Papers by Mario Belmar-Gil
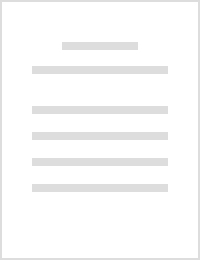
Modeling Internal Flow and Primary Atomization in a Simplex Pressure-Swirl Atomizer
Atomization and Sprays
Numerical simulations of simplex pressure-swirl atomizers can aid their design process toward bet... more Numerical simulations of simplex pressure-swirl atomizers can aid their design process toward better atomization. This work aims at studying the two-phase flow at both the internal geometry and the first millimeters of the external domain of such atomizers, where primary breakup takes place. In particular, the atomizer under study has been used in the CORIA Rouen Spray Burner (CRSB) test rig, which aims at studying lean premixed turbulent combustion. Ultimately, our goal is to complete the spray characterization in the vicinity of the injector. Such data will potentially enforce the validity of numerical simulations of nonreacting and reacting flow for this burner. Injection characteristics are analyzed through an interface capturing method within a detailed numerical simulations framework. The importance of the internal flow simulation on the final result is demonstrated in the manuscript, but it requires accurately measuring the injector internal geometry. In the present investiga...

Fuel, 2019
In this paper, a one-dimensional computational model of the flow in a common-rail injector is use... more In this paper, a one-dimensional computational model of the flow in a common-rail injector is used to compute local variations of fuel temperature (including the temperature change produced upon expansion across the nozzle) and analyse their effect on injector dynamics. These variations are accounted through the adiabatic flow hypothesis, assessed in a first part of the paper where the model features are also described. They imply variations in the fuel properties and the flow regime established across the injector internal restrictions driving the solenoid valve. An extensive validation of the model against experimental results is presented for a wide range of conditions. Multiple injection strategies are also explored, analysing the influence of the inlet fuel temperature and its variations on the mass injected by successive injections and the critical dwell time below which they cannot be separated. Results show significant changes in fuel temperature across some injector restrictions. These changes are greater the highest the rail pressure and lowest the fuel temperature at the injector inlet. In the case of the flow across nozzle orifices, the fuel can be either heated or subcooled depending on the operating conditions, the heating being especially relevant for cold-start-like fuel temperatures at the inlet. Thermal effects also influence the injection rate and duration. This influence on injector dynamics is particularly accused in the injector of study due to its ballistic nature. In this regard, the time needed to effectively separate two successive injections is greater the higher the fuel temperature and the injection pressure.

Proceedings of the Institution of Mechanical Engineers, Part G: Journal of Aerospace Engineering, 2020
Fuel efficiency improvement and harmful emissions reduction are the main motivations for the deve... more Fuel efficiency improvement and harmful emissions reduction are the main motivations for the development of gas turbine combustors. Numerical computational fluid dynamics (CFD) simulations of these devices are usually computationally expensive since they imply a multi-scale problem. In this work, gaseous non-reactive unsteady Reynolds-Averaged Navier–Stokes and large eddy simulations of a gaseous-fueled radial-swirled lean direct injection combustor have been carried out through CONVERGE™ CFD code by solving the complete inlet flow path through the swirl vanes and the combustor. The geometry considered is the gaseous configuration of the CORIA lean direct injection combustor, for which detailed measurements are available. The emphasis of the work is placed on the demonstration of the CONVERGE™ applicability to the multi-scale gas turbine engines field and the determination of an optimal mesh strategy through several grid control tools (i.e., local refinement, adaptive mesh refinemen...

International Conference on Liquid Atomization and Spray Systems (ICLASS)
Numerical simulation of injectors could help improving their designs. In particular, a two-phase ... more Numerical simulation of injectors could help improving their designs. In particular, a two-phase flow simulation of a swirl simplex atomizer allows computing the main characteristic parameters such as the spray cone angle, the fuel sheet thickness and the air core diameter. This work describes an attempt to go a step further to characterize atomization and spray characteristics with the ultimate goal to predict the spray distribution in terms of size and velocity. A commercial injector has been used in the CORIA Rouen Spray Burner (CRSB) set up to study turbulent spray combustion. This experiment has produced a well-documented database for the last two TCS workshops (see TCS 6 and 7 at http://www.tcs-workshop.org/). Even though spray measurements are used to define the fuel injection in combustion numerical simulations, the spray injection characteristics remain the main cause of uncertainties. The present work aims at answering this question: Is it possible to complete our knowledge of spray injection by numerical simulation of the full atomization process? The first challenge is to measure the inner geometry. Standards techniques such as X-ray tomography and microscopy have been applied. In order to accurately reproduce the internal throat and swirl chamber, additional measurements have been performed by silicon molding, leading to the definition of a nominal geometry that can be used for further CFD simulation. The second challenge is to produce a mesh regular enough to be compatible with the interface capturing method. Several mesh strategies have been tested starting from the swirl chamber with very thin mesh layers to capture the liquid film at the injector wall and to describe the external liquid sheet. Then, a third challenge concerns the numerical simulation itself, since it must handle the multi-scale nature of such flows until the formation of the spray. A nonreactive condition has been tested with the interFoam solver (OpenFOAM library) in a Large Eddy Simulation (LES) framework. Eventually, the last challenge is to build an analysis to connect the numerical simulation that is limited to the close vicinity of the injector and the experimental measurements that are rejected farther downstream on the dispersed spray. This last step is based on the analysis of the surface curvature distribution that is described with more detail on another presentation at this ICLASS conference.
Uploads
Papers by Mario Belmar-Gil