Papers by Sandro Birolini
Technometrics, May 1, 1999
The use of general descriptive names, registered names, trademarks, etc. in this publication does... more The use of general descriptive names, registered names, trademarks, etc. in this publication does not imply, even in the absence of a specific statement, that such names are exempt from the relevant protective laws and regulations and therefore free for general use.

Reliability and availability analysis of repairable systems is generally performed using stochast... more Reliability and availability analysis of repairable systems is generally performed using stochastic processes, including Markov, semi-Markov, and semi-regenerative processes. Markov processes apply when all involved times (failure-free, repair, logistic) are exponentially distributed. If only failure-free times are exponentially distributed, the involved process is regenerative with at least one regeneration state. Because of MTTF << MTTR (mean time to failure << mean time to repair or to restore), Markov processes can be used in most practical applications as good approximation for real situations. Nevertheless, the number of states involved in large systems, can cause computational difficulties. The use of approximate expressions can help to solve such problems, allowing also a greater computational transparency. This contribution is based on the 6th Ed. of the author's book Reliability Engineering [1 (2010)] and shows versatility & utility of approximate expressions, in particular of those based on macro-structures.

Lecture Notes in Economics and Mathematical Systems, 1985
Velocity estimation is generally under-determined. To obtain a pleasing result we impose some typ... more Velocity estimation is generally under-determined. To obtain a pleasing result we impose some type of regularization criteria such as preconditioning , limiting inversion solutions to large singular values , or characterizing the model through a small number of spline coefficients . These methods all create velocity models that can correctly model the recorded travel times, but are often geologically unrealistic. To create more geologically feasible velocity models and to speed up convergence, Michelena and Harris (1991) suggested using varying sized grid cells. Unfortunately, such a parameterization is prone to error when the wrong size blocks are chosen (Delprat-Jannaud and Lailly, 1992). Other authors have suggested locally clustering grid cells or characterizing the velocity model as a series of layers . These methods are also susceptible to errors when the wrong parameterization is chosen. An attractive alternative approach is to add an additional model regularization term to the objective function (van Trier, 1990). In theory, this regularization term should be the inverse model covariance matrix (Tarantola, 1987) obtained from some a priori information sources.
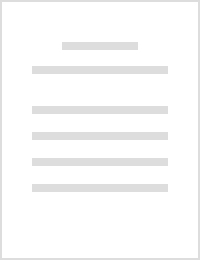
Quality and Reliability of Technical Systems, 1994
Quality and reliability assurance of complex equipment and systems requires from all engineers in... more Quality and reliability assurance of complex equipment and systems requires from all engineers involved in a project a set of specific activities from the definition to the operating phase, performed concurrently to achieve the best performance, quality, and reliability for given cost and time schedule targets. This includes the definition of goals, planning and performing analyses and tests, selection and qualification of components and materials, management of the configuration, qualification and control of production processes and procedures, as well as quality and reliability growth during production. Many of these activities are engineering tasks, others are more for coordination and control. This chapter introduces the basic concepts and discusses the main tasks and organizational requirements necessary to assure cost effectively the quality and reliability of complex equipment and systems.
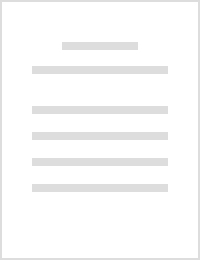
Quality and Reliability of Technical Systems, 1994
Components and materials have a major impact on the quality and reliability of the equipment and ... more Components and materials have a major impact on the quality and reliability of the equipment and systems in which they are used. Their selection and qualification must therefore be considered carefully. Besides cost and availability on the market, important selection criteria are the intended application (particular stresses), technology, quality, long-term behavior of relevant parameters, and reliability. Qualification includes characterization (at different thermal and electrical stresses), environmental tests, reliability tests, and failure analysis. This chapter deals first with the selection criteria for electronic components and then considers the qualification of complex integrated circuits (for the qualification of electronic assemblies one can refer to Section 8.3, screening of components and assemblies are considered in Sections 8.2 and 8.4, respectively). Failure modes, mechanisms, and analysis of electronic components are described in Section 3.3. Section 3.4 gives important design guidelines for reliability at the component and assembly level.

Reliability (RAMS) assurance has to be continued during the production phase, coordinated with ot... more Reliability (RAMS) assurance has to be continued during the production phase, coordinated with other quality assurance activities. In particular, for monitoring and controlling production processes, item configuration, in-process and final tests, screening procedures, and collection, analysis and correction of defects and failures. The last measure yields to a learning process whose purpose is to optimize the quality of manufacture, taking into account cost and time schedule limitations. This chapter introduces some basic aspects of quality and reliability (RAMS) assurance during production, discusses test and screening procedures for electronic components and assemblies, introduces the concept of cost optimization related to a test strategy and develops it for a cost optimized test and screening strategy at the incoming inspection. For greater details one may refer to [7.1 - 7.5, 8.1 - 8.14] for qualification and monitoring of production processes, as well as to [8.21 - 8.35] for t...
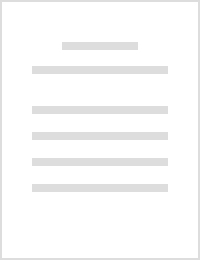
At the equipment and system level, maintainability has a significant influence on reliability and... more At the equipment and system level, maintainability has a significant influence on reliability and availability. This is particularly true if redundancy has been implemented and redundant parts can be repaired on line, i.e. without interruption of operation. Maintainability thus represents an important parameter in the optimization of the life-cycle cost (LCC). Achieving a high maintainability target requires appropriate activities which must be started early in the design phase and be coordinated by a maintenance concept. To this belong fault detection and isolation (attained with built-in tests), partitioning of the equipment or system into almost independent last repairable units (spare parts at equipment or system level), and realization of logistical support (also including after-sales service). Because of the diversity of equipment and systems as well as maintainability requirements, a maintenance concept must generally be tailored to the specific project considered. After a brief discussion of the basic terms, this chapter introduces the maintenance concept as applied to complex equipment and systems, and deals then with design guidelines for maintainability and testability, maintainability calculation techniques, and basic models for spare part provisioning.
Zuverlässigkeit von Geräten und Systemen, 1997
Qualitats- und Zuverlassigkeitsforderungen sind wichtig, um spezifizierte operationelle Bedingung... more Qualitats- und Zuverlassigkeitsforderungen sind wichtig, um spezifizierte operationelle Bedingungen zu erfullen sowie um Betriebs- und Instandhaltungskosten unter Kontrolle zu halten. Sie schaffen klare Voraussetzungen fur den Entwicklungsingenieur, mussen aber nach dem Grundsatz so gut wie notig formuliert werden, denn ubertriebene Forderungen konnen die Marktchancen eines Gerats oder Systems negativ beeinflussen. Nach einer kurzen Darlegung der allgemeinen Kundenforderung bezuglich Qualitats- und Zuverlassigkeitssicherungen von Geraten und Systemen sowie des Zusammenhangs zwischen Lebenslaufkosten und Qualitats- bzw. Zuverlassigkeitsforderungen wird in diesem Kapitel ausfuhrlich auf die Festlegung und Durchsetzung von Zuverlassigkeitsforderungen eingegangen.
Reliability Engineering, 2013
Reliability (RAMS) assurance has to be continued during the production phase, coordinated with ot... more Reliability (RAMS) assurance has to be continued during the production phase, coordinated with other quality assurance activities. In particular, for monitoring and controlling production processes, item configuration, in-process and final tests, screening procedures, and collection, analysis & correction of defects and failures.
Reliability Engineering, 2013
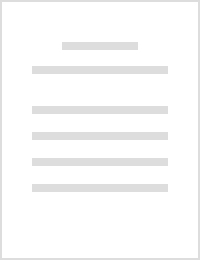
Reliability Engineering, 2010
The purpose of reliability engineering is to develop methods and tools to evaluate and demonstrat... more The purpose of reliability engineering is to develop methods and tools to evaluate and demonstrate reliability, maintainability, availability, and safety of components, equipment, and systems, as well as to support development and production engineers in building in these characteristics. In order to be cost and time effective, reliability engineering must avoid bureaucracy, be integrated in project activities, and support quality assurance and concurrent engineering efforts. This chapter introduces basic concepts, shows their relationships, and discusses the tasks necessary to assure quality and reliability of complex equipment and systems with high quality and reliability requirements. A comprehensive list of definitions is given in Appendix Al. Standards for quality management systems are discussed in Appendix A2. Refinements of management aspects are given in Appendices A3 — A5 for the cases in which tailoring is not mandatory.

Reliability Engineering, 2010
Reliability analysis during the design and development of complex components, equipment & systems... more Reliability analysis during the design and development of complex components, equipment & systems is important to detect and eliminate reliability weaknesses as early as possible and to perform comparative studies. Such an investigation includes failure rate and failure mode analysis, verification of the adherence to design guidelines, and cooperation in design reviews. This chapter presents methods and tools for failure rate and failure mode analysis of complex equipment & systems considered as nonrepairable up to system failure (except for Eq. (2.48)). Estimation and demonstration of a constant failure rate λ or of MTBF for the case MTBF ≡1/λ is in Section 7.2.3. After a short introduction, Section 2.2 deals with series -parallel structures. Complex structures, elements with more than one failure mode, and parallel models with load sharing are investigated in Section 2.3. Reliability allocation with cost considerations is discussed in Section 2.4, stress / strength and drift analysis in Section 2.5. Section 2.6 deals with failure mode and causes-to-effects analyses, and Section 2.7 gives a checklist for reliability aspects in design reviews. Maintainability is considered in Chapter 4, together with spare parts reservation and maintenance strategies with cost considerations. Repairable systems are investigated in Chapter 6 including complex systems for which a reliability block diagram does not exist, imperfect switching, incomplete coverage, reconfigurable systems, common cause failures, as well as an introduction to network reliability, BDD, E T , dynamic F T, Petri nets, computer-aided analysis, and human reliability. Risk management for repairable systems is considered in Section 6.11. Design guidelines are given in Chapter 5, qualification tests in Chapter 3, reliability tests in Chapters 7 & 8. Theoretical foundations for this chapter are in Appendix A6.
Quality and Reliability of Technical Systems, 1994
Zuverlässigkeit von Geräten und Systemen, 1997
In diesem Anhang werden die wichtigsten Begriffe auf dem Gebiet der Qualitatsund Zuverlassigkeits... more In diesem Anhang werden die wichtigsten Begriffe auf dem Gebiet der Qualitatsund Zuverlassigkeitssicherung von Geraten und Systemen eingefuhrt und umfassend diskutiert. Die angegebenen Definitionen berucksichtigen so weit wie moglich die einschlagigen Normen [A1.1–A1.5]. Eine prinzipielle Einstufung der Begriffe ist in Bild A1.1 angegeben.
Zuverlässigkeit von Geräten und Systemen, 1997
Entwicklungsrichtlinien (Design Guidelines) sind wichtig, um bei der Entwicklung und Fertigung vo... more Entwicklungsrichtlinien (Design Guidelines) sind wichtig, um bei der Entwicklung und Fertigung von Geraten und Systemen moglichst viele Ursachen fur Schwachstellen, die schwierig in einer Berechnung zu erfassen sind (Vorschadigungen, Schnittstellenprobleme, EMV-Aspekte, Transiente, Einflus von Fertigungsprozessen usw.), zu eliminieren oder zumindest unter Kontrolle zu halten. Viele dieser Regeln stutzen sich auf Erfahrungen und konnen unterschiedlich aufgenommen werden, sie gelten allgemein als Empfehlungen und stellen fur junge Ingenieure eine wertvolle Hilfe beim Ubertritt in die Praxis dar.
Zuverlässigkeit von Geräten und Systemen, 1997
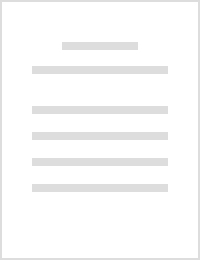
Zuverlässigkeit von Geräten und Systemen, 1997
Zuverlassigkeitsanalysen in der Entwicklungsphase dienen in erster Linie der rechtzeitigen Erkenn... more Zuverlassigkeitsanalysen in der Entwicklungsphase dienen in erster Linie der rechtzeitigen Erkennung und Beseitigung von Schwachstellen und der Durchfuhrung von Vergleichsstudien. Sie umfassen eine Ausfallratenanalyse, d. h. die Berechnung der vorausgesagten Zuverlassigkeit, und eine Ausfallartenanalyse, d. h. die systematische Untersuchung der Art und Auswirkung von Defekten und Ausfallen. In einer beschrankten Form sind auch Instandhaltbarkeitsanalysen moglich. Die Verbindung der Zuverlassigkeits- und Instandhaltbarkeitsaspekte erlaubt die Durchfuhrung von Zuverlassigkeitsanalysen im reparierbaren Fall sowie von Verfugbarkeitsanalysen. Fur Gerate und Systeme spielt ferner zunehmend die Qualitat der Software eine wichtige Rolle. In diesem Kapitel werden die Moglichkeiten solcher Untersuchungen gezeigt. Abgesehen von den Betrachtungen uber die Ausfallraten, die spezifisch fur elektronische Bauteile sind, gelten viele Resultate fur elektronische und fur mechanische Systeme. Auf die speziellen Untersuchungsmethoden mechanischer Systeme wird im Abschnitt 3.1.14 kurz eingegangen. Die fur die Sicherstellung der (intrinsischen) Zuverlassigkeit, Instandhaltbarkeit und Qualitat der Software wichtigen Entwicklungsrichtlinien (design guidelines) werden im Kapitel 4 ausfuhrlich dargelegt. Fur mathematische Grundlagen wird auf Anhang A2 verwiesen.
Reliability Engineering, 1999
A quality data reporting system is a system to collect, analyze, and correct all defects and fail... more A quality data reporting system is a system to collect, analyze, and correct all defects and failures occurring during production and testing of an item, as well as to evaluate and feedback the corresponding quality and reliability data (Fig. 1.8). The system is generally computer aided. Analysis of failures and defects must go back to the root cause in order to determine the most appropriate action necessary to avoid repetition of the same problem. The quality data reporting system should also remain active during the operating phase. This appendix summarizes the requirements for a computer aided quality data reporting system for complex equipment and systems.
Reliability Engineering, 1999
Besides quantitative reliability requirements (figures), such as MTBF, MTTR, or availability, as ... more Besides quantitative reliability requirements (figures), such as MTBF, MTTR, or availability, as given in system specifications, customers often require a quality assurance/management system, and for complex items also the realization of a quality and reliability assurance program. Such general requirements are covered by standards, the most important of which are discussed in this appendix. A basic procedure for setting up and realizing quality and reliability requirements as well as the structure and content of a quality and reliability assurance program for complex equipment and systems are considered in Appendix A3.
Reliability Engineering, 1999
The following catalog of questions can be used to generate project-specific checklists for design... more The following catalog of questions can be used to generate project-specific checklists for design reviews (Tables A3.2 (Point 10), A3.3, and 5.5) during the design and development of complex equipment and systems.
Uploads
Papers by Sandro Birolini