Papers by Patrick Mattfeld
Advanced Materials Research, 2016
Applied Mechanics and Materials, 2015
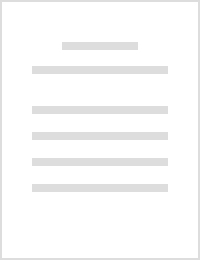
In collaboration between the Laboratory for Machine Tools and Production Engineering (WZL) and th... more In collaboration between the Laboratory for Machine Tools and Production Engineering (WZL) and the Schondelmaier GmbH Presswerk (SPW) a new warm solid forward extrusion process is developed. It aims at avoiding chevron crack formation at a greatly reduced energy input. In the new process, a direct resistance heating is carried out within the forming tool, simultaneously to the extrusion. The resulting increase in energy-efficiency was discussed in previous publications. In this work, two major challenges in terms of the practical implementation of the new hybridized process are embraced. Firstly, a tool concept is presented which integrates the electrical resistance heating into the forming tool. Secondly, a tool coating for the die inserts with a challenging combination of characteristics is derived. The characteristics are a sufficiently high wear as well as temperature resistance and, simultaneously, an adequately high electrical resistance. The latter one limits the electrical c...
Applied Mechanics and Materials, 2015
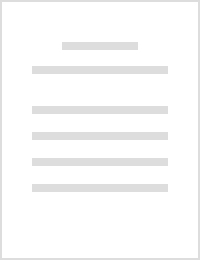
In collaboration between the Laboratory for Machine Tools and Production Engineering (WZL) and th... more In collaboration between the Laboratory for Machine Tools and Production Engineering (WZL) and the Schondelmaier GmbH Presswerk (SPW) a new warm solid forward extrusion process is developed. It aims at avoiding chevron crack formation at a greatly reduced energy input. In the new process, a direct resistance heating is carried out within the forming tool, simultaneously to the extrusion. The resulting increase in energy-efficiency was discussed in previous publications. In this work, two major challenges in terms of the practical implementation of the new hybridized process are embraced. Firstly, a tool concept is presented which integrates the electrical resistance heating into the forming tool. Secondly, a tool coating for the die inserts with a challenging combination of characteristics is derived. The characteristics are a sufficiently high wear as well as temperature resistance and, simultaneously, an adequately high electrical resistance. The latter one limits the electrical c...
The International Journal of Advanced Manufacturing Technology, 2016
Advanced Materials Research, 2016
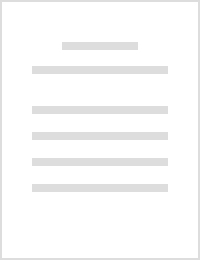
Surface and Coatings Technology, Jul 1, 2009
ABSTRACT After many essential applications e.g. in the field of machining, PVD tool coatings (phy... more ABSTRACT After many essential applications e.g. in the field of machining, PVD tool coatings (physical vapour deposition) materially gain importance for metal forming processes. Coated metal forming tools may enormously reduce tool and work piece wear, form capacities or deliver special functions formerly provided by lubricants and often toxic additives. As main properties, the coatings have to feature a very high adhesion to the substrate, a high hardness and adequate oxidation stability. To meet these requirements a nanolaminated TiHfN/CrN tool coating was developed using the arc ion plating technique. After a first development step the coating delivered the highest possible hardness in combination with the lowest possible Young's modulus. These basic properties, in combination with the ability to prevent the formation of cracks inside the coating structure, already led to outstanding performances in several metal forming processes. As a second step, this work reports the development of an additional nano-structured CrN top layer which is used for the reduction of the friction coefficient by providing a lubrication supporting functional surface. To prove the developed coating's tribological performance application oriented tests were carried out, e.g. pin-on-disc, regarding the coating's behaviour in interaction with a biodegradable synthetic ester as lubricant. Results of cup backward extrusion processes using coated punch tools are presented including measurements of the forming capacities.
Production Engineering, 2016
steel research international, 2016
Advanced Engineering Materials, 2015
Applied Mechanics and Materials, 2015
60 Excellent Inventions in Metal Forming, 2015
ABSTRACT Fine blanking is a well-established process for the production of near net shape compone... more ABSTRACT Fine blanking is a well-established process for the production of near net shape components with high quality. The produced parts are characterized by a smooth sheared edge up to 100 %, excellent surface properties with good flatness and little burr as well as close tolerances for near net shape manufacturing. These process characteristics are suitable for the efficient production of spur gears with large batch size. In this work, the application of fine blanking was extended for the production of helical gears. Therefore, the fine blanking process was modified with an additional rotary movement of the dies to realize the manufacturing of helical gears. In this contribution the process idea, experimental and numerical work as well as the potential of fine blanked helical gears is presented.
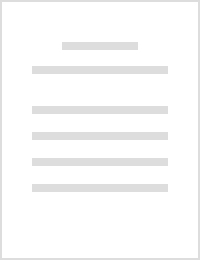
Procedia CIRP, 2013
ABSTRACT Highly stressed components like turbine blades made of IN718 (ASTM: B637), crankshafts m... more ABSTRACT Highly stressed components like turbine blades made of IN718 (ASTM: B637), crankshafts made of 42CrMo4 (ASTM: A322-4140) or connecting rods made of GGG60 (ASTM: A536-80-55-06) have to satisfy stringent requirements regarding durability and reliability. The induction of compressive stresses and strain hardening in the surface layer of technical components has proven to be a promising method to significantly increase the fatigue resistance. These required surface layer properties can be achieved by deep rolling. The determination of optimal deep rolling process parameters still requires elaborate experimental set-up and subsequent time- and cost-intensive measurements. Therefore, this work provides a new approach to determine surface layer properties by applying similarity mechanics in combination with FE-simulation of the deep rolling process. Thereby, this approach provides an efficient estimation of process results in which time-costly and challenging FE-simulations become redundant. (C) 2013 The Authors. Published by Elsevier B.V. Selection and peer-review under responsibility of International Scientific Committee of the 2nd CIRP Global Web Conference in the person of the Conference Chair Dr. Sotiris Makris
Uploads
Papers by Patrick Mattfeld