Papers by Philippe Thibaux
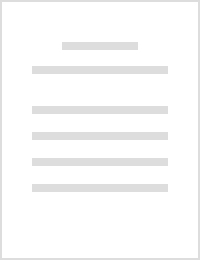
Ductile Fracture Characterization of an X70 Steel: Re-Interpretation of Classical Tests Using the Finite Element Technique
The crack arrest capacity of a linepipe is one of the most important material parameter for such ... more The crack arrest capacity of a linepipe is one of the most important material parameter for such components. In current design codes, it is expressed as the energy absorbed by a CVN impact test. This prescribed impact energy for a given pipeline is typically between 50 and 120J, depending on the grade of the material, the pressure and the dimensions of the pipe. The continuous improvement of steel production has lead to the situation that the impact values achieved in standard pipeline steel production are much larger than 200J for the base material. The question of the significance of these high impact energies can be raised, particularly considering that no correlation has been found between CVN values and crack arrest properties of very high strength materials (X100–X120). In this investigation, instrumented Charpy tests and notched tensile tests were performed on an X70 material. The same tests were also simulated using the finite element method and the Gurson-Tvergaard-Needleman damage model. The combination of supplementary experimental information coming from the instrumentation of the Charpy test and finite element simulations delivers a different insight about the test. It is observed that the crack does not break the sample in 2 parts in ductile mode. After 6–7mm of propagation, the crack deviates and stops. The propagation stops when the crack meets the part of the sample becoming wider due to bending. Finite element simulations proved that it results in a quasi constant force during a displacement of the hammer of almost 10mm. The consequence is that more than 25% of the energy is dissipated in a different fracture mode at the end of the test. Finite element simulations proved also that damage is already occurring at the maximum of the load, but that damage has almost no influence on the load for two-thirds of the displacement at the maximum. In the case of the investigated steel, it means that more than 27J, as often mentioned in standards for avoidance of brittle failure, are dissipated by plastic bending before the initiation of the crack. From the findings of this study, one can conclude that the results of the Charpy test are very sensitive to crack initiation and that only a limited part of the test is meaningful to describe crack propagation. Therefore, it is questionable if the Charpy test is adapted to predict the crack arrest capacity of steels with high crack initiation energy.

Materials Science Forum, Oct 1, 2007
A good combination of strength and toughness in HSLA steels can be achieved by the addition of mi... more A good combination of strength and toughness in HSLA steels can be achieved by the addition of microalloying elements such as Nb. Nb can retard the static recrystallization of austenite at low temperatures by either a solute drag or by a precipitation pinning (when bonded to C or N) effect. Both mechanisms result in improved mechanical properties due to grain size refinement of the transformed ferrite. In this study, 3 Nb-microalloyed model alloys were designed to investigate the solute drag and the precipitation effect separately. The first alloy, containing a stoechiometric ratio of Nb and C, was designed to study the retarding effect of NbC on the recrystallization behavior. A second alloy, containing Nb and only few ppm C, was casted in order to study the effect of Nb in solid solution. The two alloys were compared with a C-Mn reference alloy. The recrystallization behavior of the three alloys were compared by multi-hit torsion tests and double hit compression tests. The Nb-C and the Nb-very low C showed small differences in recrystallization behavior. These results show that Nb delays the recrystallization by a solute drag effect or by the formation of a very small amount of precipitates.
Science and Technology of Welding and Joining, Feb 1, 2010
Steel welding using induction heating to produce pipelines is found to have lower toughness at th... more Steel welding using induction heating to produce pipelines is found to have lower toughness at the weld junction than the base material, even after a heat treatment which reaustenitises the weld zone. Detailed crystallographic characterisation indicates that the poor toughness is due to the crystallographically coarse grains present after welding; the coarse scale is not visible using just optical microscopy. The post-weld heat treatment does not improve the situation at the weld junction, because the detrimental crystallographic characteristics are reproduced on cooling.
Materials Science Forum, 2012

Metallurgical and Materials Transactions, Jun 1, 2007
This paper deals with the problem of measuring the VVER-1000 burnup fuel cladding temperature in ... more This paper deals with the problem of measuring the VVER-1000 burnup fuel cladding temperature in a 500-900°C range in the process of experiments in a channel of the MIR research reactor to obtain data on the fuel element behavior under the influence of the parameters typical of the maximum design-basis loss-of-coolant accident (LOCA). Studying the burnup fuel cladding deformation pattern requires measurements of the cladding temperature with no (thermal, mechanical and other) impacts on the cladding in the maximum deformation region. For dynamic experiments in the MIR reactor channel with fuel testing in a vapor-gas environment, a cladding temperature measuring unit has been developed, in which the cladding is not subjected to external impacts in the maximum deformation region. In the process of being installed into the spacer grid, the thermoelectric transducer (TET) has its hot junction forced against the cladding making it possible to prevent the external impact on the cladding. The thermometric characteristic of the TET attachment, which is associated with the impact of the grid as such on its thermal condition, was studied using a laboratory facility. This technique was used in an in-pile experiment to study the fuel cladding deformation pattern. Laboratory facility (LF), experimental fuel element (EFE), electroheated fuel element simulator (EHFES), cladding, spacer grid (SG), thermoelectric transducer (TET), hot junction, temperature, heat-up rate, MIR reactor, loss-of-coolant accident (LOCA).

Materials Science and Engineering A-structural Materials Properties Microstructure and Processing, Jun 1, 2011
Recrystallization-precipitation-time-temperature (RPTT) diagrams for strains of 0.20 and O.35 hav... more Recrystallization-precipitation-time-temperature (RPTT) diagrams for strains of 0.20 and O.35 have been determined for two microalloyed steels with niobium percentages of 0.024 and 0,058, respectively, and equal percentages of carbon and nitrogen. The method knownas "back extrapolation" has been used for the determination of static recrystallization kinetics and also for the plotting of the diagrams, While a single plateau was observed on the recrystallized fraction against time curves for the first steel, as a consequence of sttain induced precipitation, these curves for the second steel showed the formation of a double plateau. whose interpretation, confirmed by calorimetric analysis, supposes the formation of two types of preci pitates, The work uses transmission microscopy to show the precipitates which are formed in both steels, as well as the size most probably capable of inhibiting recrystallization. Final]y, an analysis is made of the RPTT diagrams and of the large amount of information which they offer for designing a more appropriate rolling schedule in order to obtain finer precipitates and a better austenitic microstructure before the austenite+ferrite transformation.
STUDY OF THE RECRYSTALLIZATION BEHAVIOR IN Nb-BEARING STEELS BY MULTI-PASS, DOUBLE HIT AND STRESS RELAXATION TESTS

La pensée ne doit jamais se soumettre, ni à un dogme, ni à un parti, ni à une passion, ni à un in... more La pensée ne doit jamais se soumettre, ni à un dogme, ni à un parti, ni à une passion, ni à un intérêt, ni à une idée préconçue, ni à quoi que ce soit, si ce n'est aux faits eux-mêmes, parce que, pour elle, se soumettre ce serait cesser d'être » Henri Poincaré e tiens à remercier Monsieur Lévy, directeur de l'Ecole des Mines de Paris, pour m'avoir permis de faire une thèse dans un de ses laboratoires. Ma gratitude va également à la direction du CEMEF, ainsi qu'à celle de l'IRSID, groupe USINOR, pour m'avoir fait confiance pour mener cette étude. es membres du jury m'ont accordé un peu (ou beaucoup) de leur précieux temps. Que soient ici remerciés John J. Jonas, Hervé Biausser, Thierry Iung et Pierre Gilormini. J'espère que l'intérêt qu'ils auront trouvé dans ce travail aura été à la hauteur de la précision de leurs questions. van Chastel et Anne-Marie Chaze ont encadré ma thèse au CEMEF. Leur enthousiasme, leur créativité, et leur écoute m'ont été particulièrement profitable, et agréable, tout au long de ces trois années et quelques mois. Je voudrais que ces qualités soient également présentes dans mon travail ultérieur. l m'a été possible de séjourner plus d'une année en Moselle, pour profiter du savoir de l'IRSID. Damien Feuillu a non seulement eu à suivre mon travail à peine arrivé à l'IRSID, mais en plus a dû partager son bureau avec moi pendant près d'un an. Je te remercie pour cette collaboration. Grâce à la géographie interne de l'IRSID, aux mouvements de l'organigramme et à l'ambiguïté des thématiques abordées (trop de mécanique pour être de la métallurgie, trop de métallurgie pour être de la mécanique), de nombreuses personnes ont suivi ce travail. J'espère que l'intérêt que Jacques-Yves Bourgon, Pascal Buesler, Pascal Gratacos, Thierry Iung, Matthieu Kandel, Jérôme Giusti… auront manifesté pour ce travail aura été récompensé par les réponses apportées. enis Jouaffre a réalisé un travail plus que profitable pour ma thèse dans le cadre de son CSN à l'IBF. Je tiens à le remercier pour nos nombreuses discussions et pour son travail. e travail a été lancé sur une initiative de l'usine de Dillingen Hütte. Ma gratitude va à Messieurs A. Streisselberger et G. Haralamb pour leur écoute et leur suggestion au cours de ce travail. Leur point de vue a, je l'espère, permis de rendre ce travail plus applicable dans une optique industrielle. e nombreuses personnes ont également contribué à ce travail. Que soient ici remerciés
Characterization of the precipitation state during austenite processing of a microalloyed steel
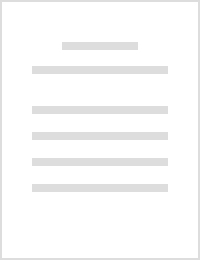
Influence of the Forming Operations on the Yield Stress Measured on Pipe
The yield stress of pipes is measured among purposes to assess the resistance of the pipe to the ... more The yield stress of pipes is measured among purposes to assess the resistance of the pipe to the internal pressure of the fluid. Unfortunately, it is not possible to sample a straight specimen in the hoop direction, and therefore the pipe has to be flattened prior to testing. In the present investigation, different materials were tested in tensile–compression mode in order to provide data for a kinematic hardening model. Based on this experimental data set, a model was built to take into account several features of the material behaviour (presence of yield point elongation, strain hardening, etc…) and the processing route (longitudinal or spiral seam weld, expander, hydrotest…). Pipe production was also sampled at different moments (base material, after leveling, after pipe forming, after hydrotest). The testing program included tensile testing and ring expansion tests. The results show that the model gives a prediction in good correspondence with the experimental results. The model also reproduces several experimental facts, like for example the presence of a yield point elongation on the base material and its absence on the flattened pipe sample. Finally, the model is compared with an industrial database containing different steel grades (from grade B to X80) and different ratios of wall thickness over diameter (t/OD) ratios. The difference of yield stress between coil and pipe is predicted on this database with an accuracy of 20MPa.
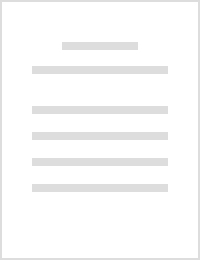
Influence of Forming and Flattening on the Measured Tensile Properties of Linepipe
Steelmakers are producing plates or coils, which are subsequently formed into pipes. The mechanic... more Steelmakers are producing plates or coils, which are subsequently formed into pipes. The mechanical properties are checked after steel and pipe production, and it is commonly observed that the tensile properties of pipes differ from the properties of plate or coil. The difference in tensile properties is attributed to the forming of the pipe and the subsequent flattening of a pipe section to make a flat tensile test sample. The reverse deformation during pipe forming and flattening is expected to cause a Bauschinger effect leading to a decrease of the yield stress of the pipe compared to the yield stress of the base material. First, a kinematics description of the pipe forming is presented. This kinematics description is important to know the deformation path followed by the material during pipe forming, flattening and tensile test. Once the deformation path is known, the stress state can be computed using constitutive laws. Three constitutive laws are presented here and their ability to describe the mechanical behaviour is further discussed. To determine the mechanical behaviour in reverse deformation paths, a specific experimental set-up has been developed to make reverse tests in tension and compression. Using this experimental facility, an X60 grade on coil has been characterized. Models parameters are fitted on the experimental data. Using these model parameters, a tensile test after forming and flattening is modelled. The simulation shows that a very accurate description of material behaviour is required to predict the final tensile properties.
The use of general descriptive names, registered names, trademarks, service marks, etc. in this p... more The use of general descriptive names, registered names, trademarks, service marks, etc. in this publication does not imply, even in the absence of a specific statement, that such names are exempt from the relevant protective laws and regulations and therefore free for general use. The publisher, the authors and the editors are safe to assume that the advice and information in this book are believed to be true and accurate at the date of publication. Neither the publisher nor the authors or the editors give a warranty, express or implied, with respect to the material contained herein or for any errors or omissions that may have been made. The publisher remains neutral with regard to jurisdictional claims in published maps and institutional affiliations.
Prediction of the micro-structure development in HHS-grades during continuous annealing and the resulting of mechanical properties
Europace, 2007
Microstructural control of ductile crack arrestability in HSLA pipeline steels

Journal of Physics: Conference Series, Jul 1, 2018
Large diameter welded pipes are amongst the most cost effective transportation means for oil and ... more Large diameter welded pipes are amongst the most cost effective transportation means for oil and gas. In general, one can differentiate between longitudinally (LSAW) and spirally welded (HSAW) pipes, whereby LSAW pipes are produced from plate and HSAW pipes from coil. Pipe forming involves several cold forming steps, such as (cyclic) bending and (mechanical) expansion. Obviously, the mechanical properties on pipe differ from those of the base material. Detailed understanding of how the mechanical properties evolve during pipe forming would help steel mills to target specific base material properties to ensure the final pipe strength. Therefore, an FE (Finite Element) model, capable of simulating different pipe forming processes, was developed using the commercial FE software Abaqus. Thereby, an advanced constitutive model, accounting for isotropic, kinematic and distortional hardening was implemented via a UMAT user subroutine. A reverse engineering strategy was applied to calibrate the constitutive model. The model was then used to simulate spiral pipe forming of a 28" x 16mm HSAW pipe.

International Journal of Fracture, 2019
The Sandia Fracture Challenges provide the mechanics community a forum for assessing its ability ... more The Sandia Fracture Challenges provide the mechanics community a forum for assessing its ability to predict ductile fracture through a blind, round-robin format where mechanicians are challenged to predict the deformation and failure of an arbitrary geometry given experimental calibration data. The Third Challenge, issued in 2017, required participants to predict fracture in an additively manufactured 316L stainless steel tensile-bar configuration containing through holes and internal cavities that could not have been conventionally machined. The volunteer participants were provided extensive materials data, from tensile tests of specimens printed on the same build tray to electron backscatter diffraction maps of the microstructure and micro-computed tomography scans of the Challenge geometry. The teams were asked to predict a number of quantities of interest in the response, including predictions of variability in the resulting fracture response, as the basis for assessment of the predictive capabilities of the modeling and simulation strategies. This paper describes the Third Challenge, compares the experimental results to the predictions, and identifies successes and gaps in capabilities in both the experimental procedures and the computational analyses to inform future investigations.
Theoretical modeling of the bainitic transformation in TRIP steels
ABSTRACT
Detection of fatigue weld cracks using optical frequency domain reflectometry-based strain sensing
Fatigue weld crack detection using distributed fiber optic strain sensing
International Journal of Fatigue, Nov 1, 2023

Sustainable Construction & Design, Nov 6, 2012
Pipelines are constructed in hostile environments where the occurrence of imposed plastic deforma... more Pipelines are constructed in hostile environments where the occurrence of imposed plastic deformations can necessitate a strain based design approach. Under such conditions not only the strength and toughness properties have to be considered; also the strain capacity of pipe and weld metal become crucial. Considering the use of spirally welded linepipe sections, the helical seam weld and anisotropic material properties pose real challenges to pipeline designers. In our work, the tensile strain capacity and defect tolerance of high strength, high toughness spiral pipes will be investigated. This paper briefly discusses the different steps in the spiral pipe manufacturing process and their influence on the mechanical properties of the pipe. The forming angle is a key parameter as it determines (a) the anisotropy in strength and toughness of the pipe steel, and (b) the orientation of possible seam weld defects. Each mechanical operation (forming, expansion) and each thermal operation (welding, coating) will affect local or global strength, toughness and ductility properties of the pipe metal. A thorough material characterization at each process step is needed for a qualitative and quantitative understanding of these effects.
Uploads
Papers by Philippe Thibaux