Papers by Kjell Mattiasson

AIP Conference Proceedings, 2005
This paper summarizes and presents the most important results from a research project on FE simul... more This paper summarizes and presents the most important results from a research project on FE simulation of hemming carried out at Volvo Cars Body Components and Chalmers University of Technology. In the automotive industry, hemming is used to join two sheet metal panels by bending the flange of the outer panel over the inner one. The final goal of the project was to simulate all of the hemming steps of production parts. In order to make threedimensional simulations of hemming possible within reasonable simulation times, it is necessary to use shell elements and not solid elements. On the other hand, the radius of curvature of the outer part in the folded area is very small, normally of the same order of magnitude as the sheet thickness. This fact raises the question if shell elements are applicable in FE simulation of hemming. One part of the project was therefore a thorough investigation of the order of magnitude of the errors resulting from the use of shell elements in FE simulation of hemming. Another part of the project was devoted to three-dimensional simulations of the hemming of an automotive hood. The influence on the rollin from several parameters, such as shell element formulation, adhesives, and anisotropy was studied. Finally, results from a forming simulation were also mapped to the flanging and hemming models in order to study the influence from the stamping of the outer panel on the roll-in.
Engineering With Computers, 2010
The cyclic three-point bending test has been frequently used for the determination of material ha... more The cyclic three-point bending test has been frequently used for the determination of material hardening parameters. The advantage of this test is that it is simple to perform, and standard test equipment can be used. The disadvantage is that the material parameter identification requires some kind of inverse approach. The current authors have previously, successfully been utilizing a method, in
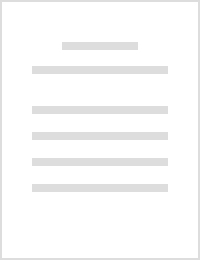
AIP Conference Proceedings, 2007
ABSTRACT The current report presents some results from a study on the prediction of necking failu... more ABSTRACT The current report presents some results from a study on the prediction of necking failure in ductile metal sheets. In particular methods for creating Forming Limit Curves (FLCs) are discussed in the present report. Three groups of methods are treated: Experimental methods, Theoretical/analytical methods, and the Finite Element Method (FEM). The various methods are applied to two different materials: An aluminum alloy and a high strength steel. These materials do both exhibit a distinct necking behavior before fracture, and they do both exhibit only a small strain rate dependence. As can be expected, the resulting FLCs from the various experimental, theoretical, and numerical methods show a substantial scatter. The reasons for these deviating results are analyzed, and some conclusions are drawn regarding the applicability of the different methods.
Engineering Computations, 1996
Argues that the dynamic-explicit approach has in recent years been successfully applied to the so... more Argues that the dynamic-explicit approach has in recent years been successfully applied to the solution of various quasi-static, elastic-plastic problems, especially in the metal forming area. A condition for the success has, however, been that the problems have been displacement-driven. The solution of similar force-driven problems, using this approach, has been shown to be much more complicated and computationally time
Computers and Structures, 1989
A Boundary Element Method is developed for the solution of large strain problems. Betti's recipro... more A Boundary Element Method is developed for the solution of large strain problems. Betti's reciprocal theorem relevant to an Updated Lagrangian formulation is established as the basis for the boundary element formulation. Fully implicit integration of the constitutive relations leads to a nonlinear virtual work equation in each increment, which is solved by iteration. In each such equilibrium equation the elastic operator is isolated, and so the Boundary Element Method can be conveniently used. A system of equations is solved with all nonlinear terms assembled on the right hand side. A numerical example shows application to the stretching of a metal sheet. Elastic and plastic cross-anisotropy (the stressed plane is isotropic) and complete incompressibility are assumed. Hill's yield criterion is adopted together with isotropic hardening.

International Journal For Material Forming, May 28, 2009
The importance of an accurate material modeling for the accuracy and reliability of sheet forming... more The importance of an accurate material modeling for the accuracy and reliability of sheet forming simulations has become increasingly evident during the last years. More advanced material models have, however, to be supported by novel methods for material characterization. The recent eight parameter yield functions Yld2000-2d and BBC2003 demand, besides data from the ordinary uniaxial tensile tests, also equibiaxial data. In the present paper a Viscous Pressure Bulge (VPB) test is described. The test yields the equibiaxial stress point and r-value, as well as a plastic hardening curve for large values of plastic strain. The test setup is based on an ARGUSS™ optical measuring system, and provides the desired result data in a very smooth and easy way. In order to verify the results from the current test, comparisons have been made with compression tests performed at Corus RD&T and hydraulic bulging tests performed at RWTH in Aachen. A discussion on how to determine the equibiaxial yield stress and how to transform the biaxial stress-strain curve to an effective stress-strain curve is included in the paper.
Journal of Materials Processing Technology, 1994
Proceedings of Numisheet 2008 Editor Pavel Hora, 2008
Uploads
Papers by Kjell Mattiasson