Papers by Vasilios Spitas

Micromachines, Nov 13, 2023
Peristaltic pumps are widely used in biomedical applications to ensure the safe flow of sterile o... more Peristaltic pumps are widely used in biomedical applications to ensure the safe flow of sterile or medical fluids. They are commonly employed for drug injections, IV fluids, and blood separation (apheresis). These pumps operate through a progressive contraction or expansion along a flexible tube, enabling fluid flow. They are also utilized in industrial applications for sanitary fluid transport, corrosive fluid handling, and novel pharmacological delivery systems. This research provides valuable insights into the selection and optimal design of the powertrain stages for peristaltic pumps implemented in drug delivery systems. The focus of this paper lies in the simulation and optimization of the performance of a power transmission gearbox by examining the energy consumption, sound levels, reliability, and volume as output metrics. The components of the powertrain consist of a helical gear pair for the first stage, a bevel gear pair for the second one, and finally a planetary transmission. Through extensive simulations, the model exhibits promising results, achieving an efficiency of up to 90%. Furthermore, alternative configurations were investigated to optimize the overall performance of the powertrain. This process has been simulated by employing the KISSsoft/KISSsys software package. The findings of this investigation contribute to advancements in the field of biomedical engineering and hold significant potential for improving the efficiency, reliability, and performance of drug delivery mechanisms.
Formulation of a non-dimensional criterion for stable dynamical response in coaxial magnetic gears
Journal of engineering mathematics, Feb 1, 2024
Use of 3D Printing in Creating Laboratory Equipment During Students' Final Projects
ICERI proceedings, Oct 31, 2023
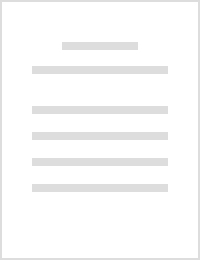
Fully ceramic versus steel gears: Potential, feasibility and challenges
Proceedings of the Institution of Mechanical Engineers, Part C: Journal of Mechanical Engineering Science
The most common gear strength calculations performed in accordance with ISO/TC 60/SC 2 include su... more The most common gear strength calculations performed in accordance with ISO/TC 60/SC 2 include surface durability and root bending strength. Typical geared power transmissions are characterized by high Hertzian contact stresses (surface durability) on the flanks – frequently in the order of 103 MPa – versus almost half an order magnitude lower first principal stresses on the tooth root (tooth bending strength). Therefore, the use of high strength special steel alloys is almost mandatory, especially in high-end applications, mainly to withstand the high contact stress values. Ceramic materials are typically characterized by high compressive strength versus very low flexural strength that at first glance makes them inefficient for gear transmissions since they are unlikely to withstand the tensile root stresses. Nevertheless, ceramic materials possess a number of advantages that makes them potential candidates for geared transmissions, such as their exceptional thermal properties, the...

Mathematical and computational applications, May 18, 2024
This work introduces a 2D model that calculates power losses in coaxial magnetic gears (CMGs). Th... more This work introduces a 2D model that calculates power losses in coaxial magnetic gears (CMGs). The eddy current losses of the magnets are computed analytically, whereas the core losses of the ferromagnetic segments are computed using an analytical-finite element hybrid model. The results were within 1.51% and 3.18% of those obtained from an FEA for the eddy current and core losses in the CMG for an indicative inner rotor speed of 2500 rpm. In addition, the significance of the circumferential magnet segmentation is demonstrated in the CMGs. Furthermore, a parametric investigation of the efficiency of the system for different applied external loads is carried out. Finally, a mesh sensitivity analysis is performed, along with the computation of the average power losses throughout one full period, resulting in an at least 80% reduction in computational costs with a negligible effect on accuracy. The developed model could be a valuable tool for the minimization of power losses in CMGs since it combines high accuracy with a low computational cost.

Materials
This work is focused on the development of creep and stress relaxation models on Inconel 625 and ... more This work is focused on the development of creep and stress relaxation models on Inconel 625 and Stainless Steel 310 materials for additive manufacturing. At the end, the operational lifespan of an industrial-scale additive manufactured recuperator is evaluated. An industrial-scale recuperator for burners with a highly complex geometry is manufactured using Continuous Wave SLM and Pulsed Wave Selective Laser Melting techniques. The recuperator operates under steady but high thermal loads, reaching temperatures of up to 875 °C. Therefore, its service life is assessed, considering creep and stress relaxation phenomena. Two different materials are evaluated: Inconel 625 and Stainless Steel 310. Tensile testing has been conducted on samples at various temperatures to acquire material parameters, incorporating appropriately the anisotropic nature of the materials. Creep parameters were determined through creep experiments and data from the literature, and the recuperator response was sim...
A Novel Monolithic Shape-Morphing Bearing for Real-Time NVH Control
Springer eBooks, 2023
3BUILD – First 3D Printed Structure in Greece
Rilem bookseries, 2023

Graphyne is a material that has unique mechanical properties, but little is known about how these... more Graphyne is a material that has unique mechanical properties, but little is known about how these properties change when the material has holes. In this work, the effect of hole geometry, considering circular, triangle, and rhombus hole configurations, on the mechanical nonlinear response of γ-graphyne structures is studied. Graphyne, graphdiyne, graphyne-3, and graphyne-4 structures are under investigation. An efficient nonlinear finite element analysis (FEA) method is adequately implemented under large deformations for this purpose. The study varied the size and shape of the holes to understand how these changes affect the nanostructure's mechanical response. The results indicate that the hole geometry significantly impacts the mechanical nonlinear response of γ-graphyne structures. The holes' size and shape affect the structures' elastic behavior, deformation, and strength. The findings can be used to optimize the design of γ-graphyne structures for specific mechanica...

MATEC Web of Conferences
Involute gears have traditionally been the preferred choice for gear transmission systems due to ... more Involute gears have traditionally been the preferred choice for gear transmission systems due to their simplicity and interchangeability. However, there are applications where they do not provide the most durable and efficient solution. While the cost of implementing optimized non-involute gears in most applications often outweighs their comparative advantages, the advent of additive manufacturing has opened up possibilities for designers to explore alternative gear tooth profiles. This is particularly relevant in the realm of plastic gears, where optimized non-involute gears produced through 3D printing can address their primary drawbacks, such as surface durability and wear resistance. In this study, a comprehensive free-form optimization process was conducted to determine the optimal tooth profile that minimizes wear on 3D printed spur gears during operation. The tooth flank geometry was represented using a 4th order B-spline curve, and a genetic algorithm was employed to determi...
Exploiting double-flank roll testing spur gear measurements to determine gear parameter deviations through numerical simulation of free-form meshing gears
Simulation Modelling Practice and Theory
Design considerations and simulation of a rolling-contact gearless automotive differential
Proceedings of the Institution of Mechanical Engineers, Part C: Journal of Mechanical Engineering Science, Feb 15, 2023
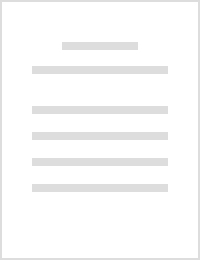
A non-linear model for elastic hysteresis in the time domain: Implementation for multiple degrees of freedom
Proceedings of the Institution of Mechanical Engineers, Part C: Journal of Mechanical Engineering Science, 2021
A model that captures the weak frequency sensitivity of elastic hysteretic damping is proposed fo... more A model that captures the weak frequency sensitivity of elastic hysteretic damping is proposed for the time-domain simulation of structures with multiple degrees of freedom (MDOF) under free or forced vibration. The model is based on a recently proposed modification to the conventional single degree of freedom (SDOF) viscous damping model, utilising a correction factor computed based on the local instantaneous response to adjust the damping coefficient such that the dissipated energy remains insensitive to the frequency characteristics of the motion. The model compares favourably to the well-established viscous (incl. Collar’s frequency correction), Rayleigh and Reid MDOF models, is applicable to any type of loading and, unlike other classes of damping models, such as Rayleigh, modal, Bouc-Wen, Biot, and Collar/Neumark, does not require extensive calibration, knowledge of the past history of motion, or a priori knowledge of the excitation characteristics and frequency.
Models and algorithm for the simulation of non-standard gear geometries in computer aided design environments
Optimisation of spur gear tooth fillet for maximum bending strength using Bezier curves
International Conference on Gears 2019, 2019
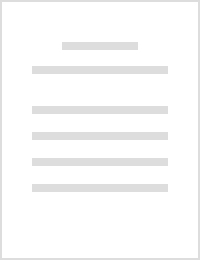
A fast, non-implicit SDOF model for spur gear dynamics
Mechanism and Machine Theory, 2021
Abstract Modeling and simulation of the nonlinear dynamic response typical in gear transmissions ... more Abstract Modeling and simulation of the nonlinear dynamic response typical in gear transmissions usually require extensive input from tooth contact analysis combined with data derived from numerical techniques that in turn comprise a time and resource-consuming procedure. In this work, an efficient SDOF model that captures meshing nonlinearities in a non-implicit manner is presented. An extensive geometric analysis designates the underlying physical mechanisms prevailing in tooth meshing enabling incorporation of the effects of backlash, varying mesh stiffness and corner contact. By this analysis, an accurate repositioning method is proposed for involute teeth contact reversal, while a general approximation function for gear pair mesh stiffness including load dependence is formulated and successfully fitted to analytical data. Consequently, distinction between single and double tooth contact is captured through a modified parametric s-curve, including the effect of corner contact. A SDOF dynamical model is formulated for a given pinion rotational velocity and solved numerically. Both static and dynamic results are compared to data available in the literature, showing high agreement with more complex methods, while maintaining the advantages of minimum required pre-calculations and low computational cost.

Modern Mechanical Engineering, 2014
In this paper a model of a high pressure hydraulic system was developed to simulate the effect of... more In this paper a model of a high pressure hydraulic system was developed to simulate the effect of increased internal leakages inside the hydraulic cylinder and the 4/2 way directional control valve and to calculate the main parameters of the hydraulic system under various loads through the use of leakage-simulating throttle valves. After the completion of modeling, the throttle valves that simulate the internal leakages were calibrated and a number of test runs were performed for the cases of normal operation and the operation with increased internal leakages. The theoretical predictions were compared against the experimental results from an actual hydraulic test platform installed in the laboratory. In all cases, modeling and experimental data curves correlate very well in form, magnitude and response times for all the system's main parameters. This proves that the present modeling can be used to accurately predict various faults in hydraulic systems, and can thus be used for proactive fault finding in many cases, especially when the defective component is not easily detected and obvious at first sight.
Fast and efficient simulation of the dynamical response of coaxial magnetic gears through direct analytical torque modelling
Simulation Modelling Practice and Theory
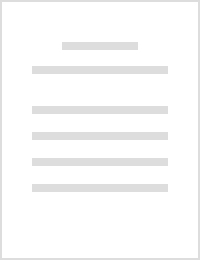
A new second order thermal model for accurate simulation of the transient and steady–state response of beta-type Stirling engines based on time-varying calculation of thermal losses
International Journal of Engine Research
A novel numerical second order transient thermal model for beta-type Stirling engines (TTMS) was ... more A novel numerical second order transient thermal model for beta-type Stirling engines (TTMS) was developed taking into account the transient heat transfer between the engine cylinder walls and pistons and the working gas in the expansion and compression space in order to determine the total power output and thermal efficiency with higher accuracy. The time-dependent energy equilibriums were formulated by including the transient thermal response of the cylinder walls and pistons until steady state operation was achieved. In addition, the transient response of the heat exchangers (cooler, regenerator and heater) was developed in order to determine more accurately the enthalpy of the working gas that enters or exits each compartment of the engine. The solution of the governing differential equations at each time step can be achieved with the implementation of a conventional fixed point algorithm. Various loss mechanisms were incorporated in order to increase the accuracy of the develop...

MATEC Web of Conferences
Magnetic gears offer significant advantages such as low noise and vibration level, lower maintena... more Magnetic gears offer significant advantages such as low noise and vibration level, lower maintenance and higher reliability compared to mechanical gears and are suitable for many applications in the industry. The coaxial magnetic gear has been extensively discussed in the literature, since it achieves higher torque densities amongst other magnetic gear configurations. The magnetic field is generated by permanent magnets mounted on the two rotors and a modulator between them. The modulator consists of ferromagnetic segments that are typically encased in a resin in order to increase its stiffness without compromising the generated magnetic field. However, due to the development of radial forces, oscillations of the ferromagnetic segments occur, which lead to torque ripples that affect the operation of the coaxial magnetic gear drive in applications where accuracy is required. This work introduces a computationally lightweight analytical 2D model in order to determine the applied radia...
Uploads
Papers by Vasilios Spitas