Papers by Staffan Jacobson

Surface & Coatings Technology, Oct 1, 2013
W-S-N films were deposited by reactive magnetron sputtering from WS2 target in Ar/N2 atmosphere. ... more W-S-N films were deposited by reactive magnetron sputtering from WS2 target in Ar/N2 atmosphere. Besides the standard evaluation of composition, structure, morphology, hardness and cohesion/adhesion, the core objective of this paper was to analyze coating tribological behavior. The chemical composition was 34 at.% N, 12 at.% O, 29 at.% W and 25 at.% S and the as-deposited films were completely amorphous. The film thickness was 2.3 µm including the approximately 300 nm thick adhesion improving titanium interlayer. The friction coefficient was lower than 0.003 when sliding in dry nitrogen. The coating showed remarkable wear resistance surviving more than 2 million laps on pin-on-dics. The excellent friction properties were attributed to the formation of a thin tungsten disulfide tribofilm on the top of the wear track of the coating and on the counterpart surface. Moreover, the coating showed ability to replenish damaged areas with solid lubricant. We demonstrated that a
Wiley-VCH Verlag GmbH eBooks, Dec 27, 2007
The Importance of Tool Surface Roughness on the Galling Tendencies in Cold Forming of Aluminium
The Role of Surface Treatment in the Tribofilm Formation on Alumina Friction Drive Components
Influence of hardness and microstructure on the mechanisms of deformation and wear of cemented ca... more Influence of hardness and microstructure on the mechanisms of deformation and wear of cemented carbides for rock drilling

Wear, Dec 1, 2020
Cemented carbide tools are successfully used to shear Cu alloy wire into zipper elements in the z... more Cemented carbide tools are successfully used to shear Cu alloy wire into zipper elements in the zipper industry. However, wear of the tools is the limiting factor for the production rate and the industry would benefit from more wear resistant tools. Previous investigations have indicated that the wear is tribochemical, and to investigate the role of Zn in commonly used Cu alloy testing is repeated against pure Cu in this work. The tool material used is a cemented carbide, in uncoated, CrC coated and CrN coated versions. The tests are performed in a simplified sliding test rig, combined with intermittent scanning electron microscopy (SEM) and energy dispersive X-ray spectroscopy (EDS) analysis. The tools are gradually worn and Cu is adhered and transferred to all tool surfaces. This process results in a pattern consisting of ridges and valleys on uncoated cemented carbide and CrC. Both are worn significantly faster than CrN, where much of the original surface roughness still remains after the full test. These worn surfaces are similar to the corresponding surfaces worn against the previously tested Cu-Zn alloy. However, the wear rate is dramatically higher in the pure Cu tests.

Tribology Letters, Apr 3, 2012
Cold forging is a group of methods effectively used in a number of industrial applications to for... more Cold forging is a group of methods effectively used in a number of industrial applications to form aluminium. Tool life and complexity of the possible shapes are mainly restricted by galling; the uneven tool surfaces caused by lumps of transferred material lead to surface damage on successive parts formed and/or problems in successive forming operations, and high stresses occurring when forming complex shapes. Earlier investigations have shown that improved surface roughness of an uncoated steel tool decreases the amount of adhered aluminium on the tool, but does not decrease the friction in the long run. Testing has also shown that when using conventional forming tools it is very important to have sufficient lubrication to avoid galling. Addition of an optimized lowfriction PVD-coating decreases the galling tendency and increases the tolerance to insufficient lubrication and lubricant film breakthrough, as long as the coating surface is smooth, whilst other similar coatings have little or no effect. The present article further investigates the mechanism behind the transfer of aluminium to the coatings. All coatings were found to be intact after testing, and so the differences were concluded to lie in the chemical properties of the coating and, if these are favourable, then in surface roughness on the micro scale.

Wear, Apr 1, 2017
In field tests, a boric acid based fuel additive has led to reduced fuel consumption. The reducti... more In field tests, a boric acid based fuel additive has led to reduced fuel consumption. The reduction was substantial, an average of 6 and 10% in passenger cars and diesel generators respectively. Aiming towards improved understanding of mechanisms behind the fuel saving, three methods to mimic the effect of the additive in the piston-ring/cylinder contact have been evaluated. A reciprocating cylinder/flat configuration with ball bearing steel against grey cast iron was used, and it was lubricated with base oil. The different methods were as following: A) repeated spraying of a small amount of the boric acid solution onto the surfaces, B) predeposition of a boric acid layer on the flat surface and C) a combination of method A) and B). The three methods all showed effects of the additive, spanning from about 20% to 50% reductions (in the latter case, from roughly 0.1 to 0.05 in coefficient of friction averaged over the stroke). The greatest potential of the additive was seen with local coefficient of frictions lower than 0.020 in tests at room temperature with Method C. This means a reduction of around 75% compared to the lowest levels measured for the reference tests run without the additive. The most stable friction test was Method A, where a small amount of boric acid solution was repeatedly sprayed onto the lubricated sliding surfaces. In this type of test, friction reductions of roughly 20% and 40% were found at 100 °C and room temperature respectively. The tribological and chemical mechanisms of boric acid in this test configuration are yet not fully understood and more studies are needed. However, the observed poor stability of the tribofilms containing boron and oxygen complicates such activities.

Wear, May 1, 2008
Traditional preparation of metallographic cross sections by cutting, polishing and etching has a ... more Traditional preparation of metallographic cross sections by cutting, polishing and etching has a long and successful history of revealing grain sizes, phase composition, gradients, etc. However, the technique is limited with respect to precision in the positioning of the cross section, and it also tends to inadvertently remove brittle constituents and conceal cracks and small details close to ductile phases, that may become smeared out by the polishing. The present paper presents an alternative cross sectioning technique for worn surfaces, developed to automatically reveal weak zones in the surface layer of a material, without the need of precise positioning, and also avoiding inadvertent removal of brittle phases. The technique is applicable to materials that exhibit brittle fracture, and is normally used for characterisation of unworn materials. It is primarily intended for studies in the SEM, since the cross sections produced typically exhibit too coarse topography to be sharply pictured in the light optical microscope. The simple and rapid preparation technique is described and examples from worn cemented carbide rock drills and hot rolls are presented to illustrate some of the capabilities of the technique.
Wear, Sep 1, 1998
The wear volume and wear distribution of chromium steel cam rollers in a high-torque hydraulic mo... more The wear volume and wear distribution of chromium steel cam rollers in a high-torque hydraulic motor has been investigated. The cam roller is a part of a novel silicon nitride/chromium steel journal bearing system. An atomic force microscope (AFM) was used to obtain topographical images of the cam roller surfaces before and after use in a full-scale test of the

International Journal of Refractory Metals & Hard Materials, Dec 1, 2018
Cemented carbide is a composite material, most commonly consisting of tungsten carbide grains in ... more Cemented carbide is a composite material, most commonly consisting of tungsten carbide grains in a metallic matrix of cobalt. The combination of a hard ceramic phase in a ductile metallic matrix combines high hardness and ability to withstand plastic deformation with toughness to avoid cracking and fracturing. Since these properties are very important in rock drilling, cemented carbides are frequently used in such applications. In earlier work, it was found that granite in sliding contact with considerably harder cemented carbides not only results in plastic deformation of the cemented carbide composite, but also in plastic deformation of some of the individual WC grains. The latter observation is remarkable, since even the two hardest granite constituents (quartz and feldspar) are significantly softer than the WC grains. This tendency to plastic deformation of the WC grains was found to increase with increasing WC grain size. The present investigation aims to increase the understanding of plastic deformation of cemented carbides in general, and the individual WC grains in particular, in a situation representative for the rock drilling application. The emphasis is put on explaining the seemingly paradoxical fact that a nominally softer counter material is able to plastically deform a harder constituent in a composite material. The experimental work is based on a scratch test set-up, where a rock crystal tip slides against a fine polished cemented carbide surface under well-controlled contact conditions. The deformation and wear mechanisms of the cemented carbide are evaluated on the sub-micrometer scale; using high resolution FEG-SEM, EDS, EBSD, BIB and FIB crosssectioning. The size of the Co-pockets, together with the shape and size of WC grains, turned out to be decisive factors in determining the degree of carbide deformation. The results are discussed with respect to their industrial importance, including rock drilling.
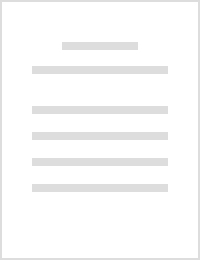
Tribology transactions, Oct 28, 2014
ABSTRACT It has been shown many times that cosputtering low-friction coatings of molybdenum disul... more ABSTRACT It has been shown many times that cosputtering low-friction coatings of molybdenum disulfide (MoS2) and tungsten disulfide (WS2) with other elements can improve the structural, mechanical, and tribological properties. To achieve the lowest friction, MoS2 or WS2 should be doped with element(s) improving the hardness and density of the coatings. On the other hand, such elements, or their compounds, should not be present in the outermost molecular layers at the sliding interface. This article suggests that there are important differences between how MoS2 and WS2 coatings respond to or react with doping elements, despite the almost identical structure and behavior of the undoped materials. Two systems have been investigated by high-resolution transmission electron microscopy (HRTEM) and scanning TEM (STEM) electron energy loss spectroscopy (EELS), W-S-C-Cr and W-S-C-Ti, and showed significant amounts of oxides, which typically formed a layer just underneath the crystalline WS2 top layer. Further, carbon was almost completely absent in the tribofilms, despite the fact that the as-deposited coatings contained as much as 40–50 at% C. An interesting observation here is that WS2 basal planes surround or embed Fe wear particles, suggesting a relatively strong adhesion or a Fe-S chemical bonding between iron/steel and WS2. The result of this is that the wear particles become pacified and remain in the contact as low-friction material.
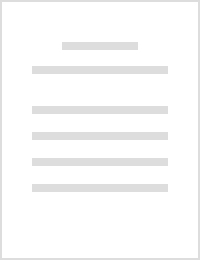
Wear, 2021
Abstract Two types of thickener systems, lithium complex (LiX) and polypropylene (PP), were chose... more Abstract Two types of thickener systems, lithium complex (LiX) and polypropylene (PP), were chosen to evaluate graphite, graphene oxide (GO) and reduced graphene oxide (rGO) as grease additives at a concentration of 0.1 wt%. To enhance the additive dispersibility, a mixture of polyalphaolefin oil (PAO) and oil soluble synthetic polyalkylene glycol (OSP-68) was used as base oil. The greases were evaluated in i) silver-coated copper contacts simulating high-load electrical contact applications subjected to fretting and ii) a steel/steel 4-ball wear test equipment. The additives showed no positive effect on friction and wear, neither in fretting nor in 4-ball tests. However, there is a statistically significant difference in wear scar diameter on the 4-ball steel contacts between the two thickener types, LiX and PP. Thus, the PP-grease lubricated steel contacts showed more wear and more tribofilms of iron oxide and grease constituents, indicating more metal-to-metal contact. Hence, the thickener type has a larger impact on the lubricating performance of the grease than do the graphite, GO and rGO additions. The results demonstrate that the addition of graphene-based materials to improve greases is not straightforward. Rather, the grease/graphene-based additive system is complex and many parameters influence the friction and wear results. Hence, more work is needed to obtain a better understanding and possibly better lubricating effects from the graphene-based additives.
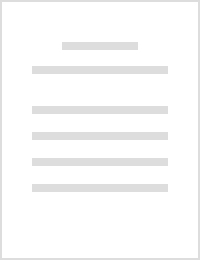
Recent developments in thin film synthesis of diamond have facilitated a host of new technical ap... more Recent developments in thin film synthesis of diamond have facilitated a host of new technical applications. These are motivated by the many attractive properties of diamond, for example high hardness, chemical inertness, transparency and heat conductivity. Unfortunately, these properties also make it difficult to fashion complex geometries. Other problems are the severely limited choice of suitable substrate materials and large surface roughness. To reduce these complications, a technology denoted replication and bodybuilding has been developed. The basic principle is to grow the diamond film onto a mold and then build a mechanical support on top of the diamond film. Then the mold is removed. Thereby, a diamond surface with the desired 3D geometry and the same surface roughness as the mold is created.Three potential applications for devices built using the replication and bodybuilding concept have been explored. Grinding tools for hard materials have proved superior to conventional technology in rate of removal as well as in resulting surface finish. Diamond surfaces have also been crafted into ultra-durable dies for injection molding of hard particle reinforced polymers. Initial testing of an abrasive diamond device, intended to make CMP processes more economical and easier to control has successfully been carried out.Diamond and diamond-like carbon is well-known for being “low-friction materials”, but are here demonstrated to actually be “high-friction materials” with the ability to disguise themselves in certain environments, most notably with the aid of water molecules. The mechanisms involved in these variations have been investigated. Using NEXAFS it is shown that high friction sliding is accompanied by changes in the material structure. These changes are induced by surface roughness as well as by strong adhesive forces.Highly hydrogenated carbon coatings, on the other hand, affording super-low friction coefficients (<0.01) under certain circumstances, will suffer an increase in friction in the presence of water.
Uploads
Papers by Staffan Jacobson