Papers by Zamzam Elsharif

Science and Technology Publishing (SCI &TECH), 2020
This paper presents experimental study about design and manufacturing of the boat. Experimental s... more This paper presents experimental study about design and manufacturing of the boat. Experimental study was based on (Damen shipyards-Stan Tender 1550: Length o.a. is 16.25m, Beam o.a. is 4.55m, Depth at sides is 2.49m, and Draught aft(approx.) is 1.40m) as module with some slightly changing in the external shape of the boat. Manufacturing technique by method Lay-up of composite material. The composite manufacturing material was fiber glass woven roving (Type E) at with polyester resin. The boat was made from swedish wood (Type :SS-EN 1611-1/G4-2) with designed dimensions for factor 1: 39.625 which were (length is 400mm, depth at sides is 61.70mm, width is 102.21mm, thickness is 5.678mm, and draught is 27.26mm) and then has warped material inter and around it after wetting it in polyester resin to obtain the required thickness. Solid work program (CATIA V5) was applied to design of the boat as views and prismatic. Also, manufactured materials (wood and fibers). In addition, the boat has been operated by small motor as perfected applying. According to studying for scientific useful from information about high good mechanical properties of composite materials as resistance of corrosion and resistance different temperatures in hot and cold specially at sea water, and some another environment such as oceans and seacoasts. Also, stiffness, ideal plastic behavior…etc, can be used of supporting swedish wood in industry as invented methods for low cost rather than metals and another materials which use in boat industry that they have been high cost.
Science and Technology Publishing (SCI &TECH), 2020
This paper presents an experimental study of a composite material for comparative some mechanical... more This paper presents an experimental study of a composite material for comparative some mechanical properties of types the E-glass. The experimental study based on manufacturing techniques by lay-up was develop to evaluate strength stress, hardness, toughness, and stressstrain characteristic for composite material. The composite manufacturing material was fiber Eglass of woven roving at [(0°)⁄((90°)⁄(±45°))]_s , [±30°/±60°]_s and chopped mat reinforced with polyester resin. All the manufacturing specimens were conducted to mechanical tests such as tensile test, Reckwell's hardness test and impact test.

Science and Technology Publishing (SCI &TECH), 2023
This paper presents theoretical studying about simulation between application finite element anal... more This paper presents theoretical studying about simulation between application finite element analysis program (FEA) with previous results and data about defected damaged area of module steel pipes. Experimental studying was based on previous papers and books [1,2] that were discussion the module which was simulated as circular corrosion crack at the middle of the pipes which were made from carbon steel (Steel-No DIN10421) with internal diameter of 83 mm, thickness 12.5 mm and length of 900 mm .The damaged area of circular was simulated at diameters 5,10,15 mm, and 20 mm for the four pipes respectively[1,2]. Also, manufacturing composite material was used of repair the fiber glass woven roving (type E) at [0°/90°/〖±45〗^° ]_s reinforced with polyester resin. A carbon steel bolted clamp was used to clamp the pipe around the defected holes to minimize the delamination effect and stop the leakage of water during the tests of the pipes [1,2]. The finite element analysis program: CATIA V5 based on apply inner pressure about defected damaged area at diameter 10 mm of pipe to evaluate the deflection, failure pressure (blister pressure) and stress-strain curves.
It has fund that good correlations between the finite element analysis (FEA) of redial strain with previous studying curves at stages of loading of pressure. Also, observed the finite element analysis (FEA) curve was lowest radial strain of failure comparing with previous studying curves of crack length 10 mm at 957.730 με while highest radial strain was theoretical model radial strain at 1389.430με of pressure. According to studying the experimental curve and the finite element curve exhibited the non-linearity only in the early stages and then became linear up to failure.The finite element analysis (FEA) curve was highest radial stress of failure comparing with previous studying curves of crack length 10 mm at 46.541 MPa while radial stress of previous studying were 32.6941 MPa. Good correlation between the finite element analysis (FEA) and theoretical model of blister deflection. The finite element analysis (FEA) was higher of blister deformation then theoretical model 22.9490 μm and 6.7014 μm respectively. Finally, The maximum blister deflection occurs at the centre of the hole ( crake length 10 mm) by finite element analysis (FEA).

Science and Technology Publishing (SCI &TECH), 2023
ــــ ــــThis paper presents theoretical studying for comparing with previous results and dat... more ــــ ــــThis paper presents theoretical studying for comparing with previous results and data about defected damaged area of two modules with new designing model (ZAMZAM MODEL)[1-3]. Two modules were simulated as circular and rectangular corrosion cracks at the middle of the pipe which was made from carbon steel with internal diameter of 83 mm, thickness 12.5 mm and length of 900 mm. The damaged area of circular was simulated at diameters 5,10,15 mm, and 20 mm for the four pipes respectively[2,3]. While rectangular was simulated at dimensions (5×10),(7×14) and (9×18) mm for the three pipes respectively [3,4]. The new designing model based on the fracture mechanics techniques were developed to evaluate the deflection, failure pressure (blister pressure) and stress strain curves for damaged area. The damage was simulated as a square at the middle of the pipe at dimensions (5×5),(7×7) and (9×9) mm for the three pipes. According to results, good correlation between the theoretical models (ZAMZAM MODEL) and fracture mechanics model. In addition, defected area hole is strongest of loading failure from other defected areas as rectangular and square were of strain 520.203 𝝁𝜺 and 1389.43 𝝁𝜺 at diameter 5,10mm respectively. While defected area square is weakest as crack during propagation of pressure failure (loading failure) were 𝟐𝟑𝟑. 𝟎𝟕𝟓𝟒 𝝁𝜺 , 437.79327 𝝁𝜺, and 660.76868 𝝁𝜺 at length 5,7,and 9mm respectively.
Advanced structured materials, Jun 27, 2019
The effect of fiber length and fiber volume fraction at different crosshead speeds on the mechani... more The effect of fiber length and fiber volume fraction at different crosshead speeds on the mechanical properties and toughness of randomly oriented glass fibers reinforced polyurethane elastomer composites were studied using standard simple tension test. The modulus of elasticity and the yield stress increase with increasing the fiber volume fraction, the fiber length and the crosshead speed. The percentage increase due to the increasing of fiber volume fraction for 10 mm fiber length is much higher than that for 5 mm fiber length, while the percentage increase due to increasing of the crosshead speed for 10 mm fiber length is lower than that for 5 mm. The toughness of the failed specimens decreases with increasing the fiber volume fraction, the crosshead speed and fiber length.
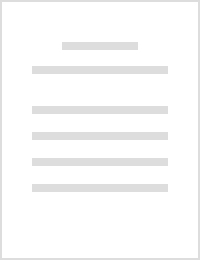
Repair Of Damaged Metal Pipes Using Composite Materials
Application of composite materials on Damaged Metal Pipes which using for Oil and Gas Industry. T... more Application of composite materials on Damaged Metal Pipes which using for Oil and Gas Industry. The subject matter or research is to introduce the composite over-wrapping repair method for metal piping systems. This needs to carry out experimental and analytical study to investigate the stress fields, failure pressure, thickness of repair laminate, diameter of holes and other related parameters on the performance of the repaired pipe. This study presents the results of research studies carried out in the Arabian Gulf Oil Company (AGOC) and in the laboratory of the Faculty of Engineering at Benghazi University in period between August 2007 and July 2008.Also, publications of work presentation at more conferences and more Journal. NEW TO THIS STUDY A carbon steel bolted clamp and screwed clamp were used to clamp the pipe around the defected holes to minimize the delamination effect and stop the leakage of water during the tests of the pipes. A special rig was designed to carry out pressurized tests on the repaired pipes. Visual basic computer program was constructed by Author.

This paper presents studies of microscopic analysis and nonlinear behavior of composite system fo... more This paper presents studies of microscopic analysis and nonlinear behavior of composite system for the rehabilitation of steel pipes by analytical models, based on the fracture mechanics and finite element techniques were developed to evaluate the deflection, failure pressure (blister pressure) and stress strain curves for damaged area [1,2]. The modeled pipes were carbon steel pipe with internal diameter of 83 mm, thickness 12.5mm and length of 900 mm. The damage was simulated as a hole at the middle of the tube. The composite repair was fiber glass reinforced polyester quiasi-istropic laminate. It was concluded that the models appear to describe the blister propagation well [1]. The experimental stress-strain relationship was nonlinear up to failure, which probably due to the matrix cracking and delamination [2]. Microscopic examination was carried out to investigate the matrix micro-crack and effect of crack density on effective modulus of laminates.
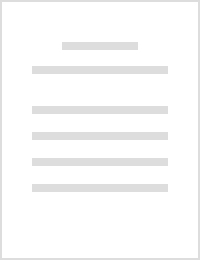
Repair of Damaged Metal Pipes Using Composite Materials
Application of composite materials on Damaged Metal Pipes which using for Oil and Gas Industry. T... more Application of composite materials on Damaged Metal Pipes which using for Oil and Gas Industry. The subject matter or research is to introduce the composite over-wrapping repair method for metal piping systems. This needs to carry out experimental and analytical study to investigate the stress fields, failure pressure, thickness of repair laminate, diameter of holes and other related parameters on the performance of the repaired pipe. This study presents the results of research studies carried out in the Arabian Gulf Oil Company (AGOC) and in the laboratory of the Faculty of Engineering at Benghazi University in period between August 2007 and July 2008.Also, publications of work presentation at more conferences and more Journal. NEW TO THIS STUDY A carbon steel bolted clamp and screwed clamp were used to clamp the pipe around the defected holes to minimize the delamination effect and stop the leakage of water during the tests of the pipes. A special rig was designed to carry out pre...

Application Design Model of Damaged Steel Pipes by using composite materials for oil and gas indu... more Application Design Model of Damaged Steel Pipes by using composite materials for oil and gas industry.This needs to carry out experimental and analytical study to investigate the stress fields, failure pressure, thickness of repair laminate, damaged area and other related parameters on the performance of the repaired pipe.This book presents the results of research studies carried out in the Arabian Gulf Oil Company (AGOC) and in the laboratory of the Faculty of Engineering at Garyounis( Benghazi) University.NEW TO THIS Book A carbon steel bolted clamp and screwed clamp were used to clamp the pipe around the defected area to minimize the delamination effect and stop the leakage of water during the tests of the pipes. A special rig was designed to carry out pressurized tests on the repaired pipes. A model based on fracture mechanics and composite lamina theory was developed to predict stress-strain behaviour at defect region.
Manufacturing and studying of Mechanical properties for types E-glass
Manufacturing and studying of Mechanical properties for types E-glass
Alexandria Engineering Journal, 2019
The effect of fiber length and fiber volume fraction at different crosshead speeds on the mechani... more The effect of fiber length and fiber volume fraction at different crosshead speeds on the mechanical properties and toughness of randomly oriented glass fibers reinforced polyurethane elastomer composites were studied using standard simple tension test. The modulus of elasticity and the yield stress increase with increasing the fiber volume fraction, the fiber length and the crosshead speed. The percentage increase due to the increasing of fiber volume fraction for 10 mm fiber length is much higher than that for 5 mm fiber length, while the percentage increase due to increasing of the crosshead speed for 10 mm fiber length is lower than that for 5 mm. The toughness of the failed specimens decreases with increasing the fiber volume fraction, the crosshead speed and fiber length.
Books by Zamzam Elsharif
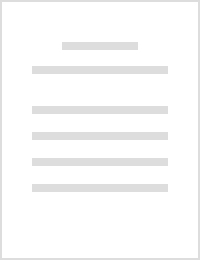
LAP LAMBERT Academic Publishing, 2015
This the book explains two applications as design of model of damaged pipes that based on fr... more This the book explains two applications as design of model of damaged pipes that based on fracture mechanics for experimental and analytical studying of composite materials.
The part one of model I presents experimental and analytical studying of a composite system for the rehabilitation of steel pipes which were developed to evaluate the deflection, failure pressure (blister pressure) and stress strain curves, also microstructure and non behavior of failure for damaged area. The modeled pipes were carbon steel pipe with internal diameter of 83 mm, thickness 12.5mm and length of 900 mm. The damage was simulated as a hole at the middle of the tube.
The part two of model II presents experimental and analytical studying of a composite system for the rehabilitation of steel pipes which were developed to evaluate the deflection, failure pressure (blister pressure) and stress strain curves for damaged area. The modeled pipe was carbon steel pipe with internal diameter of 83 mm, thickness 12.5mm and length of 900 mm. The damage was simulated as a rectangular at the middle of the tube.
In part one used of composite repair the fiber glass woven roving (type E) reinforced with polyester resin. In part two used fiber glass woven roving (type E) reinforced with epoxy resin.

LAP LAMBERT Academic Publishing, 2017
This book presents an experimental study of a composite material for comparative some me... more This book presents an experimental study of a composite material for comparative some mechanical properties of types the E-glass. This study was based on two methods. First method based on manufacturing techniques by lay-up of laminate, while second method was develop to evaluate strength stress, hardness, toughness, and stress-strain characteristic for composite material. The composite manufacturing material was fiber E-glass of woven roving at , [±30°/±60°]_s and chopped mat reinforced with polyester resin. All the manufacturing specimens were conducted to mechanical tests such as tensile test, Reckwell's hardness test and impact test.
Two types of fiber were used to study mechanical properties and its comparative during the tests of the specimens. Stress-strain curves were evaluated from data base computer.
It has been found that a good mechanical properties of experimental results in tests. Also, it has been found that the manufacturing techniques by lay-up apparel to describe the microstructure well.
Uploads
Papers by Zamzam Elsharif
It has fund that good correlations between the finite element analysis (FEA) of redial strain with previous studying curves at stages of loading of pressure. Also, observed the finite element analysis (FEA) curve was lowest radial strain of failure comparing with previous studying curves of crack length 10 mm at 957.730 με while highest radial strain was theoretical model radial strain at 1389.430με of pressure. According to studying the experimental curve and the finite element curve exhibited the non-linearity only in the early stages and then became linear up to failure.The finite element analysis (FEA) curve was highest radial stress of failure comparing with previous studying curves of crack length 10 mm at 46.541 MPa while radial stress of previous studying were 32.6941 MPa. Good correlation between the finite element analysis (FEA) and theoretical model of blister deflection. The finite element analysis (FEA) was higher of blister deformation then theoretical model 22.9490 μm and 6.7014 μm respectively. Finally, The maximum blister deflection occurs at the centre of the hole ( crake length 10 mm) by finite element analysis (FEA).
Books by Zamzam Elsharif
The part one of model I presents experimental and analytical studying of a composite system for the rehabilitation of steel pipes which were developed to evaluate the deflection, failure pressure (blister pressure) and stress strain curves, also microstructure and non behavior of failure for damaged area. The modeled pipes were carbon steel pipe with internal diameter of 83 mm, thickness 12.5mm and length of 900 mm. The damage was simulated as a hole at the middle of the tube.
The part two of model II presents experimental and analytical studying of a composite system for the rehabilitation of steel pipes which were developed to evaluate the deflection, failure pressure (blister pressure) and stress strain curves for damaged area. The modeled pipe was carbon steel pipe with internal diameter of 83 mm, thickness 12.5mm and length of 900 mm. The damage was simulated as a rectangular at the middle of the tube.
In part one used of composite repair the fiber glass woven roving (type E) reinforced with polyester resin. In part two used fiber glass woven roving (type E) reinforced with epoxy resin.
Two types of fiber were used to study mechanical properties and its comparative during the tests of the specimens. Stress-strain curves were evaluated from data base computer.
It has been found that a good mechanical properties of experimental results in tests. Also, it has been found that the manufacturing techniques by lay-up apparel to describe the microstructure well.
It has fund that good correlations between the finite element analysis (FEA) of redial strain with previous studying curves at stages of loading of pressure. Also, observed the finite element analysis (FEA) curve was lowest radial strain of failure comparing with previous studying curves of crack length 10 mm at 957.730 με while highest radial strain was theoretical model radial strain at 1389.430με of pressure. According to studying the experimental curve and the finite element curve exhibited the non-linearity only in the early stages and then became linear up to failure.The finite element analysis (FEA) curve was highest radial stress of failure comparing with previous studying curves of crack length 10 mm at 46.541 MPa while radial stress of previous studying were 32.6941 MPa. Good correlation between the finite element analysis (FEA) and theoretical model of blister deflection. The finite element analysis (FEA) was higher of blister deformation then theoretical model 22.9490 μm and 6.7014 μm respectively. Finally, The maximum blister deflection occurs at the centre of the hole ( crake length 10 mm) by finite element analysis (FEA).
The part one of model I presents experimental and analytical studying of a composite system for the rehabilitation of steel pipes which were developed to evaluate the deflection, failure pressure (blister pressure) and stress strain curves, also microstructure and non behavior of failure for damaged area. The modeled pipes were carbon steel pipe with internal diameter of 83 mm, thickness 12.5mm and length of 900 mm. The damage was simulated as a hole at the middle of the tube.
The part two of model II presents experimental and analytical studying of a composite system for the rehabilitation of steel pipes which were developed to evaluate the deflection, failure pressure (blister pressure) and stress strain curves for damaged area. The modeled pipe was carbon steel pipe with internal diameter of 83 mm, thickness 12.5mm and length of 900 mm. The damage was simulated as a rectangular at the middle of the tube.
In part one used of composite repair the fiber glass woven roving (type E) reinforced with polyester resin. In part two used fiber glass woven roving (type E) reinforced with epoxy resin.
Two types of fiber were used to study mechanical properties and its comparative during the tests of the specimens. Stress-strain curves were evaluated from data base computer.
It has been found that a good mechanical properties of experimental results in tests. Also, it has been found that the manufacturing techniques by lay-up apparel to describe the microstructure well.