Papers by Philippe Mourgue

ASME 2011 Pressure Vessels and Piping Conference: Volume 3, 2011
Dissimilar Metal Welds (DMW) are required in nuclear reactors to join low alloy steel components ... more Dissimilar Metal Welds (DMW) are required in nuclear reactors to join low alloy steel components and stainless piping. The thermal and mechanical mismatch between the dissimilar material characteristics favors the stress concentration in the weld along the austenitic/ferritic interface. Assessing the ductile tearing resistance of DMWs is an issue even for crack initiation. But predicting large crack extensions is even more difficult for several reasons: crack path deviation, J-R curve determination, transferability from specimen to structures. This paper presents an approach to determine the resistance curve of a DMW on the basis of a ductile tearing simulation using a cavity growth model. E Young's modulus J Crack driving force J i Physical crack initiation toughness M In-plane bending moment r i , r e Inside / outside radius of pipe r m
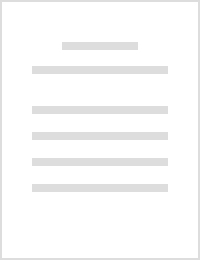
Volume 6A: Materials and Fabrication, 2013
ABSTRACT Some flaws may appear in metal components, in the weld region, and more especially in th... more ABSTRACT Some flaws may appear in metal components, in the weld region, and more especially in the case of electron beam girth weld in the slope area of the process (start and stop of the welding operation). These initial flaws can growth with delay even without any external loads. Indeed close to the junction, the material undergoes the combination of high tensile residual stresses due to welding operation and the presence of hydrogen brought by manufacturing process. Hydrogen assisted cracking is then suspected to explain the origin of crack growth through hydrogen embrittlement of the base metal.To understand by numerical modeling, at least qualitatively, the scenario of appearance of such cracks and their evolution, without any external load or under pressure load, the proposed approach consists first in simulating the welding process and its consequences on residual stress distribution and hydrogen concentrations [1]. The hydrogen diffusion computation is pursued after the welding operation simulation in order to highlight the most critical moment at which macroscopic defects may appear. Then, a macroscopic defect is created in the so determined critical zone, the stability of which is studied by estimating the energy release rate at the crack front and by comparing these values with experimental data such as the critical energy release rate at initiation and the tearing resistance curves which may depend on the hydrogen content. So, it is numerically possible to propagate the defect in the time, considering hydrogen diffusion and residual stress rebalancing, by successive crack front definition performed as the crack tip region exceeds the critical energy release rate [14]. Finally, the evolution of the defect is estimated in the same way under pressure test loading conditions. Results and discussions are presented to propose an engineering approach for the design assessment of such specific weld junctions with a low and hydrogen dependant toughness.
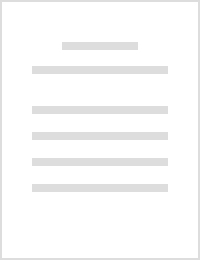
ASME 2010 Pressure Vessels and Piping Conference: Volume 6, Parts A and B, 2010
ABSTRACT In Pressurized Water Reactors, most of components have large thicknesses and their manuf... more ABSTRACT In Pressurized Water Reactors, most of components have large thicknesses and their manufacturing processes often require multipass welding. In spite of the stiffness of these components, the distortion issue may be important for operational requirements (e.g. misalignment) or controllability reasons (Non Destructive Examinations have to be feasible). These requirements may be difficult to meet by adjusting welding processes. Indeed because of the complexity of mechanisms involved during a welding operation and the high number of influencing parameters, this process is still essentially based on the experience of the welder. Furthermore the experimental estimation of the stress and distortion level in the component remains a difficult task that is subject to errors even if techniques are currently improved to become more accurate. That is the reason why AREVA NP has put many efforts into developing welding numerical simulations, in order to have a better understanding of the involved physical phenomena and also to predict the residual state allowing a qualification of the manufacturing processes in the very early phase of the welded components design. Within the framework of a R&D program whose main objective was to improve tools for numerical simulation of industrial cases of welding, AREVA NP has decided to validate new methodologies based on 3D computation by comparison with measurements. For this validation task the chosen test case concerns a peripheral adapter J-groove attachment weld on a vessel head. For such an application, operations of post-joining straightening have to be limited, if not prohibited, because of their cost or the impossibility to use them in front of a steel giant. The control of distortions during welding operations constitutes an important stake for which simulation can be of great help. Regarding distortions issues, an accurate metal deposit sequence modeling is mandatory, especially for multipass welding on such a complex geometry. The aim of this paper is to present, through a peripheral adapter J-groove attachment weld mock-up, the capabilities AREVA NP has in order to predict, in an efficient way the consequences of complex welding operations requiring 3D transient numerical simulations.

SIA conference …, 2007
Forming simulation technologies keep on developing at a rapi d pace, to address formability, tole... more Forming simulation technologies keep on developing at a rapi d pace, to address formability, tolerance control, and product performance issues throughout an increasing range of processes, and in ever more detail. Springback prediction, die compensation and assembly simulation continue to evolve, with new concepts to improve the accuracy of springback prediction and compensation. Prediction is addressed both from the numerical methods perspective, for example, using enhanced material models with elasto-plastic springback, and from a process perspective, for example by the incorporation of geomet ric drawbeads. Die compensation highlights how the integration of simulation and geometry plays an ever more important role, both in terms of improving accuracy and reducing lead time. Automotive components assembly processes include roll hemming and welding. The assembly simulation is the ideal soluti on for improving roll hemming, welding and the welding assembly processes, ensuring better part quality. The coupling of both stamping and welding simulation methodologies enables the user to optimize a complete manufacturing chain. The overall industrial objective is moving rapidly from simple Draw-Die compensation, towards full 'line die' compensation, in particular, considering the influence of 're-striking' as a mean of springback control. Tool Compensation techniques are also being applied to flanging operations. The question of springback prediction and compensation remains complex due to a significant number of influencing factors, especially the material's modeling. The evolution within material modeling must address not only new materials, but also new processes which are used to form these materials. A car component is manufactured from different parts which are stamped, cast, bent, then connected and welded together to fit the welding assembly requirement. The paper will discuss how the PAM-STAMP 2G TM integrated solution for springback prediction, compensation and roll hemming simulation and PAM-ASSEMBLY TM for assembly process design and validation are successfully implemented and coupled in industry to deliver a positive business impact on cost and quality, with emphasis on the Best Practices applied by users to different aspects of the prediction & correction methodology.
Volume 6B: Materials and Fabrication, 2014
Uploads
Papers by Philippe Mourgue