Papers by Natalia Smetankina
Lecture notes in networks and systems, 2023
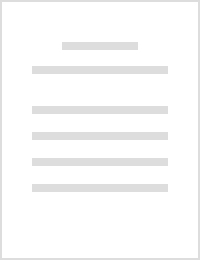
2020 IEEE KhPI Week on Advanced Technology (KhPIWeek), Oct 5, 2020
A method for calculating non-stationary temperature fields in a non-closed cylindrical multilayer... more A method for calculating non-stationary temperature fields in a non-closed cylindrical multilayer shell with a complex shape when exposed to film heat sources is offered. The shell with constant thickness isotropic layers and various physical properties is considered. The number of layers and their layout is arbitrary. Convective heat exchange occurs on the shell surfaces. The shell is affected by interlayer heat sources. The non-stationary heat conduction equation and the boundary conditions for the multilayer shell are derived from the heat balance variational equation. The temperature fields are determined while solving the nonstationary heat conduction problem for multilayer shells when the latter are heated with interlayer film heat sources. Distribution of temperature along each layer is presented by means of the Legendre polynomials. The problem is reduced to integration of a system of differential equations by modified Taylor's method. As an example, the problem of non-stationary thermal conductivity for a five-layer glazing element of an aircraft when heated with a film heat source has been solved.
International Journal of Solids and Structures, Apr 1, 1995
ABSTRACT A refined theory is used for investigating the strain-stressed state (SSS) of multilayer... more ABSTRACT A refined theory is used for investigating the strain-stressed state (SSS) of multilayer plates under impulse and impact loading. The theory takes into account the transverse shear strains in each of the layers. The broken line hypothesis holds true for a package. Experimental determination of the SSS is based on the dynamic wide-range strain measurement technique. The numerical results obtained are compared with experimental data.
Lecture notes in networks and systems, 2023
Springer eBooks, Nov 29, 2022
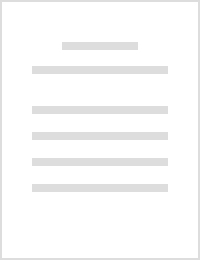
2021 IEEE 2nd KhPI Week on Advanced Technology (KhPIWeek), Sep 13, 2021
The problem of minimizing the mass of layered orthotropic constant-thickness non-closed shells at... more The problem of minimizing the mass of layered orthotropic constant-thickness non-closed shells at impulse loading is solved. The shell behavior is described within the framework of the improved theory. According to the extension method, the complex-shape shell can practically be extended to an auxiliary layered cylindrical non-closed simply supported rectangular-shape shell with the same composition of layers. An auxiliary shell is a body whose contour shape and boundary conditions yield a simple analytical solution. In this case, the auxiliary shell is a simply supported non-closed cylindrical layered one with a rectangular plan-view shape, making it possible to find the problem solution as a trigonometric series. To meet the specified boundary conditions, we apply compensating loads to the auxiliary shell. The adaptive optimization method with hybrid elements is applied to solving the problem of optimal shell design. The effect of the geometrical parameters on the optimum design of a two-layer composite shell is investigated. In addition, extremums corresponding to optimum shells and plates are found.
DOAJ (DOAJ: Directory of Open Access Journals), Apr 1, 2018
AIAA Journal, Aug 1, 1996
ABSTRACT The statement and the solution of the problem of optimal synthesis of a multilayer plate... more ABSTRACT The statement and the solution of the problem of optimal synthesis of a multilayer plate with a minimal mass at impulse loading is offered. The optimization method is represented by a hybrid search method with adaptive control of the extremum search process The multilayer plate is described by equations of the refined theory considering transverse shear. The hypothesis of a broken line holds true for a pack of layers. Numerical examples of optimization are given.
International Journal of Impact Engineering, Feb 1, 2007
The paper presents an analytical approach to investigating vibrations of an elliptic plate upon i... more The paper presents an analytical approach to investigating vibrations of an elliptic plate upon impact with an indenter having a hemispherical end. The approach is based on expanding the sought for functions to trigonometric series. The dynamic behaviour of the plate is described in terms of the Timoshenko-type theory that accounts for transverse shear strains and rotary inertia of the normal. Cases of impact in the plate focus and centre have been investigated. Theoretical results are in good agreement with experimental data obtained by using the dynamic wide-range strain measurement technique.

Lecture notes in networks and systems, Jul 28, 2021
Using an adhesive to join radiotransparent radomes with the cutout edging in the skin or with the... more Using an adhesive to join radiotransparent radomes with the cutout edging in the skin or with the airframe has several advantages as compared to other kinds of joining. Adhesive joints are maintainable, airtight, and their weight is small and the aerodynamic efficiency is high. Known analytical models enable finding the stress state of rectangular joints, in which the stresses are distributed uniformly across the joint width. The objective of the paper is to investigate the axisymmetrical stress state of the adhesive joint of a circular plate with a rigid edging. The plate is subjected to uniform pressure across the surface. The adhesive layer, functioning under shear and cleavage, is considered as a Winkler elastic foundation. The edging and plate are assumed isotropic and are made of dissimilar materials with different thicknesses. The structure considered has two areas: the adhesive joint area and the area beyond the joint-the overlay on the cutout. The problem for the adhesive joint area is reduced to a system of two differential equations for tangential and cleavage stresses in the adhesive. The problem solution is built in analytical form. Unknown coefficients are found from boundary conditions and the conjunction conditions on the edges of the areas. The problem considered for the first time is the generalisation of the classical Goland-Reissner model of an adhesive joint for an area with radial symmetry. Computational results demonstrated a good agreement with finite element analysis calculations, indicating that the suggested mathematical model is adequate.
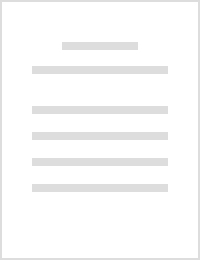
Journal of mechanical engineering, Sep 30, 2022
An experimental stand was created to study the thermobaric and chemical influence of hydrogen on ... more An experimental stand was created to study the thermobaric and chemical influence of hydrogen on the identification of hydrocarbon production. The said stand allows to reproduce chemical-technological processes as close as possible to real formation ones. This stand makes it possible to study the kinetics of not only hydrogen, thermobaric and chemical effects, but also other thermal gas chemical processes, including hydrogen generation. The main element of the experimental stand is a hydrogen generator, the components of which work at high pressures and temperatures under conditions of hydrogen embrittlement of mechanical properties and an aggressive environment that causes corrosion of its inner surface. Based on this, the development of a methodology for calculating the thermal stress state of the generator, its strength under hydrogen embrittlement conditions, and its resource becomes relevant. Based on the finite element method, a methodology for calculating non-stationary temperature fields and the thermal stress state that occur in the hydrogen generator during thermobaric and chemical processes of varying intensity is proposed. The methodology allows to take into account the features of the geometry of the structure, the time-varying temperature and pressure distributions of the reaction products, the temperature dependence of the thermophysical and mechanical properties of the hydrogen generator material. Thanks to the application of the developed software, a study of the hydrogen generator thermal stress state during two real thermobaric and chemical processes of different intensity was carried out. Graphs of temperature and pressure changes of the reaction products of hydroreactive substances in the generator over time, which were registered during the experiment conduction, were used. The distribution of non-stationary temperature fields and stresses in the hydrogen generator elements was obtained. Areas of maximum load of generator elements are defined. It was established that during the flow of the studied thermobaric and chemical processes, pressure makes a greater contribution to the thermal stress state. The obtained results and the developed theory and software can be used in the study of generators of other designs with other thermobaric and chemical processes occurring in them.

Prikladnì pitannâ matematičnogo modelûvannâ, 2019
The article is devoted to the investigation of the response of a multilayer glass to speed impact... more The article is devoted to the investigation of the response of a multilayer glass to speed impact by an axisymmetric solid. The glazing of the aircraft has a multilayer structure, the carrier layers of which are made of silicate and organic glass, polycarbonate, which are joined together by bond layers. Such structure allows to provide a smaller structure weight with account all requirements to structure strength. The purpose of the work is to create a calculation method for assessing strength of the multilayer aviation glass when interacting with the impactor simulating a ball. The method includes an algorithm for determining dynamics of the impactor penetration into a multilayer glass. The differences in the breaking of fragile and plastic material are analyzed. When impact by a thin-walled homogeneous structure, which is made of brittle material, as a result of the interaction of the straight and reflected deformation waves, the knocking of the so-called Hertz cone is observed. When punching a multilayer glass, the impactor knocks out these cones from the glass and pushes them in front of it. As a result, the pressure on the next layer until the destruction of the cone acts on a larger area, and the speed of the impactor decreases due to the involvement in the movement of additional weight from the knocked cone. The evaluation of bulletproof of multilayer glass is based on the analysis of penetration depth of the ball into the package and propagation process of deformation waves in a glass. To estimate the penetration depth of a impactor into a glass, an empirical relationship is used to calculate stresses on the contact surface of the impactor with an target, and to analyze wave propagation we use threedimensional equations with allowance for attenuation according to the Kelvin-Voigt model. The empirical dependence reflects the known determination of the value of media resistance as the sum of strength and inertial components. This addiction is complemented by a mechanism that describes the process of sequentially knocking out the Hertz cones and their involvement in motion. The test calculation of several compositions was made, which confirmed the approach efficiency. The proposed method can be applied to the calculation of bullet resistance of glazing of military and special vehicles.
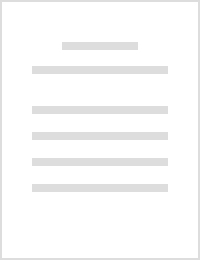
Journal of mechanical engineering, Jun 30, 2022
Ensuring the efficient and reliable safe operation of ground special equipment of various types, ... more Ensuring the efficient and reliable safe operation of ground special equipment of various types, aircrafts is an important and urgent problem. Preservation of the strength, protective properties and transparency of the glazing of machinery cabins in a wide range of temperatures under various strength influences is one of the key components of this problem. Multilayer packages made of different types of glass are used for special equipment glazing. These packages are connected to each other with adhesive polymer materials. Electrically heated glazing, which allows to avoid the special equipment icing, as well as to protect the viewing area from fogging, is used for reliable and failure-free operation of special equipment at low temperatures. Based on this, an important problem that affects the efficiency of the use of special equipment is to ensure the reliable operation of electric glass heating. With the help of a software package developed on the basis of the finite element method for the analysis of the structures thermal stress in 3D formulation, which allows to consider a wide class of practical problems of varying complexity, the problems of non-stationary and stationary thermal conductivity and thermal elasticity for a trapezoidal frontal electrically heated multilayer glazing are solved. A study of the thermal stress state of glazing with an electric heating system, which allows to avoid freezing of glass operating at low temperatures, was carried out. The reasons for which the delamination of the multi-layer glazing may occur (impermissible temperature modes, mechanical strength effects, violation of operating conditions) are determined. Multilayer glazing with an electric heating system is used for aircrafts, military equipment, land transport, which can be operated at different temperatures. In view of this, the study of their thermal stress state and determination of possible causes of delamination allows to ensure the operation reliability and increase the efficiency of the use of special equipment in different climatic conditions. It is planned to carry out further studies of the glass block thermal stress state taking into ac-count the thermostat operation and determining the temperature sensors location points, as well as changes in the physical properties of materials and the power of the heating element with temperature changes.
Springer eBooks, 2021
The problems of modeling the response of multilayer glazing to dynamic distributed and localized ... more The problems of modeling the response of multilayer glazing to dynamic distributed and localized force loading are considered. The dynamic behavior of glazing is described by equations of the layerwise generalized model that accounts for the spatial strain character and inertial loads. The stress distribution pattern is shown to be essentially nonlinear for localized loading. The response of flat glazing to a shock wave and to shocks caused by a solid, soft bodies and a bullet is considered. Computational results are compared to experimental data, as well as to those of similar computations by other investigators.
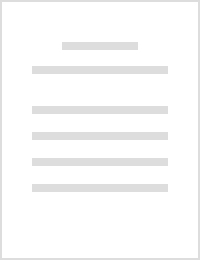
Journal of mechanical engineering, Sep 30, 2021
The safety of reliable operation of aircraft and their durability essentially depend on the stren... more The safety of reliable operation of aircraft and their durability essentially depend on the strength of the glazing, which is a critical structural element. There are a number of different requirements for glazing. To provide the necessary parameters, high-strength silicate glass is widely used, and special technologies for its strengthening are used. The analysis of the problem showed that the insufficient strength of aircraft glazing elements and the complexity of methods for monitoring the state of glass during production and operation due to the presence of microscopic surface defects, as well as the need for a reliable assessment of residual stresses, require that there be used new approaches and technical solutions for the development of modern technologies for creating structures. Ion exchange is one of the glass strengthening mechanisms, which makes it possible to reduce the negative effect of surface defects by artificially creating residual compressive stresses and reducing the thickness of the damaged layer. Computational studies, under bending strains, of the crack resistance of ion-exchange strengthened sheet glass were carried out using an in-house FEM-based software package developed to study the thermally stressed states of structures. The results obtained showed that the strength of real sheet glass fracture due to tensile stresses in bending is determined by crack-like surface defects. The creation of residual compressive stresses on the glass surface by ion exchange strengthening provides an increase in bending strength. With an increase in residual stresses and the depth of their distribution, the effect of ion-exchange treatment increases. If the depth of the zone of compressive stresses due to ion-exchange strengthening is much less than the depth of the surface crack, then the strength of the glass depends little on the maximum compressive stresses on the surface. The effect of ion-exchange strengthening increases significantly in the case of a decrease in the depth of the surface crack. The expediency of further research and comparison of calculation results with experimental data are shown. The developed technique will make it possible to solve important practical problems in studying the strength of the aircraft multilayer glazing and determining the optimal methods for eliminating defects.
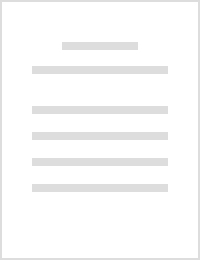
Lecture notes in mechanical engineering, Jun 7, 2019
A model was developed to simulate the process of a bird striking a rigid target. The target is a ... more A model was developed to simulate the process of a bird striking a rigid target. The target is a hinge-supported steel plate and, in the first approximation, it emulates aircraft structural components. The dynamic behavior of the plate is considered within the generalized model to allow for the spatial character of deformation of the structure. The method for solving the equation of plate motion consists in representing the solution as a double trigonometric series. The result is the transformation of the equation of motion to a system of ordinary second-order differential equations integrated by the solution expansion to a Taylor series. The model of a bird’s shock action on a plate was developed based on the experimental research. The influence of a plate’s angle of impact on the plate strain was studied for a bird-strike case. A comparison of theoretical results with experimental data showed their close fit. The suggested model of the process of a bird striking a plate is used for evaluating the strength of different aircraft components.

Strength of Materials, Nov 1, 2018
The method of strength calculations for laminated aircraft cockpit windows influenced by differen... more The method of strength calculations for laminated aircraft cockpit windows influenced by different operating factors (bird strike, pressurization) is devised. The method is based on embedding the initial uncanonical shell in the auxiliary one of canonical form in plan with the boundary conditions, which permit of a simple analytical problem solution as a trigonometric series. For satisfying the initial boundary conditions, the auxiliary shell is supplemented with compensating loads, which are continuously distributed over the contour of the initial shell. The compensating loads enter in the equations of motion for the auxiliary shell as integral relations. The system of motion equations is rearranged in the system of ordinary differential equations of second order, which is integrated by the solution expansion in the Taylor series. The windows are treated as a laminated open-ended cylindrical shell consisting of isotropic layers of constant thickness. The laminated window model is based on the modified theory of first order that accounts for transverse shear strains, thickness reduction, rotary inertia, and compression of the normal element in each layer. For the composition, the hypothesis of broken line is valid. The model of pressure pulse that apparently represents the effect of the bird impact on the windows was constructed on the basis of experimental studies. The stress-strain state of the window element in AN aircrafts was evaluated, set on the bird strike and cockpit pressurization. Five window alternatives are examined. Calculation results are in good agreement with experimental data. The results become theoretical and practical backgrounds for engineering calculations and optimum design of laminated aircraft window elements influenced by different operating factors. Thus, the advanced method can be applied to estimation of the lifetime of existing window elements and development of the new ones.
Springer eBooks, Nov 26, 2022
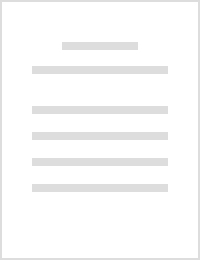
Вісник двигунобудування, 2019
The most optimal approach in the practical solution of the problems of the rocket structures stre... more The most optimal approach in the practical solution of the problems of the rocket structures strength is a combination of theoretical studies with their parallel verification by a correctly performed experiment. In this article a methodology and a calculation model have been developed and computer studies have been carried out for the inter-stage module of the Cyclone-4M launch vehicle during separation. The method of calculating the inter-stage module dynamics is based on the three-dimensional finite element method with the solution of the problem in time by the Wilson finite-difference method. The applied methodology and model for calculating the dynamic stress-strain state of the inter-stage module take into account the main features of the structure and loading,that determines the adequacy of modeling and strength and stiffness estimates. All the main strength elements are represented in the design model of the inter-stage module,namely,the shell,longitudinal and transverse reinforcements systems by the stringers and frames. The virtual mass of the discharged first stage and the eccentricity pneumatic pushers’ action are taken into account in the model. Two finite element models with different discretization – initial and refined – were used in the calculations. The refined model is associated with greater discretization of the design of the inter-stage module in the vicinity of the areas of application of loads – pneumatic tappets brackets. The calculated data are presented by the results of three studies – natural vibration frequencies and mode shapes,estimates of the stress-strain state under static loading with the maximum possible load and calculations of the vibration process. The duration of pneumatic pushers is much longer than the period of fundamental tone natural vibrations. This determines the quasi-static behavior of the inter-step module deformation. Dynamic stresses in the inter-stage module are very limited and have a localized character near the brackets of pneumatic pushers. The inter-stage module load-carrying capability can be increased by reinforcing the airframe in the pneumatic pushers’ holder area.
Uploads
Papers by Natalia Smetankina
Багатошарове оскління розглядається як прямокутна багатошарова пластина, яка зібрана з ізотропних шарів сталої товщини. На бічній поверхні пластини підтримується нульова температура. На зовнішніх поверхнях відбувається конвективний теплообмін, а на границях контакту шарів розташовані плівкові джерела тепла.
Рівняння нестаціонарної теплопровідності для довільного шару пластини після перетворення Лапласа за часом зводиться до операторного рівняння. Так само перетворюються початкові і граничні умови. Розв’язок операторного рівняння шукаємо у вигляді добутку трьох функцій від просторових координат, що дозволяє перейти до системи звичайних диференціальних рівнянь. Розв’язок цієї системи можна записати у вигляді подвійного тригонометричного ряду з урахуванням граничних умов на бічній поверхні пластини. Коефіцієнти розвинення у ряд визначаються з системи лінійних алгебраїчних рівнянь, яка формується з граничних умов на зовнішніх поверхнях та границях контакту шарів. Права частина системи містить коефіцієнти розвинення функцій міжшарових джерел тепла. Після визначення коефіцієнтів оригінал шуканої функції знаходиться за другою теоремою розкладання, а розв’язок задачі має вигляд подвійного тригонометричного ряду.
Як приклад розв’язана задача нестаціонарної теплопровідності для п’ятишарового
елемента оскління літака при нагріванні плівковим джерелом тепла. Джерело має прямокутну форму і розташоване між першим та другим шарами елемента оскління. Проведено порівнювальний аналіз розподілу температури вздовж товщини елемента з результатами, одержаними іншими методами.
Запропонований підхід може бути використаний при проектуванні безпечного багатошарового оскління різних транспортних засобів в умовах експлуатаційних та аварійних термосилових навантажень.