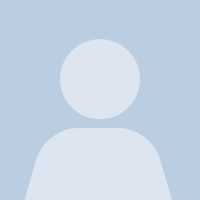
J. Galván
PhD in Chemistry. Senior Reseach Scientist at CSIC
less
Related Authors
James Marrow
University of Oxford
Nicole Herbots
Arizona State University
Joseph Buhagiar
University of Malta
Petra Reinke
University of Virginia
Saeed Farahany
Buein Zahra Technical University
Irina Kolesnik
Moscow State University
Juan Carlos Galvan
CSIC (Consejo Superior de Investigaciones Científicas-Spanish National Research Council)
Saviour Umoren
University of Uyo, Uyo, Nigeria
Maderas. Ciencia y Tecnologia
Universidad del Bio-bio
OLUYEMI DARAMOLA, PhD
Federal University of Technology Akure
InterestsView All (13)
Uploads
Papers by J. Galván
This paper studies the possible dependence of corrosion performance on surface
conditions for Mg alloy specimens in 0.6 M NaCl solution. EIS measurements are used
to compare the corrosion resistance of surfaces immediately after polishing, after
months of ageing in air exposure, and in the as-received condition. Considering the
evolution of the capacitive arc diameter of the Nyquist diagram, the surface conditions
are seen to have an effect only in the early stages of testing. Other notable features
include a marked tendency of the capacitive arc to decrease with immersion time in the
case of the AZ61 alloy; a moderate tendency of this arc size to increase from the start
of the test with the AZ31 alloy, and the evolution of the capacitive arcs towards
practically steady state sizes with immersion time in the case of both alloys. These
results seem to be caused by the offsetting of two opposing factors: the blocking of
pores in the air-formed film by corrosion products, and the attack and/or transformation
of the film by the saline solution. Stabilisation of the arc size by extending the
immersion time reflects the attainment of a dynamic balance between corrosion and
continuous film reconstruction processes.
the chemical composition, structure and thickness of the thin native oxide film
formed spontaneously in contact with the laboratory atmosphere on the surface
of freshly polished commercial AZ31 and AZ61 alloys with a view to furthering
the understanding of protection mechanisms. For comparative purposes, and to
more fully describe the behaviour of the native oxide film, the external oxide
films formed as a result of the manufacturing process (as-received condition)
have been characterised. The technique applied in this research to study the
thin oxide films (thickness of just a few nanometres) present on the surface of
the alloys has basically been XPS (X-ray photoelectron spectroscopy) in
combination with ion sputtering. Corrosion properties of the alloys were studied
2
in 0.6M NaCl by measuring charge transfer resistance values, which are
deduced from EIS (electrochemical impedance spectroscopy) measurements
after 1 hour of exposure. Alloy AZ61 generally showed better corrosion
resistance than AZ31, and the freshly polished alloys showed better corrosion
resistance than the alloys in as-received condition. This is attributed to a
combination of (1) higher thickness of the native oxide film on the AZ61 alloy
and (2) greater uniformity of the oxide film in the polished condition. The
formation of an additional oxide layer composed by a mixture of spinel
(MgAl2O4) and MgO seems to diminish the protective properties of the passive
layer on the surface of the alloys in as-received condition.
Keywords: Magnesium alloys, native oxide film; chemistry and s
This paper studies the corrosion rate of magnesium alloys AZ31 and AZ61 exposed in
humid air under continuous condensation conditions. The approximately parabolic
shape of the corrosion progress curves suggests that the process is controlled by
factors related with the corrosion product layer growing on the metallic surface.
Complementary EIS measurements provide evidence of the restriction of surface
activity by the accumulation of corrosion products. According to gravimetric results
there is an initial period in which only a small part of the corroded metal is incorporated
in the corrosion product layer, but after longer testing times the proportion of metal that
comes to form part of this layer tends to increase very significantly
AZ31 and AZ61 magnesium alloy substrates with different surface finish, the chemistry of
the outer surface of the conversion coatings that grows after their subsequent immersion on
saturated aqueous NaHCO3 solution treatment and the enhancement of corrosion resistance
have been studied. The significant increase in the amount of aluminum and carbonate
compounds on the surface of the conversion coating formed on the AZ61 substrate in
polished condition seems to improve the corrosion resistance in low chloride ion
concentration solutions. In contrast, the conversion coatings formed on the AZ31 substrates
in polished condition has little effect on their protective properties compared to the
respective as-received surface.
oxide surface layers induced by heating in air at 200ºC for time intervals from 5
minutes up to 60 minutes on commercial AZ31 and AZ61 magnesium alloys
with a view to a better understanding of their protective properties. A strong link
was found between the aluminium enrichment observed in the surface of the
oxide layer and the decrease in the protective properties of the heat treated
AZ31 alloy. In contrast, no significant changes have been observed in the case
of the heat treated AZ61 alloy.
This paper studies the possible dependence of corrosion performance on surface
conditions for Mg alloy specimens in 0.6 M NaCl solution. EIS measurements are used
to compare the corrosion resistance of surfaces immediately after polishing, after
months of ageing in air exposure, and in the as-received condition. Considering the
evolution of the capacitive arc diameter of the Nyquist diagram, the surface conditions
are seen to have an effect only in the early stages of testing. Other notable features
include a marked tendency of the capacitive arc to decrease with immersion time in the
case of the AZ61 alloy; a moderate tendency of this arc size to increase from the start
of the test with the AZ31 alloy, and the evolution of the capacitive arcs towards
practically steady state sizes with immersion time in the case of both alloys. These
results seem to be caused by the offsetting of two opposing factors: the blocking of
pores in the air-formed film by corrosion products, and the attack and/or transformation
of the film by the saline solution. Stabilisation of the arc size by extending the
immersion time reflects the attainment of a dynamic balance between corrosion and
continuous film reconstruction processes.
the chemical composition, structure and thickness of the thin native oxide film
formed spontaneously in contact with the laboratory atmosphere on the surface
of freshly polished commercial AZ31 and AZ61 alloys with a view to furthering
the understanding of protection mechanisms. For comparative purposes, and to
more fully describe the behaviour of the native oxide film, the external oxide
films formed as a result of the manufacturing process (as-received condition)
have been characterised. The technique applied in this research to study the
thin oxide films (thickness of just a few nanometres) present on the surface of
the alloys has basically been XPS (X-ray photoelectron spectroscopy) in
combination with ion sputtering. Corrosion properties of the alloys were studied
2
in 0.6M NaCl by measuring charge transfer resistance values, which are
deduced from EIS (electrochemical impedance spectroscopy) measurements
after 1 hour of exposure. Alloy AZ61 generally showed better corrosion
resistance than AZ31, and the freshly polished alloys showed better corrosion
resistance than the alloys in as-received condition. This is attributed to a
combination of (1) higher thickness of the native oxide film on the AZ61 alloy
and (2) greater uniformity of the oxide film in the polished condition. The
formation of an additional oxide layer composed by a mixture of spinel
(MgAl2O4) and MgO seems to diminish the protective properties of the passive
layer on the surface of the alloys in as-received condition.
Keywords: Magnesium alloys, native oxide film; chemistry and s
This paper studies the corrosion rate of magnesium alloys AZ31 and AZ61 exposed in
humid air under continuous condensation conditions. The approximately parabolic
shape of the corrosion progress curves suggests that the process is controlled by
factors related with the corrosion product layer growing on the metallic surface.
Complementary EIS measurements provide evidence of the restriction of surface
activity by the accumulation of corrosion products. According to gravimetric results
there is an initial period in which only a small part of the corroded metal is incorporated
in the corrosion product layer, but after longer testing times the proportion of metal that
comes to form part of this layer tends to increase very significantly
AZ31 and AZ61 magnesium alloy substrates with different surface finish, the chemistry of
the outer surface of the conversion coatings that grows after their subsequent immersion on
saturated aqueous NaHCO3 solution treatment and the enhancement of corrosion resistance
have been studied. The significant increase in the amount of aluminum and carbonate
compounds on the surface of the conversion coating formed on the AZ61 substrate in
polished condition seems to improve the corrosion resistance in low chloride ion
concentration solutions. In contrast, the conversion coatings formed on the AZ31 substrates
in polished condition has little effect on their protective properties compared to the
respective as-received surface.
oxide surface layers induced by heating in air at 200ºC for time intervals from 5
minutes up to 60 minutes on commercial AZ31 and AZ61 magnesium alloys
with a view to a better understanding of their protective properties. A strong link
was found between the aluminium enrichment observed in the surface of the
oxide layer and the decrease in the protective properties of the heat treated
AZ31 alloy. In contrast, no significant changes have been observed in the case
of the heat treated AZ61 alloy.