Papers by Nicholas Dagalakis

The 6-Degree of Freedom Tri-Stage Micro Positioner (6DFTSMP) can generate high accuracy, small di... more The 6-Degree of Freedom Tri-Stage Micro Positioner (6DFTSMP) can generate high accuracy, small displacement, and high-resolution motions. The moving platform of the device has six degrees (6-D) of freedom motions (translation and rotation about three orthogonal axes, X-Y-Z). The 6DFTSMP is unique because it derives its input motion from a monolithic tri-stage base plate and has struts that may have specially designed flexures. The 6DFTSMP capitalizes on the availability of inexpensive high quality planar micro-positioning stages for the control of its moving platform. Because the struts, which connect the planar micro positioning stages with the moving platform are oriented in a parallel mechanism fashion the in plane motion of the stages is converted into a translation and rotation about three orthogonal axes. Two experimental prototypes of the 6DFTSMP have been built and various mathematical models have been developed. A micro-position and orientation measurement sensor nest has b...
Simple programming and monitoring tools had to be developed to control the NIST RoboCrane ® to ac... more Simple programming and monitoring tools had to be developed to control the NIST RoboCrane ® to accommodate crane operators. The programmed move instructions are generated by an off-line graphic animator, and the data files are transferred through the internet. The data are of neutral text format and any robot controller with the proper interpreter can understand them. The controller operation can be monitored from a remote location, and control instructions can be issued remotely. An animation feedback interface allows for the graphic monitoring of the operation of the robot, the display of position errors, and sensor outputs. Various network tools are being tested for the real time transfer of data necessary for the last two interfaces. Again, the interface data are of neutral format.

2010 IEEE/RSJ International Conference on Intelligent Robots and Systems, 2010
This paper describes the operator assisted automated assembly of a 3-legged spatial platform by u... more This paper describes the operator assisted automated assembly of a 3-legged spatial platform by using a vision guided multi-probe assembly process. This is the first step towards the ultimate goal of building a microscale active spatial platform. Two issues are highlighted in this paper: contact management and vision feedback. Using multiple probes for part grasping and manipulation has the advantage of robustness and versatility as compared to micro-grippers. However, the contacts between the probes and the part need to be carefully managed to ensure a grasp that is stable for part pickup and yet manipulable to allow part motion in a controlled fashion. By using vision guidance, the probes can be coordinated to grasp the parts and lift them off the die securely and reliably. We show that the contacts act as point contacts with friction, so when a part is pressed against a stationary probe, the part rotates about the axis between the contacts, changing its orientation so it may be inserted into a slot in the substrate. We have demonstrated that the three legs can be assembled in a fully automated fashion via stereo vision feedback. The platform is at present assembled via teleoperation. The assembled microstructure measures 450 µm×600 µm. We are now working on the full automation of the assembly onto a substrate populated with MEMS actuators.
Handbook of Industrial Robotics
A brief description of the industrial robots related standards activities at the national and int... more A brief description of the industrial robots related standards activities at the national and international level is presented. The robot performance and safety standards are discussed in greater detail. A thorough list of national and international standards and committee drafts is provided with a brief description of each one of them.

Volume 2: 28th Biennial Mechanisms and Robotics Conference, Parts A and B, 2004
This paper presents an analysis tool and design method for MEMS parallel mechanisms. Due to proce... more This paper presents an analysis tool and design method for MEMS parallel mechanisms. Due to processing constraints in MEMS fabrication, flexure joints are frequently used in MEMS mechanisms. Flexure joints offer advantages over other joint designs due to their monolithic characteristics. They can be used to reduce the size of manipulators or to increase the precision of motion. Their inherent flexibility, however, also results in task space compliance which needs to be carefully designed to match the task specification. This paper presents an analysis and design tool for such mechanisms by using the differential kinematics. Performance metrics are chosen based on manipulability and task stiffness matrices, which in turn are used in a multi-objective optimization. As an illustrative example, a 1-DOF MEMS parallel mechanism based on the macro- and meso-scale models designed by NIST is considered with several choices of performance metrics and design variables. The resulting designs ar...
Journal of Offshore Mechanics and Arctic Engineering, 1989
This describes the first phase of an effort to develop a robot crane for shipbuilding application... more This describes the first phase of an effort to develop a robot crane for shipbuilding applications. The focus of this phase is on the study of the stiffness characteristics of this robot as a function of its geometry payload and height. A brief description of the design of the main part of the robot crane consisting of a six-wire parallel link manipulator is given. The stiffness of the manipulator to side loads and moments was studied. The nonlinear and linearized mathematical model of the manipulator stiffness matrix is derived. Stiffness measurement tests were conducted using a small size laboratory model. The results of these tests for various external loads, heights, and payloads are given. Computer simulation and theoretical results are also discussed.

Journal of Micromechanics and Microengineering, 2012
In micro-electro-mechanical systems (MEMS) it is difficult to obtain a large range of motion with... more In micro-electro-mechanical systems (MEMS) it is difficult to obtain a large range of motion with a small coupled error. This limitation was overcome by designing and fabricating a nested structure as a serial kinematic mechanism (SKM). In this paper, a MEMS-based XY stage is reported for multifinger manipulation application. The SKM MEMS XY stage is implemented by embedding a single degree-of-freedom (DOF) stage into another single DOF stage. The proposed MEMS XY stage is fabricated by deep reactive ion etching (DRIE) from both sides of a silicon-on-insulator (SOI) wafer. This SKM MEMS stage has the capability to generate more than 50 μm displacements along each X-and Y-axes. This nested structure also suppressed the coupled motion error to 0.6% of the original actuation displacement. For the demonstration on the micro-particle manipulation, a 15 μm sized polypropylene particle is manipulated and rotated by operating two individual fingers attached to proposed MEMS stages.

IEEE Transactions on Robotics, 2012
This paper describes the algorithm development and experimental results of a vision-guided multip... more This paper describes the algorithm development and experimental results of a vision-guided multiprobe microassembly system. The key focus is to develop the capabilities required for the construction of 3-D structures using only planar microfabricated parts. Instead of using grippers, multiple sharp-tipped probes are coordinated to manipulate parts by using vision feedback. This novel probe-based approach offers both stable part grasping and dexterous part manipulation. The light weight of the part and relatively slow motion means that only kinematics-based control is required. However, probe motions need to be carefully coordinated to ensure reliable and repeatable part grasping and manipulation. Machine vision with multiple cameras is used to guide the motion. No contact force sensor is used; instead, vision sensing of the probe bending is used for the grasp force control. By combining preplanned manipulation sequences and vision-based manipulation, repeatable spatial (in contrast with planar) manipulation and insertion of a submillimeter part have been demonstrated with an experimental testbed consisting of two actuated probes, a passive probe, an actuated die stage, and two cameras for vision feedback.

IEEE Transactions on Robotics, 2005
Flexure joints are frequently used in precision-motion stages and microrobotic mechanisms due to ... more Flexure joints are frequently used in precision-motion stages and microrobotic mechanisms due to their monolithic construction. The joint compliance, however, can affect the static and dynamic performance of the overall mechanism. In this paper, we consider the analysis and design of general platform-type parallel mechanisms containing flexure joints. Based on static performance measures such as task-space stiffness and manipulability, and constraints such as joint stress, mechanism size, and workspace volume, we pose the design problem as a multiobjective optimization. We first calculate the Pareto frontier, which can then be used to select the desired design parameters based on secondary criteria, such as performance sensitivity and dynamic characteristics. To facilitate design iteration, we apply the pseudo rigid-body approach with a lumped approximation of the flexure joints. A planar mechanism is used to illustrate the analysis and design techniques.
IEEE Transactions on Instrumentation and Measurement, 2011
The scale of nano objects requires very precise position determination. The state-of-the-art mani... more The scale of nano objects requires very precise position determination. The state-of-the-art manipulators involve accurate nanometer positioning. This paper presents the design of a capacitive displacement sensor for a nanopositioning application. The challenges of designing a capacitor sensitive to nanometer movements that fits in the area of a few hundred square micrometers are described. Analysis of several different designs was carried out using commercial simulation software. Results suggest a sensing resolution of 10 nm displacement. A sensor prototype was fabricated and tested.

Fall Meeting of Society of Experimental Stress …, 1980
When you hear a mysterious new sound when driving your car you know that it usually means trouble... more When you hear a mysterious new sound when driving your car you know that it usually means trouble. Now such signals can be translated into a "signature" which identifies the problem by a technique called "Random Decrement". First the vibrations have to be picked up by a sensor like the pickup in a record player. Then these signals which appear meaningless in their original form are sorted and a characteristic signature is established which engineers can relate to the mechanical properties of the system. If a flaw such as a fatique crack develops, the signature changes, thus warning the operator of impending failure. The "Random Decrement" technique is particularly well suited to the class of problems in which characteristics are desired of an in-service structure subjected to unknown random excitation such as wind, earthquakes, waves, sound, traffic loads, etc •• Analysis requires only the measurement of the dynamic response of a structure, and not the excitation. Continuous automatic monitor ing is possible. The method has been applied in flight flutter testing of the F-16 aircraft, in monitoring the seals during operation of a wind tunnel, in detecting cracks and measuring damping in structures such as ships, bridges, pipes and machinery. More recently it is being used in a joint ONR-USGS research program for remote detection of underwater structural failures in ocean platforms.

Journal of Research of the National Institute of Standards and Technology, 2008
Members of the staff from the Food and Drug Administration (FDA), the National Cancer Institute (... more Members of the staff from the Food and Drug Administration (FDA), the National Cancer Institute (NCI), the University of Texas at Arlington (UTA), the National Institute of Standards and Technology (NIST), and ASTM International, in cooperation with other government agencies, private industries, and universi-ties, agreed to collaborate in order to document and prioritize the measurement and measurement-related standards needs of a few categories of medical devices. The ultimate goal of this identification initiative is to help NIST direct resources, or to create partnerships, to provide solutions to these needs (). Discoveries and technology developments during the 20th century made possible the development of a significant number of medical devices that have radically transformed the way medical care is delivered today. These include computed axial tomography (CAT) in 1972, magnetic resonance imaging (MRI) in 1977, positron emission tomography (PET) in
The 4D/RCS architecture provides a reference model for military unmanned vehicles on how their so... more The 4D/RCS architecture provides a reference model for military unmanned vehicles on how their software components should be identified and organized. It defines ways of interacting to ensure that missions, especially those involving unknown or hostile environments, can be analyzed, decomposed, distributed, planned, and executed intelligently, effectively, efficiently and in coordination. To achieve this, the 4D/RCS reference model provides well defined and highly coordinated sensory processing, world modeling, knowledge management, cost/benefit analysis, behavior generation, and messaging functions, as well as the associated interfaces. The 4D/RCS architecture is based on scientific principles and is consistent with military hierarchical command doctrine.
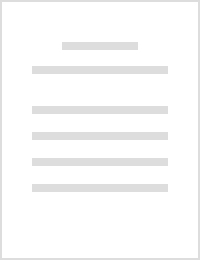
researching new concepts in robotic cranes for several years. These concepts use the basic idea o... more researching new concepts in robotic cranes for several years. These concepts use the basic idea of the Stewart platform parallel link manipulator. The unique feature of the NIST approach is to use cables as the parallel links and to use winches as the actuators. Based on this idea, a revolutionary new type of robot crane has been developed and aptly named the RoboCrane. The RoboCrane provides six degree-of-freedom load stabilization and maneuverability. This is accomplished through the following control modes: master/slave; joystick input; operator panel input; preprogrammed trajectory following (teach programing, graphical off-line programing, or part programing); and sensor based motion compensation. The current control system includes both the controller and user interface within the same control level, which makes controller enhancements and modifications difficult and error prone. A Real-time Control System (RCS) [1] is currently being developed to include the above control mod...

The Intelligent Systems Division (ISD) at the National Institute of Standards and Technology has ... more The Intelligent Systems Division (ISD) at the National Institute of Standards and Technology has been using modeling and simulation and software for conceptual design and prototyping of advanced robotic cranes. RoboCrane® concepts have been developed for various applications, such as military ISO-container handlers on land and sea, large-scale welding and gripping, and nuclear waste remediation. The capability to develop our models in an advanced solid modeler and convert them into moving, controlled designs is critical to achieve the level of confidence that is required before building a full-scale prototype. Although we do have scaledprototypes of some of our designs, the computer model, controlled with simulation programming and developed from imported solid models, offers a good way for sponsors to see the concepts and capabilities of the RoboCrane® systems. This overview paper summarizes the efforts of ISD in developing the RoboCrane® simulations and the important role simulati...
Sources indicate that 8.8% of revision hip surgery could be attributed to malpositioning of the i... more Sources indicate that 8.8% of revision hip surgery could be attributed to malpositioning of the implant (Heck D.A., 2006; Malchau H., 2002). This includes dislocation (5.8%) and technical error (3.0%). A revision orthopaedic surgery is significantly more risky and painful than the original operation. The total number of revision hip and knee replacement surgeries in the U.S. in 2005 was ~18,285 (HCUPnet/AHRQ). The 8.8% of these revision surgeries amounts to 1,609 operations. Since the cost of a revision surgery is ~$45,621 (Heck D.A.), the total cost of these revision operations was $73,407,838. It is natural that people started looking into the use of new technologies like Computer Assisted Surgery (CAS) to reduce implant malpositioning.

espite the tremendous growth in the use of robots during the last Df ive years, no standard robot... more espite the tremendous growth in the use of robots during the last Df ive years, no standard robot performance and calibration tests exist. Cur-rentfy, several commitees formed by the International Organization for Standardization (ISO) are working on the development of such standards on the intema-tional level. In the US, several technical committees of the Robotic Industries Association (RIA) in Ann Arbor, MI. in collaboration with the American National Standards institute, are working for the establishment of similar standards. Fundamental to the establishment of these robot performance and calibration tests is the existence of reliable and accurate m e t r o l o g y sensors to perform the required measurements. Our experience is that noncontact sensors are preferable since contact force (depending on its magnitude) could have a significant effect on the robot's dynamic response. Thus, optical metrology sensors could be ideal for such uses assum-robot testing and calibration a...
Uploads
Papers by Nicholas Dagalakis