Papers by toyabur rahman toyab

Ceramics International, 2017
Most piezoelectric vibration energy harvesters are conventional single-degree-of-freedom (SDOF) s... more Most piezoelectric vibration energy harvesters are conventional single-degree-of-freedom (SDOF) systems, and typically perform well at the single resonant mode-which makes the harvesters less efficient for low ambient vibration frequencies. In this work, we have proposed and experimentally validated a piezoelectric multimodal energy harvester having several mechanical degrees of freedom (DOFs). This multi-modal vibration energy harvester has a unique design that helps to obtain multiple resonant mode operation of the harvester at the lower frequency range. The finite element method (FEM) simulation model has been used to predict the mode shapes of the proposed energy harvester at different vibration modes. The experimental results imply that the proposed energy harvester can obtain four peak values in the range of 10-20 Hz, which are concentrated around 10, 14, 16, and 20 Hz respectively. In addition, the piezoceramic material lead zirconate titanate (PZT) has been used as a piezoelectric element that has excellent piezoelectric properties. A prototype multimodal energy harvester with four piezoelectric elements is fabricated, where a single piezoelectric element generated a peak power with a maximum of 249 µW delivered to an optimum load Paper no.-0299 2 of 55 KΩ at 16 Hz resonant mode under 0.4 g base acceleration. In order to increase the output power and bandwidth, it is always a good idea to use multiple piezoelectric elements in one harvester structure; consequently, four piezoelectric elements of the fabricated prototype are connected in parallel. The device with parallel connected piezoelectric modules generates a peak output power of 740 µW across an equivalent optimum load resistance at 3rd resonant mode (16 Hz), while the device's base is excited at 0.4 g acceleration.

Nano Energy, 2018
Owing to the climate change and energy crisis, harvesting energy from our surroundings and the co... more Owing to the climate change and energy crisis, harvesting energy from our surroundings and the construction of self-powered wireless environmental monitoring systems are promising approaches in modern times. In this paper, an ultra-compact highly efficient miniaturized windmill comprising a hybridized nanogenerator (MW-HNG) is reported based on three conversion mechanisms i.e. triboelectric nanogenerator (TENG), piezoelectric nanogenerator (PENG), and electromagnetic generator (EMG). The MW-HNG is designed as a 3D-printed fully-enclosed structure for the natural wind energy harvesting by converting into rotational motion: all harvesting units reside in a common rotation system to effectively and simultaneously produce electricity. At a wind speed of 6 m/s, the flexible-blade-based hybridization-mode (contact-lateral sliding-separation-contact) TENG and coupled PENG can generate maximal power values of 1.67 mW and 1.38 mW at optimal load resistances of 10 MΩ and 330 KΩ, respectively. In contrast, the multipole-magnet-based EMG can obtain a maximal output power of 268.6 mW at 180 Ω. The MW-HNG demonstrates a quick charging ability for capacitors and the capability to feed hundreds of LEDs. Further, a self-powered wireless sensor system is developed for real-time environmental monitoring by combining an MW-HNG, a customized power management circuit, and wireless sensor unit (a smartphone 2 to display sensor data). Our proposed MW-HNG is suitable for self-powered wireless sensor networks (WSNs) in the subway system by generating high-power electrical output from moving-induced wind mechanical energy.
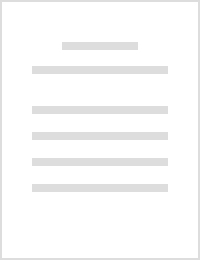
Energy Conversion and Management
Abstract In this paper, we proposed and experimentally validated a vibration-based multimodal hyb... more Abstract In this paper, we proposed and experimentally validated a vibration-based multimodal hybrid piezoelectric–electromagnetic energy harvester having multiple mechanical degrees-of-freedom. This multimodal hybrid energy harvester (MHEH) has a unique design, which helps it to achieve multiple close resonant modes of vibration in a certain frequency range. Using a low-spring-stiffness material (polyacrylate) as a substrate assists MHEH in reducing the higher resonant frequencies into a low frequency range. The two combined conversion mechanisms (piezoelectric–electromagnetic) are exploited to obtain higher output power from low input accelerations at ambient vibrations. The finite element method simulation model is employed to predict and optimize the mode shapes of the proposed MHEH for different vibration modes. The simulation and experimental result imply that the proposed MHEH can operate at four resonant modes of vibration in the range of 12–22 Hz, which are concentrated around 12, 15, 17, and 22 Hz. An MHEH prototype is fabricated, where four lead-zirconate-titanate elements are used as piezoelectric materials, and NdFeB magnets with conductive coils are used as electromagnetic parts in the same system. Here, a single piezoelectric generator can produce a maximum of 250.23 µW of power across an optimum load of 90 KΩ at the 3rd resonant mode (17 Hz) under 0.4 g (3.92 ms −2 ) acceleration. On the other hand, a single electromagnetic generator can deliver a maximum power of 244.17 µW to a 10 Ω optimum load under the same conditions. Meanwhile, all eight generators of the MHEH operate simultaneously at their respective resonant frequencies.

Energy Conversion and Management, 2018
Keywords: Hybrid energy harvester Multi-degree-of-freedom Low-frequency vibrations Piezoelectric ... more Keywords: Hybrid energy harvester Multi-degree-of-freedom Low-frequency vibrations Piezoelectric Electromagnetic A B S T R A C T In this paper, we proposed and experimentally validated a vibration-based multimodal hybrid piezo-electric-electromagnetic energy harvester having multiple mechanical degrees-of-freedom. This multimodal hybrid energy harvester (MHEH) has a unique design, which helps it to achieve multiple close resonant modes of vibration in a certain frequency range. Using a low-spring-stiffness material (polyacrylate) as a substrate assists MHEH in reducing the higher resonant frequencies into a low frequency range. The two combined conversion mechanisms (piezoelectric-electromagnetic) are exploited to obtain higher output power from low input accelerations at ambient vibrations. The finite element method simulation model is employed to predict and optimize the mode shapes of the proposed MHEH for different vibration modes. The simulation and experimental result imply that the proposed MHEH can operate at four resonant modes of vibration in the range of 12-22 Hz, which are concentrated around 12, 15, 17, and 22 Hz. An MHEH prototype is fabricated, where four lead-zirconate-titanate elements are used as piezoelectric materials, and NdFeB magnets with conductive coils are used as electromagnetic parts in the same system. Here, a single piezoelectric generator can produce a maximum of 250.23 µW of power across an optimum load of 90 KΩ at the 3rd resonant mode (17 Hz) under 0.4 g (3.92 ms −2) acceleration. On the other hand, a single electromagnetic generator can deliver a maximum power of 244.17 µW to a 10 Ω optimum load under the same conditions. Meanwhile, all eight generators of the MHEH operate simultaneously at their respective resonant frequencies.

Nano Energy, 2019
Owing to the climate change and energy crisis, harvesting energy from our surroundings and the co... more Owing to the climate change and energy crisis, harvesting energy from our surroundings and the construction of self-powered wireless environmental monitoring systems are promising approaches in modern times. In this paper, an ultra-compact highly efficient miniaturized windmill comprising a hybridized nanogenerator (MW-HNG) is reported based on three conversion mechanisms i.e. triboelectric nanogenerator (TENG), piezoelectric nanogenerator (PENG), and electromagnetic generator (EMG). The MW-HNG is designed as a 3D-printed fully-enclosed structure for the natural wind energy harvesting by converting into rotational motion: all harvesting units reside in a common rotation system to effectively and simultaneously produce electricity. At a wind speed of 6 m/s, the flexible-blade-based hybridization-mode (contact-lateral sliding-separation-contact) TENG and coupled PENG can generate maximal power values of 1.67 mW and 1.38 mW at optimal load resistances of 10 MΩ and 330 KΩ, respectively. In contrast, the multipole-magnet-based EMG can obtain a maximal output power of 268.6 mW at 180 Ω. The MW-HNG demonstrates a quick charging ability for capacitors and the capability to feed hundreds of LEDs. Further, a self-powered wireless sensor system is developed for real-time environmental monitoring by combining an MW-HNG, a customized power management circuit, and wireless sensor unit (a smartphone to display sensor data). Our proposed MW-HNG is suitable for self-powered wireless sensor networks (WSNs) in the subway system by generating high-power electrical output from moving-induced wind mechanical energy.

Most piezoelectric vibration energy harvesters are conventional single-degree-of-freedom (SDOF) s... more Most piezoelectric vibration energy harvesters are conventional single-degree-of-freedom (SDOF) systems, and typically perform well at the single resonant mode-which makes the harvesters less efficient for low ambient vibration frequencies. In this work, we have proposed and experimentally validated a piezoelectric multimodal energy harvester having several mechanical degrees of freedom (DOFs). This multi-modal vibration energy harvester has a unique design that helps to obtain multiple resonant mode operation of the harvester at the lower frequency range. The finite element method (FEM) simulation model has been used to predict the mode shapes of the proposed energy harvester at different vibration modes. The experimental results imply that the proposed energy harvester can obtain four peak values in the range of 10–20 Hz, which are concentrated around 10, 14, 16, and 20 Hz respectively. In addition, the piezoceramic material lead zirconate titanate (PZT) has been used as a piezoelectric element that has excellent piezoelectric properties. A prototype multimodal energy harvester with four piezoelectric elements is fabricated, where a single piezoelectric element generated a peak power with a maximum of 249 µW delivered to an optimum load of 55 KΩ at 16 Hz resonant mode under 0.4 g base acceleration. In order to increase the output power and bandwidth, it is always a good idea to use multiple piezoelectric elements in one harvester structure; consequently, four piezoelectric elements of the fabricated prototype are connected in parallel. The device with parallel connected piezoelectric modules generates a peak output power of 740 µW across an equivalent optimum load resistance at 3rd resonant mode (16 Hz), while the device's base is excited at 0.4 g acceleration.
Uploads
Papers by toyabur rahman toyab