Papers by Redha Benhadj-djilali
Optimizing 5-Axis Sculptured Surface Finish Machining Through Design of Experiments and Neural Networks
Volume 1: Applied Mechanics; Automotive Systems; Biomedical Biotechnology Engineering; Computational Mechanics; Design; Digital Manufacturing; Education; Marine and Aerospace Applications, 2014
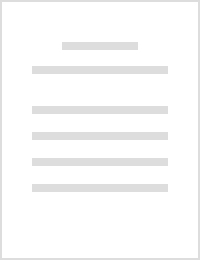
Evaluation of 3- and 5-axis sculptured surface machining in CAM environment through design of experiments
International Journal of Computer Integrated Manufacturing, 2014
ABSTRACT Sculptured surface machining (SSM) is an operation widely applied to several industrial ... more ABSTRACT Sculptured surface machining (SSM) is an operation widely applied to several industrial fields such as aerospace, automotive and mould/die. The number of the parameters and strategies involved to program such machining operations can be enormously large owing to surface complexity and advanced design features. This study focuses on the examination of machining strategies and related parameters for the assessment of roughing and finishing stages. A fractional factorial design implementing an L27 Taguchi orthogonal array (OA) was established to conduct machining experiments with the use of a computer-aided manufacturing (CAM) software. Fractional factorial design specifics involve the statistical elimination of unimportant parameters, thus reducing experimental runs without the loss of useful information. Two scenarios were considered to machine a sculptured part; one involving 3-axis roughing/3-axis finish machining experiments and the other one involving 3-axis roughing/5-axis finish machining experiments. Roughing operation was common for both scenarios. The problem was subjected to discrete technological constraints to reflect the actual industrial status. For each machining phase, two quality objectives reflecting productivity and part quality were determined. Roughing experiments were tested to minimise machining time and remaining volume, whilst finishing experiments were subjected to minimise machining time and surface deviation between the designed and the machined 3D model. Quality characteristics were properly weighted to formulate a single objective criterion for both machining phases. Results indicated that DOE applied to CAM software, enables NC programmers to have a clear understanding about the influence of process parameters for SSM operations, thus generating efficient toolpaths to improve productivity, part quality and process efficiency. Practically the work contributes to machining improvement by through the proposition of machining experimentation methods using safe and useful platforms such as CAM systems; the investigation of approaches to avoid problem oversimplification mainly when large number of machining parameters should be exploited and the evaluation of quality criteria which allow their assessment directly form CAM software.

The International Journal of Advanced Manufacturing Technology, 2014
To ensure the quality of machined products at minimum cost and maximum effectiveness, it is cruci... more To ensure the quality of machined products at minimum cost and maximum effectiveness, it is crucial that selection of optimum machining parameters should be done when computer numerically controlled (CNC) machine tools technology is employed. Traditionally, experience of the operator plays a major role in the selection of efficient parameter values; however, attaining optimum ones each time by even skilled end users, is extremely difficult. This paper takes advantage of the possibilities of current computer-aided design (CAD)/computer-aided manufacturing (CAM) technology and implements a genetic algorithm for optimising CNC machining operations mainly for sculptured surfaces. The algorithm has been developed as a hosted application to a cutting-edge CAD/CAM system. Collaboration among applications has been achieved through programming for software automation by utilising the application programme interface of the system. The approach was implemented to a group of test sculptured models with different properties whilst one of them has been actually machined using typical resources. Results obtained after the implementation indicated that the methodology is capable of providing optimum values for process parameters on its way to maintain both productivity and high quality.
Materials Forming, Machining and Tribology, 2014

This work considers the issue of assessing finished part quality through calculation of the local... more This work considers the issue of assessing finished part quality through calculation of the local difference between finished part geometry and the ideally designed geometry. Using common surface analysis tools available to most commercial CAM software, machined 3D models are measured by collecting surface points from a number of sub-regions and computing their variances. Stratified random sampling is applied to create the sub-regions from which sampling is done, whilst hypothesis testing is made to verify homogeneity of variances. The notion is to use a single number of surface points capable of describing the error distribution without the loss of significant information. Results have shown that the proposed philosophy can dramatically reduce cost in terms of machining experimentation while allowing the creation of short and accurate tool paths for sculptured surfaces when using CAM software. It is also mentioned that the proposed approach may be further intergrated to CAM software through automation routines thus; contribute to manufacturing optimization tasks.
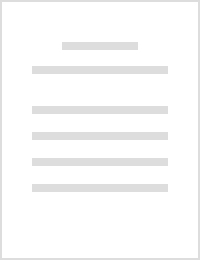
Intelligent CNC Tool Path Optimization for Sculptured Surface Machining Through a Virus-Evolutionary Genetic Algorithm
Materials Forming, Machining and Tribology, 2015
ABSTRACT Priorities for manufacturers worldwide include their attempt towards optimizing modern m... more ABSTRACT Priorities for manufacturers worldwide include their attempt towards optimizing modern manufacturing systems to satisfy the needs of their customers. Major goal of the proposed study is to present a novel optimization methodology based on Artificial Intelligence using the Virus Theory of Evolution. The methodology implements a Virus-Evolutionary Genetic Algorithm to undertake sculptured surface tool path optimization in terms of geometrical machining error to reflect part quality and machining time to reflect productivity for both 3- and 5-axis sculptured surface machining. The algorithm implements its virus operators to create efficient solution representations, to rabidly reproduce enhanced schemata during the evaluations’ loops, and finally come up with the optimum machining parameters based on the available resources and constraints ought to be imposed. Through a fully automated environment, time-consuming activities and repetitive tasks are no more of the CNC programmers’ concern since the algorithm handles the CAM system’s routines to handle them for its own benefit. The proposed methodology is deemed capable of providing uniform tool paths with low geometric machining error distribution as well as high productivity rates to the best possible extent.
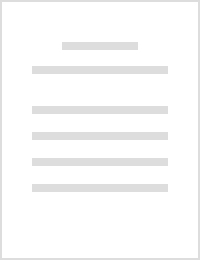
Intelligent CNC Tool Path Optimization for Sculptured Surface Machining Through a Virus-Evolutionary Genetic Algorithm
Materials Forming, Machining and Tribology, 2015
ABSTRACT Priorities for manufacturers worldwide include their attempt towards optimizing modern m... more ABSTRACT Priorities for manufacturers worldwide include their attempt towards optimizing modern manufacturing systems to satisfy the needs of their customers. Major goal of the proposed study is to present a novel optimization methodology based on Artificial Intelligence using the Virus Theory of Evolution. The methodology implements a Virus-Evolutionary Genetic Algorithm to undertake sculptured surface tool path optimization in terms of geometrical machining error to reflect part quality and machining time to reflect productivity for both 3- and 5-axis sculptured surface machining. The algorithm implements its virus operators to create efficient solution representations, to rabidly reproduce enhanced schemata during the evaluations’ loops, and finally come up with the optimum machining parameters based on the available resources and constraints ought to be imposed. Through a fully automated environment, time-consuming activities and repetitive tasks are no more of the CNC programmers’ concern since the algorithm handles the CAM system’s routines to handle them for its own benefit. The proposed methodology is deemed capable of providing uniform tool paths with low geometric machining error distribution as well as high productivity rates to the best possible extent.
Binary Image Coding Algorithm Using Tactile Data Information
Conference on Imaging Science, Systems and Technology, 2003
This paper describes the formulation and design principles of operation of a pneumatic proximity-... more This paper describes the formulation and design principles of operation of a pneumatic proximity-to-tactile sensing device for automated recognition of objects within flexible manufacturing environments. This sensing device utilises a densely packed line array of piezoresistive pressure sensors, providing continuous variable output. The sensing head or plane of the device incorporates a corresponding line array of air jets which form

The International Journal of Advanced Manufacturing Technology, 2014
To ensure the quality of machined products at minimum cost and maximum effectiveness, it is cruci... more To ensure the quality of machined products at minimum cost and maximum effectiveness, it is crucial that selection of optimum machining parameters should be done when computer numerically controlled (CNC) machine tools technology is employed. Traditionally, experience of the operator plays a major role in the selection of efficient parameter values; however, attaining optimum ones each time by even skilled end users, is extremely difficult. This paper takes advantage of the possibilities of current computer-aided design (CAD)/computer-aided manufacturing (CAM) technology and implements a genetic algorithm for optimising CNC machining operations mainly for sculptured surfaces. The algorithm has been developed as a hosted application to a cutting-edge CAD/CAM system. Collaboration among applications has been achieved through programming for software automation by utilising the application programme interface of the system. The approach was implemented to a group of test sculptured models with different properties whilst one of them has been actually machined using typical resources. Results obtained after the implementation indicated that the methodology is capable of providing optimum values for process parameters on its way to maintain both productivity and high quality.
Uploads
Papers by Redha Benhadj-djilali