Papers by VivekSheel Rajput

To machine "difficult-to-cut" materials including ceramics, glass, and silicon wafers, a hybrid a... more To machine "difficult-to-cut" materials including ceramics, glass, and silicon wafers, a hybrid and widely recognized process known as electrochemical discharge machining (ECDM) is used. It employs the working principle of electrochemical machining (ECM) and electric-discharge machining (EDM) processes to remove the material by combining chemical etching with thermal melting. The materials machined using ECDM exhibits enormous implementations in the field of MEMS and lab-on-chip. Different facets of the ECDM process have been researched in an effort to escalate its effectiveness ever since it was originally shown. The present chapter discusses the critical research potentials of the ECDM process that was documented in the past decades. Additionally, it covers the impact of several input process factors, including electrical, electrolyte, and tool electrode, on ECDM performance. A summarized report on ECDM hybridization, and variants are also given in a lucid manner. It also identifies future directions that might enhance the ECDM process's overall machining performance. It is concluded that with the help of gas film dynamics controlled by variables such as electrolyte characteristics and tool motions, ECDM can machine non-conductive materials with precision. Pulsed voltage, suggested electrolytes (NaOH, KOH), and regulated tool properties (material, shape, and rotation) are important factors. Spherical tool electrodes help minimize overcut and taper comparative to other tools while machining depth and geometrical accuracies can be further improved by implementing hybridization such as magnetic assistance and ultrasonic assistance.
I-Manager's Journal on Future Engineering and Technology, 2019

Spark assisted chemical engraving (SACE) is a triumph process for processing the non-conductive m... more Spark assisted chemical engraving (SACE) is a triumph process for processing the non-conductive materials such as glass, ceramics, composites, quartz, and so on regardless of their physical properties. It shows different criticalness in the field of microelectromechanical systems (MEMS) and lab-onchips for manufacturing items with the miniaturized scale on a large scale. Due to the increasing demand for micro-components such as microsensors, micro-batteries, micro-needles, etc in aerospace, nuclear, and medical industries, there has been an escalation in the product miniaturizations. The material removal phenomena in SACE is a consolidated impact of electrochemical machining (ECM) and electric discharge machining (EDM) together. This article discusses the fundamental principles, recent studies, and influential parameter's effect on gas film stability. Moreover, the performance enhancement of the SACE process and the influence of varying discrete process parameters includes applied voltage, electrolyte concentration, tool feed rate, tool shape is discussed. Result revealed that any change in the applied voltage and electrolyte concentration results in the variable spark intensity over the work material. Tool shape significantly affects the formation of the stabilized gas film at its vicinity and its feed rate controls the effective machining gap for electrolyte availability. The present study on SACE reveals that machining with an optimum range of input parameters is crucial for its effectiveness and repeatability. The study highlights the conceivable future regions to improve the machining performance of the SACE process.

Industrial Engineering Journal, 2023
Spark assisted chemical engraving (SACE) is a triumph process for processing the non-conductive m... more Spark assisted chemical engraving (SACE) is a triumph process for processing the non-conductive materials such as glass, ceramics, composites, quartz, and so on regardless of their physical properties. It shows different criticalness in the field of microelectromechanical systems (MEMS) and lab-onchips for manufacturing items with the miniaturized scale on a large scale. Due to the increasing demand for micro-components such as microsensors, micro-batteries, micro-needles, etc in aerospace, nuclear, and medical industries, there has been an escalation in the product miniaturizations. The material removal phenomena in SACE is a consolidated impact of electrochemical machining (ECM) and electric discharge machining (EDM) together. This article discusses the fundamental principles, recent studies, and influential parameter's effect on gas film stability. Moreover, the performance enhancement of the SACE process and the influence of varying discrete process parameters includes applied voltage, electrolyte concentration, tool feed rate, tool shape is discussed. Result revealed that any change in the applied voltage and electrolyte concentration results in the variable spark intensity over the work material. Tool shape significantly affects the formation of the stabilized gas film at its vicinity and its feed rate controls the effective machining gap for electrolyte availability. The present study on SACE reveals that machining with an optimum range of input parameters is crucial for its effectiveness and repeatability. The study highlights the conceivable future regions to improve the machining performance of the SACE process.
International Journal of Advance Research and Innovation, 2021
Lecture notes in mechanical engineering, 2023
Journal of Materials Research
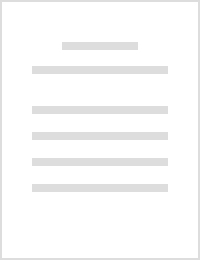
Proceedings of the Institution of Mechanical Engineers, Part C: Journal of Mechanical Engineering Science
Electrochemical discharge machining drilling (ECDD) is acknowledged as a hybrid machining process... more Electrochemical discharge machining drilling (ECDD) is acknowledged as a hybrid machining process that employs the thermal erosion and etching action for drilling. Apart from experimental findings, very rare 3D simulation studies have been covered for analyzing the ECDD. In the present investigation, a 3D simulation of the ECDD process is performed to analyze the process based on the finite element method (FEM). The predicted results are found to be in consensus with the experimental results. An increment of 10.79 mg and 5.04 mg in MRR is noticed with the concentration level increase from 10 wt.% to 60 wt.% and voltage level increase from 35V to 55V. However, a maximum error of 12.68% is observed with the FEM method of prediction when compared to experimental results. The simulation study is followed by the multi-objective optimization (Taguchi’s L16) using grey relational analysis (GRA) for controlling the ECDD parameters. The simultaneous numerical and experimental assessment of t...
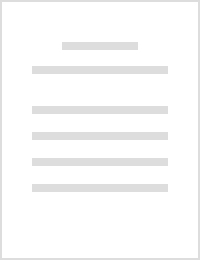
Journal of Micro and Nano-Manufacturing
Electrochemical discharge machining (ECDM) is distinguished as a novel process that involves ther... more Electrochemical discharge machining (ECDM) is distinguished as a novel process that involves thermal heating and chemical dissolution for the micromachining of “difficult-to-machine” materials like ceramics and quartz. This paper comprehensively reviews the study on gas film, the effect of various input parameters on ECDM performance, such as electrical parameters, electrolyte parameters, and tool electrode parameters, are also likewise discussed. Moreover, a summarized report on thermal modeling, gas film, discrete input parameters, hybridization, and variants in the ECDM process is also provided in a lucid manner. Based on the review, it is concluded that the machining performance of the ECDM process especially in terms of material removal rate (MRR), roughness, tool wear (TW), and thermal cracks is strongly influenced by the input parameters. The formation of the gas film induces variable machining features that can be controlled by altering the machining conditions. Additionally...
Abstract: Digital human modeling (DHM) reduces the product design and manufacturing task cycle ti... more Abstract: Digital human modeling (DHM) reduces the product design and manufacturing task cycle time by eliminating the need to construct physical setup. This paper discusses the current research on digital human modelling, their capabilities and issues generating with the growing demands of technology. With the latest computer technology, human manikin has been modified which can easily simulate and replicate the actual workplace scenario. Anthropometric databases developed which are essential part of any DHMs software are also discussed. Limitations in current DHM model are also discussed.

International Journal for Research in Applied Science and Engineering Technology
Electrochemical discharge machining is recognized as one of the novels and hybrid processes for m... more Electrochemical discharge machining is recognized as one of the novels and hybrid processes for machining nonconductive materials irrespective of their chemical and physical properties. It utilizes the application of thermal heat and chemical dissolution to remove the material. Since the ECDM process comprises the involvement of several input variables, the tool electrode feed rate is identified as the crucial variable that signifies the formation of gas film underneath the tool electrode based on gap availability. This present study focusses on the performance evaluation of the ECDM process based on tool electrode feed rate i.e., the effect of tool electrode feed rate on material removal rate (MRR) is evaluated. Applied voltage, electrolyte concentration are the other two variables picked alongside tool feed rate while MRR is selected as a response parameter. The experiments are performed according to Taguchi's L9 orthogonal array. Results revealed that the tool feed rate significantly affects the material removal as too high feed deteriorates the MRR. The combination of input variables for maximizing the MRR is acquired through S/N ratios and determined as 4mm/min, 50V and 20 wt.%, tool feed being the dominant one with 76.86 % contribution.
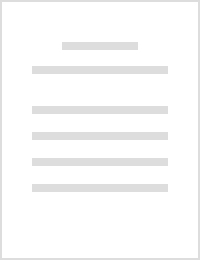
With the need of increasing demand for enhancing the properties of composite materials to be used... more With the need of increasing demand for enhancing the properties of composite materials to be used in different applications such as structural, aerospace, automobile, coating etc, the bio-inspired self-healing materials have been developed with the purpose of repairing themselves under damage caused by mechanical usage over time. These materials are bio-inspired (ex: healing of human skin) and designed on the basis of two different strategies: (a) release of healing agent into the cracks and (b) reversible cross links. This review paper comprehensively discusses the different methods (or approaches) of self healing mechanism in composite materials which is used to alleviate the effect of damage and to restore mechanical properties. Generally, two different self healing approaches are used (a) Extrinsic and (b) Intrinsic. Extrinsic utilizes the release of healing agents from the container ( i.e. Hollow glass tubes, Capsules, micro-vascular) which ruptures once crack propagates inside...

International Journal of Innovative Research in Science, Engineering and Technology, 2013
The productivity of operators and their performance are mainly depends upon the workspace in whic... more The productivity of operators and their performance are mainly depends upon the workspace in which he intends to work. This can be achieved only when they are comfortable in their workplaces designed for their best performance. Poorly designed tractors force operator to attain awkward posture which leads to musculoskeletal (MSDs) discomfort thereby reducing their efficiency and productivity. In order to eliminate discomfort study was conducted to evaluate tractor comfort from operator’s perspective and identifying poorly designed areas. Human comfort in tractors can be evaluated by direct involvement of the operators. In this study twenty operators were used to complete a questionnaire followed by an interview to get the detailed feedback of the tractor design. Objective of the thesis is (a) to evaluate tractor design for comfort (b) to identify poorly designed areas that need improvement (c) comparison of four tractor models (swaraj 855, ford 3630, Mahindra 555 and johndeere 5310) ...
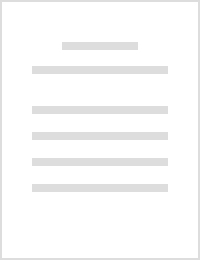
Electro-chemical discharge machining (ECDM) is a proven and novel technology for machining electr... more Electro-chemical discharge machining (ECDM) is a proven and novel technology for machining electrically non-conductive materials such as glass, quartz etc with effective material removal rate (MRR). These materials are very difficult to machine with traditional machining methods owing to their brittle nature. Material removal mechanism in ECDM is a combination of both removal mechanism of both electro-chemical machining (ECM) and electro-discharge machining (EDM) simultaneously i.e. material removal occurs due to thermal erosion and chemical dissolution. This review article discusses the fundamental physical principle of ECDM process along with the reporting of the critical research findings on machining performance. The influence of various control parameters such as applied voltage, electrolyte concentration, tool shape, tool rotation and vibration on material removal rate, surface roughness and tool wear was discussed comprehensively. On the basis of literature study, it was obse...
In electrochemical discharge machining (ECDM), sustaining the effective machining gap during micr... more In electrochemical discharge machining (ECDM), sustaining the effective machining gap during micro-drilling is strenuous because of the tool contact with the material. It deteriorates the geometric...

SN Applied Sciences
With the increased utilization of glass in micro-electromechanical systems (MEMS) applications, n... more With the increased utilization of glass in micro-electromechanical systems (MEMS) applications, need is generated to produce micro-features on glass with excellent surface quality, i.e., better hole circularity and less thermal cracks. Sparkassisted chemical engraving (SACE) has proven to be an emerging and reliable technology for micro-machining of glass that includes local joule heating of the work material for its removal. However, some problems need to be covered in the micro-hole drilling process such as low machining depth, low aspect ratio, high thermal cracks, and an increase in machining time with the increase in depth. Moreover, few finite element modeling (FEM) studies have been reported to analyze the material removal aspects in SACE. This present study developed the FEM-based thermal model to analyze the material removal rate (MRR) and investigated the different machining conditions to improve the micro-hole drilling process in SACE. Improvement in depth and aspect ratio can be achieved by using a different tool's shape which variably enhances the flow of electrolytes and thereby increases the formation rate of gas film. Pointed and cylindrical tools were used for micro-drilling operations. MRR, hole entrance diameter, machining depth, aspect ratio, thermal cracks, and machining time were observed under different machining conditions. FEM study revealed that MRR improves with the increase in both the applied voltage and electrolyte concentration. The MRR was predicted by utilizing the plots of temperature distributions and was found in accordance with the experimental results of MRR. The experimental study concluded that the pointed tool produced micro-holes with a higher machining depth and aspect ratio at an improved machining rate, while the cylindrical tool produced micro-holes with a smaller number of thermal cracks and better circularity.
Digital human modeling (DHM) reduces the product design and manufacturing task cycle time by elim... more Digital human modeling (DHM) reduces the product design and manufacturing task cycle time by eliminating the need to construct physical setup. This paper discusses the current research on digital human modelling, their capabilities and issues generating with the growing demands of technology. With the latest computer technology, human manikin has been modified which can easily simulate and replicate the actual workplace scenario. Anthropometric databases developed which are essential part of any DHMs software are also discussed. Limitations in current DHM model are also discussed.
Journal of Mechanical Science and Technology
Journal of The Electrochemical Society
Uploads
Papers by VivekSheel Rajput