Papers by Luis Norberto López Lacalle
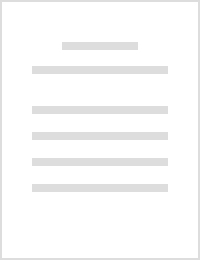
High‐performance IO for seismic processing on the cloud
Concurrency and Computation: Practice and Experience, Feb 26, 2021
SummaryMost of the applications in the seismology field rely on the processing of up to hundreds ... more SummaryMost of the applications in the seismology field rely on the processing of up to hundreds of terabytes of data and their performance is strongly affected by IO operations. In this article, we analyze the main file structures currently used to store seismic data and propose a new intermediate data structure to improve IO performance while still complying with established standards. We show that, throughout a common workflow in seismic data analysis, our IO performance gain greatly surpasses the overhead of translating data to the intermediate structure. This approach enables a speedup of up to 208 times in reading time when using classical standards (e.g., SEG‐Y) and our intermediate structure is up to 1.8 times more efficient than modern formats (e.g., ASDF). Considering cache‐friendly applications, our speedups over the direct use of SEG‐Y reach 8000 times. We also performed a cost analysis on the AWS cloud showing that, in our approach, HDDs can be 1.25 times more cost‐effective than SSDs.
Machining of large dies based on the prediction of the press/die deformation
Intelligent Production Machines and Systems, 2006
In this work a methodological scheme for a reduction of both the try-out and lead-time of complex... more In this work a methodological scheme for a reduction of both the try-out and lead-time of complex dies is presented. The finite element simulation of the tool behaviour along the stamping process results in criteria for the best design of high-cost dies/punches. Using it, modifications of the main geometry, components and functional parameters are recommended. Examples are deeply explained as experimental evidences.
Machining of large dies based on the prediction of the press/die deformation
In this work a methodological scheme for a reduction of both the try-out and lead-time of complex... more In this work a methodological scheme for a reduction of both the try-out and lead-time of complex dies is presented. The finite element simulation of the tool behaviour along the stamping process results in criteria for the best design of high-cost dies/punches. Using it, modifications of the main geometry, components and functional parameters are recommended. Examples are deeply explained as experimental evidences.
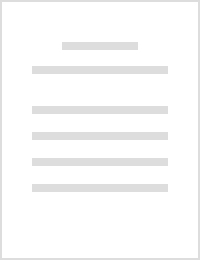
Wear of Form Taps in Threading of Steel Cold Forged Parts
Journal of Manufacturing Science and Engineering, 2015
Tapping of blind or through holes is a common operation in several applications in the automotive... more Tapping of blind or through holes is a common operation in several applications in the automotive, windmill towers, general machinery, and other industrial sectors. On the other hand, tapping is usually performed at the final manufacturing stage of components, so operation errors can lead to very expensive scraps. This article focuses on the performance of different forming taps since there are no standardized procedures for evaluating form tapping, beyond the mere visual assessment or go/no-go tests. Tool behavior was studied according to four aspects: (a) wear analysis of tap forming lobes, (b) measurement of thrust force and torque during tapping, (c) metallographic study of threads, and finally (d) evaluation of coating and tap geometry. In the work presented here, tap wear and thread quality are correlated with processes monitoring parameters. A useful conclusion for tap manufacturers is that taps with hexagonal section and 5 pitches in the chamfer zone led to lower thrust forc...
Etude expérimentale et modélisation de l’usure des outils lors du perçage et du détourage de CFRP
Revue des composites et des matériaux avancés, 2013
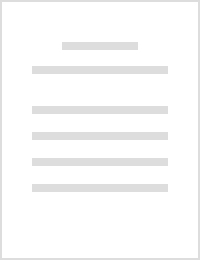
Drilling of Intermetallic Alloys Gamma Tial
AIP Conference Proceedings, 2011
ABSTRACT Due to their high strength/weight ratio and resistance to corrosion and wear, superalloy... more ABSTRACT Due to their high strength/weight ratio and resistance to corrosion and wear, superalloys such as gamma TiAl or Inconel 718 appear as the best choice for the high mechanical/thermal demands in the vicinity of the combustion chamber of aircraft engines. There are assembled parts such as cases, disks or blisks; in the manufacturing of these components the last drilling operation could jeopardize the full work integrity adding new costs to the just very expensive parts. Therefore drilling is a high-added value step in the complete sequence. The present work is framed within the study of hole making in advanced materials used for lightweight applications in aerospace sector. Within this context, the paper presents the results from milling tests on three types of gamma TiAl alloys (extruded MoCuSi, ingot MoCuSi and TNB) to define an optimal set of cutting parameters, which will contribute to open the increase in use of these special alloys. Drilling tools made of integral hard metal were used, applying different feeds and cutting speeds. The influence of cutting speed and feed is discussed.
Burnishing of rotatory parts to improve surface quality
In this paper, the use of rolling burnishing process to improve the final quality of railway and ... more In this paper, the use of rolling burnishing process to improve the final quality of railway and automotive workpieces is studied. The results are focused on the improvement of the manufacturing processes of rotary workpieces used in railway and automotion industry, attending to generic target of achieving `maximum surface quality with minimal process time'. Burnishing is a finishing operation in

International Journal of Machine Tools and Manufacture, 2009
Chatter vibration problems arise during machining. This paper aims to produce a strategy that can... more Chatter vibration problems arise during machining. This paper aims to produce a strategy that can detect the emergence of chatter so that subsequently, in accordance with the lobe on the stability diagram where the process is located, the proper strategy may be determined, either by taking the machine to a stable spindle speed or causing continuous variation in spindle speed. The effectiveness of this strategy is contrasted for a number of different cases, using both simulation and experimental testing. The context targeted by the strategy is a high-speed mill roughing operation for cases of vibration arising on the headstock/cutting tool unit, when high material removal rates (MRR) must be maintained. Industrial implementation of the strategy and the chatter detection and diagnosis algorithm is carried out using a portable digital assistant (PDA).
The International Journal of Advanced Manufacturing Technology, 2007
In this work a methodological scheme for a reduction of both the try-out and lead-time of complex... more In this work a methodological scheme for a reduction of both the try-out and lead-time of complex dies is presented. The finite element simulation of the system press/tool behaviour along the stamping process results in criteria for the best design of high-cost dies/punches. Modifications of the main geometry, components and functional parameters are so recommended. Die deflection during the pressing process is in this work investigated. With the proposed methodology die manufacturers are able to avoid errors coming from die deformation due to their asymmetrical shape. At the same time, time of manual adjustment and polishing is reduced in a 30%. Examples are deeply explained as well as experimental evidences.
Modelo de elementos finitos del bruñido
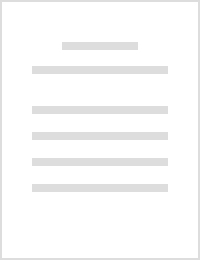
Five-Axis Machining and Burnishing of Complex Parts for the Improvement of Surface Roughness
Materials and Manufacturing Processes, 2011
In this paper the ball burnishing is applied on sculptured surfaces, aiming at enhance surface ro... more In this paper the ball burnishing is applied on sculptured surfaces, aiming at enhance surface roughness. Different strategies are possible for burnishing, the continuous burnishing (CB) which uses a 5-axis interpolation of the machine tool, and the patch burnishing (PB) using a more simple 3 + 2 axis interpolation. Using both techniques complex parts are burnished and a big improvement in surface roughness achieved, but some differences between both approaches appear.Two parts have been previously machined in a five-axis milling centre, and finished using the ball burnishing approaches. The first one is a steel AISI 1045 with a hemisphere shape, which geometry is simple. The second one is a steel DIN 1.2379 part (64 HRC), with more complex features. Surface quality was evaluated for both burnishing approaches, obtaining significant improvements on surface roughness and hardness. The main general conclusion is that ball burnishing reduces roughness without penalizing the manufacturing time or surface integrity, and therefore is suitable for complex surfaces.

EKAIA Euskal Herriko Unibertsitateko Zientzia eta Teknologia Aldizkaria
Sektore aeronautikoan erabiltzen diren super-aleazio termorresistenteak lantzea erronka zaila da,... more Sektore aeronautikoan erabiltzen diren super-aleazio termorresistenteak lantzea erronka zaila da, ebaketa erremintak azkar higatzen baititu. Horregatik, erreminta horien errendimendua hobetzeko, fabrikatzaileek, ebaketa geometriaren eragina ulertzea funtsezkoa dela uste dute. Hori dela eta, artikulu honetan erremintaren ebaketa sorbatzeko erradioak eta jaulkitze- zein azpijan-angeluek daukaten eragina aztertzen da. Abiapuntu gisa, diseinu esperimental (DOE) bat burutu da, non aurrean aipatutako hiru parametroen eragina kuantifikatzen den, Elementu Finituen Metodoaren (EF) bitartez. Ondoren, proba esperimentalekin ekin da, EF softwaretik lortutako emaitza teorikoak balioztatzeko. Emaitzek erakusten dute ebaketa sorbatzaren erradioak erremintaren higaduran eragin zuzena daukala eta balio egokia aukeratuz erremintaren bizitza erabilgarria areagotzeko gai dela.
On the relationship between cutting forces and anisotropy features in the milling of LPBF Inconel 718 for near net shape parts
International Journal of Machine Tools and Manufacture

Applied Sciences
In this work, a new method for solving a delay differential equation (DDE) with multiple delays i... more In this work, a new method for solving a delay differential equation (DDE) with multiple delays is presented by using second- and third-order polynomials to approximate the delayed terms using the enhanced homotopy perturbation method (EMHPM). To study the proposed method performance in terms of convergency and computational cost in comparison with the first-order EMHPM, semi-discretization and full-discretization methods, a delay differential equation that model the cutting milling operation process was used. To further assess the accuracy of the proposed method, a milling process with a multivariable cutter is examined in order to find the stability boundaries. Then, theoretical predictions are computed from the corresponding DDE finding uncharted stable zones at high axial depths of cut. Time-domain simulations based on continuous wavelet transform (CWT) scalograms, power spectral density (PSD) charts and Poincaré maps (PM) were employed to validate the stability lobes found by u...

Metals
Any manufacturing equipment designed from scratch requires a detailed follow-up of the performanc... more Any manufacturing equipment designed from scratch requires a detailed follow-up of the performance for the first units placed in service during the production ramp-up, so that lessons learned are immediately implemented in next deliveries and running equipment is accordingly updated. Component failure analysis is one of the most valuable sources of improvement among these lessons. In this context, a failure-assessment based design revision of the conveying system of a newly developed press hardening furnace is presented. The proposed method starts with a forensic metallurgical analysis of the failed components, followed by an investigation of the working conditions to ensure they match the forensic observations. The results of this approach evidenced an initially unforeseen thermo-mechanical damage produced by a combination of thermal distortions, material ageing, and mechanical fatigue. Once the cause–effect relationship for the failure is backed up by evidence, an improved design ...

Metals
The present work focuses on the manufacturing of Ti-6Al-4V parts using hot single point increment... more The present work focuses on the manufacturing of Ti-6Al-4V parts using hot single point incremental forming (SPIF), a non-conventional forming technology mainly oriented toward the fabrication of prototypes, spare parts, or very low volume series. In the used procedure, the entire sheet is heated and kept at uniform temperature while the tool incrementally forms the part, with the limited accuracy of the obtained parts being the major drawback of the process. Thus, this work proposes two approaches to improve the geometric accuracy of Ti-6Al-4V SPIF parts: (i) correct the tool path by applying an intelligent process model (IPM) that counteracts deviations associated with the springback, and (ii) skip overforming deviations associated with the deflection of the sheet along the perimeter of the part based on a design improvement. For this purpose, a generic asymmetric design that incorporates features of a typical aerospace Ti-6Al-4V part is used. The results point out the potential o...

International Journal of Precision Engineering and Manufacturing-Green Technology
The present work focuses on a new approach to hot form hard-to-work materials by Single Point Inc... more The present work focuses on a new approach to hot form hard-to-work materials by Single Point Incremental Forming (SPIF) technology using a global heating of the sheet. A set of trials was carried out in order to identify the optimum temperature cycles to minimize geometric distortions associated to each process stage on the fabrication of parts made of Ti-6Al-4V. On the one hand, heating trials allowed defining the optimal procedure to improve the temperature distribution homogeneity along the sheet and consequently to minimize its thermal distortion previous to the forming stage. On the other hand, the influence of both working temperature and the applied cooling on the geometric accuracy was evaluated by means of SPIF trials. For this purpose, a generic asymmetric design with typical aeronautical features was used. These trials pointed out that high forming temperatures allow reducing significantly the material springback whereas a controlled cooling (with an intermediate stress relief treatment) minimizes both the distortion of the part during the cooling and the mechanical stresses accumulated on the clamping system. Furthermore, the work includes a post-forming material evaluation to determinate the influence of the employed processing conditions on microcracks, alpha-case layer, microstructure and hardness.

International Journal of Precision Engineering and Manufacturing-Green Technology
Nowadays, the need for not only technically but also environmentally efficient machining processe... more Nowadays, the need for not only technically but also environmentally efficient machining processes is increasing. In this context, the reduction of oil emulsion type coolants used during machining of aeronautical engine components supposes a great challenge. In this paper, a novel approach based on the design, optimization and validation of a nozzle adaptor combining cryogenic technology and minimum quantity lubrication systems is proposed. The proposed work also deals with the aim of obtaining a cost-effective process. Thus, CO 2 flow and velocity was optimized in this line. Theoretically-based analysis were performed and compared with computational fluid dynamics (CFD) simulations and with real experimental tests as well. Once optimizing these key factors, two nozzle adaptors were designed and simulated by CFD. Different geometries were tested looking for the most efficient design. Finally, to obtain a feasible industrial product, the developed nozzle was tested as a CryoMQL demonstrator comparing with other lubricoolant techniques during milling Inconel 718. Results show a successful balance between technical and environmental issues using this technology when milling aeronautical alloys.
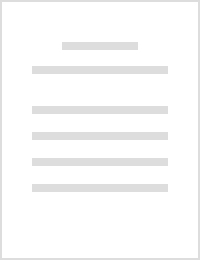
Aeronautics Advanced Manufacturing Center, the Bet to Surpass the Valley of Death between University and Company
Materials Science Forum
The present times are changing and need new formulas that satisfy the need for effective transfer... more The present times are changing and need new formulas that satisfy the need for effective transfer between universities and companies. In the Basque Country, attending to this demand the Aeronautics Advanced Manufacturing Center (CFAA) has been founded. This center belongs to the University of the Basque Country (UPV/EHU) and has several companies related to this strategic sector as partners. The CFAA, equipped with the latest machinery and technology, born to be a catalyst for research activity in the field of advanced manufacturing for aeronautical sector, focusing its activity on the called Pillar 2 of the MRL scale (Manufacturing Readiness Level) as the proximity to the final application. Belonging to the UPV/EHU, this center allows stays of doctoral students, students for performing their master and bachelor’s degree projects. This implies a high quality training, and closer to reality, in manufacturing technologies.
A cryo lubri-coolant approach for finish milling of aeronautical hard-to-cut materials
International Journal of Mechatronics and Manufacturing Systems, 2016
Uploads
Papers by Luis Norberto López Lacalle