Papers by Bipul Chandra Mondal

Pipelines are extensively used as the most economic means of transporting oil and gas. The steel ... more Pipelines are extensively used as the most economic means of transporting oil and gas. The steel pipelines have been widely used for these applications due to the high strength to weight ratio of the material, resulting in lower material cost. These pipelines are subjected to corrosions during the service life, resulting in the reduction of wall thicknesses. The prediction of the remaining strength of a corroded pipeline is required for fitness-for-purpose assessment. For the prediction of the remaining strength, different models were developed based on simplified results of analysis and/or empirical fits to limited experimental data which are expressed in terms of burst pressure. The established design codes adopt simplified design equations for the burst pressure prediction for corroded pipelines. However, the burst pressures predicted using the simplified equations are not consistent with the burst test results and results obtained from rigorous finite element (FE) analyses. Besi...
Thin-Walled Structures, 2022
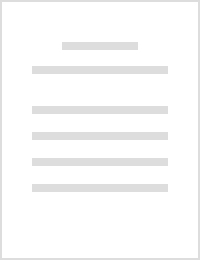
Engineering Failure Analysis, 2019
Abstract In the conventional method of analysis for the remaining strength assessment of a corrod... more Abstract In the conventional method of analysis for the remaining strength assessment of a corroded pipeline, von Mises failure criterion is used. This continuum-based modelling approach is unable to assess the cracking of the pipeline. In this study, a fracture mechanics approach is used for the assessments of burst pressures of pipelines with corrosion only defects, pipelines with crack-like defects and pipelines with crack-in-corrosion defects. The fracture mechanics approach with the J-integral was found to simulate successfully the burst pressures obtained from rapture tests of pipelines with corrosion only defects and crack-in-corrosion defects. The conventional von Mises stress-based approach and design equations can reasonably be used for predicting the burst pressures of pipelines with corrosion only defects. However, the fracture mechanics approach is required for pipelines with crack-like defects and crack-in-corrosion defects. A parametric study is presented with calculations of the J-integrals for pipelines with crack-in-corrosion defects for various crack depths and crack lengths.
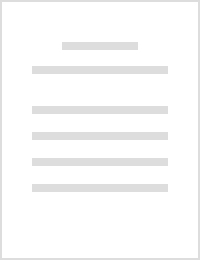
Engineering Structures, 2019
Abstract The remaining strength of corroded pipeline is generally assessed considering the intern... more Abstract The remaining strength of corroded pipeline is generally assessed considering the internal pressure only. However, pipelines are often subjected to axial forces and bending moments due to external loadings, which may significantly reduce the burst pressure of the pipeline. This paper presents a study using finite element analysis on the effects of axial forces and bending moments to the burst pressures of corroded pipelines. It is revealed that the compressive axial force and the closing bending moment, causing compression in the corroded area, affect the burst pressure most significantly. Considering the axial compression and closing bending moment, failure loci of combined bending moments and internal pressures are developed for different axial forces. The developed failure loci can be used for assessing the burst pressure of corroded pipelines subjected to axial forces and bending moments.
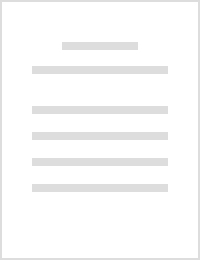
Journal of Pressure Vessel Technology, 2017
Burst pressure models are used for the fitness-for-purpose assessment of energy pipelines. Existi... more Burst pressure models are used for the fitness-for-purpose assessment of energy pipelines. Existing burst pressure models for corroded pipelines are unable to predict the pipe capacity correctly. In this paper, an improved burst pressure model is developed for corroded pipelines considering the burst pressure of flawless pipes and a reduction factor due to corrosion separately. The equation for the burst pressure of flawless pipe is revised based on the theory of the thick wall cylinder. A new model for the Folias factor is proposed for calculating the reduction factor. The new model for the Folias factor incorporates the depth of corrosion defect, whereas the existing models do not account for the effect of the defect depth. The authors' earlier work revealed that the Folias factor depends on the depth of defect. The proposed burst model reasonably predicts the burst pressures obtained from finite element (FE) analysis conducted in this study and the burst test results availabl...
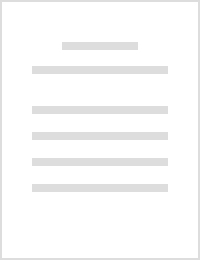
Journal of Pressure Vessel Technology, 2016
Codes/standards have been developed to calculate accurately the burst pressure for corroded pipel... more Codes/standards have been developed to calculate accurately the burst pressure for corroded pipelines. Five burst pressure models are evaluated in this paper using three-dimensional finite-element (FE) analysis. The finite-element models are validated using burst test results available in the literature. The design codes/standards are found to calculate variable burst pressures with respect to the finite-element calculations and the laboratory test results. The variability in the calculated burst pressures is attributed to the use of different flow stresses for the material and different burst pressure reduction factors for the corroded geometry. The Folias factor is considered as the major parameter contributing to the burst pressure reduction factor. Three different equations are currently used to calculate the Folias factor in the design codes that are expressed in terms of l2/(Dt). However, the finite-element evaluation presented here reveals that the Folias factor also depends ...
Volume 5A: Pipeline and Riser Technology, 2015
Today's construction robots are largely machines which simply carry out a construction task. Full... more Today's construction robots are largely machines which simply carry out a construction task. Fully robotised construction must include automation and integration of the numerous management functions together with robotisation of the construction task. Important management functions, including planning, scheduling and budgeting , are discussed with a view to their automation using powerful microcomputers. These functions are shown to be suitable for automation using artificial intelligence techniques and the subsequent integration of these automated functions into a robotised construction project system is proposed.

Pipeline with multiple corrosion defects are often observed in the field. The strength of pipe wi... more Pipeline with multiple corrosion defects are often observed in the field. The strength of pipe with multiple corrosion patches depends on the corrosion patch intensity, their locations along longitudinal and circumferential directions of the pipe, in addition to the parameters influencing the strength of pipe with single corrosion defect. The existing design codes recommend the spacing between the corrosion patches when the interacting corrosion patches can be considered as a single patch for calculating the burst pressure of the defected pipe. In this paper, the strength and deformation characteristics of corroded pipe are investigated using finite element analysis. The parameters considered in the analysis are pipe geometries, number of corrosion patches, spacing between multiple corrosions, edge conditions (e.g. sharp and elliptical edges) and the locations of the corrosion patches. The spacing of the corrosion patches are varied along the pipe length and pipe circumference with ...
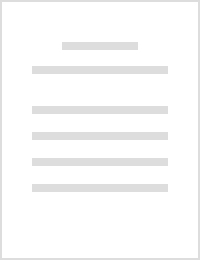
Canadian Journal of Civil Engineering
The strength of pipeline with multiple corrosion patches depends on the number of corrosion patch... more The strength of pipeline with multiple corrosion patches depends on the number of corrosion patches within an area on the pipe surface, the locations of corrosion patches along the longitudinal and circumferential directions of the pipe. In this paper, the strength and deformation characteristics of corroded pipeline are investigated using finite element analysis. Pipes with different diameters and different depths of corrosion patches are considered. The spacing of the corrosion patches is varied along longitudinal, diagonal, and circumferential directions of the pipes. The study shows that the limiting spacing for interaction of corrosion patches depends predominantly on pipe wall thickness, corrosion depth, and the location of the defects. The diameter of the pipe has some influence on the interaction for large diameter pipes. A new interaction rule for the limiting spacing for interaction is developed for longitudinally spaced corrosion patches. For circumferentially spaced corr...
Canadian Journal of Civil Engineering, 2017
Uploads
Papers by Bipul Chandra Mondal