Papers by Theresa Coetsee
Low temperature vaporisation of Cr from fluoride flux reacted at 1350 °C with Al–Cr–Fe powder: Thermochemical analysis of gas phase reactions and nano-strand formation
Journal of materials research and technology/Journal of Materials Research and Technology, May 1, 2024

Mineral Processing and Extractive Metallurgy Review, Jul 15, 2019
Manganese ore smelting is reviewed in terms of processing parameters such as feed material partic... more Manganese ore smelting is reviewed in terms of processing parameters such as feed material particle sizes, energy input methods, heat transfer modes, smelting mechanisms, experimental findings on specific smelting aspects, and rates of MnO reduction and carbon dissolution into ferrous alloys. This paper provides a comprehensive current review of our fundamental understanding of manganese ore smelting. Process parameters and resultant cost effects are discussed in terms of existing industrial smelting processes, the Submerged Arc Furnace (SAF) and the Blast Furnace (BF), and the AlloyStream process demonstration plant. Bench-scale experimental results for AlloyStream induction furnace smelting are discussed with reference to rate measurements reported in literature. The experimental results clearly illustrate the importance of higher alloy bath temperatures in induction smelting to improve alloy production rates, whilst the effect of alloy bath chemistry was of less importance. AlloyStream process benefits and issues are discussed with reference to the SAF and BF processes.

Extensive work is reported in literature on the reduction of iron oxides with carbonaceous reduct... more Extensive work is reported in literature on the reduction of iron oxides with carbonaceous reductants. Most of this work considered isothermal reaction of the material mixture, although as shown in some studies, isothermal reaction conditions are not often the norm because of sample size and heating arrangement in the experiment. In industrial processes, such as the rotary hearth type processes and the IFCON ® process for iron ore reduction, the norm is non-isothermal reaction. Simulation of industrial processes should take non-isothermal reaction into account if the heat transfer effects within the process are to be investigated. To avoid the complications of coal volatiles in the experimental setup , few studies were done with coal as reductant. The primary aim of the work presented here is to quantify radiation heat transfer to the surface of an iron ore and coal mixture heated uni-directionally from the sample surface to show the importance of heat transfer in the IFCON ® process. Secondary aim of this work are to show the effects of layer thickness, coal volatiles, phase chemistry and particle size in this reaction system. The experimental setup consists of a tube furnace modified to transport the sample into and out of the experimental tube furnace heating zone under a protected atmosphere, whilst the product gas is analysed throughout the experiment by quadropole mass spectrometer. The sample surface temperature, heating zone temperatures and material bed temperatures were measured throughout the experiment. A sample cutter-splitter was developed to divide the reacted sample into three horizontal segments for chemical analyses. The sample surface temperature and the heating zone temperatures were used as inputs to a radiation network calculation to quantify radiation heat transferred to the sample surface. The radiation network calculation was calibrated against heat-mass balance calculations for pre-reduced ore and graphite samples reacted at furnace temperatures of 1300, 1400 and 1500°C. The results show that radiative and conduction heat transfer control prevails for 16 mm to 40 mm material layers heated uni-directionally from the material layer surface. It is shown that coal volatiles contribute to reduction in the stagnant material layer. Also, smaller particle sizes result in increased reaction rates because of a decrease in the diffusion limited effects which were seen in reaction of the base size of coal and ore particles.
Identifying Oxygen Transfer Pathways During High Heat Input Submerged Arc Welding: A Case Study into CaF2-SiO2-CaO-TiO2 Fluxes
Metallurgical and Materials Transactions B

Processes
The scope of this work is to improve the SAW process understanding and present an improved descri... more The scope of this work is to improve the SAW process understanding and present an improved description of the SAW process in terms of gas-slag-metal reactions with alloy powder and Al powder additions. The scope does not include the materials properties of the weld metal. The latter may easily be optimised in the future by changing the weld metal chemistry once the process reactions of different element powders in SAW are understood. Aluminium as de-oxidiser element was applied to SAW to lower the oxygen partial pressure in the process. The results show the Al-Ni-Cr-Co-Cu alloyed weld metal total oxygen content was reduced to 257 ppm O, compared to the base case weld metal at 499 ppm O, made with the same flux and no metal powder additions. Thus, the aluminium that was added as a de-oxidiser element to the SAW process effectively lowered the original flux-induced partial oxygen pressure, both in the arc cavity and at the interface of the molten flux–weld pool phases. This partial ox...

Journal of The South African Institute of Mining and Metallurgy, Feb 10, 2023
The CSIR-Ti process employs lithiothermic reduction of titanium tetrachloride feedstock to produc... more The CSIR-Ti process employs lithiothermic reduction of titanium tetrachloride feedstock to produce titanium sponge. The product is therefore contaminated by a range of lithium and chloride species. In this study we examine the effects of particle size, temperature, and HCl concentration as input leaching variables on the removal of chlorides from the crude titanium sponge. A review of the aqueous chloride chemistry of Li and Ti provided initial conditions for leaching of impurity species from the sponge. Experimental results confirm that the effectiveness of leaching and removal of dissolved impurities from the sponge are dependent on leaching kinetics, which are influenced by temperature, particle size, and morphology. Of the variables tested, reaction temperature had the strongest influence on the oxygen content of the leached product. The HCl lixiviant concentration had a negligible effect under the conditions tested. Leaching of crude titanium sponge (−10 mm size fraction after crushing) at 14°C in either 1 M or 0.032 M HCl yielded a titanium sponge product that met the ASTM standard specification for commercially pure Grade 1 titanium, i.e., oxygen content < 0.18 mass% and chloride content < 0.15 mass%.

Journal of The South African Institute of Mining and Metallurgy, 2020
The CSIR is developing a process to produce commercially pure (CP) Grade 4 titanium metal powder ... more The CSIR is developing a process to produce commercially pure (CP) Grade 4 titanium metal powder via direct metallothermic reduction of TiCl 4. Crude titanium produced by this method is inevitably contaminated with unreacted reducing metal and titanium subchlorides occluded in halide salt. For the product to meet stringent titanium industry quality requirements, the concentration of impurities must be held to acceptably low levels. Acid leaching was identified as a suitable method for purifying the crude reduction mass, due to the solubility of the by-products and the potential for cost-saving provided by this method compared to vacuum distillation. However, purification by leaching poses drawbacks such as high oxygen impurity concentrations in the product, due to the dissolution of subchlorides in water to form insoluble hydroxides and oxychlorides that concentrate on the surface of the titanium powder. The crude titanium was leached under different conditions using water and 1 M and 0.035 M hydrochloric acid at a temperature below 50°C. The 1 M acid leach yielded a product with the lowest oxygen content, demonstrating that when the pH of the media and temperature are controlled, the drawbacks associated with acid leaching can be overcome and the process used successfully for downstream purification of the crude product.
Processes, Oct 1, 2021
This article is an open access article distributed under the terms and conditions of the Creative... more This article is an open access article distributed under the terms and conditions of the Creative Commons Attribution (CC BY

Processes
Aluminium metal is not typically added to the submerged arc welding (SAW) process because it is e... more Aluminium metal is not typically added to the submerged arc welding (SAW) process because it is easily oxidised to form unwanted slag in the weld pool. The successful application of aluminium as a de-oxidiser is illustrated in this study by preventing oxidation of Cr and Co to their oxides, thereby preventing element loss to the slag. Unconstrained pure metals of Al, Cr, Co and Cu were applied to investigate the gas formation behaviour of these elements in the SAW arc cavity. Of interest is the effect of copper in the arc cavity in terms of its possible substitution for aluminium. The results confirmed that the Al-Cr-Co-Cu alloyed weld metal total oxygen content was lowered to 176 ppm O, in comparison to 499 ppm O in the weld metal formed from welding with the original flux, which excluded metal powder additions. This lower ppm O value of 176 ppm O confirms that the added aluminium powder effectively lowered the original flux-induced partial oxygen pressure in the arc cavity, and at...
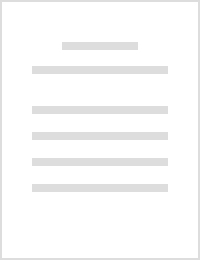
Purification of titanium sponge produced by lithiothermic reduction of titanium tetrachloride: Effect of leaching conditions
Journal of the Southern African Institute of Mining and Metallurgy
The CSIR-Ti process employs lithiothermic reduction of titanium tetrachloride feedstock to produc... more The CSIR-Ti process employs lithiothermic reduction of titanium tetrachloride feedstock to produce titanium sponge. The product is therefore contaminated by a range of lithium and chloride species. In this study we examine the effects of particle size, temperature, and HCl concentration as input leaching variables on the removal of chlorides from the crude titanium sponge. A review of the aqueous chloride chemistry of Li and Ti provided initial conditions for leaching of impurity species from the sponge. Experimental results confirm that the effectiveness of leaching and removal of dissolved impurities from the sponge are dependent on leaching kinetics, which are influenced by temperature, particle size, and morphology. Of the variables tested, reaction temperature had the strongest influence on the oxygen content of the leached product. The HCl lixiviant concentration had a negligible effect under the conditions tested. Leaching of crude titanium sponge (-10 mm size fraction after ...

Processes
This review is focused on the thermochemical behaviour of fluxes in submerged arc welding (SAW). ... more This review is focused on the thermochemical behaviour of fluxes in submerged arc welding (SAW). The English-language literature from the 1970s onwards is reviewed. It was recognised early on that the thermochemical behaviour of fluxes sets the weld metal total ppm O and the element transfer extent from the molten flux (slag) to the weld pool. Despite the establishment of this link between the flux-induced oxygen potential and element transfer, it is also well accepted that the slag–metal equilibrium does not control SAW process metallurgy. Instead, the gas phase must be taken into account to better describe SAW process metallurgy equilibrium calculations. This is illustrated in the gas–slag–metal equilibrium simulation model developed by Coetsee. This model provides improved accuracy in predicting the weld metal total ppm O values as compared to the empirical trend of Tuliani et al. Recent works on the application of Al metal powder with alloying metal powders provide new insights ...

Processes
Unconstrained metal powders of Cu, Cr, Ni and Al were applied to submerged arc welding (SAW) to c... more Unconstrained metal powders of Cu, Cr, Ni and Al were applied to submerged arc welding (SAW) to clarify the chemical behaviour of copper in this modified SAW process. Aluminium metal is avoided in SAW because it is easily oxidised. Excessive aluminium oxides in the form of slag or inclusions in the weld metal will lead to poor weld metal materials properties. Aluminium is an effective deoxidiser and can be used to prevent Cr and Ni loss to the slag by preventing oxidation of these metals. The results show that carbon steel was alloyed to 5.3% Cr, 5.3% Ni, 3.6% Al and 5.2% Cu at 80% Cr yield, 81% Ni yield, 54% Al yield and 79% Cu yield. BSE (backscattered electron) images of the three-dimensional (3D) post-weld slag sample show 3D structures within the slag dome. The 3D structures contain features of vapour formation and recondensation. In addition, nano-strands appear in the 3D structures and confirm the vaporisation and recondensation of fluorides. The chemical behaviour of copper ...

Processes
Aluminium metal is avoided as main reactant in submerged arc welding (SAW) because it is easily o... more Aluminium metal is avoided as main reactant in submerged arc welding (SAW) because it is easily oxidised in this process. Aluminium is an effective de-oxidiser and can be used to prevent Cr and Co loss to the slag by preventing oxidation of these metals. In our novel application of aluminium metal powder in SAW we demonstrate the modification of flux oxygen behaviour. The Co-Cr-Al-alloyed weld metal total oxygen content is decreased to 180 ppm O, compared to 499 ppm O in the weld metal from the original flux, welded without metal powder additions. The flux oxygen behaviour is modified by the added aluminium powder through the lowering of the original flux-induced partial oxygen pressure in the arc cavity and at the molten flux-weld pool interface. Carbon steel was alloyed to 5.9% Co, 6.3 % Cr and 5.1% Al at 81% Co yield, 87% Cr yield and 70% Al yield. Gas-slag-alloy thermochemical equilibrium calculations confirm the partial oxygen-pressure-lowering effect of aluminium. BSE (backsca...

Minerals
Chromium alloying of weld metal is usually accomplished via weld wire. This is done because chrom... more Chromium alloying of weld metal is usually accomplished via weld wire. This is done because chromium has a high affinity for oxygen and is therefore not easily transferred across the arc. The formation chromium (VI) is one of the main concerns in welding with chromium containing consumables, especially in open arc processes, and less so in SAW (submerged arc welding). This study investigates the chemical behaviour of chromium in the application of unconstrained metal powders of Al, Cr, Cu and Ti in SAW. The application of aluminium in SAW is used to control the oxygen partial pressure in the process to prevent oxidation of elements of high oxygen affinity, such as chromium. The speciation of chromium was investigated in two-dimensional (2D) and three-dimensional (3D) post-weld slag samples. In the 2D slag samples, the chromium is contained in low concentrations in the oxy-fluoride matrix phase. The 3D samples showed dome structures in which evidence of vapour formation was identifie...

Journal of the Southern African Institute of Mining and Metallurgy, 2021
SYNOPSIS Accretions often form in furnaces when slag and charge materials attach to the refractor... more SYNOPSIS Accretions often form in furnaces when slag and charge materials attach to the refractory wall and build up over time. Accretion formation is usually unwanted because it reduces the working volume of the reactor and hinders material flow through the reactor. However, in some instances a thin, stable accretion layer may be desirable to protect the underlying refractory material. In order to prevent and/or manage accretion formation, it is important to understand the underlying principles of this phenomenon in the particular reactor. Excessive accretion formation hampered production at the Exxaro FerroAlloys ferrosilicon melting and atomization plant. This plant uses induction furnaces in which a 15% silicon-iron alloy is produced by batch smelting a mixture of ferrosilicon of 75%Si grade and low-carbon steel. The molten ferrosilicon alloy is then gas-atomized to a powdered product for use as a dense medium in mineral processing plants. The objective of this study was to inve...

Journal of the Southern African Institute of Mining and Metallurgy, 2020
The CSIR is developing a process to produce commercially pure (CP) Grade 4 titanium metal powder ... more The CSIR is developing a process to produce commercially pure (CP) Grade 4 titanium metal powder via direct metallothermic reduction of TiCl 4. Crude titanium produced by this method is inevitably contaminated with unreacted reducing metal and titanium subchlorides occluded in halide salt. For the product to meet stringent titanium industry quality requirements, the concentration of impurities must be held to acceptably low levels. Acid leaching was identified as a suitable method for purifying the crude reduction mass, due to the solubility of the by-products and the potential for cost-saving provided by this method compared to vacuum distillation. However, purification by leaching poses drawbacks such as high oxygen impurity concentrations in the product, due to the dissolution of subchlorides in water to form insoluble hydroxides and oxychlorides that concentrate on the surface of the titanium powder. The crude titanium was leached under different conditions using water and 1 M and 0.035 M hydrochloric acid at a temperature below 50°C. The 1 M acid leach yielded a product with the lowest oxygen content, demonstrating that when the pH of the media and temperature are controlled, the drawbacks associated with acid leaching can be overcome and the process used successfully for downstream purification of the crude product.

Processes
Unconstrained metal powders of chromium and nickel, in combination with aluminium, were used in t... more Unconstrained metal powders of chromium and nickel, in combination with aluminium, were used in the submerged arc welding (SAW) process to simplify weld metal alloying. Unconstrained metal powders refer to non-alloyed metal powders that are not constrained in tubular wire, such as fluxed-cored and metal-cored wire. Aluminium powder is used to control the oxygen potential at the molten flux–weld pool interface. The results presented here show that the addition of aluminium powder to the weld metal enhances Cr and Ni yields to 89% for Cr and 91% for Ni, compared to lower values reported in pre-alloyed powder application. Alloying of the carbon steel in the base plate and weld wire combination was achieved at 6.0% Cr, 6.2% Ni, and 4.5% Al, with the weld metal oxygen controlled to 162 ppm O. Thermodynamic analysis was applied to investigate the likely gas reactions in the arc cavity emanating from the chemical interaction between Cr, Ni, and Al. The effects of gas-based chemical reactio...

Applied Sciences
The application of cobalt and aluminium powders in unconstrained format, not as metal powder in t... more The application of cobalt and aluminium powders in unconstrained format, not as metal powder in tubular wire nor as pre-alloyed powder, is used in this work to simplify weld metal alloying. The objective of this study is to demonstrate the application of unconstrained cobalt and aluminium powders in Submerged Arc Welding SAW to alloy the weld metal and to control the weld metal oxygen content. Aluminium powder is used to control the oxygen potential at the weld pool-slag interface in order to prevent oxidation of cobalt. The results presented here show that with the addition of Aluminium powder, 70% yield of Cobalt was achieved from the cobalt powder to the weld metal. The carbon steel base-plate material and weld wire materials combination were alloyed to 5.3% Co and 4.2% Al, whilst controlling the weld metal total oxygen content to 230 ppm. Thermodynamic analysis is applied to investigate the possible chemical interaction reactions between Co and Al compounds, as well as the role ...

Applied Sciences
Nickel alloying of carbon steel is used to enhance steel strength and toughness. Nickel alloying ... more Nickel alloying of carbon steel is used to enhance steel strength and toughness. Nickel alloying of the weld metal via solid weld wire presents several difficulties as highlighted previously, such as work hardening of the solid weld wire in manufacturing and feeding through the SAW wire feeding mechanism, and expensive and time consuming manufacturing of multiple weld wire formulations. The application of nickel and aluminium powders in unconstrained format, meaning not as fluxed cored wire or as metal cored wire, is used to simplify weld metal alloying. Al powder is used to control the oxygen potential at the weld pool-molten flux interface. The results presented here show that the addition of Al powder to the weld metal enhances Ni yield to the weld metal, at 85%, compared to pre-alloyed powder Ni yields of 57–78% as applied in previous work. Carbon steel was alloyed to 6.9% Ni and 3.7% Al. Thermodynamic analysis is applied to elucidate the chemical interaction between Ni and Al, ...

Minerals Engineering, 2019
Manganese ores differ extensively in their mineralogical and bulk chemical composition. Consequen... more Manganese ores differ extensively in their mineralogical and bulk chemical composition. Consequently these ores follow different mineralogical morphology development paths as the reduction reaction proceeds in the production furnace. Mineralogical factors such as composition and distribution of initial liquid silicate formed at specific temperatures, as well as iron and manganese metallisation patterns, are significant determining factors in the relative importance of different parallel reduction reaction mechanisms in each ore type. Applied mineralogy techniques were used to identify and analyse matrix liquid silicate phase formation in manganese ore reacted at 1300°C with Carbon Black reductant. The study includes three South African ores from the Kalahari Manganese Field, the ores represent both the Wessels-type and Mamatwan-type mineralogy. FactSage computational thermodynamic calculations were made to explain liquid silicate phase formation and its evolution with increased reaction time. Matrix silicate phase liquidus temperatures and pseudo-ternary phase diagrams in the MnO-FeO-SiO 2-CaO-MgO-Al 2 O 3 composition system were calculated. Matrix liquid silicate formed at the relatively low reaction temperature of 1300°C within all three ores, although different quantities of liquid silicate formed along differing composition paths set by ore mineralogy.
Uploads
Papers by Theresa Coetsee