Papers by Izelu Christopher
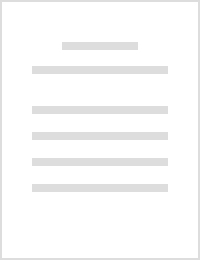
This paper presents an aspect of a series of experimental studies in which the effect of the fact... more This paper presents an aspect of a series of experimental studies in which the effect of the factors, such as depth of cut, feed rate and tool overhang on the response variables, such as machining induced vibration and surface roughness, during hard turning of 41Cr4 alloy structural steel on a conventional lathe with standard cutting tool is of major interest. The response surface methodology, based on central composite design of experiment, was used, and the analysis performed in Design Expert 9 software environment. Quadratic regression models were obtained and evaluated for the response variables as functions of the selected factors. The optimal settings of these factors required to minimize the response variables were also determine. The influence of the factors on the response variables were established through analysis of variance. The optimum setting of 58.2409 mm, for the tool overhang; 0.170594 mm/rev, for the feed rate; and 1.2192 mm, for the depth of cut would minimize th...

In this research work, the effectiveness of stainless steel sheet for the production of motor cyc... more In this research work, the effectiveness of stainless steel sheet for the production of motor cycle exhaust muffler burn protector was investigated. Energy Dispersive X-Ray fluorescence method was used to determine the chemical composition of the stainless steel materials and exhaust muffler of the motor cycle. The stainless steel sheet was perforated and folded to frustum shape to achieve aero dynamic shape and used as protective cover on the exhaust muffler to protect the leg from burns. The burn protector produced was mounted on Jincheng AX 100 motor cycle and driving test carried out for 15 days using operational periods of 10 minutes, 20 minutes, 30 minutes, 60 minutes and 90 minutes to determine its effectiveness. Cole Palmer thermocouple digital meter was used to measure the surface temperatures of the exhaust muffler and burn protector at the end of each operation cycle and data generated was averaged. The experimental results show that the longer the driving period the high...

An aspect of a set of hard turning experiment conducted on 41Cr4 alloy steel to investigate the i... more An aspect of a set of hard turning experiment conducted on 41Cr4 alloy steel to investigate the influence of the machining, cutting tool and work-piece variables on the machining induced vibration and surface roughness is presented. The response surface methodology, based on central composite design of experiment was adopted. Analysis of the response data was performed in the Design Expert 9 environment. The obtained Quadratic regression models were evaluated for the machining induced vibration and surface roughness as functions of the work-piece overhang, feed rate and depth of cut. The influence of the factors on the response variables were established through analysis of variance.The optimal settings of these factors as are required to minimize the response variables were also determine. It was found that the optimum setting of80 mm, for the work-piece overhang; 0.15 mm/rev, for the feed rate; and 2.32666 mm, for the depth of cut would minimize the machining induced vibration of ...

In this research work, induced vibrations and surface roughness of a tool-work-piece system in a ... more In this research work, induced vibrations and surface roughness of a tool-work-piece system in a turning process and their effect on product quality are examined. Attempts have been made to use vibration signals in predicting surface quality of product from lathe machine operation using response surface methodology. The surface roughness of machined parts is also predicted using the response surface methodology. The data are generated by lathe turning of 41Cr4 Alloy steel samples at different levels of low, medium and high of selected machining parameters. Prediction equations for induced vibration and surface roughness for 41Cr4 alloy steel was generated. From the experimental results, it shows that increasing the acceleration of cutting tool with increase in the tool nose radius will cause an increase in surface roughness of work piece if induced vibration in the system is significant. This effect interacts with other independent variables such as depth of cut and cutting speed.

International Journal of Innovative Research in Science, Engineering and Technology, 2013
This research work investigates the influence of alloying elements on Heat Affected Zone (HAZ) to... more This research work investigates the influence of alloying elements on Heat Affected Zone (HAZ) toughness of welded mild steel joints by identifying the alloying elements and experimentally determining their influence on the strength property of the weld. The ten V- notch impact test specimens made from all weld metal were used to conduct Charpy impact energy test. The chemical compositions of each of the all weld metals were determined. A relationship was established between the chemical compositions and their Charpy impact energy absorbed. The significance of alloying elements on the impact of the absorbed energy is explained by the theory of coefficient of variation. Small coefficient of variation means that the element considered is expected to have a high reliability. The coefficient of variation calculated and presented shows that Si, Cu and Mn have low reliability in term of toughness since the coefficient of variation in these elements is high (positive or negative). Also Mn ...
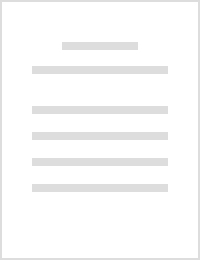
This study investigates experimentally the relationship between induced vibration and surface rou... more This study investigates experimentally the relationship between induced vibration and surface roughness in turning of 41Cr4 Alloy steel using Response Surface Methodology RSM. The levels of process cutting parameters in the study are limited to the following data; Depth of cut (1.0, 2.0, 3.0 mm), cutting speed (260, 320, 400 rpm), feed rate (0.15, 0.20, 0.30 mm/rev), tool nose radius (0, 1, 2 mm), tool overhang (50, 55, 60 mm) and work piece overhang (80, 100, 120 mm). The data are generated by lathe turning of 41Cr4 Alloy steel samples at different levels of low, medium and high. From the study it shows that Induced vibration has a significant effect on surface roughness of work piece. The surface roughness of work piece is proportional to cutting tool acceleration. This effect interacts with other independent variables such as depth of cut, cutting speed and cutting tool overhang etc. Experimental results have shown that induced vibration has significant impact on surface roughnes...
Automation, Control and Intelligent Systems, 2016
This paper presents a qualitative evaluation of wave-induced motions in an oilrig drill ship posi... more This paper presents a qualitative evaluation of wave-induced motions in an oilrig drill ship positioning system which incorporates a priori knowledge of noise contamination in the measured data. The noise contamination β defined in the function of the known form (P(X, β)) and X takes the specific values z, which from Cramer-Rao bound, gives the smallest possible variance with which the estimate of β can be determined. A conceptual model of the problem based on the maximum likelihood techniques in terms of joint probability distribution functions enhanced convergence of the iteration process. A filter was postulated to define the error covariance matrix which yielded unbiased estimates of the measured data.

International Journal of Mechanical Engineering and Applications, 2015
It is important to achieve high quality weld in underwater welding as it is vital to the integrit... more It is important to achieve high quality weld in underwater welding as it is vital to the integrity of the structures used in the offshore environment. Due to the difficulty in ensuring sound welds as it relates to the weld bead geometry, it is important to have a robust control mechanism that can meet this need. This work is aimed at designing a control mechanism for underwater wet welding which can control the welding process to ensure the desired weld bead geometry is achieved. Obtaining optimal bead width, penetration and reinforcement are essential parameters for the desired bead geometry. The method used in this study is the use of a control system that utilizes a combination of fuzzy and PID controller in controlling flux cored arc welding process. The outcome will ensure that optimal weld bead geometry is achieved as welding is being carried out at different water depth in the offshore environment. The result for the hybrid fuzzy-PID gives a satisfactory outcome of overshoot, rise time and steady error. This will lead to a robust welding system for oil and gas companies and other companies that carry out repair welding or construction welding in the offshore.

International Journal of Mechanical Engineering and Applications, 2016
Product quality, productivity and organizational goodwill are often the major concern of every pr... more Product quality, productivity and organizational goodwill are often the major concern of every production or manufacturing unit. These criteria, more especially product quality, cannot readily and effectively be met through dependence on the skills of an operator. Hence, the need for optimization in order to identify the best process condition, derived from parametric combinations of process variables, for the manufacturing process. The work presented concerns an aspect of a series of hard turning experiments on 41Cr4 alloy structural steel conducted to model, predict and optimize the machining induced vibration, and the surface roughness as functions of the cutting speed, feed rate, and the tool nose radius. The response surface methodology, based on the central composite design of experiment is employed in the study, and analysis of the generated data performed with the aid of Design expert 9 software. A quadratic regression model was suggested as best fits for both the machining induced vibration and surface roughness data. These were confirmed by analyses of variance, which also revealed the tool nose radius and cutting speed, as well as the feed rate and cutting speed to be important factors that determine changes in the machining induced vibration and surface roughness, respectively. The optimum setting of the tool nose radius at 1.72301 mm, feed rate at 0.15 mm/rev, and the cutting speed at 311.075 rev/min minimized the machining induced vibration to a value of 0.08 mm/min 2 and the surface roughness to a value of 4.74 µmm.

International Journal of Mechanical Engineering and Applications, 2016
Product quality, productivity and organizational goodwill are often the major concern of every pr... more Product quality, productivity and organizational goodwill are often the major concern of every production or manufacturing unit. These criteria, more especially product quality, cannot readily and effectively be met through dependence on the skills of an operator. Hence, the need for optimization in order to identify the best process condition, derived from parametric combinations of process variables, for the manufacturing process. The work presented concerns an aspect of a series of hard turning experiments on 41Cr4 alloy structural steel conducted to model, predict and optimize the machining induced vibration, and the surface roughness as functions of the cutting speed, feed rate, and the tool nose radius. The response surface methodology, based on the central composite design of experiment is employed in the study, and analysis of the generated data performed with the aid of Design expert 9 software. A quadratic regression model was suggested as best fits for both the machining induced vibration and surface roughness data. These were confirmed by analyses of variance, which also revealed the tool nose radius and cutting speed, as well as the feed rate and cutting speed to be important factors that determine changes in the machining induced vibration and surface roughness, respectively. The optimum setting of the tool nose radius at 1.72301 mm, feed rate at 0.15 mm/rev, and the cutting speed at 311.075 rev/min minimized the machining induced vibration to a value of 0.08 mm/min 2 and the surface roughness to a value of 4.74 µmm.

This paper presents the use of a computer oriented numerical approach in the characterization of ... more This paper presents the use of a computer oriented numerical approach in the characterization of the crank-double rocker mechanism of automobile windscreen wipers. The vector loop-closure technique, Newton-Raphson method for solution of nonlinear systems, and the concepts of velocity coefficients and velocity coefficient derivatives are used to formulate angular position, velocity and acceleration models for the kinematic analysis. The generalized energy-based equation of motion for single degree of freedom planar systems, the principles of virtual work, and those of force and moment equilibrium are used to formulate output torque, pin-joint or internal and reactive force models for the kinetostatic analysis. The effects of input speed, input torque and wiper contact friction on power transmission capability of the mechanism are studied in numerical experiments with the derived models, using ANOVA with repeated measures to establish these effects. It is found that the numerical models described, to acceptable levels, the kinematic and kinetostatic characteristics of the mechanism. The oscillatory or rocking motion is characteristic of the rockers, while the combined oscillatory and reciprocating motion is characteristic of the connecting links. Also, the input speed, input torque and friction factor have significant influence on the power transmission capability of first loop of the mechanism, whereas, only the friction factor has significant influence on the power transmission capability of second loop of the mechanism. The results showed that the derived models are quite suitable for the purpose of design and analysis of the mechanism and its extensions.

– In this research work, induced vibrations and surface roughness of a tool-work-piece system in ... more – In this research work, induced vibrations and surface roughness of a tool-work-piece system in a turning process and their effect on product quality are examined. Attempts have been made to use vibration signals in predicting surface quality of product from lathe machine operation using response surface methodology. The surface roughness of machined parts is also predicted using the response surface methodology. The data are generated by lathe turning of 41Cr4 Alloy steel samples at different levels of low, medium and high of selected machining parameters. Prediction equations for induced vibration and surface roughness for 41Cr4 alloy steel was generated. From the experimental results, it shows that increasing the acceleration of cutting tool with increase in the tool nose radius will cause an increase in surface roughness of work piece if induced vibration in the system is significant. This effect interacts with other independent variables such as depth of cut and cutting speed. Keyword– Response surface methodology, induced vibration, surface roughness, alloy steel, Depth of cut, cutting speed and tool nose radius
– The effect of turning parameters on induced vibration and work surface roughness of 41Cr4 alloy... more – The effect of turning parameters on induced vibration and work surface roughness of 41Cr4 alloy steel was experimentally examined. Response Surface Methodology in conjunction with third order composite factorial Design is used to evaluate the effect of turning parameters on induced vibration amplitude and surface roughness. The results, from the turning operations performed in the experiment, gave rise to a predictive second order response surface equation. Besides, it was observed that turning parameters (dept of cut, cutting speed and work piece overhang) had significant effect on the surface roughness of work piece, and to a relative degree, influenced induced vibration. It also shows that the induced vibration and surface roughness of work-piece is directly proportional to the depth of cut, cutting speed and work piece overhang.

As one of the fifth major urban cities in Nigeria, high demand for electricity in Port Harcourt, ... more As one of the fifth major urban cities in Nigeria, high demand for electricity in Port Harcourt, Rivers State, Nigeria is evident, and hence, requires high installed capacity for steady conventional energy source. At present this is hardly met, coupled with its attendant risk of undesirable emissions and other identified disadvantages. This paper considers that the conventional energy source may be supported or entirely replaced by the alternative or renewable sources to meet demands for electricity as well as minimize risks of undesirable emissions including other limitations of the conventional sources. It therefore presents a study of wind energy conversion system to be installed along the Choba banks of the New Calabar River. The system should be capable of serving electricity need of the University of Port Harcourt and the University of Port Harcourt Teaching Hospital all in Port Harcourt. The study is focused on the horizontal axis wind farm turbine rotor aerodynamic performance analysis, using the blade element momentum theory, and economic evaluation of the wind energy conversion system. It showed that, to meet with the total power requirement of 21 [MW] in the University and its Teaching Hospital for a projected period of 20 years, rotor blades of each of the wind farm turbines, which are optimally designed for capacity of 1.5 [MW], wind velocity of 17.5 [m/s], and for airfoil shape of NACA 2412, are desired. The power and torque of the designed turbines, using these blades and having positive non linear relationship with wind velocity, were achieved. Besides, an economic study of the system revealed savings in costs of N8, 633,032,101.98 in comparison with the existing diesel plant.

The development and sitting of wind energy conversion systems, for electrical power generation an... more The development and sitting of wind energy conversion systems, for electrical power generation and other applications, in various states of the Federal Republic of Nigeria demand proper wind resource assessment of the project sites. This paper therefore presents an assessment of wind resource for wind energy utilization in Port Harcourt, River State, Nigeria. The average monthly wind velocity data, obtained from the Nigerian Meteorological Agency, Port Harcourt, River State, Nigeria, was used, in conjunction with the logarithmic profile equation, to determine wind velocity data at a desired hub height, and with the Rayliegh probability distribution function, a form of Weibull probability distribution function, to determine wind velocity and energy distribution. The results obtained include the wind velocity distribution, wind energy distribution, and the optimum average wind velocity of 17.75 m/s at an altitude of 50 m, which corresponds to the optimum power density or yield of 1370.13 W/m 2. The results also revealed a maximum power density or yield of 10731.08 W/m 2. This amount of energy corresponds to a maximum average wind velocity of 35.25 m/s beyond which the power density drops off. These results are quite adequate and indicative of high wind energy potentials for Port Harcourt, River State, Nigeria.

This study investigates experimentally the relationship between induced vibration and surface rou... more This study investigates experimentally the relationship between induced vibration and surface roughness in turning of 41Cr4 Alloy steel using Response Surface Methodology RSM. The levels of process cutting parameters in the study are limited to the following data; Depth of cut (1.0, 2.0, 3.0 mm), cutting speed (260, 320, 400 rpm), feed rate (0.15, 0.20, 0.30 mm/rev), tool nose radius (0, 1, 2 mm), tool overhang (50, 55, 60 mm) and work piece overhang (80, 100, 120 mm). The data are generated by lathe turning of 41Cr4 Alloy steel samples at different levels of low, medium and high. From the study it shows that Induced vibration has a significant effect on surface roughness of work piece. The surface roughness of work piece is proportional to cutting tool acceleration. This effect interacts with other independent variables such as depth of cut, cutting speed and cutting tool overhang etc. Experimental results have shown that induced vibration has significant impact on surface roughness which can be used to control the finished surface of a work pieces during mass production.

This research work investigates the influence of alloying elements on Heat Affected Zone (HAZ) to... more This research work investigates the influence of alloying elements on Heat Affected Zone (HAZ) toughness of welded mild steel joints by identifying the alloying elements and experimentally determining their influence on the strength property of the weld. The ten V-notch impact test specimens made from all weld metal were used to conduct Charpy impact energy test. The chemical compositions of each of the all weld metals were determined. A relationship was established between the chemical compositions and their Charpy impact energy absorbed. The significance of alloying elements on the impact of the absorbed energy is explained by the theory of coefficient of variation. Small coefficient of variation means that the element considered is expected to have a high reliability. The coefficient of variation calculated and presented shows that Si, Cu and Mn have low reliability in term of toughness since the coefficient of variation in these elements is high (positive or negative). Also Mn is less reliable than Si. The implication of this is that the increase in the addition of Mn alloying elements would deteriorate the toughness profile of the weld as well as its Heat Affected Zones (HAZ). Other alloying elements such as C, P, Ni, Cr, Nb and V have high reliability; therefore these elements would tend to improve the HAZ toughness.

This paper presents the use of a computer oriented numerical approach in the characterization of ... more This paper presents the use of a computer oriented numerical approach in the characterization of the crank-double rocker mechanism of automobile windscreen wipers. The vector loop-closure technique, Newton-Raphson method for solution of nonlinear systems, and the concepts of velocity coefficients and velocity coefficient derivatives are used to formulate angular position, velocity and acceleration models for the kinematic analysis. The generalized energy-based equation of motion for single degree of freedom planar systems, the principles of virtual work, and those of force and moment equilibrium are used to formulate output torque, pin-joint or internal and reactive force models for the kinetostatic analysis. The effects of input speed, input torque and wiper contact friction on power transmission capability of the mechanism are studied in numerical experiments with the derived models, using ANOVA with repeated measures to establish these effects. It is found that the numerical models described, to acceptable levels, the kinematic and kinetostatic characteristics of the mechanism. The oscillatory or rocking motion is characteristic of the rockers, while the combined oscillatory and reciprocating motion is characteristic of the connecting links. Also, the input speed, input torque and friction factor have significant influence on the power transmission capability of first loop of the mechanism, whereas, only the friction factor has significant influence on the power transmission capability of second loop of the mechanism. The results showed that the derived models are quite suitable for the purpose of design and analysis of the mechanism and its extensions.
Uploads
Papers by Izelu Christopher