem. The presented approach is based on the extensive mathematical modeling of the SRM drive. The nonlinear characteristics of the SRM have been obtained with the finite element method (FEM) software. The obtained FEM results have further been used in a transient lumped-parameter Matlab/Simulink model of the SRM drive, where the so-called Torque Sharing Function control technique with optimized control parameters was implemented to reduce the torque ripple and also to increase efficiency.
SAE Technical Paper Series, 2010
ABSTRACT
Late 2006 Punch Powertrain started the development of a hybrid powertrain. To meet the next gener... more Late 2006 Punch Powertrain started the development of a hybrid powertrain. To meet the next generation of hybrids head on Punch Powertrain defined ambitious targets with respect to fuel saving, total cost and vehicle implications. To supply hybrid powertrains to OEMs a minimal impact on the vehicle side is required. This paper focuses on the chosen parallel topology, the general system optimisation strategy, the technology and components selection and the control system development. Simulations for different target vehicles are performed with detailed component maps. The fuel consumption target is well within reach. Actual hardware tests are planned for 2009.
Uploads
Papers by Steven Bervoets