Papers by Walter Wukovits

Chemical engineering transactions, Aug 1, 2018
In combination with a complex global market environment, the iron and steel industry is dealing w... more In combination with a complex global market environment, the iron and steel industry is dealing with increasing demands for reduction of environmental and greenhouse emissions. Alternative iron making technologies such as Corex® and Finex® can offer solutions for these challenges. The melter gasifier is the central unit operation of these well-established alternative iron making processes. Both offer considerable advantages with respect to economic characteristics and environmental emissions. Similar to the conventional iron making process of the blast furnace route, a variety of different input materials is required for these processes including coal, coke, lump or fine ore, iron ore pellets as well as limestone and dolomite. Most of these raw materials also carry minor amounts of unwanted compounds such as alkali or zincbased species. The presence of these materials inside a melter gasifier can lead to instability, problematic process conditions and refractory damages. A better understanding of the distribution of these problematic species is therefore of great importance to plant manufacturers and operators. A variety of different multiphase reactions are responsible for the distribution of trace materials within the melter gasifier. In order to get a better understanding of the complex nature of these reactions, a thermodynamic investigation was carried out using calculation routines of HSC Chemistry and FactSage. Based on the findings of this investigation, a multi-zone model was developed using the simulation platform of the gPROMS ModelBuilder®. The model is separated into distinct reaction zones across the height of the melter gasifier to depict the main iron ore reduction process as well as the governing reactions of trace material components. Validation of the model was carried out using reference data of existing plants. The model described in this work is used to analyse the behaviour of trace materials within a melter gasifier. Due to the highly integrated material flows of the Corex® and Finex® iron making processes, the impact on their operational characteristics can be investigated as well. Through this it is possible to optimise the raw material input of these processes, potentially leading to reduced fuel demand and environmental emissions.
Chemical engineering transactions, Aug 20, 2010
In this work were developed three different membrane gas permeation unit models in Aspen Custom M... more In this work were developed three different membrane gas permeation unit models in Aspen Custom Modeller. These models were based in the solution-diffusion mechanism and describe a single membrane module. Two of the three models built, considered a discretization of the membrane's module whereas the other model considered the membrane as a block. The models' results were compared against experimental data measured from the separation of carbon dioxide and methane for validation. The model that presented itself to be the most suitable one was used on sensitivity analysis calculations for the separation of hydrogen and carbon dioxide with a reverse-selective PDMS membrane. The models that provided the best results in validation were the discretized ones.
Carbon Resources Conversion, Mar 1, 2022
18th World Hydrogen Energy Conference, 2010

Bhm Berg- Und Hüttenmännische Monatshefte, Feb 17, 2020
This work represents an extended abstract of a study presented at the PRES 2016 conference. Despi... more This work represents an extended abstract of a study presented at the PRES 2016 conference. Despite the fact that alternative processes such as Corex® and Finex® have already been established on industrial scale, the blast furnace route continues to be the most important process used to produce pig iron. Due to its importance, a variety of models of the blast furnace process have been developed in the past decades. In addition to this, a wellestablished analogue representation of blast furnace operation is given by the Rist operating diagram. The target of this work was to create a comprehensive blast furnace model in the process simulation platform of gPROMS ModelBuilder®, which enables the description of interdependencies between the main blast furnace process, raceway conditions as well as the overall thermodynamic process conditions within a single mathematical model. As an example of possible applications of the developed model, a detailed analysis of the model behaviour under varying coke substitution scenarios was carried out in order to evaluate their CO2 abatement potentials.
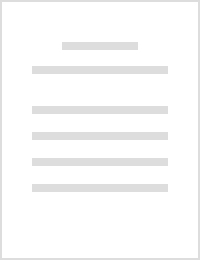
Chemical engineering transactions, Aug 20, 2016
Despite the fact that alternative processes such as Corex® and Finex® have already been establish... more Despite the fact that alternative processes such as Corex® and Finex® have already been established on industrial scale, the blast furnace route continues to be the most important process used to produce pig iron. Due to its importance, a variety of models of the blast furnace process have been developed in the past decades. In addition to this, a well-established analogue representation of blast furnace operation is given by the Rist operating diagram.The target of this work is to create a comprehensive blast furnace model in the simulation platform of gPROMS ModelBuilder®. Based on elemental assignments and empirical component distribution correlations, the blast furnace process is depicted by means of a black box model. The thermodynamic process boundaries are analysed in a Rist sub-model. Furthermore, an additional sub-model is used to calculate the adiabatic flame temperature in front of the blast furnace tuyeres. This modelling concept enables the description of interdependencies between the main blast furnace process, raceway conditions as well as overall thermodynamic process conditions within a single mathematical model.A detailed analysis of the model behaviour under varying coke substitution scenarios was carried out. The achieved simulation results demonstrate the applicability of the developed model for simulation of the blast furnace process under a wide range of operation conditions. The model also provides the means for simulation of different blast furnace route setups which allow for further optimisation regarding process efficiency, fuel consumption and environmental emissions of the blast furnace process.

Chemical engineering transactions, Aug 1, 2018
Iron and steel making requires a wide range of different raw materials which are significantly in... more Iron and steel making requires a wide range of different raw materials which are significantly influencing process performance and demands a continuous optimisation of process routes also with respect to energy efficiency as well as environmental emissions. Steadily changing raw material prices and qualities, market situations and product variations are challenging integrated steel plant operators in production planning and cost optimization. To successfully counter this global market situation by the use of a simulation platform, the effort was taken to develop a holistic model library for optimization of integrated steel plants. This simulation platform-"m.simtop" is capable of a sophisticated depiction of any integrated steel plant setup and a wide range of calculation functionalities including optimization routines. In a detailed process analysis with m.simtop of a central European iron making routeconsisting of a sinter plant, two blast furnaces including hot blast stoves and a hot metal desulphurisation ladlesimulation results were compared to operation data and showed highly accurate accordance. The special task of this process analysis was to specifically trace sulphur in the iron making production routean environmentally and operationally crucial element. Due to this study generated simulation results delivered more insight on the sulphur distribution throughout the production process and robust figures which can be used for strategic operation planning are thus now available. In this summary the process chain, its depiction in m.simtop and related results are described.

DOAJ (DOAJ: Directory of Open Access Journals), Sep 1, 2022
In 2015/2016, the total municipal solid waste (MSW) collected by local authority in the U.K. was ... more In 2015/2016, the total municipal solid waste (MSW) collected by local authority in the U.K. was 26 million tonnes and over 57% is still put into landfill or incinerated. MSW is a promising feedstock for biobutanol production as it has a high lignocellulosic fibre content such as paper, wood, and food waste, about 50 wt% of a typical MSW stream. The study evaluates acetone, butanol, ethanol and hydrogen production from autoclaved municipal solid waste feedstock. Life cycle assessment is undertaken to evaluate the acetone, butanol, ethanol and hydrogen production process, considering cogeneration of heat and power from residual biogenic waste based on experimental data and process modelling. Acetone, butanol, and ethanol product yield can be achieved at 12.2 kg butanol, 1.5 kg ethanol, 5.7 kg acetone, and 0.9 kg hydrogen per tonne MSW. The product yield is relatively low compared to other lignocellulosic feedstocks primarily because of the lower hydrolysis yield (38% for glucose) achieved in this study; however, hydrolysis yields could be improved in future optimisation work. The conversion shows a net primary energy demand of À1.11 MJ/MJ liquid biofuels (butanol and ethanol) and net greenhouse gas emission of À12.57 g CO 2 eq/MJ liquid biofuels, achieving a greenhouse gas reduction of 115% compared to gasoline comparator.
Chemie Ingenieur Technik, Aug 27, 2010
Die Umsetzung des Lignins wird dabei über den verfolgt. Zurzeit ist ein enzymatischer Umsatz von ... more Die Umsetzung des Lignins wird dabei über den verfolgt. Zurzeit ist ein enzymatischer Umsatz von 12 % möglich. Als Referenz wurde eine chemische Lignindegradierung mit einem Umsatz von 37 % etabliert. Die sechs Generationen des Algorithmus zeigen eine Kongruenz der Enzymkonzentrationen von LiP, MnP und VeP, während Laccase keinen Einfluss hat. Des Weiteren be-einflussen die Konzentrationen von Mangan und Oxalat die Umsetzung, während die Variation von ABTS-und H 2 O 2 nur eine geringe Auswirkung hat.
AIMS bioengineering, 2014
Clean Technologies and Environmental Policy, Jan 29, 2014
DOAJ (DOAJ: Directory of Open Access Journals), Sep 1, 2022

Chemical engineering transactions, Apr 20, 2011
Fermentation of biomass residues and second generation biomasses is a possible way to enable a su... more Fermentation of biomass residues and second generation biomasses is a possible way to enable a sustainable production of hydrogen. The HYVOLUTION-project investigates the production of hydrogen by a 2-stage fermentation process of biomass. It consists of a dark fermentation step of sugars to produce hydrogen, CO 2 and organic acids followed by a photo-heterotrophic fermentation, in which all intermediates are converted to more hydrogen and CO 2. This work compares the use of mesophilic and thermophilic bacteria in the dark fermentation step, analyzing the effects on the overall process. Based on experimental results, simulation models developed with Aspen Plus V7.1 ® are used to calculate the mass-and energy balances of the process. Results show that dark fermentation at mesophilic conditions requires a higher amount of feedstocks but almost no heat input as well as smaller equipment. However, better economic performance is assumed for the thermophilic operation of the dark fermentation step.

Chemical engineering transactions, May 20, 2007
The main objective of this work is to evaluate different scenarios of small-scale bioethanol prod... more The main objective of this work is to evaluate different scenarios of small-scale bioethanol production (1000, 5000 and 10000 tons bioethanol/year) from wheat and maize with innovative energy supplying facilities. All of them provide energy exclusively by exploitation of biogenic residual substances of the bioethanol process in order to substitute fossil fuels. Further residuals result from sustainable crop rotation concepts as well as by-products from grain production. The most valuable process options for renewable energy supply are identified as: (1) biogas production from stillage and co-substrates utilised in a combined heat and power (CHP) plant, (2) biogas production from stillage only utilised in a gas-fired boiler, and (3) process steam production by straw incineration. Process simulation results show that 16 out of 18 analysed plant scenarios achieve at least 100 % thermal energy supply by renewables.
Chemie Ingenieur Technik, Jul 25, 2012
Abbildung. Membranflächen für zweistufige Trennung mit konventionellen Membranen. Abbildung. Form... more Abbildung. Membranflächen für zweistufige Trennung mit konventionellen Membranen. Abbildung. Formel zur Temperaturabhängigkeit der Löslichkeit.
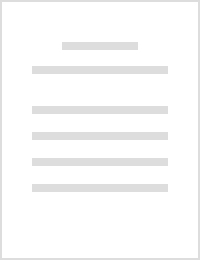
Chemical Engineering and Processing, Dec 1, 2014
Abstract Due to the important role of thermal membrane separation processes for the chemical indu... more Abstract Due to the important role of thermal membrane separation processes for the chemical industry, simulation of those process steps is more and more relevant. In the simulation software AspenPlus© no unit operation for a membrane distillation step is available. Due to the lack of built in membrane distillation (MD) models, the aim of this work was to develop one for application in conceptual design on the AspenPlus © platform. Therefore, this paper presents a user-customize one dimensional unit operation for vacuum MD on the basis of the dusty gas model. Binary butanol water mixtures of different concentrations served as feed streams. Experimental investigations on a hollow fibre and tubular polypropylene (PP) membrane module with a pore diameter of 0.2 μm resulted in raw data on transmembrane flux and selectivity. These experiments served to generate a component permeance data bank. On the basis of the results, a regression for the component permeance was performed. The implementation of the generated permeance functions in the programming code resulted in a unit operation in AspenPlus © reproducing well the experimental work. Comparison of the model with the laboratory results show very good reliability for the different membranes investigated.
Bioresource Technology, Aug 1, 2012
h i g h l i g h t s " The addition of bubble inducting materials is beneficial for inert gas redu... more h i g h l i g h t s " The addition of bubble inducting materials is beneficial for inert gas reduction. " For optimal bacteria growth in dark fermentation cysteine is required in the medium. " Reduced pressure is an alternative method to inert gas sparging. " For large scale application vacuum-sealed systems are necessary.
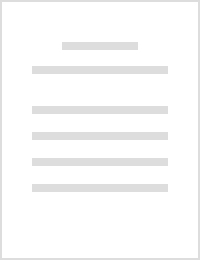
Chemical Engineering and Processing, Jun 1, 2016
Abstract Pervaporation experiments of dilute aqueous butanol solutions were carried out with thre... more Abstract Pervaporation experiments of dilute aqueous butanol solutions were carried out with three PDMS [poly(dimethyl siloxane)] membranes. Based on the experimental results of the best performing membrane a regression for both butanol and water permeability was done in the software R and implemented in a user defined pervaporation unit operation in the software Aspen Custom Modeler. With the implementation of the pervaporation step in Aspen Plus the hybrid pervaporation and distillation purification chain can be simulated in consistent way. Calculation of pervaporation of a 0.5 wt% BuOH-water solution with the experimentally investigated PDMS membrane results in a permeate stream with a concentration of 9 wt% BuOH. Application of membrane distillation resulted in a permeate butanol concentration of only 3 wt% and a considerable higher specific energy demand compared to pervaporation. For product purities of 99 wt% of BuOH a hybrid pervaporation and distillation process saves around 50% of the energy demand compared to state of the art distillation. A sensitivity analysis of the pervaporation step reveals, that for the hybrid pervaporation and distillation process compared to state of the art distillation the energy demand decreases already exceeding 5 wt% BuOH in the permeate stream.
Applied Thermal Engineering, Nov 1, 2007
Process simulation was used to decrease the external heat demand during the production of bioetha... more Process simulation was used to decrease the external heat demand during the production of bioethanol by integration in a network of facilities for heat and power generation. Models for bioethanol fermentation and purification process, the production of DDGS as well as production and utilization of biogas were developed to calculate the heat demand of bioethanol-production and the amount of heat and power generated from residues of the bioethanol process. Depending on the form of biogas utilization (CHP-plant, biogas fired boiler) and the capacity of the bioethanol plant, the conversion of stillage from the bioethanol process to biogas covers a considerable amount of the heat demand necessary for bioethanol-production and purification.
Elsevier eBooks, 2007
The economic competitiveness of ethanol as a liquid fuel strongly depends on the amount of energy... more The economic competitiveness of ethanol as a liquid fuel strongly depends on the amount of energy used during the production. To a sustainable production of fuel ethanol contributes also the use of energy from renewable sources. Process simulation is used to integrate a bio-ethanol plant in a network of facilities for heat and power production from residues of ethanol and feedstock production. Results show that depending on plant capacity and form of biogas utilization it is possible to cover heat demand using biogas produced from stillage of bioethanol fermentation. Partial combustion of straw from feedstock production even enables to cover the heat demand of small ethanol facilities.
Uploads
Papers by Walter Wukovits