Papers by Roger Bostelman
Sensors, Jun 15, 2023
This article is an open access article distributed under the terms and conditions of the Creative... more This article is an open access article distributed under the terms and conditions of the Creative Commons Attribution (CC BY

Advanced mobile manipulators offer the manufacturing industry the potential of a highly adaptive ... more Advanced mobile manipulators offer the manufacturing industry the potential of a highly adaptive system to perform precision assembly tasks in agile environments. Developing performance measurement capabilities for mobile manipulator systems will support the advancement of manipulator-vehicle coordination, precision, accuracy, and robustness. The National Institute of Standards and Technology (NIST) developed a measurement methodology for advanced mobile manipulators, which are mobile robots with an onboard robot arm, each from a different manufacturer and with a different controller. The measurement methodology is designed to assess the performance of mobile manipulators for manufacturing applications such as assembly, where position and orientation accuracy are critically important. The proposed methodology used an artifact designed at NIST to simulate an assembly task station. An optical tracking system measured the location of the targets, the mobile base position and orientation, and the position of a manipulator end-of-arm tool. The experimental data collected, using three different system computers, were timestamped using local clocks synchronized via the NIST internal and local area networks to align the data streams. The mobile manipulator system, the experimental methodology, the data analysis, and the results of the measurement methodology uncertainty and mobile manipulator positioning uncertainty using the novel artifacts are described in this paper. For the system tested, the mobile manipulator detection of 2 mm diameter fiducials can be achieved after registration. With validation from the optical tracking system, the study demonstrated that the Reconfigurable Mobile Manipulator Artifact (RMMA) has potential for serving as a novel standalone, low-cost test method for measuring the positioning uncertainty of mobile manipulators within a measurement uncertainty of 2 mm.
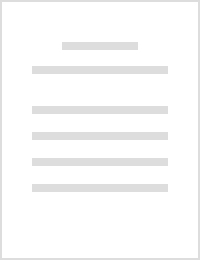
Automatic through autonomous - Unmanned Ground Vehicles (A-UGVs) have the potential to be applied... more Automatic through autonomous - Unmanned Ground Vehicles (A-UGVs) have the potential to be applied over a wide range of manufacturing systems under industry 4.0 paradigm. In order to use A-UGVs efficiently in a manufacturing system, it is necessary to select the A-UGV suitable for each factory or workplace. A framework for evaluating the A-UGV performance under a specific manufacturing environment is needed. ASTM International Committee F45 has been developing standards2 providing a basis for A-UGV manufacturers and users to compare tasks to the A-UGV capabilities. This paper proposes information models for A-UGV performance measurement along the standards development. The standard needs are analyzed to show how the standard and information model can be used for the introduction of A-UGVs into factories. The information model in this paper provides a structured way to describe the factory elements affecting the A-UGV performance, and the measured A-UGV performances against the factory elements. To validate the proposed information model, an A-UGV performance testbed was built and the information model instance is developed to describe the testbed elements. An A-UGV is tested against the testbed elements and the measured performance is described by the other instance. This paper contributes to mutual understanding, between A-UGV makers and users, to deliver A-UGV performance information efficiently and to provide basis for A-UGVs to be tested under the same conditions.
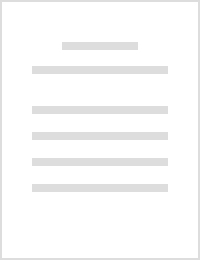
Volume 2A: Advanced Manufacturing, Oct 30, 2022
With the advancement of factory logistics into the autonomous era comes the need to validate the ... more With the advancement of factory logistics into the autonomous era comes the need to validate the safety and performance characteristics of Autonomous-Unmanned Ground Vehicles (A-UGVs) working in these application spaces ASTM Committee F45 has been developing standards for A-UGV performance measurement in various domains. The object detection and obstacle avoidance performance of A-UGVs in factories needs to be managed carefully as the action may cause severe damages, particularly when obstacles are either not detected or erroneously detected. In this paper, the grid-video measurement method is proposed to measure the small (e.g., short and/or thin) obstacle avoidance performance of A-UGVs. First, this paper describes the need for measuring the A-UGV performance through examples of small obstacles and the required A-UGV capability to avoid them. Next, the grid-video measurement method is introduced as a low cost, standard method to measure the small obstacle avoidance performance of A-UGVs. An experiment using blocks demonstrates how the grid-video measurement method can be used effectively to measure the A-UGV obstacle avoidance performance, and it shows that the performance changes upon A-UGV specification, obstacle sizing, and environmental conditions quantitively. The method and experimental results proposed in this paper will be used to support ASTM F45 standard development.
2019 Third IEEE International Conference on Robotic Computing (IRC)
A-UGV has been defined by ASTM Committee F45 as an “Automatic, Automated, or Autonomous vehicle t... more A-UGV has been defined by ASTM Committee F45 as an “Automatic, Automated, or Autonomous vehicle that operates while in contact with the ground without a human operator”. However, what do the levels actually mean to manufacturers, users, or especially potential users? This paper defines, and in many cases provides examples of, recommended autonomy levels for all three automatic, automated, and autonomous unmanned ground vehicles.

Workplace MusculoSkeletal Disorders (WMSD) continue to be the most significant source of industri... more Workplace MusculoSkeletal Disorders (WMSD) continue to be the most significant source of industrial workforce injuries. Exoskeletons are emerging as personal protective equipment (PPE) for sustained, repetitive, or intensive industrial tasks. This technical note describes and evaluates a proposed test method comprised of a novel testing apparatus, the Position and Load Test Apparatus for Exoskeletons (PoLoTAE), which was designed and developed at the National Institute of Standards and Technology (NIST), to simulate a wide variety of industrial tasks. The test method used commercially-available, low-cost and readilyadaptable sensors, building materials, and an initial set of qualitative and analytical methods to evaluate perceived user comfort, exoskeleton fit-for-task, and impact of exoskeleton on task productivity. The study includes analysis of simple subjective and quantitative measurement methods to obtain perceived comfort, effort, exoskeleton support, fit, task rate, and task completion times. Lastly, we include the limitations of this study and suggested improvements towards the development of test methods for the use of exoskeletons for industrial tasks, and towards providing more information for validation of models to understand the human-exoskeleton kinetic and kinematic interactions.
PubMed, 2017
Optical tracking systems are used in a wide range of fields, and their market has dramatically in... more Optical tracking systems are used in a wide range of fields, and their market has dramatically increased over the past several years, reaching $1.2 billion in sales revenue in 2014. This article describes the new ASTM E3064 standard test method procedures for optical tracking systems and will outline the theoretical basis for the analysis of the data from these systems. By way of an example, we will also verify the performance of a 12-camera optical tracking system using these standard procedures and related analysis. An artifact, developed at the National Institute of Standards and Technology (NIST), was verified by a coordinate measuring machine (CMM) and then used in two experiments to verify the test method. This and other in-depth articles are intended to be base references for ASTM E3064.
The National Institute of Standards and Technology's (NIST) Intelligent Systems Division (ISD) is... more The National Institute of Standards and Technology's (NIST) Intelligent Systems Division (ISD) is working with the material handling industry, specifically on automated guided vehicles, to develop next generation vehicles. ISD is also a participant in the Defense Advanced Research Project Agency (DARPA) Learning Applied to Ground Robots (LAGR) Project embedding learning algorithms into the modules that make up the Four Dimensional/Real-Time Control System (4D/RCS). 4D/RCS is the standard reference model architecture which ISD has applied to control many intelligent systems. Technology from LAGR is being transferred to the material handling industry through the NIST Industrial Autonomous Vehicles Project. This paper describes the 4D/RCS structure and control applied to LAGR and the transfer of this technology through a demonstration to the automated guided vehicles industry.

Proceedings of SPIE, May 27, 2005
The performance evaluation of an obstacle detection and segmentation algorithm is explained upon ... more The performance evaluation of an obstacle detection and segmentation algorithm is explained upon comparing a new range camera to ground truth. Automated Guided Vehicles (AGVs) in factory-like environments may one day utilize this algorithm for advanced vehicle navigation along with using a new 3D real-time range camera. Our approach expands on the US and British Safety Standards, which allow for non-contact safety sensors on vehicles, by performing tests on objects specifically sized in both standards. These successful tests placed the recommended, as well as smaller, material-covered and sized objects on the vehicle path for static measurement. The segmented (mapped) obstacles were then verified in range to the objects and object size using simultaneous, absolute, ground truth measurements obtained from a relatively accurate 2D scanning laser rangefinder. The 3D range cameras are expected to be relatively inexpensive, used indoors and possibly one day used outdoors for several potential mobile robot applications that build upon experimental results explained in this paper.

Proceedings of SPIE, Oct 1, 2006
The National Institute of Standards and Technology (NIST) has been studying pallet visualization ... more The National Institute of Standards and Technology (NIST) has been studying pallet visualization for the automated guided vehicle (AGV) industry. Through a cooperative research and development agreement with Transbotics, an AGV manufacturer, NIST has developed advanced sensor processing and world modeling algorithms to verify pallet location and orientation with respect to the AGV. Sensor processing utilizes two onboard AGV, single scan-line, laser-range units. The "Safety" sensor is a safety unit located at the base of a forktruck AGV and the "Panner" sensor is a panning laser-ranger rotated 90 degrees, mounted on a rotating motor, and mounted at the top, front of the AGV. The Safety sensor, typically used to detect obstacles such as humans, was also used to detect pallets and their surrounding area such as the walls of a truck to be loaded with pallets. The Panner, was used to acquire many scan-lines of range data which was processed into a 3D point cloud and segment out the pallet by a priori, approximate pallet load or remaining truck volumes. A world model was then constructed and output to the vehicle for pallet/truck volume verification. This paper will explain this joint government/industry project and results of using LADAR imaging methods.

The National Institute of Standards and Technology, Intelligent Systems Division has collected da... more The National Institute of Standards and Technology, Intelligent Systems Division has collected data measuring the performance of a mobile manipulator; i.e., an automatic guided vehicle (AGV) 1 with onboard robot arm, from two different manufacturers. The performance measurement concept uses a novel artifact and method that have been verified using an optical tracking system (OTS), which can measure AGV position, manipulator motion, and position uncertainty. The data needed to make these three measurements was collected during two tests; both tests have corresponding timestamps relative to global positioning system (GPS) time, where the computer clocks are synchronized using the Network Time Protocol. This paper provides detailed explanation of the data from mobile-manipulator, performance-measurement tests. It is expected that the user of the information within this document and the data files that accompany this document will have sufficient knowledge to implement mobile manipulation testing and evaluation.
The National Institute of Standards and Technology (NIST) is developing test methods for contact ... more The National Institute of Standards and Technology (NIST) is developing test methods for contact bumpers used on Automated Guided Vehicles (AGVs) as a basis for safety standards. This paper describes proposed test methods, force measurements for contact bumpers, and the associated impact force theory. The results of this study are provided as reference to the AGV industry as a possible resolution for currently non-existent AGV contact bumper test methods safety standards.

ASTM International eBooks, Apr 1, 2016
Multi-camera motion capture systems are commercially available and typically are used in the ente... more Multi-camera motion capture systems are commercially available and typically are used in the entertainment industry to track human motions for video gaming and movies. These systems are proving useful as ground truth measurement systems to assess the performance of robots, autonomous ground vehicles, and assembly tasks in smart manufacturing. In order to be used as ground truth, the accuracy of the motion capture system must be at least ten times better than a given system under test. This chapter creates an innovate artifact and test method to measure the accuracy of a given motion capture system. These measurements will then be used to assess the performance of the motion capture system and validate that it can be used as ground truth. The motion capture system will then serve as ground truth for evaluating the performance of an automatic guided vehicle (AGV) with an onboard robot arm (mobile manipulator) and for evaluating the performance of robotic workstation assembly tasks that utilize robot arms and hands.
Uploads
Papers by Roger Bostelman