Papers by Paul Fredericks
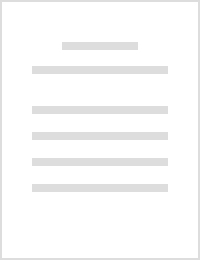
All Days, Mar 28, 2007
Access to previously unattainable offshore drilling targets continues to expand through advanceme... more Access to previously unattainable offshore drilling targets continues to expand through advancements in Managed Pressure Drilling (MPD) and Dynamic Annular Pressure Control (DAPC) technologies since their first application on the Mars TLP in 2005. Shell Exploration & Production Company successfully executed a second MPD operation, eliminating lost circulation and hole instability risks by utilizing a DAPC system on the Auger TLP. Redevelopment drilling in maturing deepwater fields is challenged by high circulating density (ECD) and depletion induced fracture gradient (FG) reduction for intervals that still require original mud weights (MW) for borehole stability. The DAPC system provides automated control of surface applied annular backpressure to the wellbore to a specified bottom hole pressure (BHP) set point. This allowed drilling on the Auger TLP with a surface mud weight lower than required by conventional drilling, effectively reducing the ECD magnitude on the open hole. The well design will be discussed, along with the equipment, methods, planning, preparation and training to successfully execute MPD offshore. Execution results and key learnings will be summarized.
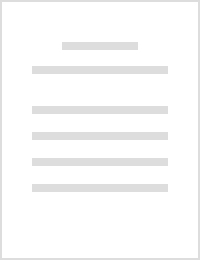
All Days, 2007
Access to previously unattainable offshore drilling targets continues to expand through advanceme... more Access to previously unattainable offshore drilling targets continues to expand through advancements in Managed Pressure Drilling (MPD) and Dynamic Annular Pressure Control (DAPC) technologies since their first application on the Mars TLP in 2005. Shell Exploration & Production Company successfully executed a second MPD operation, eliminating lost circulation and hole instability risks by utilizing a DAPC system on the Auger TLP. Redevelopment drilling in maturing deepwater fields is challenged by high circulating density (ECD) and depletion induced fracture gradient (FG) reduction for intervals that still require original mud weights (MW) for borehole stability. The DAPC system provides automated control of surface applied annular backpressure to the wellbore to a specified bottom hole pressure (BHP) set point. This allowed drilling on the Auger TLP with a surface mud weight lower than required by conventional drilling, effectively reducing the ECD magnitude on the open hole. The w...
Summary In deepwater exploration wells uncertainty in pore pressure (PP) and fracture gradient (F... more Summary In deepwater exploration wells uncertainty in pore pressure (PP) and fracture gradient (FG) and the margin between them increases the potential risk of gas influx, lost circulation, and wellbore instability. The risk of total losses is even greater in deepwater exploration prospects that contain salt and fractured carbonates. A new managed pressure drilling (MPD) system has been used in Guyana to drill deepwater exploration wells that have many of the same problems and potential risks that will occur in Mexico.
Automation is fast becoming a standard feature of Managed Pressure Drilling (MPD) systems for con... more Automation is fast becoming a standard feature of Managed Pressure Drilling (MPD) systems for constant bottom hole pressure (BHP) control. However, there are no standards for automation that an operator can use to distinguish one system’s capability from another. Comparison of different MPD service companies is further complicated by the lack of a standard method for determining reliability. Even if a standard methodology existed, because MPD automation is still very much an emerging technology there is still insufficient data to establish reliability benchmarks in different applications. In this paper we will discuss various practical measures that may be used to evaluate the level of performance for automated MPD services and quantify its value to the drilling operation. Actual data from automated MPD jobs will be used to illustrate and explain these measures.
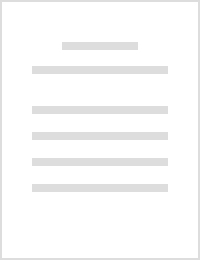
More often than not, high pressure and high temperature reservoirs are found in geological settin... more More often than not, high pressure and high temperature reservoirs are found in geological settings that carry inherently greater risk to drilling. Uncertain pressures, complex lithology, indeterminate flow-back, and the potential for high pressure well control are just some of the risks that drilling faces on an everyday basis. Decision making processes designed to mitigate those risks can carry significant non-productive time and cost. Emerging automated Managed Pressure Drilling services offers a solution to mitigate some of the critical risks associated with HPHT drilling and thereby reduce drilling costs. As a solution, automated MPD provides specialized technology to control drilling pressure but it also provides specialized procedures for HAZID/HAZOP contingencies, equipment integration, training, and drilling operations. This paper will describe: MPD equipment and rig compatibility MPD training requirements MPD value propositions for HPHT Case history data will be used as much as possible to illustrate those topics and as they relate to the planning for and implementation of MPD in HPHT wells.
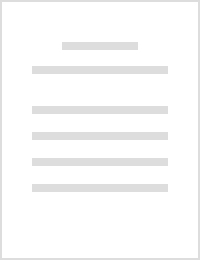
All Days, Feb 2, 2010
Development efforts by Shell in South Texas have focused on technology solutions to eliminate the... more Development efforts by Shell in South Texas have focused on technology solutions to eliminate the often encountered troubles drilling through significantly depleted sands to get to over pressured reservoirs below. The limits imposed by those conflicting conditions create narrow windows in which the difference between equivalent circulating density (ECD) and static bottom hole pressure (BHP) can be the difference between lost circulation and influx. Liner drilling with statically underbalance (SUB) mud is one solution Shell uses in low permeability reservoirs to eliminate lost circulation in part because it eliminates swab and surge effects and heavy trip margins. But by itself that solution doesn't work everywhere. In the McAllen and Pharr fields the amount by which the risk of losses can be reduced with liner drilling is limited because the sands can be more permeable and more likely to flow with SUB mud. For that reason Shell turned to automated managed pressure drilling (MPD) as a solution to drill more permeable reservoirs with SUB mud without influx. For the past two years Shell has used those complementary solutions in the McAllen-Pharr fields to improve drilling efficiency and reduce costs with mud statically less than pore pressure and constant bottom hole pressure (BHP). Recently, Shell drilled the Bales #7 well in the McAllen Field Wide Unit using a new scaled-down automated MPD system. The lower 700 feet of the 6½ hole was drilled in with 3½ production tubing with 15.7 ppg static mud into a target sand with an expected pore pressure of 15.8 ppg. In that interval the ECD was 16.2 ppg and the fracture gradient was 16.5 ppg which was the narrowest window that Shell has drilled in the McAllen-Pharr area to date. During casing drilling operations there was a steady flow of drill gas that varied between 1100 and 1400 units. Even with the drill gas the MPD system managed the BHP at a 16.2 ppg set point, +/− 0.18 ppg, without the use of an automated back pressure pump. That allowed Shell to avoid losses and the cost of a 5½ contingency liner drilling operation. In addition, and in the first of its kind application, Shell used the system to manage the BHP while cementing the drilled-in production tubing. With its smaller footprint, more efficient automated control, and proven ability to manage constant BHP this new MPD system can provide onshore and offshore operators a solution to improve drilling and cementing operations in mature depleted fields.
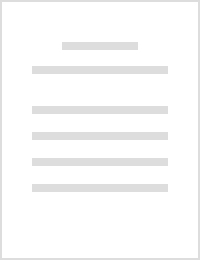
All Days, Sep 9, 1996
Although at-bit measurements provide rapid detection of changing lithology, real-time logging-whi... more Although at-bit measurements provide rapid detection of changing lithology, real-time logging-while-drilling (LWD) services are helpful in steering a horizontal well through the pay zone. Furthermore, these services provide the petrophysical data for formation evaluation. As the picture becomes more complex, standard LWD tools provide information that may help keep a well on track if the tools are used in a proactive manner. The responses of standard LWD resistivity and nuclear measurements have been well characterized in the literature. Therefore, these responses can be used to describe a reservoir, specifically the changing lithology and the geometrical structure of the formation. Forward modeling studies of 2- MHz LWD resistivity devices can identify changing geological facies. Neutron-density measurement, by the nature of the system, gives directionality to the measurement that identifies how the beds are approaching the tool and, therefore, the well. Examples presented from recently drilled horizontal wells clearly illustrate the application of these standard measurements in a complex horizontal well environment. Introduction Pay zone steering (PZS) is a geological steering technique that can help to (1) drive a well into a formation at the appropriate attitude and (2) recognize when the well is at or near the desired distance from a resistivity interface, such as the top of a formation, or fluid contact. In complex geological formations where faulting and stratigraphic features are present, these functions are performed by at-bit measuring tools, preferably with directional sensing tools. In simple circumstances, the PZS technique can use the standard, more economical, Logging-While-Drilling (LWD) services. PZS differs from normal geological steering operations because it predicts the expected log response before drilling and uses this predicted log to identify critical landmarks during drilling operations. If the measured log compares well with the prediction, then the well is assumed to be on track. Current measurement technology has advanced to the point where operators can seriously consider replacing wireline logs with LWD. Since a PZS operation uses standard LWD services, these services can also be used for a reservoir evaluation normally performed with wireline logs. An evaluation using LWD tools has several advantages.–savings in rig time for reservoir analysis–improved reservoir evaluation because of shorter exposure times, reduced invasion effects, better borehole conditions, and less formation damage–reduced risk inherent in LWD operations–quantifiable corrections and tool characterization Pay Zone Steering Principles PZS depends on the operator's ability to identify different formation layers using LWD devices. This layering is the basis for most geological models of the earth; this assumes that the layers occur in a predictable sequence and each layer has distinct physical and petrophysical parameters. This earth model is defined by the geologist who uses various surveys along with a geological understanding of the field to identify the various strata (seismic surveys, mud logs, wireline logs). P. 403
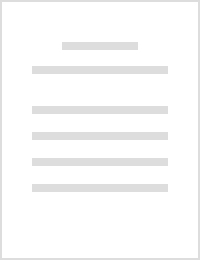
A rank exploration well drilled in Southwest Louisiana recently with Managed Pressure Drilling (M... more A rank exploration well drilled in Southwest Louisiana recently with Managed Pressure Drilling (MPD) techniques reached new operating levels for depth, pressure, and temperature. The exploration well reached a total depth of 29,426 ft at a maximum bottomhole pressure (BHP) and temperature of ~30,000 psi and ~500° F, respectively. Below 15,000 feet, the increased solubility of gas posed a particularly difficult risk for kick detection. The need for precise kick detection was magnified further by the uncertain magnitude of the pore pressure, the reduced kick tolerance, and well conditions conducive to swabbing during tripping operations. Managed pressure drilling techniques were employed to mitigate these risks. This paper will describe the processes that were used to identify the functional requirements and limitations of the MPD equipment that was selected to achieve the well objectives. The MPD process flow paths were designed early in the planning phase of the project to minimize any potential misapplication of MPD techniques during the execution phase. The paper will also include a description of the substructure vertical space limits that are created when installing MPD equipment. These designs were also completed in the early planning phase because the stack-height design defines the substructure spacing requirements, which can have a significant impact on rig selection and substructure requirement. The case history presented in this paper will document: The successful early detection of influxes of less than 3 barrelsThe implementation of managed pressure stripping procedures that resulted in increased tripping speedsThe application of MPD techniques that reduced the time spent circulating and managing gas at surface The above actions saved ample amounts of rig time in each of these areas. Additional MPD techniques were utilized to perform dynamic leak off and in-flow tests which yielded accurate data that will be used to refine earth models for possible future well applications. Key improvement opportunities were identified during the execution phase through daily communication meetings with the service provider, which were used to improve MPD plans, procedures, and reliability.
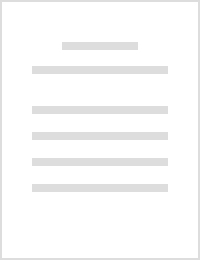
All Days, Oct 8, 1989
The Dual Propagation Resistivity (DPR*) tool provides two electromagnetic propagation resistivity... more The Dual Propagation Resistivity (DPR*) tool provides two electromagnetic propagation resistivity measurements to improve formation evaluation in all types of muds. It transmits a 2 MHz signal into the formation and measures the phase difference and amplitude ratio between two closely spaced antennas. These measurements are converted into phase difference resistivity, Rpd, and amplitude ratio resistivity, Rar, and together with gamma ray they are transmitted to the surface for real-time decision making. They are also stored in downhole memory and can be sampled as fast as every 5 seconds producing a high density data log for petrophysical analysis. The sample rate can be adjusted on the rig for changes in the drilling rate of penetration. penetration. The depth of investigation of Rar is deeper than Rpd but both are deep enough to eliminate most borehole effects. Beds as thin as the antenna spacing can be detected and the vertical resolutions are such that no corrections are needed in beds too thin for conventional induction tools. Two curves allow the effects of invasion and hydrocarbon to be distinguished, and log quality to be better controlled. Log behavior is similar to a dual induction log in most lithologies but there are important differences. Normally, the DPR logs are made just after drilling when invasion is not deep enough to affect either Rar or Rpd. In this case they both will read true formation resistivity, Rt. In a hydrocarbon sand Rpd and Rar will both read high, though Rar will be less accurate than Rpd if Rt is over 20 ohm-meters. Ideally, Rpd and Rar should read the same in impermeable lithologies, regardless of resistivity. In high resistivity formations Rpd is more accurate than Rar and it is less affected by the dielectric constant of the formation. Log quality is monitored in real-time by evaluating the separation of the two resistivities as a function of the lithology. In an impermeable, low resistivity formation the curves will read the same. If they do not, and the lithology does not change, then damage to one, or both, of the antennas is indicated. The DPR tool is calibrated for temperature and the antennas are hardened against the effects of hydrostatic pressure. Introduction The DPR tool, shown in Figure 1, was developed to provide accurate resistivity measurements when traditional techniques used by MWD short normal and wireline induction devices are unable to do so. For example, short normal resistivity measurements, though offering some thin bed detection, are limited by moderate-to-high concentrations of chlorine in the mud and are blocked by oil base muds. Induction logs offered on wireline are sometimes impossible to get in very high angle, rugose, or unevenly drilled wells. They also suffer from bad hole conditions that commonly develop between the time the hole is drilled and the time the wireline logs are finally run. The DPR tool is a high frequency electromagnetic resistivity tool that operates in oil, and salt saturated muds. It will detect beds as thin as 6 inches (15.2 cm), though it will not read Rt in these because of shoulder bed effects. However, given no invasion it will read Rt in beds which are too thin for induction tools to read without correction. It provides two resistivities with different vertical resolutions and depths of investigation. Rpd has better vertical resolution and accuracy than Rar but it is a more shallow measurement. Both require only little correction for contrasts of 100-to-500:1 between apparent formation resistivity, Ra, and mud resistivity, Rm. Testing began in late 1986 and continued to early 1989. The downhole and surface systems were tested in novel ways that included running the subs on a wireline in test wells at the Conoco Borehole Test Facility in Ponca City, Oklahoma. P. 521
Drilling contractor, 2006
Automation is fast becoming a standard feature of Managed Pressure Drilling (MPD) systems for con... more Automation is fast becoming a standard feature of Managed Pressure Drilling (MPD) systems for constant bottom hole pressure (BHP) control. However, there are no standards for automation that an operator can use to distinguish one system’s capability from another. Comparison of different MPD service companies is further complicated by the lack of a standard method for determining reliability. Even if a standard methodology existed, because MPD automation is still very much an emerging technology there is still insufficient data to establish reliability benchmarks in different applications. In this paper we will discuss various practical measures that may be used to evaluate the level of performance for automated MPD services and quantify its value to the drilling operation. Actual data from automated MPD jobs will be used to illustrate and explain these measures.
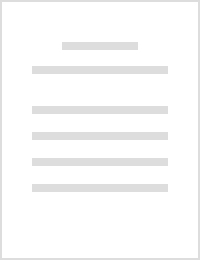
More often than not, high pressure and high temperature reservoirs are found in geological settin... more More often than not, high pressure and high temperature reservoirs are found in geological settings that carry inherently greater risk to drilling. Uncertain pressures, complex lithology, indeterminate flow-back, and the potential for high pressure well control are just some of the risks that drilling faces on an everyday basis. Decision making processes designed to mitigate those risks can carry significant non-productive time and cost. Emerging automated Managed Pressure Drilling services offers a solution to mitigate some of the critical risks associated with HPHT drilling and thereby reduce drilling costs. As a solution, automated MPD provides specialized technology to control drilling pressure but it also provides specialized procedures for HAZID/HAZOP contingencies, equipment integration, training, and drilling operations. This paper will describe: MPD equipment and rig compatibility MPD training requirements MPD value propositions for HPHT Case history data will be used...
L'invention concerne un procede et un dispositif de diagraphie en cours de forage permettant ... more L'invention concerne un procede et un dispositif de diagraphie en cours de forage permettant d'obtenir des informations concernant une formation. Le dispositif selon l'invention fait intervenir une pluralite d'ensembles de nervures comportant des capteurs montes sur patins sur une ou plusieurs douilles rotatives ou non, fixees a un boitier rotatif faisant partie d'un ensemble de forage. Les capteurs selon l'invention peuvent etre des capteurs de densite, des capteurs de neutrons, des capteurs a resonance magnetique nucleaire, des capteurs de resistivite, des capteurs soniques, des capteurs dielectriques ou tout autre type de capteurs. Dans un autre mode de realisation, les capteurs tournent avec le train de tiges.
Drilling Contractor, 2007
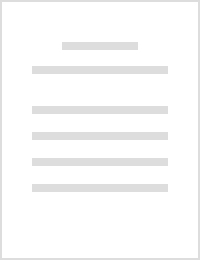
SPE/IADC Managed Pressure Drilling and Underbalanced Operations Conference and Exhibition, 2016
A rank exploration well drilled in Southwest Louisiana recently with Managed Pressure Drilling (M... more A rank exploration well drilled in Southwest Louisiana recently with Managed Pressure Drilling (MPD) techniques reached new operating levels for depth, pressure, and temperature. The exploration well reached a total depth of 29,426 ft at a maximum bottomhole pressure (BHP) and temperature of ~30,000 psi and ~500° F, respectively. Below 15,000 feet, the increased solubility of gas posed a particularly difficult risk for kick detection. The need for precise kick detection was magnified further by the uncertain magnitude of the pore pressure, the reduced kick tolerance, and well conditions conducive to swabbing during tripping operations. Managed pressure drilling techniques were employed to mitigate these risks. This paper will describe the processes that were used to identify the functional requirements and limitations of the MPD equipment that was selected to achieve the well objectives. The MPD process flow paths were designed early in the planning phase of the project to minimize ...
Drilling Contractor, 2007
Uploads
Papers by Paul Fredericks