Papers by Mohamed Gouda Alkalla
Tribology International, Dec 1, 2020
This is a PDF file of an article that has undergone enhancements after acceptance, such as the ad... more This is a PDF file of an article that has undergone enhancements after acceptance, such as the addition of a cover page and metadata, and formatting for readability, but it is not yet the definitive version of record. This version will undergo additional copyediting, typesetting and review before it is published in its final form, but we are providing this version to give early visibility of the article. Please note that, during the production process, errors may be discovered which could affect the content, and all legal disclaimers that apply to the journal pertain.

International Journal for Numerical Methods in Engineering, Nov 26, 2020
This article proposes a new approach called revolutionary superposition layout (RSL) for obtainin... more This article proposes a new approach called revolutionary superposition layout (RSL) for obtaining optimum designs of non-concurrent multi-loads structures in general, and for connecting rod (CR) in particular. Since the compression and tension resulted from the combustion and exhaust strokes are non-concurrent loads, the importance of this approach arises up. RSL depends on combining the optimum-design layouts obtained from different individual non-concurrent load cases into one resultant design. This final design efficiently sustains all different loads applied to it. RSL presents a simple, less computational effort in the dynamic environment, and less time-consuming method. RSL has been compared with a multi-load optimization method called bound formulation (BF) for obtaining the optimum design of some simple models before dealing with the CR model afterward. Two distinctive optimum topological designs of CR produced by RSL have proved their feasibility and achieved considerable improvements against both the conventional CR design being used nowadays in the automotive industry and the BF method designs, as well. A comparative study between them was accomplished based on both structural and modal analyses in ANSYS. As a result, the proposed RSL design shows a significant reduction of compliance, displacement/deflection and mass moment of inertia by 57.2%, 68.7% and 5.9%, respectively, compared to conventional one.
Propeller-Type Skid Steering Climbing Robot Based on a Hybrid Actuation System
International Journal of Robotics & Automation, 2018
EJBot is a propeller-type skid steering climbing robot (SSCR) based on both thruster and differen... more EJBot is a propeller-type skid steering climbing robot (SSCR) based on both thruster and differentiable driving systems. Its adhesion principle utilizes a simultaneous hybrid actuation system consisting of propeller thrust forces and driving wheel torques. EJBot can climb different kinds of surfaces, moreover, exploring the industrial vessels’ interiors for implementing the inspection tasks efficiently. kinematics and dynamics analysis are presented in this article for EJBot as an SSCR. The experimental results validate the theoretical findings and ensure the stability of the robot’s adhesion and navigation systems. The robot can cross over significant obstacles with 40mm height.
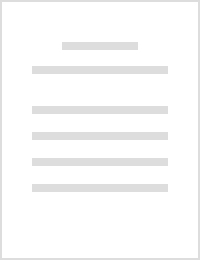
Versatile climbing robot for vessels inspection
This work focuses on proposing and designing a new climbing robot to explore the interiors of ind... more This work focuses on proposing and designing a new climbing robot to explore the interiors of industrial vessels and enables a human outside the vessels to implement required regular inspection tasks efficiently. There are two main adhesion systems in the literature: magnetic and air suction systems. The magnetic system climbs surfaces made of ferromagnetic materials only, while air suction system cannot handle irregular surfaces due to possible seals damage. Opposite to previous climbing robots, the proposed robot here can climb and navigate vessels made from different materials besides handling possible irregular surfaces during inspection. Its main task is visual inspection of welds and any critical spots inside these vessels. The novelty of this robot comes from utilizing a hybrid actuation system. This hybrid actuation system consists of upturned propellers fixed on mobile robot and motorized wheels of the mobile robot. The pressure generated from the upturned propellers increase the friction force between the wheels of the mobile robot and the wall. The wheels' motors generate the required torque either to fix the robot in any position or to move it to any place. Since the motion of the robot comes mainly from the motorized wheel, the stability of the system during navigation is guaranteed. Size and topology optimizations are carried out to achieve optimum design of the proposed robot. Simulation results of the designed robot using ADAMS software prove its feasibility.

Advanced Robotics, Aug 29, 2019
This paper presents a new kind of climbing robots called EJBot, which has not been restricted to ... more This paper presents a new kind of climbing robots called EJBot, which has not been restricted to climb certain surface materials or terrains. EJBot is inspired by propeller-based aviation systems, however, its adhesion principle is opposite to flight concept. Thanks to the hybrid actuation system embedded in this robot which gives a good and stable adhesion. This hybrid system consists of propeller thrust forces and wheel torques actuated simultaneously to generate the proper adhesion force. It is similar to a car climbing a ramp, it needs both weight of the car and the wheels' torques. Without these torques, the car will roll down. Consequently, the thrust forces of the propellers increase the traction force capacity, then the wheels' role arises to generate the convenient torques for stopping the robot or navigating it on the structures. The feasibility of this adhesion concept is verified by the first and second modules of EJBot as presented in the simulation and practical results.
A novel propeller-type climbing robot for vessels inspection
ABSTRACT
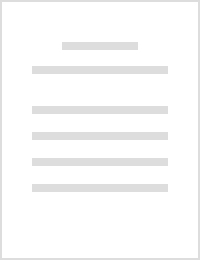
Tele-operated propeller-type climbing robot for inspection of petrochemical vessels
Industrial Robot-an International Journal, Mar 20, 2017
Purpose The purpose of this paper is to propose a new propeller-type climbing robot called EJBot ... more Purpose The purpose of this paper is to propose a new propeller-type climbing robot called EJBot for climbing various types of structures that include significant obstacles, besides inspection of industrial vessels made of various materials, including non-ferromagnetic material. The inspection includes capturing images for important spots and measuring the wall thickness. Design/methodology/approach The design mainly consists of two coaxial upturned propellers mounted on a mobile robot with four standard wheels. A new hybrid actuation system that consists of propeller thrust forces and standard wheel torques is considered as the adhesion system for this climbing robot. This system generates the required adhesion force to support the robot on the climbed surfaces. Dynamic simulation using ADAMS is performed and ensures the success of this idea. Findings Experimental tests to check the EJBot’s capabilities of climbing different surfaces, such as smooth, rough, flat and cylindrical surfaces like the real vessel, are successfully carried out. In addition, the robot stops accurately on the climbed surface at any desired location for inspection purposes, and it overcomes significant obstacles up to 40 mm. Practical implications This proposed climbing robot is needed for petrochemical and liquid gas vessels, where a regular inspection of the welds and the wall thickness is required. The interaction between the human and these vessels is dangerous and not healthy due to the harmful environment inside these vessels. Originality/value This robot utilizes propeller thrusts and wheel torques simultaneously to generate adhesion and traction forces. Therefore, a versatile robot able to climb different kinds of structures is obtained.
Nanomaterials, Jan 10, 2023
This article is an open access article distributed under the terms and conditions of the Creative... more This article is an open access article distributed under the terms and conditions of the Creative Commons Attribution (CC BY
Biologically-inspired mechanisms for space applications
Institution of Engineering and Technology eBooks, Aug 24, 2021
Maǧallaẗ Kulliyyaẗ Dār Al-ʿulūm, Oct 3, 2020
Bulletin of the Faculty of Engineering. Mansoura University, Jul 19, 2020
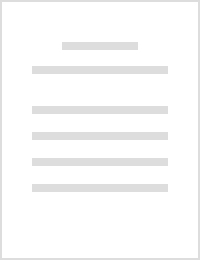
Integrated structure/control design of high-speed flexible robot arms using topology optimization
Mechanics Based Design of Structures and Machines, Nov 11, 2019
Abstract Most robotic applications demand lightweight and high-speed manipulators for considerabl... more Abstract Most robotic applications demand lightweight and high-speed manipulators for considerably reducing the consumed power and achieving high production rates. The two ways for seeking such high-speed arms are; applying advanced control algorithms and/or performing an extensive optimization of the arm structure itself. Therefore, the topology optimization technique is proposed here for obtaining an optimal robot arm design from both structure and control viewpoints. Results of some researches, that have been previously accomplished by size and shape optimization, were encouraging enough to extend and propose this optimization approach. The method of moving asymptotes (MMA) as an optimization algorithm, the finite element analysis (FEA) by ANSYS, and the time-optimal control method are integrated to gain an optimum design capable of attaining the minimum traveling time. The proposed methodology focuses on performing different comparisons between the proposed optimum topological designs and their initial designs for different robot arms’ sizes and materials. It also distinguishes between the proposed optimum design and the previously achieved one by size optimization under the same operational conditions. Therefore, the significance of the proposed technique is emphasized. It shows that the traveling time is reduced by 44.8%, while the previous work only achieved 23.5%. In addition, the mass is reduced to nearly half of its initial value, taking into account the air damping as the real case in all terrestrial applications.
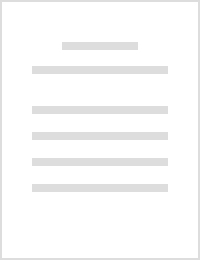
DROD: A hybrid biomimetic undulatory and reciprocatory drill: Quantitative analysis and numerical study
Acta Astronautica
Abstract This article presents a novel hybrid evolution of the biologically-inspired dual-recipro... more Abstract This article presents a novel hybrid evolution of the biologically-inspired dual-reciprocating drill (DRD). The proposed system combines the reciprocation motion used by previous iterations of the wood wasp drill with a proposed new undulatory/oscillation motion. This is inspired by the caudal fins of marine creatures, which use this motion to generate a thrust force to propel themselves through water, and sandfish, which use an undulatory body motion to bury and hide themselves in sand. It is proposed that including this motion will significantly enhance the performance of the DRD, resulting in the design of the novel dual reciprocation oscillation drill (DROD). The development of this third generation of the DRD system is also targeting full integration with planetary rovers. Several improvements have also been proposed to improve its suitability for a space exploration mission, such as a compact size, a large (173 cm 3 ) automated sampling compartment, potential stem flexibility and customised drill bits for exploiting the various regolith physical properties on planetary bodies. This article presents a quantitative and numerical analysis of the DROD design. The feasibility of the DROD has been proved by the kinematics and dynamics simulations produced by MATLAB and ADAMS. Finally, the effectiveness of different drilling motions was studied numerically using discrete element modelling and multi-body dynamic (EDEM-ADAMS) co-simulations. This revealed the underlying mechanisms of the drill–soil interactions and will pave the way for the development of robust numerical models for different regoliths in the future.
Bulletin of the Faculty of Engineering. Mansoura University, 2020
Propeller-Type Skid Steering Climbing Robot Based on a Hybrid Actuation System
International Journal of Robotics and Automation, 2018
EJBot is a propeller-type skid steering climbing robot (SSCR) based on both thruster and differen... more EJBot is a propeller-type skid steering climbing robot (SSCR) based on both thruster and differentiable driving systems. Its adhesion principle utilizes a simultaneous hybrid actuation system consisting of propeller thrust forces and driving wheel torques. EJBot can climb different kinds of surfaces, moreover, exploring the industrial vessels’ interiors for implementing the inspection tasks efficiently. kinematics and dynamics analysis are presented in this article for EJBot as an SSCR. The experimental results validate the theoretical findings and ensure the stability of the robot’s adhesion and navigation systems. The robot can cross over significant obstacles with 40mm height.
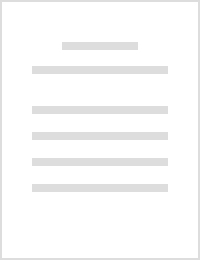
Tele-operated propeller-type climbing robot for inspection of petrochemical vessels
Industrial Robot: An International Journal, 2017
Purpose The purpose of this paper is to propose a new propeller-type climbing robot called EJBot ... more Purpose The purpose of this paper is to propose a new propeller-type climbing robot called EJBot for climbing various types of structures that include significant obstacles, besides inspection of industrial vessels made of various materials, including non-ferromagnetic material. The inspection includes capturing images for important spots and measuring the wall thickness. Design/methodology/approach The design mainly consists of two coaxial upturned propellers mounted on a mobile robot with four standard wheels. A new hybrid actuation system that consists of propeller thrust forces and standard wheel torques is considered as the adhesion system for this climbing robot. This system generates the required adhesion force to support the robot on the climbed surfaces. Dynamic simulation using ADAMS is performed and ensures the success of this idea. Findings Experimental tests to check the EJBot’s capabilities of climbing different surfaces, such as smooth, rough, flat and cylindrical sur...
A novel propeller-type climbing robot for vessels inspection
2015 IEEE International Conference on Advanced Intelligent Mechatronics (AIM), 2015
ABSTRACT
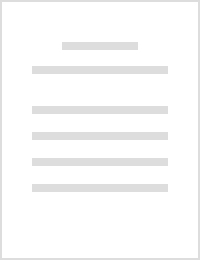
Versatile climbing robot for vessels inspection
2015 International Conference on Control, Automation and Robotics, 2015
This work focuses on proposing and designing a new climbing robot to explore the interiors of ind... more This work focuses on proposing and designing a new climbing robot to explore the interiors of industrial vessels and enables a human outside the vessels to implement required regular inspection tasks efficiently. There are two main adhesion systems in the literature: magnetic and air suction systems. The magnetic system climbs surfaces made of ferromagnetic materials only, while air suction system cannot handle irregular surfaces due to possible seals damage. Opposite to previous climbing robots, the proposed robot here can climb and navigate vessels made from different materials besides handling possible irregular surfaces during inspection. Its main task is visual inspection of welds and any critical spots inside these vessels. The novelty of this robot comes from utilizing a hybrid actuation system. This hybrid actuation system consists of upturned propellers fixed on mobile robot and motorized wheels of the mobile robot. The pressure generated from the upturned propellers increase the friction force between the wheels of the mobile robot and the wall. The wheels' motors generate the required torque either to fix the robot in any position or to move it to any place. Since the motion of the robot comes mainly from the motorized wheel, the stability of the system during navigation is guaranteed. Size and topology optimizations are carried out to achieve optimum design of the proposed robot. Simulation results of the designed robot using ADAMS software prove its feasibility.
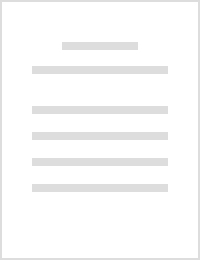
Integrated Structure/Control Design of High Speed Flexible Robots Based on Time Optimal Control
Journal of Dynamic Systems, Measurement, and Control, 1995
This paper presents the integrated structure/control design of high speed single link robots base... more This paper presents the integrated structure/control design of high speed single link robots based on time-optimal control and finite element analysis. First, the solutions of a time optimal control problem are analyzed with respect to the arm link inertia and its structural flexibility. A new technique is developed to further reduce the optimal traveling time by redesigning the arm structure through the trade-off analysis between the arm inertia and its natural frequency. In the latter half of the paper, the design criterion is extended to multiple indices by considering residual vibrations, load bearing capacity and other design constraints. For suppressing residual vibrations, a simple feedback control is designed and its dynamic performance with respect to pole-zero locations is improved along with other criteria through mechanical structure modification. The finite element method is used as a modeling tool and the shape of the arm geometry is modified as design parameters. An a...
Development of a multi-sample acquisition technique for efficient planetary subsurface exploration
Acta Astronautica, Sep 1, 2022
Uploads
Papers by Mohamed Gouda Alkalla