Papers by Burkhard Corves
Integrative Produktionstechnik für Hochlohnländer, 2011
Selected mechatronic design solutions that have been developed at the Department of Mechanism Des... more Selected mechatronic design solutions that have been developed at the Department of Mechanism Design and Machine Dynamics at RWTH Aachen University will be presented. These mechatronic systems are taken from the field of glass machinery, textile machinery and robotics. It will be shown that for a proper design process modelling, simulation and optimization are indispensable.
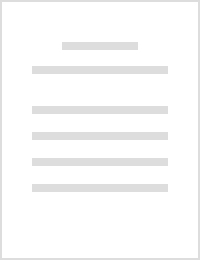
The most important aim of the IFToMM is “to promote research and development in the field of Mach... more The most important aim of the IFToMM is “to promote research and development in the field of Machines and Mechanisms by theoretical and experimental methods, along with their practical application” (see article 2.1 of the statutes [12]). This is strongly connected with access to current knowledge, experience and skills in the field of mechanism and machine science (resp. motion science). However this content is characterized by a high diversity and heterogeneity, because it is mostly scattered, represented in different forms (physical model, drawings, textbooks etc.), languages and mediums. Therefore there is a need to establish an open access, multilingual digital library in this field of techno-cultural heritage. Against this background, members of three IFToMM-Commissions initiated a joint project called thinkMOTION. In this project, which promotes the idea of open access, the techno-cultural heritage and the current developments in motion science will be widely accessible via Europeana, which is the search platform for European digital libraries initiated by the European Commission. The content is useful for a wide range of user groups, such as interested laymen, engineers, scientists, lecturers, pupils, students all over the world, in that it opens new possibilities in multilingual searching, browsing and using of information sources.
In spite of known methods and available tolerance software there are tolerance investigation prob... more In spite of known methods and available tolerance software there are tolerance investigation problems of guidance mechanisms and especially convertible roof mechanisms that can be suitably solved only with special knowledge of kinematic coherences. A new method will be presented that uses substitute mechanisms to solve special tolerance investigation problems of guidance mechanisms. With the help of an example of use the new developed method will be compared with standard tolerance investigation approaches.
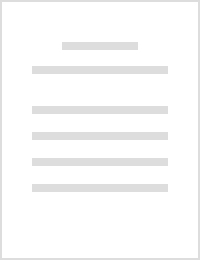
ABSTRACT Cooperating robots are a flexible solution for handling and assembling large-scale objec... more ABSTRACT Cooperating robots are a flexible solution for handling and assembling large-scale objects, but they cause high procurement costs and personnel costs for programming. The purpose of the project is to simplify the programming by a new hardware concept of the control system and to guarantee an easy reconfiguration to flexibly adapt and re-use robot cells. Derived from existing solutions, a modular control system had been developed to simplify the programming procedure. It subordinates all robots under an independent central control module, which leads to equality, exchangeability and reconfigurability of the robots. The control system was implemented in a layout of simple kinematic units which can be easily reconfigured within an assembly platform. Therefore the modularity of the control system must follow the modularity of the complete mechatronic system. The control concept is independent from the robot manufacturer and will be validated for different industrial robots in future research. The project targets on applications in aircraft production, where large-scale objects in small batches have to be assembled with cooperating robots.
In this presentation the development of a spherical linkage mechanism for passenger vehicle swive... more In this presentation the development of a spherical linkage mechanism for passenger vehicle swivel joint tow coupling is reviewed. The idea for the swivel joint tow coupling emerged after a cooperation between the Department of Mechanism Theory and Dynamics of Machines (IGM) of the RWTH-Aachen University and a market leading manufacturer of tow bar mechanisms. Presently, the swivel joint mechanism has been patented worldwide [1]. Additionally, a prototype of the tow coupling is currently in an advanced design phase, in which the possibilities for cost optimization and suitability for series production are assessed. The dimensions of the spherical mechanism were defined using the dynamic spatial geometry program “GECKO” currently developed at IGM.

Production Engineering, 2011
The demand for more versatile assembly and handling systems to facilitate customized production i... more The demand for more versatile assembly and handling systems to facilitate customized production is gaining in importance, especially with regard to the constantly-increasing cost pressure, to expansion of the range of product versions and the shortening of innovation cycles. As a cost-effective approach for frequently changing assembly tasks, a novel manipulation concept has been developed by combining given robot technologies. This new handling system has a modular and adaptable layout, which consists of several mobile arms to manipulate the object in six-dimensional Cartesian space. After grasping, when the arms are attached to the object, the mechanical architecture is similar to parallel manipulators or cooperating robots. As the mounting and gripping points of the arms can easily be changed, the manipulator can be reconfigured so as to match the user’s preferences and needs. In addition to the kinematic adaption the regarding task, the hardware and new functions can be reconfigured as well. Contact elements, measurement and assembly devices as well as testing modules can easily be in integrated in the concept. A modular automatic control concept combined with a self-optimizing planning tool helps the user to find the optimal configuration and realize it in an economic way.
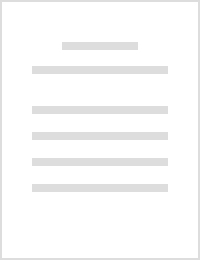
In addition to the well-known application fields of composite materials in the aircraft industry,... more In addition to the well-known application fields of composite materials in the aircraft industry, sport cars and wind energy, there are further potential applications e.g. rail, automobile and machine construct. In contrast to dry technology (prepreg), wet technology using reinforced textile preforms offers a cost-effective production of composite structures. These are due to low cost materials, easier storage conditions and automation possibilities. In this work, a new multifunctional robot end-effector system for automated manufacture of textile preforms is developed, designed and implemented. The robot end-effector system consists of an adaptive end-effector (AEE) to grasp, manipulate and lay-up the composite fabric onto a flat or curved mold and a novel double tool changer (DTC) to drape the fabric in the mold. The AEE is modular designed and features local passive and active degrees of freedom (DOF) to adapt the fabric geometry to the mold geometry. Furthermore, it is integrated with eight gripper elements with different grasp principles, such as ice-gripper or needle-gripper. Robots using DTC can carry two small tools (in this case two rollers to drape the fabric) and interchange them in the working position. With AEE and DTC, many manual processes in the production chain of textile preforms can be automated and can also be applied to the cost-efficient production of fibre composite parts. The application of this robot end-effector will be demonstrated by the production of a convertible car roof (CCR) with a pilot plant.

Demand for more versatile assembly and handling systems to facilitate customised production is ga... more Demand for more versatile assembly and handling systems to facilitate customised production is gaining in importance. A new handling principle has been developed as a cost-effective approach to adapt to component-dependent tasks. It is based upon the gripping and movement of objects by multiple arms within a parallel kinematic structure. This structure combines the advantages of a system of co-operating robots with a simplified drive concept, in which the number of drives used is sharply reduced. On this basis, a modular assembly platform is being developed which, in addition to the kinematic units, also facilitates the integration of measurement, testing and joining modules. The modular concept also creates the conditions for a versatile, demand-driven layout of multiple kinematic units. This facilitates not only cooperative handling of large components using several gripping points, but also the transfer of objects handled between the individual units. These features of adaptivity are the basis for self-optimisation, which then can be implemented within a suitable control system.
The paper gives a historical overview of the development of mechanism or kinematic models for mot... more The paper gives a historical overview of the development of mechanism or kinematic models for motion generation in mechanical engineering. Models can serve for teaching purposes and also serve as small test rigs when investigating the running behaviour and estimating the running quality of a mechanism or machine. So the development of mechanisms and machines through the last centuries since Antiquity is also coupled to the development of design of virtual and physical mechanism models.
Uploads
Papers by Burkhard Corves