Papers by Marian Piwowarski
Przeprowadzono analize dla ukladow kogeneracyjnych z mikroturbinami wykorzystującymi cieplo odpad... more Przeprowadzono analize dla ukladow kogeneracyjnych z mikroturbinami wykorzystującymi cieplo odpadowe z silnikow tlokowych. Rozwazono cztery glowne źrodla ciepla odpadowego z silnikow tlokowych: spaliny wylotowe, woda chlodząca silnik, olej smarny i cieplo z systemu turbodaladowania. Obliczenia przeprowadzono dla silnikow General Electric Jerbacher typow: J320 GS-C25 i J416 GS-B05. Uwzgledniono rozne czynniki robocze silowni (zarowno “suche”, jak i “mokre”) oraz rozne cycle termodynamiczne. Nasze badanie wykazaly, ze wykorzystując cieplo odpadowe silnikow, mozna nie tylko podgrzewac wode, ale takze wytwarzac energie elektryczną. W ten sposob mozna podnieśc sprawnośc ogolną wytwarzania energii elektrycznej nawet o 20%.
Energy Conversion and Management, Apr 1, 2023
Advances in Vibration Engineering, 2012
The paper presents the results of experimental investigations into pressure forces generated in a... more The paper presents the results of experimental investigations into pressure forces generated in a turbine labyrinth seal. The experiments were performed on a single-stage air model turbine of the impulse type. The performed experimental research proved that in a shroud clearance the pressure pulsates and the effects of the nozzle trailing edge thickness as well as the influence of the rotor blades are observed. The exemplary results of the investigations are presented in the paper.
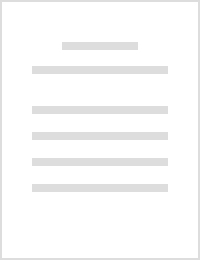
Advances in Vibration Engineering, 2014
In the paper a design of a multi-stage micro-turbine with partial admission of all the stages is ... more In the paper a design of a multi-stage micro-turbine with partial admission of all the stages is described in detail and the results of particular experimental investigations and numerical calculations are shown, followed by conclusions. The co-generative micro-power plant with the HFE7100 as a working medium was designed and built for experimental investigations. The values of the main cycle parameters were as follows:heat output: 20kW; electric output: 3 kW; rotor speed: 8000 rpm–12000 rpm. The micro-turbine experimental stand was designed to enable the measurement of the electric output, rotor speed, medium mass flow rate and the working medium parameters (pressure, temperature) in nearly 40 points located along the turbine and on its circumference. The turbine performance was calculated for HFE7100 but also for air and nitrogen as a working medium for testing purposes. In the first stage of experiments the turbine behavior was checked using these gases and the results were compared with the calculation data. The details, including the strength and deformation of particular turbine elements, are discussed in the paper. The dynamic behavior of the turbogenerator rotor system was also examined. The changes of a turbine inlet pressure and rotor speed in the case of varying turbine power, emergency shutdown and blackout were measured and presented in the paper in differentworking conditions.

Diagnostyka, 2002
Streszczenie Zagadnienia poruszone w pracy dotycz bada eksperymentalnych wymusze aerodynamicznych... more Streszczenie Zagadnienia poruszone w pracy dotycz bada eksperymentalnych wymusze aerodynamicznych generowanych w uszczelnieniach nadbanda owych stopni turbinowych. Referat sk ada si z trzech cz ci. W pierwszej opisano stanowisko powietrznej turbiny modelowej typu tarczowego z cylindrycznymi opatkami, która odwzorowuje typowy stopie cz ci wysokopr nej turbiny parowej oraz omówiono uk ad pomiarowy pozwalaj cy na wyznaczenie rozk adu ci nie w szczelinie nadbanda owej. Przedstawiono wp yw takich parametrów, jak mimo rodowe przemieszczenie osi wirnika wzgl dem osi korpusu, zmiana luzu osiowego i sko ne ustawienie osi wirnika wzgl dem osi korpusu na si y i momenty generowane w uszczelnieniu nadbanda owym. Sprawdzono hipotez , e w przypadku labiryntowego, promieniowego uszczelnienia nadbanda owego decyduj cy wp yw na rozk ad oraz warto ci generowanych si i momentów aerodynamicznych wywiera zmiana luzu promieniowego i sko ne przemieszczenie osi wirnika wzgl dem osi korpusu, a zmiana luzu osiowego odgrywa znacznie mniejsz rol. S owa kluczowe: dynamika wirników, drgania samowzbudne.

Biuletyn Wojskowej Akademii Technicznej, 2012
Streszczenie. w niniejszej pracy przeprowadzono analizę projektową instalacji grzewczej opartej n... more Streszczenie. w niniejszej pracy przeprowadzono analizę projektową instalacji grzewczej opartej na sprężarkowej pompie ciepła. instalacja ta zasila systemy centralnego ogrzewania i przygotowania ciepłej wody użytkowej w jednorodzinnym budynku mieszkalnym znajdującym się w miejscowości koleczkowo. w analizie zawarto ocenę strat i zysków cieplnych budynku, obliczenia zapotrzebowania na moc cieplną analizowanego obiektu oraz koncepcyjne rozwiązania instalacji grzewczej. zaproponowano wariant optymalny ze względu na maksymalną sprawność, do którego dobrane zostały jego główne elementy. Przeanalizowano wpływ grupy wybranych czynników chłodniczych na sprawność oraz parametry pracy zaproponowanej pompy ciepła. Słowa kluczowe: energetyka, instalacja grzewcza, pompa ciepła Analysis of low temperature factors for a heating system in a detached residential building Abstract. This study involves a design analysis of the heating system based on a compression heat pump. This installation supplies central heating and tap water heating systems in a detached residential building situated in koleczkowo. The analysis includes an assessment of heat loss and gain of the building, calculations of the demand for the heating power of the building under analysis and conceptual solutions concerning the heating system. The optimal variant was proposed with regard to its maximum efficiency, for which the main elements were chosen. The effects of the set of selected cooling factors on the efficiency and operating parameters of the proposed heat pump are also analysed.
In the paper a multi-stage micro-turbine with partial admission of all the stages is described in... more In the paper a multi-stage micro-turbine with partial admission of all the stages is described in detail and the results of the numerical calculations and experimental investigations are presented, followed by an appropriate discussion and conclusions.

TASK Quarterly : scientific bulletin of Academic Computer Centre in Gdansk, 2003
Flows in the shroud clearance affect leakage losses and, thus, the turbine stage efficiency. Howe... more Flows in the shroud clearance affect leakage losses and, thus, the turbine stage efficiency. However, at the same time, the distribution of pressure in the seal gaps plays an important role in the generation of the so-called "pressure forces", which may cause self-excited rotor vibrations of the aerodynamic type. Our investigations were carried out in order to show how a CFD code can cope with determining the pressure field in a rotor-blade shroud clearance. Experimental investigations of the pressure field in the shroud clearance were performed on a one-stage air model turbine of the impulse type. Measurements of pressure distribution were carried out for various rotor speeds and turbine loads. 3D calculations of flows in the model turbine were performed using the FLUENT CFD code. The calculations were carried out for the same variants which had been measured experimentally. In this part of the paper, the experimental stand and the numerical methods are described, while a detailed numerical analysis and a comparison between the experimental and the calculated results are presented in parts II and III, respectively.
Advances in Vibration Engineering, 2014

DOAJ (DOAJ: Directory of Open Access Journals), Jul 1, 2003
Experimental and theoretical investigations of the pressure field in the shroud clearance were pe... more Experimental and theoretical investigations of the pressure field in the shroud clearance were performed on a one-stage air model turbine of the impulse type. Measurements of pressure distribution were carried out for various rotor speeds and turbine loads. 3D calculations of flows in this turbine were performed using the FLUENT CFD code. The calculations were carried out for variants which had been measured experimentally. The experimental data have been compared to theoretical results obtained with 3D codes for turbomachinery calculations. The Sliding Mesh and Multiple Reference methods have given very similar results of average values of pressure distribution and the velocity field in the shroud clearance. These results correspond to the experimental data. The pressure pulsations were determined only by the Sliding Mesh method, and these results have also been compared with the experiment. Stage flow calculations carried by the Sliding Mesh method with a structural shroud mesh and with a minimum number of 2-2.5 million cells have given a range of non-stationary pressure pulsations corresponding to the experimental data.

Energies, Aug 19, 2019
The efficiency of a gas turbine can be affected by the use of different biofuels usually with a r... more The efficiency of a gas turbine can be affected by the use of different biofuels usually with a relatively Lower Heating Value (LHV). The paper evaluates the impact of calorific value of fuel on turbine performance and analyzes the possibilities of optimizing turbine construction from the point of view of maximum efficiency for a particular fuel. The several variants of design of small power microturbines dedicated to various biofuels are analyzed. The calculations were carried out for: gas from biomass gasification (LHV = 4.4 MJ/kg), biogas (LHV = 17.5 MJ/kg) and methane (LHV = 50 MJ/kg). It is demonstrated that analyzed solution enables construction of several kW power microturbines that might be used on a local scale. Careful design of such devices allows for achieving high efficiency with appropriate choice of the turbine construction for specific fuel locally available. Such individually created generation systems might be applied in distributed generation systems assuring environmental profits.

Energies, Aug 21, 2020
The efficiencies of the Organic Rankine Cycle (ORC) are not very high and only very seldom do the... more The efficiencies of the Organic Rankine Cycle (ORC) are not very high and only very seldom do they exceed 20%. The increase and optimization of initial parameters and certain modifications of the thermodynamic cycle make it possible to overcome these drawbacks. A new modified cycle has been described and analyzed in detail in the paper. Similarly to the Ericsson cycle for gas turbines, isothermal expansion in the turbine is suggested for the power plant with organic media. The new cycle and the typical ORC power plants have the same block diagram. The only difference is that expansion in the proposed cycle occurs not adiabatically but as an isothermal process. The thermodynamic calculations have been carried out for 11 various fluids and 4 different cycles. The obtained results have clearly shown that cycles with isothermal expansion (isothermal turbines) are characterized by remarkably higher efficiency than typical power plants with adiabatic turbines. The increase in efficiency varies from 6 to 12 percent points for cycles with saturated live vapor and from 4 to 7 percent points for cycles with superheated live vapor. The performed analyses have shown that it is possible to achieve a very high efficiency (over 45%) of organic cycle, which is a very competitive value. In such cases the proposed power plants can achieve an efficiency which is higher than that of modern steam turbine plants with supercritical parameters.
Energies, May 21, 2021
This article is an open access article distributed under the terms and conditions of the Creative... more This article is an open access article distributed under the terms and conditions of the Creative Commons Attribution (CC BY

Energies, Mar 12, 2020
Organic Rankine Cycle (ORC) power plants have become very popular and have found their applicatio... more Organic Rankine Cycle (ORC) power plants have become very popular and have found their applications in systems with renewable sources of energy. So far their overall efficiencies are not very impressive and only for the upper temperature of about 300 • C do they exceed 20%. A drawback of these cycles is the limitation of the cycle upper temperature due to the heat exchanger technology and the materials used. However, it is possible to overcome these difficulties by certain modifications of the thermodynamic cycles, a proper choice of the working medium and the optimization of cycle parameters. In the paper the problems of choosing the working medium and the question of higher temperature at the turbine inlet have been discussed. Different modifications of the schemas of the thermodynamic cycles have also been taken into account. The variants of power plants with regenerators, reheaters and heat exchangers have been considered. The proposed increase in temperature (in some cases up to 600 • C or higher) and innovative modifications of the thermodynamic cycles allow to obtain the power plant efficiency of above 50%. The modified cycles have been described in detail in the paper. The proposed cycles equipped with regenerators and reheaters can have the efficiency even slightly higher than classical steam turbine plants with a reheater and regenerators. Appropriate cycle and turbine calculations have been performed for the micro power plants of turbine output in the range of 10 kW-300 kW (up to several MW in some cases). The best arrangements achieved very high values of the overall cycle efficiency.

Energies, Sep 11, 2019
The use of various biofuels, usually of relatively small Lower Heating Value (LHV), affects the g... more The use of various biofuels, usually of relatively small Lower Heating Value (LHV), affects the gas turbine efficiency. The present paper shows that applying the proposed air bypass system of the combustor at the turbine exit causes tan increase of efficiency of the turbine cycle increased by a few points. This solution appears very promising also in combined gas/steam turbine power plants. The comparison of a turbine set operating according to an open cycle with partial bypassing of external combustion chamber at the turbine exit (a new solution) and, for comparison, a turbine set operating according to an open cycle with a regenerator. The calculations were carried out for different fuels: gas from biomass gasification (LHV = 4.4 MJ/kg), biogas (LHV = 17.5 MJ/kg) and methane (LHV = 50 MJ/kg). It is demonstrated that analyzed solution enables construction of several kW power microturbines that might be used on a local scale. Such turbines, operated by prosumer's type of organizations may change the efficiency of electricity generation on a country-wide scale evidently contributing to the sustainability of power generation, as well as the economy as a whole.
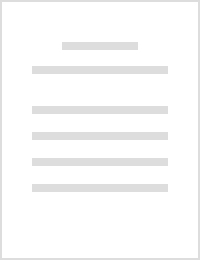
ABSTRACT The experimental investigations into the pressure field in the shroud clearance were per... more ABSTRACT The experimental investigations into the pressure field in the shroud clearance were performed on a one-stage air model turbine of impulse type. Measurements of pressure distribution were carried out for different rotor eccentricities, different values of axial gap and of rotor-stator misalignment, different rotor speeds and different turbine load. The experimental investigations proved that: a) the pressure in the blade tip clearance is not stationary but it pulsates, b) the effect of nozzle trailing edge can be observed in the blade shroud clearance, c) for a given turbine output, the rotor-stator eccentricity and rotor-stator misalignment appear the most important parameters influencing the pressure distribution in the shroud clearance. Aiming to investigate the pressure pulsation transmission through the leakage flow in the blade shroud clearances, pulsations of different amplitudes and frequencies were excited in the turbine inlet duct and corresponding changes of pressure were measured along the shroud width, followed by appropriate harmonic analysis. The investigations were performed for forced pulsations with frequencies ranging from 1Hz to 8 Hz. In all the examined cases, the frequency of pressure pulsations remained unchanged, while the amplitude of the pulsation decreased gradually along the tip clearance. The frequency of these pressure pulsations in the tip clearance was equal to the frequency of the pressure pulsation at the turbine stage inlet and to the frequency of pressure pulsation at the turbine flow passage’s exit.
ABSTRACT The experimental investigation into pressure field in the shroud clearance and rotor tra... more ABSTRACT The experimental investigation into pressure field in the shroud clearance and rotor trajectory were performed on an one-stage air model turbine of impulse type. Basing on the pressure distribution, the aerodynamic forces and moments were investigated as a function of rotor eccentricity, axial gap, rotor-stator misalignment, rotor speed and turbine load. We obtained the following results: 1. confirmation of the linear correlation between the rotor eccentricity (or rotor-stator misalignment angle) and aerodynamic forces, 2. proof that radial eccentricity influences the average location of the rotor, while the general shape of rotor trajectory remains unchanged, 3. proof that although the axial component of the pressure force is relatively low, the moments exerted by this force should be take into account when total aerodynamic moments are determined.
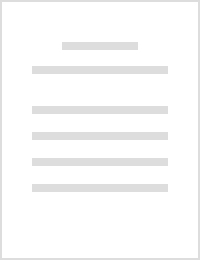
Polish Journal of Environmental Studies, 2014
This article presents basic results of the design analysis of a combined gas-vapour micro power p... more This article presents basic results of the design analysis of a combined gas-vapour micro power plant with a waste-heat boiler without exhaust reheat, working in the vapour section in the organic rankine cycle (ORC) system. The analysis concerned working media most frequently used in those types of power plants and that plan to be used in the future. The object of the analysis was a micro power plant with a 30 kW gas (air) turbine for which the low-boiling medium was selected in such a way as to obtain maximum possible power output of the vapour turbine and, consequently, the highest efficiency of the combined cycle. The analysis also included vapour micro power plants with heat regeneration for so-called dry media and cycles without heat regeneration for so-called wet media. The amount of thermal energy available for utilization in the cogeneration micro power plant at the assumed condenser temperatures equalling 95oC, 55oC, and 30oC, respectively, was assessed. The most favourable medium in terms of the obtained power output and efficiency of the combined cycle was selected and the effect of the low-boiling medium on design parameters of the vapour micro turbine was assessed.
Energies, Mar 25, 2022
Towards Designing an Innovative Industrial Fan: Developing Regression and Neural Models Based on ... more Towards Designing an Innovative Industrial Fan: Developing Regression and Neural Models Based on Remote Mass Measurements.
Uploads
Papers by Marian Piwowarski