Papers by Prabhakar Pagilla
On Feedback Control Of Nonlinear Mechanical Systems Subject To Holonomic/nonholonomic Constraints
ABSTRACT
Control Engineering Practice, Aug 1, 2015
Proportions of reversible and irreversible magnetization processes in the overall magnetization p... more Proportions of reversible and irreversible magnetization processes in the overall magnetization process were studied in a complex view of magnetic, thermal and electrical properties of iron-phenolphormaldehyde resin composites. They were determined experimentally at different values of magnetic induction along the initial curve. The results of total, differential, reversible and irreversible permeability measurement as well as the analysis of DC energy losses revealed the same tendencies: The numbers of movable domain walls (determining the extent of reversible processes) depend on the magnetic particle size and the resin content through the demagnetizing fields produced by the particle surfaces, lowering the interaction between particles. Thermal diffusivity was compared with Hashin-Shtrikman model indicating good insulation of particles.

IFAC Proceedings Volumes, 2014
Motion coordination of differential drive robots with wheel slip is considered in this work. In a... more Motion coordination of differential drive robots with wheel slip is considered in this work. In applications involving motion coordination of multiple wheeled vehicles, much of the existing work has assumed a pure rolling condition between the wheel and ground while deriving the vehicle dynamics and subsequently in the development of model-based controllers that can achieve and maintain the desired formation of vehicles. Wheel slip is common when using differential drive mobile robots as the orientation of the robot is achieved by commanding a velocity differential between the two driven wheels of the mobile robot. In formations of wheeled mobile robots, to maintain the desired spacing between vehicles, rapid accelerations and decelerations may be needed to maintain the desired spacing between vehicles. In this paper, we assume wheel slip and model the dynamics of each mobile robot with a simple Coulomb friction-based traction force model to distinguish between slip and no-slip conditions. Based on this dynamic model of the mobile robot with wheel slip, a formation controller is developed by limiting the torque to the wheel motors of each robot to avoid slip and achieve and maintain the desired formation. Experiments are conducted with a formation that is a platoon of three wheeled mobile robots. Experimental results are shown and discussed to investigate occurrence of wheel slip and its effect on coordination.

A computer program for conducting model simulations for zero speed splice unwinds is described in... more A computer program for conducting model simulations for zero speed splice unwinds is described in this paper. A typical unwind system consisting of the unwinding material roll, festoon, dancer, and pull rolls is considered. The developed computer model is general enough to be applicable to a variety of unwinds containing these components. The paper also provides a procedure for determining zero speed splicing parameters when the characteristics of the festoon and the splicer, such as number of carriage rollers, festoon capacity, clamp and dwell time, etc., are given; this method can be employed for the selection of splicing parameters, such as acceleration and deceleration profiles, splice diameter, spindle speed profiles, etc. The computer model can predict the transport behavior of webs through the unwinds; this was verified by comparing data from model simulations and experiments on a production unwind. The computer program can be used to evaluate different scenarios of unwind op...

2021 IEEE/ASME International Conference on Advanced Intelligent Mechatronics (AIM), 2021
Workpiece localization is the process of obtaining the location of a workpiece in a reference fra... more Workpiece localization is the process of obtaining the location of a workpiece in a reference frame of a robotic workspace. The location (position and orientation) is represented by the transformation between a local frame associated with the workpiece and the specified reference frame in the workspace. In this work, we study the workpiece localization problem without the two commonly adopted restrictive assumptions: the data used to calculate the transformation is readily available and the correspondence between the data sets used for calculation is known. The goal is to automate the localization process starting from efficient data collection to determining the workpiece location in the workspace. We describe a strategy that includes the following aspects: predicting the correspondence between the measured data and the workpiece CAD model data; generating representative vectors that would aid in determining the next-best-view for collecting new information of the workpiece location; evaluating a search region to find the next sensor location that satisfies both the robot kinematics as well as sensor field-of-view constraints while giving the maximum view gain; and calculating the rigid body transformation from the local frame to the world frame to localize the workpiece. Numerical simulation and experimental results are presented and discussed for the proposed strategy.
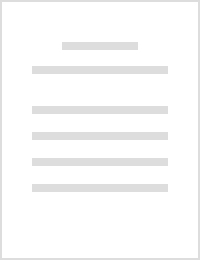
A novel path following control framework for robot manipulators using a rotation minimizing frame
2021 60th IEEE Conference on Decision and Control (CDC), 2021
We describe a novel path following pose control framework for articulated robots which is needed ... more We describe a novel path following pose control framework for articulated robots which is needed for many material handling and surface finishing where constant speed travel is desirable. Using a rotation minimizing frame (RMF) associated with the geometric path, we develop a path following position control law by projecting the robot translation states onto the RMF and based on an analytical description of the reference orientation dynamics of the RMF, we derive a stabilizing controller for orientation control along the path with the Modified Rodrigues parameters to avoid the unwinding problem encountered when rotations of more than 180 degrees are encountered. The effectiveness of the proposed path following framework is verified via simulations on a torque actuated KUKA iiwa robot using a physics-based simulation engine called Bullet.
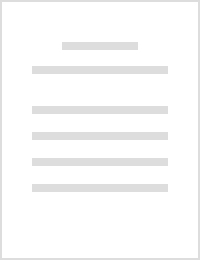
Blended Shared Control with Subgoal Adjustment
2018 IEEE International Conference on Systems, Man, and Cybernetics (SMC), 2018
Combining the benefits of robust situational awareness of human operators with the efficiency and... more Combining the benefits of robust situational awareness of human operators with the efficiency and precision of automatic control has been an important topic of human-machine shared control. The emphasis is on keeping human operators in the loop while automatic control providing assistance to improve task performance. Given a task with specific subgoals, execution of a task using blended shared control involves predicting the operator’s intent of subgoal transitions and deciding the blending weights for inputs from the human operator and automatic control. In this paper we address the problem of subgoal adjustment in blended shared control which is typically initiated by the operator’s intent and necessary to sustain the shared control performance for changing subgoal conditions. First, we provide a method to predict operator’s intent of visiting a subgoal. Based on intent prediction, we propose a method for subgoal adjustment where the adjustment is encoded by a hyperrectangle. The volume of the hyper-rectangle is obtained by using a hyperbolic slope transition function which is based on the distance between subgoals. The adjustment actions within the hyper-rectangle are facilitated by a skill-weighted action integral that takes into consideration the skill level of the operator. The approach is tested on a scaled hydraulic excavator platform with multiple novice operators and a skilled operator. Experimental results are presented and discussed.
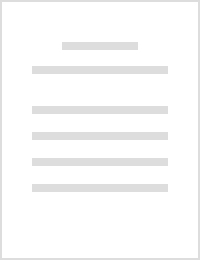
Optimal configurations to minimize disturbance propagation in manufacturing networks
2017 American Control Conference (ACC), 2017
In this paper, we consider the problem of determining optimal configurations of Roll-to-Roll (R2R... more In this paper, we consider the problem of determining optimal configurations of Roll-to-Roll (R2R) process machines which consist of many interconnected dynamic elements to transport flexible materials (webs) on rollers. The problem is to optimally locate the controlled dynamic elements within the R2R machine so as to minimize the effect of disturbances propagated by the transported web. Typical disturbances on R2R machines include misalignment and out-of-roundness of rollers which cause web wrinkles and registration errors if unattenuated. The central contribution of this paper is to pose the combinatorial problem of determining the optimal configuration for a R2R machine as a Mixed-Integer Semi-Definite Program (MISDP) and provide an algorithm to efficiently compute feasible configurations and bounds on their sub-optimality. The proposed algorithm is based on tools such as McCormick relaxations, outer-approximation via eigenvalue cuts, and bound tightening procedures. We provide numerical results for representative R2R systems to show the efficiency of the proposed algorithm.

IFAC-PapersOnLine, 2020
We describe a novel path following control scheme for robot manipulators where constant tool velo... more We describe a novel path following control scheme for robot manipulators where constant tool velocity of travel on a surface is desirable. The path following scheme is applicable to general situations where the surface geometry is typically given in terms of measured data from a sensor. Considering the measured data points as control points, we utilize a cubic spline interpolation to generate a closed-form geometric description for the 3D path. Since joint velocity control is quite common in many industrial robots and most surface finishing tasks require travel with constant velocity along the path, we consider a 3D kinematic model for the end-effector with control inputs as rate of change of orientation and translational velocity that is locally tangent to the surface along the path. By utilizing a path variable and the tangent vector along the path, we formulate a converging path as the path that is traversed from a given robot endeffector position to the desired path and subsequent travel on the desired path on the surface. To evaluate the performance of the scheme, we have conducted a number of real-time experiments on a six degree-of-freedom industrial robot for several paths which can be employed for sanding of structures or deburring of large industrial cast parts and gears.
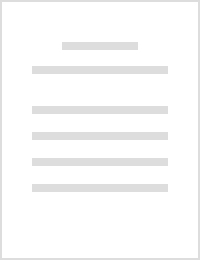
A Novel Path Following Scheme for Robot End-Effectors
2020 American Control Conference (ACC), 2020
In this paper we describe a novel path following scheme for robot end-effectors that is particula... more In this paper we describe a novel path following scheme for robot end-effectors that is particularly suitable for robotic surface finishing operations where constant velocity of travel on the surface is desirable. The scheme is applicable to general situations where the path is typically given in terms of measured data from a sensor, and also to paths that are specified in terms of analytical curves (circular or ellipsoidal). Considering the given data points as control points, we utilize cubic spline interpolation to generate a closed-form geometric description for the path. Since velocity control is quite common in many industrial robots and most surface finishing tasks require travel with constant velocity along the path, we consider a kinematic model for the end-effector with control inputs as rate of change of orientation and translational velocity. By utilizing a path variable and the tangent vector along the path, we describe the complete path as the path that is taken from the initial robot end-effector point to the desired path and subsequent travel on the desired path. To evaluate the performance of the scheme, we have conducted a number of real-time experiments on an industrial robot for circular paths and for paths generated for gear deburring and chamfering, and results from those experiments will be discussed.

IFAC-PapersOnLine, 2020
Accurate positioning of the workpiece in the robotic work cell is currently required to perform m... more Accurate positioning of the workpiece in the robotic work cell is currently required to perform machining operations such as chamfering in order to obtain high quality products. However, registration and workpiece fixturing errors are inevitable and lead to uncertainty in the desired robot end-effector trajectory which will lead to poor quality of the finished product. This paper proposes a method for robotic gear chamfering that can compensate for the registration error of the workpiece while avoiding use of expensive and time-consuming metrology devices for accurately registering the gear in the robot workspace. We highlight the problems in chamfering with workpiece uncertainty when traditional contour following methods are employed. A novel chamfering trajectory based on a part identification procedure is proposed that can account for the gear registration uncertainty. A force control strategy is employed in identifying the gear center and gear root positions. Based on this identification, we employ a novel force/motion strategy that can simultaneously chamfer two edges of the adjacent gear teeth. We have conducted a number of real-time experiments with a six degree-of-freedom robot to evaluate the proposed strategy, and representative chamfering experimental results are presented and discussed.
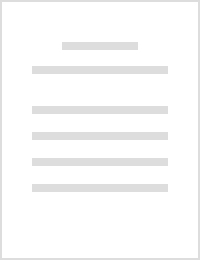
A Review of Manufacturing Process Control
Journal of Manufacturing Science and Engineering, 2020
Smart manufacturing concepts are being integrated into all areas of manufacturing industries, fro... more Smart manufacturing concepts are being integrated into all areas of manufacturing industries, from the device level (e.g., intelligent sensors) to the efficient coordination of business units. Vital components of any manufacturing enterprise are the processes that transform raw materials into components, assemblies, and finally products. It is the manufacturing process where smart manufacturing is poised to make substantial impact through process control, i.e., the intelligent manipulation of process variables to increase operation productivity and part quality. This article discusses three areas of manufacturing process control: control-oriented modeling, sensing and monitoring, and the design and construction of controllers. The discussion will center around the following manufacturing processes: machining, grinding, forming, joining, and additive. While many other important processes exist, the discussions of control of these mechanical manufacturing processes will form a framewo...
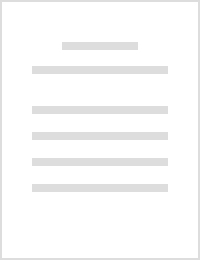
Dual-edge robotic gear chamfering with registration error compensation
Robotics and Computer-Integrated Manufacturing, 2021
Abstract This paper describes a novel method for robotic gear chamfering called dual-edge chamfer... more Abstract This paper describes a novel method for robotic gear chamfering called dual-edge chamfering which can facilitate simultaneous chamfering of the two edges of adjacent gear teeth and overcome typical registration errors arising due to the placement of the workpiece in the robot workspace. Deviations of the robot end-effector trajectory when compared to the nominal trajectory due to registration errors are discussed first; such trajectory deviations caused by typical registration errors due to gear center translation and rotation are quantified. Dual-edge chamfering process is described and an efficient trajectory design strategy is developed by considering the kinematic constraints imposed by the profiles of the gear edge and the abrasive tool. The dual-edge chamfering robot trajectory is facilitated by a simple procedure for identifying the gear and gear root centers by employing the robot. To execute the dual-edge chamfering trajectory, an efficient motion/force control strategy that includes active compliance from the tool mounted on the robot is proposed. A number of real-time experiments are conducted to evaluate the proposed method by employing a commercial six degree-of-freedom robot. Two types of large cylindrical metal gears are utilized for testing, an external gear with teeth on the outside and an internal gear with teeth on the inside. In addition to these, two different robotic compliant tools with axial and radial compliance are tested. A representative sample of the experimental results are presented and discussed.

IEEE Transactions on Intelligent Transportation Systems, 2018
In this paper, we investigate the benefits of Vehicleto-Vehicle (V2V) communication for autonomou... more In this paper, we investigate the benefits of Vehicleto-Vehicle (V2V) communication for autonomous vehicles and provide results on how V2V information helps reduce employable time headway in the presence of parasitic lags. For a string of vehicles adopting a Constant Time Headway Policy (CTHP) and availing the on-board information of predecessor's vehicle position and velocity, the minimum employable time headway (hmin) must be lower bounded by 2τ0 for string stability, where τ0 is the maximum parasitic actuation lag. In this paper, we quantify the benefits of using V2V communication in terms of a reduction in the employable time headway: (1) If the position and velocity information of r immediately preceding vehicles is used, then hmin can be reduced to 4τ0/(1 + r); (2) furthermore, if the acceleration of 'r' immediately preceding vehicles is used, then hmin can be reduced to 2τ0/(1 + r); and (3) if the position, velocity and acceleration of the immediate and the r-th predecessors are used, then hmin ≥ 2τ0/(1 + r). Note that cases (2) and (3) provide the same lower bound on the minimum employable time headway; however, case (3) requires much less communicated information.
IFAC Proceedings Volumes, 2004
In many web process lines, a belt-pulley transmission system is used to drive the driven rollers,... more In many web process lines, a belt-pulley transmission system is used to drive the driven rollers, unwind, and/or winder rolls. Though the belt pulley transmission system offers certain advantages over direct-driven system and gear driven systems, the compliance of belt adds additional dynamics which need to be studied. This paper addresses the issue of compliance of belt on the speed control system. A model which includes the compliance of the belt is proposed. Analysis of the dynamic model to address issues such as the feedback scheme to be used and the choice of the feedback gains is performed. Simulation results for a prototype web unwind station with a belt-pulley transmission system are presented and discussed.
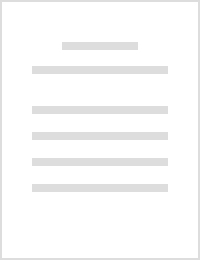
A Combinatorial Approach for Developing Ring Communication Graphs for Vehicle Formations
Journal of Dynamic Systems, Measurement, and Control, 2017
In this paper, we study vehicle formations employing ring-structured communication strategies and... more In this paper, we study vehicle formations employing ring-structured communication strategies and propose a combinatorial approach for developing ring graphs for vehicle formations. In vehicle platoons, a ring graph is formed when each vehicle receives information from its predecessor, and the lead vehicle receives information from the last vehicle, thus forming a ring in its basic form. In such basic form, the communication distance between the first and the last vehicle increases with the platoon size, which creates implementation issues due to sensing range limitations. If one were to employ a communication protocol such as the token ring protocol, the delay in updating information and communication arises from the need for the token to travel across the entire graph. To overcome this limitation, alternative ring graphs which are formed by smaller communication distances between vehicles are proposed in this paper. For a given formation and a constraint on the maximum communicati...
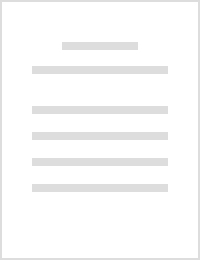
Intent aware shared control in off-nominal situations
2016 IEEE 55th Conference on Decision and Control (CDC), 2016
We propose a new shared control technique that takes into account the operator's intent to qu... more We propose a new shared control technique that takes into account the operator's intent to quickly relinquish control to the operator in off-nominal conditions. Human-machine shared control is an emerging area of research in which the autonomous control is utilized to augment the operator's performance. Existing work has established that shared control can improve cycle times in nominal conditions, that is, when the operating environment satisfies the assumptions made in the design of the optimal augmenting controller. However, these methods can be too slow to relinquish control in off-nominal cases, when the operator needs to deviate from the nominally optimal trajectory due to unforeseen obstacles or other uncertainties. In this paper, we attempt to address this gap by mathematically quantifying operator intent. The resulting technique provides autonomous control augmentation to the operator when they are attempting to drive the system along the suggested optimal trajectory, but offers little hindrance to the operator when they are attempting to deal with off-nominal conditions. Theoretical results show that the performance of the presented intent aware shared control technique is at least as good as existing techniques, and that it results in improved obstacle reaction time. Human interaction experiments on the Zermelo's navigation problem in the presence of a random pop-up obstacle show a significant reduction in obstacle collision with our method when compared to existing work.

ISA Transactions, 2016
In this work we consider the problem of controlling the load speed of a mechanical transmission s... more In this work we consider the problem of controlling the load speed of a mechanical transmission system consisting of a belt-pulley and a gear-pair to transmit mechanical power from the motor shaft to the load shaft. The system is modeled as two inertias (motor and load) connected by a compliant transmission system. In practice, control systems using either motor speed feedback or load speed feedback have been employed. If the transmission is assumed to be rigid, then using either the motor or load speed feedback provides the same result. In the presence of transmission compliance, which may be due to belt compliance or torsional compliance of long shafts, the stability and performance characteristics of the closed-loop system are quite different based on whether motor speed or load speed feedback are employed. In this paper we investigate both the motor and load speed feedback options by considering transmission compliance and utilizing the singular perturbation method. We also propose and discuss a control scheme that utilizes both motor and load speed feedback. An adaptive feedforward action is employed for this control scheme to reject torque disturbances on the load. We consider an experimental platform of such a system for conducting experiments that is typically utilized in roll-to-roll manufacturing. Representative experimental results are shown and discussed.
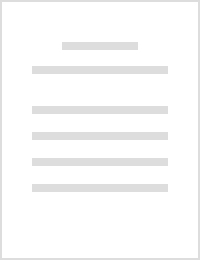
Speed Control of an Inertia Load Connected to a Motor Through a Compliant Mechanical Transmission System
Volume 3: Multiagent Network Systems; Natural Gas and Heat Exchangers; Path Planning and Motion Control; Powertrain Systems; Rehab Robotics; Robot Manipulators; Rollover Prevention (AVS); Sensors and Actuators; Time Delay Systems; Tracking Control Systems; Uncertain Systems and Robustness; Unmann..., 2015
In this paper, we focus on the problem of controlling the load speed of a mechanical transmission... more In this paper, we focus on the problem of controlling the load speed of a mechanical transmission system consisting of a belt-pulley and a gear-pair. We consider two inertias (motor and load) system connected by a compliant transmission. Because of the transmission dynamics, regulation of motor shaft speed may not translate to regulation of load speed. Further, determination of whether to use of motor speed or load speed feedback or a combination of both that would facilitate control of load speed is of importance. In this paper we investigate both the motor and load speed feedback options by considering transmission compliance and utilizing the singular perturbation method. We propose a two degree of freedom control system that utilizes both motor and load speed feedback and an adaptive feedforward scheme to reject torque disturbances on the load. Experiments conducted on a typical industrial transmission system that is commonly employed in roll-to-roll manufacturing are discussed,. A representation sample of the experimental results are presented and discussed.Copyright © 2015 by ASME
Uploads
Papers by Prabhakar Pagilla