Papers by Dr. Arup Kumar Mandal

For the recovery of aluminium from industrial waste bottom ash, a new concept was developed for s... more For the recovery of aluminium from industrial waste bottom ash, a new concept was developed for smelting reduction in presence of metal solvent bath. Nitrogen plasma arc was generated by passing current and nitrogen gas through a hollow graphite electrode. Nitrogen plasma generated heat for reduction as well as melting under inert atmosphere inside the furnace. Pellets containing 50%bottom ash, 50% iron slime and charcoal were fed in the plasma zone above the liquid steel bath which was acted as for the absorption of reduced metals after reduction of oxides present in the wastes. Due to the immediate absorption of aluminium in the liquid steel bath after subsequent reduction from waste, vaporization loss of aluminium metal got minimized. The percent recovery of aluminium were determined in case of different exposure time, types of arcing and plasma gas etc. Maximum recovery of aluminium was recovered upto 21% with 30 minute exposure of pellets containing 50% bottom ash and 50% iron slime. It was observed that aluminum, could be recovered effectively from the wastes.
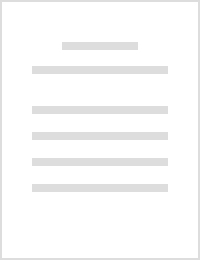
Metallurgical and Materials Transactions B-process Metallurgy and Materials Processing Science, Oct 27, 2015
A new concept for maintaining inert atmosphere with high temperature ~1973 K (1700 °C) inside the... more A new concept for maintaining inert atmosphere with high temperature ~1973 K (1700 °C) inside the furnace during smelting reduction was described, in which recovery of metallic values from wastes was done in the presence of metal bath which acts as a solvent. Nitrogen plasma arc was generated by passing current and nitrogen gas through a hollow graphite electrode. In this way, the heat for reduction reactions and melting of metal and slag phases under inert atmosphere was maintained. The mixture of bottom ash and carbonaceous reducing agent was fed in the form of pellets near the plasma zone above the liquid iron bath, used for the absorption of reduced metals after reduction of oxides present in the wastes. Percent recovery of metallic values and different consumption parameters were calculated. It was observed that aluminum, iron, and silicon could be recovered effectively from the wastes.
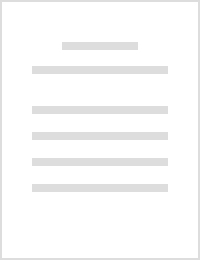
The effect of lime addition in hematite iron ore pellets on its physico-chemical as well as mecha... more The effect of lime addition in hematite iron ore pellets on its physico-chemical as well as mechanical properties with respect to blast furnace requirement was studied in a laboratory scale with varying basicity i.e. 0-2.0.Increasing addition lime produced more calcium-alumino-silicate phases (slag) as evidenced by SEMEDAX analysis. These phases have low melting points which enhances sticking behaviourof pellets, as well as imparting strength to the pellets (resulting increasing compressive strength, tumbler, abrasion and shatter index) and decreasing the porosity. The low basicity pellets were predominantly oxide-bonded, while high basicity pellets were mostly slag bonded. This means that pellets should be fired at sufficiently high enough temperature to generate liquid phases to get the sufficient strength but not so high as to cause pellets to stick. The properties of fluxed pellets were compared with the properties of iron ore lump and pellets, which are being used in blast furn...

Journal of Mining and Metallurgy, Section B: Metallurgy, 2020
The present work demonstrates the extraction of nickel from low-grade chromite overburden by usin... more The present work demonstrates the extraction of nickel from low-grade chromite overburden by using solid state reduction and direct smelting route. Goethite & Quartz are present as major phases whereas chromite, hematite were identified as minor phases in the mineral. Solid state reduction of pellets were carried out inside a horizontal tube furnace at 1000?C, 1200?C, 1400?C for 30, 60, 90 and 120 minutes respectively with creating reducing atmosphere. Pellets of varying basicity (i.e. 0.5, 0.6, 0.7, 0.8 and 0.9) were used directly in the EAF for smelting studies. Highest percent of nickel (2%) having ~ 91% recovery were obtained in solid state reduction route for pellets which was reduced at 1400?C for 120 minute. Similar recovery (~90%) of nickel was obtained inside the ingot (0.67% Ni ) by using pellets of 0.9 basicity through smelting route. From the present investigation, it could be concluded that the solid state reduction as well as smelting routes are feasible for the recove...

International Journal of Science and Engineering, 2013
The present study deals with the utilization of fines generated from comminution process (crushin... more The present study deals with the utilization of fines generated from comminution process (crushing, grinding and screening) of the Run of Mines into value added products i.e. fluxed iron ore pellets. The study comprises to understand the physical and mechanical behavior of five distinguished chemical compositions of green and dried iron ore pellets with respect to a typical Mini Blast furnace (MBF) burden data and furnace operating parameter. The maximum basicity of pellets was calculated 2.37 to make slag neutral when blast furnace runs at 100% high ash coke (avg. ash content= 29%). The crushing strength and drop number of various green pellets were measured. Green Crushing Strength was decreased with increasing lime fines. The addition of lime fines as a burnt lime, which has acicular structure creates less plasticity and brittle like fracture occurred. Due to formation of hard CaCO3 layer on the surface, after increasing lime contain crushing strength was increased in the air and oven dry pellets with respect to acid pellet (0% lime fines addition).

Utilization of fly ash can reduces the solid waste disposal problem and minimization of pollution... more Utilization of fly ash can reduces the solid waste disposal problem and minimization of pollution also. Conventional production of bricks usually utilizes clay and shale as the source material and requires high temperature (900– 1000 °C) kiln firing which is energy intensive, adversely affect the landscape, and can release high level of waste materials. Utilization of fly ash for making lime activated bricks not only give the waste utilization but also save earth shale as well as energy consumption and CO2 emission. The present study deals with the utilization of fly ashes for making lime activated fly ash bricks and their different property characterization after a normal water curing method up to 21 days. The crushing strength was observed 2.02, 3.17 and 5.32 MPa for 7, 14 and 21 days curing respectively. On the other hand apparent porosity and water absorption was observed 52, 52 , 50 and 46, 47 and 43% for 7 , 14 and 21 days curing respectively. The SEM-EDAX analysis was observe...
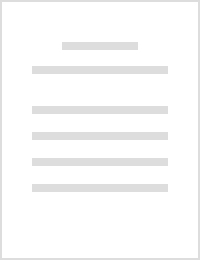
Materials Today: Proceedings, 2021
Abstract Steel plants are the primary producer of solid waste materials like slags from blast fur... more Abstract Steel plants are the primary producer of solid waste materials like slags from blast furnaces and L.D. Plant with fly ash /bottom ash from the power plant, iron ore slimes from ore washing plant, coal/coke from coke ovens, etc. It is estimated that about 84% of total solid waste generation is in iron ore tailings (Fines/ Slimes), coal combustion residues (Fly Ash or Bottom Ash), and the remaining 16% constitute all others, including slag. The above wastes (Iron ore slime & Bottom ash/ Fly ash) are being used for landfilling and in few countries to get value-added products. However, the partial or bulk utilization of such waste is still an academic issue in India. The present paper reviews past and recent research work to utilize two significant unutilized waste (Iron ore slime & Bottom Ash). The promising areas for utilization of Iron Ore Slime and Bottom Ash are the making of bricks (constructional, insulation), use as bed filter materials, and Ferro / master alloys' production as a part of metal recovery using smelting reduction process. (e.g., Al, Si, etc.).
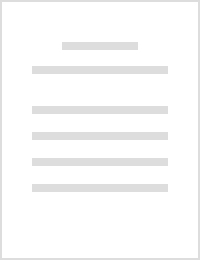
IEEE Transactions on Plasma Science, May 1, 2018
The extraction of metals like Al and Si from bottom ash having alumina and silica requires high t... more The extraction of metals like Al and Si from bottom ash having alumina and silica requires high temperature for their reduction. Only transferred arc plasma (TAP) furnace could meet this requirement. The TAP furnace was fabricated indigenously for performing experiments in laboratory based on the information available in the literature, related to the furnace design. The furnace was fully characterized for its smooth functioning by observing parameters like arc length, energy, and electrode consumption as well as the generation of sound level. It was found that the required temperature could be achieved by varying arc length, arc current, power rating as well as plasma gases. Arc length could be adjusted by varying power rating and changing voltage for required heat distribution above the melt. The accessories like the charge feeding system, gas purification and its flow system, gas exit system, the pouring system were worked satisfactorily. Sound level could be controlled by controlling arc current with the plasma gas. The thickness of lining was found sufficient to hold liquid metal either in graphite or magnesite crucible. Increased melt temperature (~200 °C) and ~10-dB lower sound level could be achieved by using nitrogen plasma as compared to the normal arc. But, hydrogen plasma produces more ~100 °C melt temperature, and ~5-dB sounds as compared to nitrogen plasma. Based on the results of the operational trial, it could be concluded that the TAP furnace was found to be a suitable tool for melting 2-kg iron and its various attachment were also found to be trouble-free operation.

Waste Management & Research, May 24, 2017
The issues of disposal and environmental problems are increased by the generation of bottom ash f... more The issues of disposal and environmental problems are increased by the generation of bottom ash from the thermal power plants day by day; hence, its recycling is required. The present study aimed to make thermal insulation blocks using as raw material bottom ash and iron ore slime as a binder and to characterize their engineering properties. Two different fineness values of bottom ash were considered with varying amounts of iron ore slime (0-10%) to make the blocks. Blocks were dried followed by firing at 1000, 1100 and 1200°C, respectively. Cold crushing strength, density and thermal conductivity of these fired blocks showed increasing behaviour with firing temperature, fineness of bottom ash and iron ore slime content. In contrast, a reverse trend was observed in the case of porosity. With increasing firing temperature, the formation of lower melting phases like iron silicate followed by iron aluminium silicate was observed, which imparts the strength inside the blocks. The coarser particles of bottom ash increase the interparticle spaces, which enhances the apparent porosity, resulting in higher thermal insulation property in the blocks. Blocks having better thermal insulation property could be possible to make effectively from coarse bottom ash by adding iron ore slime as a binder.

Waste Management & Research, Mar 29, 2018
Though the majority of research on fly ash has proved its worth as a construction material, the u... more Though the majority of research on fly ash has proved its worth as a construction material, the utility of bottom ash is yet questionable due to its generation during the pulverized combustion process. The bottom ash produced during the fluidized bed combustion (FBC) process is attracting more attention due to the novelty of coal combustion technology. But, to establish its suitability as construction material, it is necessary to characterize it thoroughly with respect to the geotechnical as well as mineralogical points of view. For fulfilling these objectives, the present study mainly aims at characterizing the FBC bottom ash and its comparison with pulverized coal combustion (PCC) bottom ash, collected from the same origin of coal. Suitability of FBC bottom ash as a dike filter material in contrast to PCC bottom ash in replacing traditional filter material such as sand was also studied. The suitability criteria for utilization of both bottom ash and river sand as filter material on pond ash as a base material were evaluated, and both river sand and FBC bottom ash were found to be satisfactory. The study shows that FBC bottom ash is a better geo-material than PCC bottom ash, and it could be highly recommended as an alternative suitable filter material for constructing ash dikes in place of conventional sand.

Journal of Cleaner Production, Sep 1, 2017
The fly ash (FA) and red mud (RM) are the primary solid waste produced in the aluminum plant. Pre... more The fly ash (FA) and red mud (RM) are the primary solid waste produced in the aluminum plant. Present work investigates the possible utilization of these wastes for preparation of insulation bricks by blending different proportion of their mixture with sawdust. Study of the effect of varying FA:RM ratio, firing temperature (T f) and sawdust blending on the physical properties of bricks has been carried out. Bricks having 60:40 ratio of FA:RM were found to possess maximum strength independent of T f. It showed that higher firing temperature increases the strength of bricks. The blending of sawdust improves the porosity and the thermal insulation properties of the bricks. Bricks fired at 1100 C and made by blending of minimum 7.5% saw dust, with 40% red mud in fly ash fulfills the criterion of 'Type-A' insulation brick as per IS:2042 standards. These bricks are suitable for insulation in the ambiance having low to medium temperature (up to 600 C) applications.
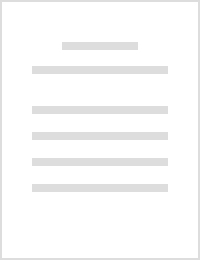
The Journal of solid waste technology and management, May 19, 2017
Red mud from primary aluminium extraction plants creates environmental pollution due to improper ... more Red mud from primary aluminium extraction plants creates environmental pollution due to improper method adaptation in larger scale utilization. The aim of the present investigation was to utilize these wastes for making geopolymer sample with the help of bottom ash to replace sand and also to examine the strength development with the addition of gypsum. Bricks were made with different finenesses of bottom ash and cured in water. Variation in strength, water absorption , and bulk density was determined by variation of red mud-bottom ash ratio, fineness of bottom ash and curing time. Results showed increased strength properties with increasing bottom ash, curing time and fineness up to 30% bottom ash. More red mud content decreased the available silica and alumina content, needed for the polymerization reaction, resulting in a reduction in bricks' strength. The maximum compressive strength 7.56MPa was achieved at 28 days of curing at red mud-bottom ash ratio of 55:30 for fine bottom ash bricks. Obtained results were correlated with the results of previous work and it was concluded that red mud could be polymerized to quite a larger amount with the addition of bottom ash, gypsum for getting comparable properties with those of the commercial materials.
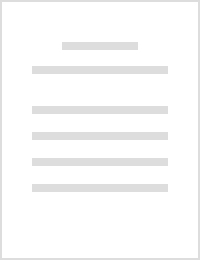
Journal Of The Institution Of Engineers (india): Series A, Dec 1, 2014
ABSTRACT India focuses on attention towards “greener and cleaner” environment surrounding us. For... more ABSTRACT India focuses on attention towards “greener and cleaner” environment surrounding us. For that, the engineers and scientists have joined hands together to accept the challenges for recycling wastes from industries. The generation of Bottom Ash (BA) from thermal power plants which are being increased day by day and facing disposal and environmental problems. In spite of that, it is being used as landfills which has no commercial value, but now needs to think on its utilization as useable supplementary materials. But from the literature survey, it was found that a little amount of research have been carried out on BA in the area based on its adsorption capability of dyes; pelletization efficiency of cold bonded aggregate; compressive strength, durability, water absorption characteristics and density variation in concrete and mortar; in order to ensure its usage as adsorption as well as construction material. The present paper deals with a critical review on BA as an adsorbent, light weight aggregate as well as partial replacement of fine aggregate in concrete. In addition, physical and chemical properties, transportation and disposal mechanism and environmental effects are also discussed.
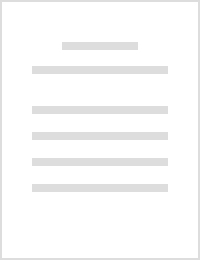
Journal of Sustainable Metallurgy, May 10, 2017
The present paper deals with the effect of charge material on the recovery of aluminum from the i... more The present paper deals with the effect of charge material on the recovery of aluminum from the industrial solid waste. For the efficient recovery of aluminum metal having a lower vaporization temperature, smelting was carried out in the presence of metal (iron) solvent bath inside a graphite crucible. Nitrogen plasma arc was generated by passing the current as well as the nitrogen gas through a hollow graphite electrode. Charge containing bottom ash or a mixture of iron ore slime and bottom ash along with a reductant of different reactivity was used either in the form of powder or pellets. Liquid iron bath below the plasma arc zone was utilized as a solvent for the absorption of reduced metals after reduction of the oxides present in the wastes. The quick absorption of aluminum in the liquid iron bath subsequent to the reduction of oxides under an inert atmosphere minimized the vaporization loss of aluminum. The effects of carbon content and its reactivity, form of charge material, charge-layer thicknesses for different charge compositions on the recovery of aluminum were studied for 30 min of plasma exposure times in all cases. Maximum recovery of aluminum was found for the charge in powder form having a mixture of bottom ash and iron ore slime along with the increased carbon content as well as charge-layer thickness, respectively. The recovery of aluminum was found to be up to 40.80% for the powder charge containing 50% bottom ash and 50% iron ore slime with the char in double stoichiometry carbon.
Journal of Materials in Civil Engineering, Apr 1, 2017
AbstractThis paper presents experimentally investigated results of iron slime addition as additiv... more AbstractThis paper presents experimentally investigated results of iron slime addition as additives in making bottom ash bricks. Bottom ash from coal burning thermal power stations of two different...

Plasma Science & Technology, Jan 23, 2018
The utilization of industrial solid waste for metal recovery requires high-temperature tools due ... more The utilization of industrial solid waste for metal recovery requires high-temperature tools due to the presence of silica and alumina, which is reducible at high temperature. In a plasma arc furnace, transferred arc plasma furnace (TAP) can meet all requirements, but the disadvantage of this technology is the high cost. For performing experiments in the laboratory, the TAP was fabricated indigenously in a laboratory based on the different inputs provided in the literature for the furnace design and fabrication. The observed parameters such as arc length, energy consumption, graphite electrode consumption, noise level as well as lining erosion were characterized for this fabricated furnace. The nitrogen plasma increased by around 200 K (200°C) melt temperature and noise levels decreased by ∼10 dB compared to a normal arc. Hydrogen plasma offered 100 K (100°C) higher melt temperature with ∼5 dB higher sound level than nitrogen plasma. Nitrogen plasma arc melting showed lower electrode and energy consumption than normal arc melting, whereas hydrogen plasma showed lower energy consumption and higher electrode consumption in comparison to nitrogen plasma. The higher plasma arc temperature resulted in a shorter meltdown time than normal arc with smoother arcing. Hydrogen plasma permitted more heats, reduced meltdown time, and lower energy consumption, but with increased graphite consumption and crucible wear. The present study showed that the fabricated arc plasma is better than the normal arc furnace with respect to temperature generation, energy consumption, and environmental friendliness. Therefore, it could be used effectively for smelting-reduction studies.
Journal of the institution of engineers (India) series D, Jul 24, 2023
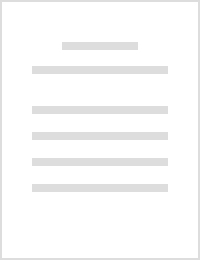
Canadian Metallurgical Quarterly, Mar 3, 2022
The preparation of finer iron ore particles which can be used suitably in pelletization, decrease... more The preparation of finer iron ore particles which can be used suitably in pelletization, decreases the binder requirement in the process, but increases the energy consumption during crushing and ball milling. Therefore, using relatively coarser iron ore particles with a suitable binder may help decrease energy input and slag volume. The present study was undertaken for the utilisation of iron ore fines in the range of −0.25 + 0.05 mm along with a suitable binder. Iron ore fines were classified into three size ranges (SR1(−0.25 + 0.1), SR2(−0.1 + 0.05) and SR3(−0.05)mm). Pellets of the above material were prepared using lime as a binder for basicity 0, 1 and 2 respectively, to observe hardening and reduction behaviour. Hardened pellets were characterised using cold crushing strength and porosity. Reduced pellets were characterised using XRD and SEM. It was observed that the cold crushing strength of hardened fluxed pellets decreased from 222 to 12 kg/pellet, and porosity increased from 30 to 43% with an increase in selected particle size. % Reduction increases from 89 to 99% with an increasing iron ore particle size. X-ray diffraction and scanning electron microscopy study confirms the increase in Fe content and iron whiskers growth in reduced pellets with increasing particle size. The optimum property was observed for the SR2 size range with the lime binder, which can produce highly reducible DRI (90-99%).

India as a 4th steel producer in the world has resulted due to adaptation of new technologies in ... more India as a 4th steel producer in the world has resulted due to adaptation of new technologies in the field of iron and steel making since from the last few decades. Keeping in view for increasing quality of hot metal and its production rate, efficiency of the furnace operations with keeping clean environment, adaptation of few newer technologies and practices in the area of Blast Furnace iron making are selected for this paper. Selected areas are described with salient features such as burden preparation including different raw materials such as iron ore, coke, lime stone, sinter/pellets etc, burden distribution including bell less top charging design, furnace structure design, cast house design and practice with multi tap-hole and runner, furnace cooling system design changes with staves cooler, use of carbon refractory materials in hearth lining, hot blast quality improvement, efficiency enhancement of gas cleaning system, automatic process control and taking care of environmental...
Uploads
Papers by Dr. Arup Kumar Mandal
Results of Cold Crushing Strength and porosity of fired bricks show increasing and decreasing behavior respectively with increasing firing temperature, fineness of BA and IS content. SEM micrograph shows pores structure for coarse BA bricks as well as presence of low melting constituents inside the bricks. XRD analysis of 1000°C fired bricks revealed that the formation of minor amount of calcium silicate, aluminium silicate and also magnetite. With increasing firing temperature, the formation of iron silicate followed by iron aluminium silicate occurred which imparts the strength inside brick. Maximum Cold Crushing Strength of 165.29 Kg/cm2 was achieved for bricks having Coarse BA: Fine BA =1:3 with 10%IS , fired at 1200 °C, whereas maximum porosity was achieved upto 45.8 % having 0% IS ,fired at 1000°C. However, the optimum strength having comparable porosity (33 to 32%) was achieved 56 to78 Kg/cm2 in the product made at 1200°C, having Coarse BA: Fine BA =1:1 ratio with 5-10% IS addition.
The present investigation examines the improvements in strength of lime–FA-RM bricks through low temperature steam curing along with additives like gypsum. Results of strength, water absorption relationships were observed with the variation of RM-FA ratio, addition of coarse aggregate, different curing methods and time. The characterization of the unfired bricks thus produced was carried out by XRD and SEM analysis. The test results reveal that strength increases with increase in coarse aggregate addition and curing time. It was also observed that increasing RM content gradually increases the strength of bricks .The maximum strength of 6.30 MPa was achieved at a RM–FA ratio of 45:40 in the water curing of 28 days. Steam curing at 800C was observed to decrease the curing time in 24 hours and could achieve a good strength of 4.41 MPa. After increasing the RM content, the available SiO2 content needed for polymerization reaction decreases resulting in reduction in bricks strength. The best results after 28 days of water absorption at ambient temperature was found at RM-FA ratio of 45:40
1. B. V. V. Reddy and K. Gaurav, Materials and Structure, 44 (2011), p.1793.
2. J. M. Sharma, Ph.D. (Met. Engg.) Thesis, Banaras Hindu University, Varanasi, India (1990).
3. J.E. Oti , J.M. Kinuthia , Applied Clay Science, 58 (2012), p. 52