Papers by Vladimir Brailovski
... a temperature of the heat treatment intended to restore the superelasticity or shape ... for ... more ... a temperature of the heat treatment intended to restore the superelasticity or shape ... for specimens annealed at 550 and 625 C reveals beneficial effect of the ... OPTIMIZATION OF THE POST-DEFORMATION ANNEALING HEAT TREATMENT FOR NITI SHAPE MEMORY ALLOYS ...
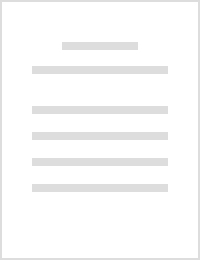
Clinical Biomechanics, 2015
Spinal disorders can be treated by several means including fusion surgery. Rigid posterior instru... more Spinal disorders can be treated by several means including fusion surgery. Rigid posterior instrumentations are used to obtain the stability needed for fusion. However, the abrupt stiffness variation between the stabilized and intact segments leads to proximal junctional kyphosis. The concept of spinal rods with variable flexural stiffness is proposed to create a more gradual transition at the end of the instrumentation. Biomechanical tests were conducted on porcine spine segments (L1-L6) to assess the stabilization capacity of spinal rods with different flexural stiffness. Dual-rod fusion constructs containing three kinds of rods (Ti, Ti-Ni superelastic, and Ti-Ni half stiff-half superelastic) were implanted using two anchor arrangements: pedicle screws at all levels or pedicle screws at all levels except for upper instrumented vertebra in which case pedicle screws were replaced with transverse process hooks. Specimens were loaded in forward flexion, extension, and lateral bending before and after implantation of the fusion constructs. The effects of different rods on specimen stiffness, vertebra mobility, intradiscal pressures, and anchor forces were evaluated. The differences in rod properties had a moderate impact on the biomechanics of the instrumented spine when only pedicle screws were used. However, this effect was amplified when transverse process hooks were used as proximal anchors. Combining transverse hooks and softer (Ti-Ni superelastic and Ti-Ni half stiff-half superelastic) rods provided more motion at the upper instrumented level and applied less force on the anchors, potentially improving the load sharing capacity of the instrumentation.
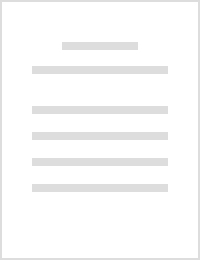
Proceedings of the Institution of Mechanical Engineers. Part H, Journal of engineering in medicine, Jan 23, 2015
This study investigates the use of braided tubular superelastic cables, previously used for stern... more This study investigates the use of braided tubular superelastic cables, previously used for sternum closure following sternotomy, as sublaminar fixation method. It compares the biomechanical performance of spinal instrumentation fixation systems with regular sublaminar cables and proprietary superelastic cables. A hybrid experimental protocol was applied to six porcine L1-L4 spinal segments to compare multifilament sublaminar cables (Atlas, Medtronic Sofamor Danek, Memphis, TN) with proprietary superelastic cables. First, intact total range of motion was determined for all specimens using pure moment loading. Second, pure moments were imposed to the instrumented specimens until these intact total ranges of motion were reproduced. Compared to the intact specimens, the use of superelastic cables resulted in stiffer instrumented specimens than the use of multifilament cables for all the loading modes except axial torsion. Consequently, the superelastic cables limited the instrumented s...
Materials Science and Engineering, 1986
ABSTRACT
Experimental Techniques, 2009
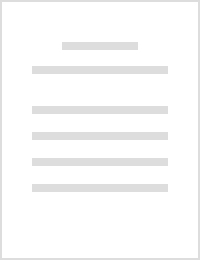
ESOMAT 2009 - 8th European Symposium on Martensitic Transformations, 2009
ABSTRACT Comparative HV-microhardness and TEM studies of Ti-50.0at%Ni and 50.26at%Ni alloys subje... more ABSTRACT Comparative HV-microhardness and TEM studies of Ti-50.0at%Ni and 50.26at%Ni alloys subjected to cold-rolling (e=0.3, 1 and 1.72) and post-deformation annealing at 100-700°C (1 hour) are presented. Based on the TEM-measured grain size data for Ti-50.0at%Ni alloy as a function of an annealing temperature (TPDA) higher than 250°C, it was possible to evaluate the grain size (d) of the near-equiatomic Ti-Ni alloys at TPDA<250°C, using exponential extrapolation distribution of the d-TPDA data. It was shown that below a critical grain size (dc = 10 nm), the smaller the grain size (as a result of the decrease in annealing temperature), the lower the microhardness. This softening phenomena can be described, with good correlation between the approximation and experimental data, by the normal-abnormal Hall-Petch transition caused by the influence of the intercrystalline regions and by the melting temperature grain-size dependence. Note to the reader: On pages 05011-p3, 05011-p4 and 05011-p5 several mistakes have been corrected on October 19, 2009.
ESOMAT 2009 - 8th European Symposium on Martensitic Transformations, 2009
ABSTRACT

Metallography, Microstructure, and Analysis, 2014
AbstrAct Purpose: The major problem restricting universal employment of intermetallic phase base ... more AbstrAct Purpose: The major problem restricting universal employment of intermetallic phase base alloy is their low plasticity which leads to hampering their development as construction materials. The following work concentrates on the analysis of microstructure and plasticity of ordered FeAl (B2) alloy during cold and hot deformation and rolling process. Design/methodology/approach: After casting and annealing, alloy specimens were subjected to axialsymmetric compression in the Gleeble 3800 simulator at temperatures ranging from 800, 900 and 1000°C at 0.1s -1 strain rate. In order to analyse the processes which take place during deformation, the specimens after deformation were intensely cooled with water. The process was conducted on the K -350 quarto rolling mill used for hot rolling of flat products. The process was conducted in some stages at temperature ranging from 1200-1000°C: Structural examination was carried out using light microscopy. The examination of the substructure was carried out by transmission electron microscopy (TEM). Findings: The research carried out enabled the understanding of the phenomena taking place during hot rolling of the investigated alloy. which has been also confirmed in plastometric studies conducted in the form of hot compression tests. The microstructure analyses applying optic and electron microscopy have revealed the structure reconstruction processes occurring in FeAl alloys during cold and hot deformation. Practical implications: The research carried out enabled the understanding of the phenomena taking place during deformation and annealing of the investigated alloy. The obtained sheets can be used as constructional elements working in complex stress fields, at a high temperature and corrosive environments. The results will constitute the basis for modelling the structural changes. Originality/value: The obtained results are vital for designing an effective thermo -mechanical processing technology for the investigated FeAl alloy.
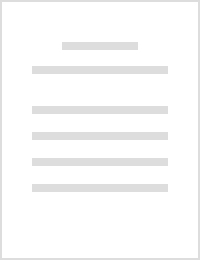
Materials Characterisation V, 2011
ABSTRACT Creep is an important factor that contributes to the load loss and tightness failure of ... more ABSTRACT Creep is an important factor that contributes to the load loss and tightness failure of bolted joints. Retightening of the joint can be expensive, time consuming and therefore is an undesirable solution. Currently most efforts are focussed on reducing load losses directly by tightening to yield, improving material creep properties or making joints less rigid. An alternative solution of current interest is the use of bolts in shape memory alloy (SMAs). However, very few experimental studies are available that demonstrate its feasibility. The objective of this study is to exploit the benefit of the shape memory and superelasticity behaviors of a SMA stud to recover the load losses due to creep and thermal exposure of a gasket in a bolted joint assembly. This paper explores several avenues to investigate and model the thermo-mechanical properties of a bolted joint with a Nickel-Titanium SMA stud. A stiffness-based analytical model which incorporates the Likhachev model of SMA is used as a representation of an experimental bolted joint assembly. Using this model the rigidity of the experimental setup is optimized to make the best use of the SMA properties of the stud. This theoretical model is validated by a Finite Element (FE) Model using a custom FE material model which also implements the SMA material model. Finally an experimental test bench with an optimized stiffness derived from analytical simulations is used, with and without gaskets to demonstrate the ability of the SMA stud to recover load losses. Keywords: shape memory alloys, bolted joints, creep, superelasticity, SMA. 1 Introduction Load losses due to creep in any bolted joint can be problematic, even small creep losses of 0.1mm, can cause a total loss of bolt load. Several methods are in use to
Materials Science Forum, 2012
ABSTRACT The processes of structure formation in Ti-Ni and in Ti-Nb-Zr, Ti-Nb-Ta shape memory all... more ABSTRACT The processes of structure formation in Ti-Ni and in Ti-Nb-Zr, Ti-Nb-Ta shape memory alloys (SMA) under thermomechanical treatment (TMT) were studied. The TMT comprised cold rolling with true strains from e=0.25 to 2 and post-deformation annealing. Differences in these processes between two groups of alloys are considered. The main conclusions are as follows: nanostructures created by TMT are useful for radical improvement of the SMA functional properties, and an optimum nanostructure (nanocrystalline structure, nanosubgrained structure or theirmixture) should be selected by taking into account other structural and technological factors.
Materials Science Forum, 2008
Materials Science Forum, 2008
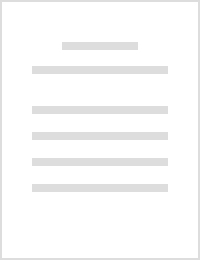
Materials Science Forum, 2013
ABSTRACT The influence of thermomechanical processing on the Ti-21.8Nb-6Zr (TNZ) and Ti-19.7Nb-5.... more ABSTRACT The influence of thermomechanical processing on the Ti-21.8Nb-6Zr (TNZ) and Ti-19.7Nb-5.8Ta (TNT) (at%) alloys’ structure, phase composition, mechanical and functional properties is studied. Both alloys possess polygonized dislocation substructure (average subgrain size 100 nm), and manifest superelastic behavior at room temperature and recovery stress generation during constant-strain temperature scanning experiments. After aging treatment, both alloys were -phase precipitation hardened, but their mechanical behavior was impacted differently -- it was detrimental for TNZ and beneficial for TNT. The different impact of aging heat treatment on the mechanical behavior of these alloys is explained by the differences in the -phase nucleation rate, precipitates’ size, shape, volume fraction and distribution, and by their effect on the alloys’ critical stresses and transformation temperatures.
Materials Science Forum, 2012
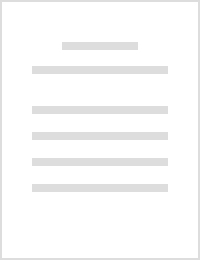
Materials Science Forum, 2013
ABSTRACT The Ti-21.8Nb-6Zr and Ti-19.7Nb-5.8Ta (at.%) shape memory alloys are thermomechanically ... more ABSTRACT The Ti-21.8Nb-6Zr and Ti-19.7Nb-5.8Ta (at.%) shape memory alloys are thermomechanically treated by cold drawing and post-deformation annealing at 550-600°C forming a nanosubgrained structure in the β-phase. Cyclic mechanical testing using a “loading-unloading” mode with 2% tensile strain in each half-cycle reveals the non-perfect superelastic behavior of both alloys during the very first cycles of testing, which becomes perfect during further mechanocycling. The Young’s modulus of thermomechanically-treated alloys is low (about 45 GPa), and it decreases during mechanocycling (n=10 cycles) down to 25-35 GPa, approaching the Young’s modulus of cortical bone tissues. The Young’s modulus obtained in the 10th cycle is stable or changes only slightly during a further 40-day pause at room temperature and then during repeated mechanocycling. The residual strain per cycle, the transformation yield stress and the mechanical hysteresis decrease during mechanocycling. Subsequent to a 40-day pause at room temperature, they restore their initial values. Repeated mechanocycling is accompanied by a repeated decrease of these parameters.
Materials Science Forum, 2013
The technique and preliminary results of in situ X-ray diffraction analysis of the martensitic tr... more The technique and preliminary results of in situ X-ray diffraction analysis of the martensitic transformation in the newly developed Ti-Nb-Zr SMA for biomedical application are presented. To perform the in situ analysis, an original tensile stage, powered by a Ti-Ni SMA actuator and fit within the "TTK450" thermal chamber of a "PANalytical X'Pert Pro" diffractometer is designed, manufactured and validated. The tensile stage working principle and analysis methodology are described in detail. Preliminary results obtained during in-situ X-ray analysis of the phase transformations in Ti-Nb-Zr SMA are also presented.
Uploads
Papers by Vladimir Brailovski