Papers by Nikhil Ranjan Dhar

The growing demands for high productivity of machining need use of high cutting velocity and feed... more The growing demands for high productivity of machining need use of high cutting velocity and feed rate. Such machining inherently produces high cutting temperature, which not only reduces tool life but also impairs the product quality. Metal cutting fluids changes the performance of machining operations because of their lubrication, cooling, and chip flushing functions but the use of cutting fluid has become more problematic in terms of both employee health and environmental pollution. Because of them some alternatives has been sought to minimize or even avoid the use of cutting fluid in machining operations. Some of these alternatives are dry machining and machining with minimum quantity of lubrication (MQL). This paper deals with experimental investigation on the role of MQL on cutting temperature, tool wear, surface finish and dimensional deviation in turning of AISI-1040 steel at industrial speed-feed combinations by uncoated carbide insert. The encouraging results include significant reduction in cutting temperature, tool wears and dimensional inaccuracy by MQL mainly through favorable chip-tool and work-tool interaction.
ASME eBooks, Nov 15, 2010

gazi university journal of science, Mar 25, 2010
In all machining processes, tool wear is a natural phenomenon and it leads to tool failure. The g... more In all machining processes, tool wear is a natural phenomenon and it leads to tool failure. The growing demands for high productivity of machining need use of high cutting velocity and feed rate. Such machining inherently produces high cutting temperature, which not only reduces tool life but also impairs the product quality. Metal cutting fluids changes the performance of machining operations because of their lubrication, cooling, and chip flushing functions but the use of cutting fluid has become more problematic in terms of both employee health and environmental pollution. The use of cutting fluid generally causes economy of tools and it becomes easier to keep tight tolerances and to maintain workpiece surface properties without damages. Due to these problems, some alternatives has been sought to minimize or even avoid the use of cutting fluid in machining operations. Some of these alternatives are dry machining and machining with minimum quantity lubrication (MQL). This paper deals with the experimental investigation on the role of MQL on cutting temperature, tool wear, surface roughness and dimensional deviation in turning of AISI-4340 steel at industrial speed-feed combinations by uncoated carbide insert. The encouraging results include significant reduction in tool wear rate, dimensional inaccuracy and surface roughness by MQL mainly through reduction in the cutting zone temperature and favorable change in the chip-tool and work-tool interaction.
Materials Today: Proceedings, Jun 1, 2023
Materials Today: Proceedings, 2022
International Journal of Machining and Machinability of Materials, 2006
Int. J. Machining and Machinability of Materials, Vol. 1, No. 1, 2006 ... Effects of cryogenic co... more Int. J. Machining and Machinability of Materials, Vol. 1, No. 1, 2006 ... Effects of cryogenic cooling by liquid nitrogen jets on tool wear, surface finish and dimensional deviation in turning different steels ... Department of Industrial and Production Engineering, Bangladesh University of ...
International Journal of Nanomanufacturing
Materials Today: Proceedings
Lecture notes in mechanical engineering, Sep 21, 2022
Advances in Materials and Processing Technologies
Materials Today: Proceedings, 2022
Journal of Production Systems and Manufacturing Science, Sep 26, 2020
International Journal on Interactive Design and Manufacturing (IJIDeM), 2022

The International Journal of Advanced Manufacturing Technology, 2017
This paper presents the analysis of average surface roughness, cutting force, and feed force in t... more This paper presents the analysis of average surface roughness, cutting force, and feed force in turning of difficultto-machine Ti-6Al-4Valloy by experimental investigation and performance modeling. Based on knowledge of the literature, to pacify the elevated temperature in machining Ti-6Al-4V and to ensure a clean environment, the experiments are carried out in cryogenic (liquid nitrogen) condition by following the Taguchi L 18 mixed-level orthogonal array. Afterward, the models of responses have been formulated by the response surface methodology (RSM) and artificial neural network (ANN). The higher values of correlation coefficient (≥96%) and lower values of error determined the adequacy of the developed models. Comparative study of both models revealed that the RSM-based model revealed greater accuracy for the testing data and hence recommended. Analysis of variance (ANOVA) determined the effects of cutting speed, feed rate, and insert configuration on the quality characteristics. The results revealed that a cutting speed not exceeding 110 m/min is likely to generate favorable machining responses. In addition, the higher feed rate was found to ensure better machining performances. Moreover, the desirability-based multi-response optimization determined that a cutting speed of 78 m/min, a feed rate of 0.16 mm/rev, and use of the SNMM tool insert are capable of minimizing surface roughness at 1.05 μm, main cutting force at 315 N, and feed force at 208 N.
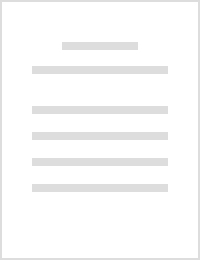
Measurement, 2016
In this study, an artificial neural network (ANN) based predictive model of average surface rough... more In this study, an artificial neural network (ANN) based predictive model of average surface roughness in turning hardened EN 24T steel has been presented. The prediction was performed by using Neural Network Tool Box 7 of MATLAB R2015a for different levels of cutting speed, feed rate, material hardness and cutting conditions. To be specific the dry and high pressure coolant (HPC) jet environments were explored as cutting conditions. The experimental runs were determined by full factorial design of experiment. Afterward the 3-n-1, 3-n-2 and 4-n-1 ANN architectures were trained by utilizing the Levenberg–Marquardt (LM), Bayesian regularization (BR) and scaled conjugate gradient (SCG) algorithms, and evaluated based on the lowest root mean square error (RMSE). The 3-10-1 and 3-4-2 ANN models, trained by BR, revealed the lowest RMSE. A good prediction fit of the models was established by the regression coefficients higher than 0.997. At last, the behavior of the surface roughness in respect of speed-feed-hardness for dry and HPC conditions has been analyzed. The HPC reduced surface roughness by the efficient cooling and lubrication whereas the higher hardness of material induced higher average surface roughness due to higher restraining force against tool imposed cutting force.
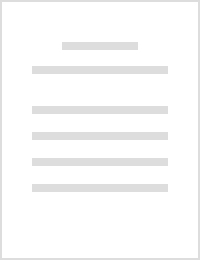
Machining Science and Technology, 2014
□ Residual stress is one of the critical characteristics for assessing the qualities and function... more □ Residual stress is one of the critical characteristics for assessing the qualities and functionalities of machined products in light of its direct effect on endurance limit, distortion, and corrosion resistance. Primary factors responsible for residual stresses distribution include mechanical effects, thermal effects, microstructure evolutions, and a combination of these mechanisms. This study investigates the effects of minimum quantity lubrication (MQL) on machining force, temperature and residual stress through a physics-based modeling method. Both the lubrication and cooling effects caused by MQL air-oil mixture contribute to changes in friction due to boundary lubrication as well as variations in the thermal stress due to heat loss. The modified Oxley's model is employed to predict the cutting force and temperature directly from cutting conditions. The predicted cutting force and temperature are then coupled into a thermal-mechanical model which incorporates the kinematic hardening and strain compatibility to predict the machining-induced residual stress under lubricated conditions. The proposed analytical method is experimentally verified by orthogonal cutting tests for AISI 4130 alloy steel in the context of forces, temperatures, and residual stresses.
International Journal on Interactive Design and Manufacturing (IJIDeM)
International Journal on Interactive Design and Manufacturing (IJIDeM), 2022
Uploads
Papers by Nikhil Ranjan Dhar