Papers by Mohanad Alabdullah
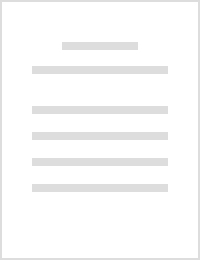
A Preliminary Study on Machinability of Super Austenitic Stainless Steel
Volume 2A: Advanced Manufacturing, Nov 13, 2015
Stainless steel is the most widely used alloys of steel. The reputed variety of stainless steel h... more Stainless steel is the most widely used alloys of steel. The reputed variety of stainless steel having customised material properties as per the design requirements is Duplex Stainless Steel and Austenitic Stainless Steel. The Austenite Stainless Steel alloy has been developed further to be Super Austenitic Stainless Steel (SASS) by increasing the percentage of the alloying elements to form the half or more than the half of the material composition. SASS (Grade-AL-6XN) is an alloy steel containing high percentages of nickel (24%), molybdenum (6%) and chromium (21%). The chemical elements offer high degrees of corrosion resistance, toughness and stability in a large range of hostile environments like petroleum, marine and food processing industries. SASS is often used as a commercially viable substitute to high cost non-ferrous or non-metallic metals. The ability to machine steel effectively and efficiently is of utmost importance in the current competitive market. This paper is an attempt to evaluate the machinability of SASS which has been a classified material so far with very limited research conducted on it. Understanding the machinability of this alloy would assist in the effective forming of this material by metal cutting. The novelty of research associated with this is paper is reasonable taking into consideration the unknowns involved in machining SASS. The experimental design consists of conducting eight milling trials at combination of two different feed rates, 0.1 and 0.15 mm/tooth; cutting speeds, 100 and 150 m/min; Depth of Cut (DoC), 2 and 3 mm and coolant on for all the trials. The cutting tool has two inserts and therefore has two cutting edges. The trial sample is mounted on a dynamometer (type 9257B) to measure the cutting forces during the trials. The cutting force data obtained is later analyzed using DynaWare supplied by Kistler. The machined sample is subjected to surface roughness (Ra) measurement using a 3D optical surface profilometer (Alicona Infinite Focus). A comprehensive metallography process consisting of mounting, polishing and etching was conducted on a before and after machined sample in order to make a comparative analysis of the microstructural changes due to machining. The microstructural images were capture using a digital microscope. The microhardness test were conducted on a Vickers scale (Hv) using a Vickers microhardness tester. Initial bulk hardness testing conducted on the material show that the alloy is having a hardness of 83.4 HRb. This study expects an increase in hardness mostly due to work hardening may be due to phase transformation. The results obtained from the cutting trials are analyzed in order to judge the machinability of the material. Some of the criteria used for machinability evaluation are cutting force analysis, surface texture analysis, metallographic analysis and microhardness analysis. The methodology followed in each aspect of the investigation is similar to and inspired by similar research conducted on other materials. However, the novelty of this research is the investigation of various aspects of machinability and drawing comparisons between each other while attempting to justify each result obtained to the microstructural changes observed which influence the behaviour of the alloy. Due to the limited scope of the paper, machinability criteria such as chip morphology, Metal Removal Rate (MRR) and tool wear are not included in this paper. All aspects are then compared and the optimum machining parameters are justified with a scope for future investigations.
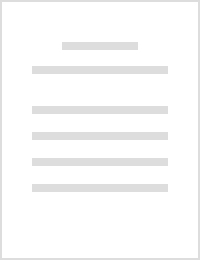
An investigation on machinability assessment of Al-6XN and AISI 316 alloys: an assessment study of machining
Machining Science and Technology, Mar 4, 2019
Abstract This work presents machinability assessment of AL-6XN super austenitic stainless steel a... more Abstract This work presents machinability assessment of AL-6XN super austenitic stainless steel alloy. Cutting forces, surface roughness, work hardening tendency and tool wear were analyzed. The assessment was conducted based on a comparison between the AL-6XN alloy and the well-known alloy in the machining field AISI 316. Finite element analysis (FEA) study was also conducted and used in this assessment. Experimental results showed maximum increase of 70% and 57% in the feed and normal forces of the AL-6XN alloy, respectively. Maximum increase in the work hardening tendency of 59% was recorded for the AL-6XN alloy while only 29% was recorded for the 316 alloy. The roughness analysis recorded an increase of 186% for the AL-6XN alloy compared to the 316 alloy. Tool wear analysis revealed the build-up edge formation, severe chipping, flank and crater wear (CW) during cutting AL-6XN alloy whereas small chipping, flank and CW were noticed during cutting 316 alloy. FEA study showed when the AL-6XN alloy machined using 65 and 94 m/min cutting speeds, the increases (compared to the 316 alloy) were: 12% and 8% in plastic strain; 20% and 20% in stresses; 48% and 100% in residual tensile stresses; 22% and 92% in residual compressive stresses, respectively.
Machinability analysis of super austenitic stainless steel
This research reports and evaluates the machinability of super austenitic stainless steel, AL-6XN... more This research reports and evaluates the machinability of super austenitic stainless steel, AL-6XN alloy by understanding the plastic deformation during the machining process using designated experiments and finite element modelling. The findings recorded confirm responsible machinability factors such as high plastic strain, work-hardening tendency, surface residual stress and tool wear

Materialwissenschaft Und Werkstofftechnik, Feb 23, 2017
This work aimed to identify the work-hardening regions in shear zones when the AL-6XN super auste... more This work aimed to identify the work-hardening regions in shear zones when the AL-6XN super austenitic stainless steel alloy was machined using a turning machine. A quick-stop approach was used to generate frozen chip roots. Two cutting speeds of 94 m/min and 65 m/min, a feed rate of 0.2 mm/rev and depth of cut of 1 mm were applied in this study. Microhardness measurements were executed in the hardening region (workpiece-shear zone-chip zone). Results showed that the hardness values were significantly increased in the primary shear zone and the formed chip. The wear of the cutting tool used to machine the alloy was investigated using scanning electron microscope. Excessive notch wear was located on the cutting edge when 65 m/min cutting speed was utilized while at 94 m/min cutting speed, the cutting edge was completely damaged as a flake of the edge was removed due to hard cutting processes. The profile measurement of the cutting tool was executed using an optical profilometer to reveal the changes in the cutting edges locations and profiles and their implication on machining process.
Finite Element Analysis Machining Assessment Study of AL-6XN and Inconel 718 alloys
International Journal of Machining and Machinability of Materials, 2021
Machinability analysis of super austenitic stainless steel
This research reports and evaluates the machinability of super austenitic stainless steel, AL-6XN... more This research reports and evaluates the machinability of super austenitic stainless steel, AL-6XN alloy by understanding the plastic deformation during the machining process using designated experiments and finite element modelling. The findings recorded confirm responsible machinability factors such as high plastic strain, work-hardening tendency, surface residual stress and tool wear
Analysis of Heat Generated in the Shear Zone during Machining of Titanium Alloy Ti6Al4V Using Infrared Thermal Camera
Materials Science Forum, 2018
Machining represents a thermo-mechanical reaction based on factors such as plasticity, wear and f... more Machining represents a thermo-mechanical reaction based on factors such as plasticity, wear and friction. The experimental design consists of conducting a series of turning trials on a titanium alloy Ti6Al4V using combinations of cutting parameters namely spindle speed (n) of 770 rpm; feed rate (f) of 0.2 and 0.4 mm/rev; and depth of cut (d) of 1 and 2 mm. The length of cut (L) of 10 mm remains constant for all trials. All trails are done under dry conditions. In this paper, a detailed investigation has been carried out to study the temperature at shear zone and the effect of cutting variables on temperature has been evaluated. The temperature in shear zone for each trial was measured using an infrared thermal camera.
旋削AL6XNスーパーオーステナイト系ステンレス鋼中の被削性に及ぼす加工硬化,工具摩耗と幾何学応答の影響:AL6XN合金の加工硬化と摩耗の研究【Powered by NICT】
Materialwissenschaft Und Werkstofftechnik, 2017

Materialwissenschaft und Werkstofftechnik, 2017
This work aimed to identify the work‐hardening regions in shear zones when the AL‐6XN super auste... more This work aimed to identify the work‐hardening regions in shear zones when the AL‐6XN super austenitic stainless steel alloy was machined using a turning machine. A quick‐stop approach was used to generate frozen chip roots. Two cutting speeds of 94 m/min and 65 m/min, a feed rate of 0.2 mm/rev and depth of cut of 1 mm were applied in this study. Microhardness measurements were executed in the hardening region (workpiece–shear zone–chip zone). Results showed that the hardness values were significantly increased in the primary shear zone and the formed chip. The wear of the cutting tool used to machine the alloy was investigated using scanning electron microscope. Excessive notch wear was located on the cutting edge when 65 m/min cutting speed was utilized while at 94 m/min cutting speed, the cutting edge was completely damaged as a flake of the edge was removed due to hard cutting processes. The profile measurement of the cutting tool was executed using an optical profilometer to re...
MATEC Web of Conferences, 2017
This paper presents tool wear study when a machinability test was applied using milling on Super ... more This paper presents tool wear study when a machinability test was applied using milling on Super Austenitic Stainless Steel AL6XN alloy. Eight milling trials were performed under two cutting speeds, 100 m/min and 150 m/min, combined with two feed rates at 0.1mm/tooth and 0.15 mm/tooth and two depth of cuts at 2 mm and 3 mm. An Alicona 3D optical surface profilometer was used to scan cutting inserts flank and rake face areas for wear. Readings such as maximum and minimum deviations were extracted and used to analyse the outcomes. Results showed various types of wear were generated on the tool rake and flank faces. The common formed wear was the crater wear. The formation of the build-up edge was observed on the rake face of the cutting tool.

Journal of Metallurgy, 2016
Inferior surface quality is a significant problem faced by machinist. The purpose of this study i... more Inferior surface quality is a significant problem faced by machinist. The purpose of this study is to present a surface texture analysis undertaken as part of machinability assessment of Super Austenitic Stainless Steel alloy-AL6XN. The surface texture analysis includes measuring the surface roughness and investigating the microstructural behaviour of the machined surfaces. Eight milling trials were conducted using combination of cutting parameters under wet machining. An optical profilometer (noncontact) was used to evaluate the surface texture at three positions. The surface texture was represented using the parameter, average surface roughness. Scanning Electron Microscope was utilised to inspect the machined surface microstructure and correlate the microstructure with the surface roughness. Results showed that maximum roughness values recorded at the three positions in the longitudinal direction (perpendicular to the machining grooves) were 1.21 μm (trial 1), 1.63 μm (trial 6), ...

International Journal of Manufacturing Engineering, 2016
This paper presents a study of tool wear and geometry response when machinability tests were appl... more This paper presents a study of tool wear and geometry response when machinability tests were applied under milling operations on the Super Austenitic Stainless Steel alloy AL-6XN. Eight milling trials were executed under two cutting speeds, two feed rates, and two depths of cuts. Cutting edge profile measurements were performed to reveal response of cutting edge geometry to the cutting parameters and wear. A scanning electron microscope (SEM) was used to inspect the cutting edges. Results showed the presence of various types of wear such as adhesion wear and abrasion wear on the tool rake and flank faces. Adhesion wear represents the formation of the built-up edge, crater wear, and chipping, whereas abrasion wear represents flank wear. The commonly formed wear was crater wear. Therefore, the optimum tool life among the executed cutting trails was identified according to minimum length and depth of the crater wear. The profile measurements showed the formation of new geometries for t...
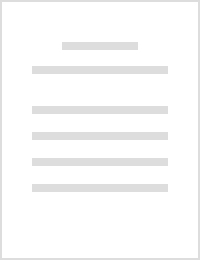
A Preliminary Study on Machinability of Super Austenitic Stainless Steel
Volume 2A: Advanced Manufacturing, 2015
Stainless steel is the most widely used alloys of steel. The reputed variety of stainless steel h... more Stainless steel is the most widely used alloys of steel. The reputed variety of stainless steel having customised material properties as per the design requirements is Duplex Stainless Steel and Austenitic Stainless Steel. The Austenite Stainless Steel alloy has been developed further to be Super Austenitic Stainless Steel (SASS) by increasing the percentage of the alloying elements to form the half or more than the half of the material composition. SASS (Grade-AL-6XN) is an alloy steel containing high percentages of nickel (24%), molybdenum (6%) and chromium (21%). The chemical elements offer high degrees of corrosion resistance, toughness and stability in a large range of hostile environments like petroleum, marine and food processing industries. SASS is often used as a commercially viable substitute to high cost non-ferrous or non-metallic metals. The ability to machine steel effectively and efficiently is of utmost importance in the current competitive market. This paper is an a...

The International Journal of Advanced Manufacturing Technology, 2016
This paper presents a finite element cutting model based on physical microstructure to investigat... more This paper presents a finite element cutting model based on physical microstructure to investigate the thermomechanical behaviour of AL-6XN Super Austenitic Stainless Steel in the primary shear zone. Frozen chip root samples were created under dry turning operation to observe the plasticity behaviour occurring in the shear zones to compare with the model for analysis. Chip samples were generated under cutting velocities at 65 and 94 m/min, feed rate at 0.2 mm/rev and depth of cut at 1 mm. Temperature on the cutting zone was recorded by infrared thermal camera. Secondary and backscatter electron detectors were used to investigate the deformed microstructure and to calculate the plastic strain. Experimental results showed the formation of microcracks (build-up edge triggers) at the chip root stagnation zone of both samples. The austenite phase patterns were evident against the cutting tool tip in the stagnation zone of the chip root fabricated at 65 m/min. The movement of these patterns caused the formation of the slip lines within the grains. The backscatter diffraction maps showed the formation of special grain boundaries within the slip lines, workhardening layer and in the chip region. Strain measurements in the microstructures of the chip roots fabricated at 94 and 65 m/min showed high values of 6.5 and 5.7 (mm/mm) respectively. The finite element model was used to measure the stress, strain, temperature and chip morphology. Numerical results were compared to the outcomes of the experimental work to validate the finite element model. The model validating process showed good agreement between the experimental and numerical results, and the error values were calculated. For a 94-and 65-m/min cutting speeds, 7.5 and 5.2% were the errors in the strain, 3 and 2.5% were the error in the temperature and 4.7 and 6.8% were the error in the shear plane angles.

International Journal of Materials Forming and Machining Processes, 2017
The AL6XN Super Austenitic Stainless Steel alloy is a commonly used steel in corrosive environmen... more The AL6XN Super Austenitic Stainless Steel alloy is a commonly used steel in corrosive environments and tough applications. This paper aims to investigate the execution of a machining process on the AL6XN alloy. A wet machining process has been executed to machine the alloy under a combination of various cutting conditions using an up milling approach. Two cutting speeds, two cutting depths and two feeds were used. The outputs obtained and listed in this paper are the microstructure analysis, surface microhardness and the chip morphology. The microstructure of the AL6XN alloy was revealed using Electron Microscope and Electron Backscatter Diffraction (EBSD). Work hardening layer was located in the subsurface of the machined alloy. EBSD data assured that no phase transformation was occurred within the deformed microstructure due to machining. The chip cross-section was revealed to identify the presence of the shear bands and to calculate the alloy serration degree.
Uploads
Papers by Mohanad Alabdullah