Papers by Yee-Hsien (Thomas) Ho

Thin Solid Films, Oct 1, 2019
The use of columnar structures in thermal barrier coatings (TBCs) enables producing materials wit... more The use of columnar structures in thermal barrier coatings (TBCs) enables producing materials with lower thermal conductivities that are also able to accommodate thermal expansion during temperature cycling events. However, open porosity leads to the failure of TBCs because of the rapid oxidation of the coating-substrate interface. Here we propose to create an oxidation-induced sealing process to mitigate any oxidation or potential chemical attack. This is achieved by premixing the top surface with a carbide phase (TiC or SiC) that oxidizes in contact with air to seal the surface through volume expansion. Laser processing was used as a technique to fabricate YSZ-Al2O3-TiC or YSZ-Al2O3-SiC layers on 316 stainless steel substrates to understand the viability of this process as well as this coating design in creating self-healing thermal barrier coatings. Nanocomposite self-healing coatings and single-phase yttria-stabilized zirconia (YSZ) reference layers were produced using a laser fluence of 17.0 J/mm 2 (800W), 19.1 J/mm 2 (900W), and 25.5 J/mm 2 (1200 W) to optimize process conditions. These coatings were subsequently annealed at 720 °C for 12 hours to ensure complete oxidation of the TiC(SiC) phase in the former coating. Xray diffraction and cross-sectional energy dispersive x-ray spectroscopy (EDS) elemental mapping confirmed the creation of the desired columnar structure to accommodate thermal stresses and that a post-annealing treatment was required to achieve complete oxidation of the TiC(SiC) phase. The migration of TiO2 phase to the crack site was demonstrated using cross-sectional scanning electron microscopy (SEM) in tandem with elemental mapping via energy dispersive spectroscopy. The suggested optimum laser fluence to create a viable self-healing composite was found to be 17.0 J/mm 2 since higher values resulted in significant interdiffusion between the substrate and the coating as indicated by cross-sectional SEM/EDS. Laser processing was demonstrated to be a viable technique that has the potential to create a self-healing layer that seals YSZ-based underlayers from diffusion.
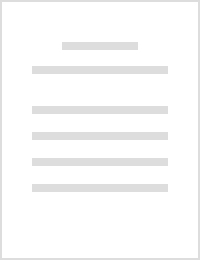
Journal of The Mechanical Behavior of Biomedical Materials, Sep 1, 2014
A laser based surface nitriding process was adopted to further enhance the osseo-integration, cor... more A laser based surface nitriding process was adopted to further enhance the osseo-integration, corrosion resistance, and tribological properties of the commonly used bioimplant alloy, Ti-6Al-4V. Earlier preliminary osteoblast, electrochemical, and corrosive wear studies of laser nitrided titanium in simulated body fluid clearly revealed improvement of cell adhesion as well as enhancement in corrosion and wear resistance but mostly lacked the in-depth fundamental understanding behind these improvements. Therefore, a novel integrated experimental and theoretical approach were implemented to understand the physical phenomena behind the improvements and establish the property-structure-processing correlation of nitrided surface. The first principle and thermodynamic calculations were employed to understand the thermodynamic, electronic, and elastic properties of TiN for enthalpy of formation, Gibbs free energy, density of states, and elastic properties of TiN were investigated. Additionally, open circuit potential and cyclic potentio-dynamic polarization tests were carried out in simulated body fluid to evaluate the corrosion resistance that in turn linked with the experimentally measured and computationally predicted surface energies of TiN. From these results, it is concluded that the enhancement in the corrosion resistance after laser nitriding is mainly attributed to the presence of covalent bonding via hybridization among Ti (p) and N (d) orbitals. Furthermore, mechanical properties, such as, Poisson׳s ratio, stiffness, Pugh׳s ductility criteria, and Vicker׳s hardness, predicted from first principle calculations were also correlated to the increase in wear resistance of TiN. All the above factors together seem to have contributed to significant improvement in both wear and corrosion performance of nitride surface compared to the bare Ti-6Al-4V in physiological environment indicating its suitability for bioimplant applications.
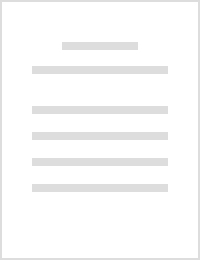
Nanomaterials and Energy, 2014
Nanocrystalline zinc titanate (ZnTiO3) coatings were deposited by atomic layer deposition (ALD) o... more Nanocrystalline zinc titanate (ZnTiO3) coatings were deposited by atomic layer deposition (ALD) on AISI 52100 steel to study ZnTiO3 corrosion protection. The main aim of this study was to determine how the coating can inhibit pitting formation of 52100 steel in both saline solution and simulated body fluid (SBF) media. Potentiodynamic polarization tests revealed increasing corrosion potentials for the ALD ZnTiO3-coated steel specimens with protective efficiencies of 83 and 73% in saline solution and SBF, respectively. Atomic force microscopy analysis of both the ZnTiO3-coated and uncoated steel revealed a high surface potential value for the ZnTiO3-coated sample as compared to the uncoated sample with a relatively low surface potential. The corrosion rates for the coated steels in both media were calculated and observed to drop by an order of magnitude. Due to the conformality, homogeneity and density of the ALD ZnTiO3 coatings, migration of Cl− and OH− ions from the electrolytes we...
Surface and Coatings Technology, 2012
A highly intense laser beam from a continuous wave diode-pumped ytterbium laser source was used t... more A highly intense laser beam from a continuous wave diode-pumped ytterbium laser source was used to synthesize a corrosion and wear resistant aluminum coating rich in Al12Mg17 intermetallic phase by direct melting of aluminum precursor powders on AZ31B Mg alloy substrates. The coating composition and microstructure were studied by X-ray diffraction, scanning electron microscopy, transmission electron microscopy and high resolution

Materials Science and Engineering: C, 2013
A high intensity continuous wave diode pumped ytterbium laser source was used to deposit CaP coat... more A high intensity continuous wave diode pumped ytterbium laser source was used to deposit CaP coatings on a Ti-6Al-4V biocompatible alloy in order to generate a physically textured surface, enhancing osseointegration. Scanning electron microscopy (SEM), scanning transmission electron microscopy (STEM) and energy dispersive spectroscopy (EDS) studies were coupled with X-ray and micro diffraction work to determine the structure, composition, and phases present in various zones of a sample prepared across the coating/substrate interaction zone. Three-dimensional thermal modeling was also carried out to determine the cooling rate and maximum temperature experienced by different regions of the substrate. Combining these results provide us with valuable insights regarding the thermo-physical as well as chemical interactions that take place across the coatingsubstrate interface.
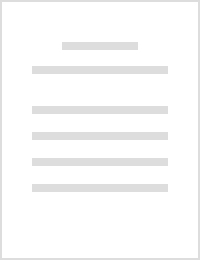
Materials Technology, 2012
ABSTRACT This paper addresses the critical issues associated with using conventional bioimplants ... more ABSTRACT This paper addresses the critical issues associated with using conventional bioimplants (stainless steel, cobalt–chromium and titanium alloy), and it emphasises on Mg as a potential material for fabricating load bearing bioimplants (hip, knee, shoulder and elbow). Hydroxyapatite (HAp) is a well established biodegradable coating material, while its combination with Mg enhances its corrosion resistance and biodegradability, thereby extending its longevity as a bioimplant material. A laser (2 kW IPG ytterbium of 1064 nm) coating of HAp on Mg alloy (AZ31B) was achieved under different processing conditions, and its corrosion behaviour and biodegradability were studied in simulated body fluid. Preliminary results indicate an improved corrosion resistance (48%) and biodegradability (180%) of AZ31B coated with HAp for selected laser process variables (power, scanning speed and beam indexing). Further, a detailed investigation is in progress in efforts to address many critical issues related to the fabrication and longevity of load bearing bioimplants.

Journal of biomaterials applications, 2015
Magnesium alloys are the potential degradable materials for load-bearing implant application due ... more Magnesium alloys are the potential degradable materials for load-bearing implant application due to their comparable mechanical properties to human bone, excellent bioactivity, and in vivo non-toxicity. However, for a successful load-bearing implant, the surface of bio-implant must allow protein absorption and layer formation under physiological environment that can assist the cell/osteoblast growth. In this regard, surface wettability of bio-implant plays a key role to dictate the quantity of protein absorption. In light of this, the main objective of the present study was to produce favorable bio-wettability condition of AZ31B Mg alloy bio-implant surface via laser surface modification technique under various laser processing conditions. In the present efforts, the influence of laser surface modification on AZ31B Mg alloy surface on resultant bio-wettability was investigated via contact-angle measurements and the co-relationships among microstructure (grain size), surface roughnes...
His wisdom, patience, diligence, and enthusiasm towards academic scientific research were the exc... more His wisdom, patience, diligence, and enthusiasm towards academic scientific research were the excellent pattern to me during my graduate education. Without his support, encouraging, and guidance it would be nearly impossible to me to complete this thesis. I am truly indebted to Dr. Dahotre give me such the precious opportunity to generate valuable
Two dimensional (2D) layered materials have recently attracted significant research interest owin... more Two dimensional (2D) layered materials have recently attracted significant research interest owing to their unique physical and chemical properties for efficient electrochemical energy storage devices. Here, we present a neoteric approach to fabricate high performance MoS₂ thin film supercapacitor electrodes by using a direct magnetron sputtering technique. The novel three-dimensional (3D) porous structure of the MoS₂ film exhibits an excellent capacitance of ∼330 F cm⁻³ along with a high volumetric power and energy density of 40–80 W cm⁻³ and 1.6–2.4 mW h cm⁻³, respectively. Moreover, the optimized MoS₂ electrode shows an outstanding cyclic stability, yielding capacitance retention over 97% after 5000 cycles of charging/discharging. The contemporary approach to MoS₂ supercapacitor electrode fabrication will enable new opportunities in flexible electronic and energy devices.
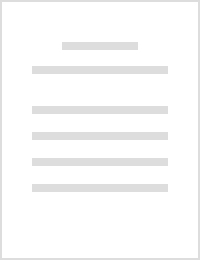
Magnesium and its alloys have been considered for load-bearing implant materials due to their sim... more Magnesium and its alloys have been considered for load-bearing implant materials due to their similar mechanical properties to the natural bone, excellent biocompatibility, good bioactivity, and biodegradation. Nevertheless, the uncontrollable corrosion rate in biological environment restrains their application. Hydroxyapatite (HA, Ca10(PO4)6(OH)2) is a widely used bio-ceramic which has bone-like mineral structure for bone fixation. Poor fracture toughness of HA makes it not suitable for load-bearing application as a bulk. Thus, HA is introduced into metallic surface in various forms for improving biocompatibility. Recently friction stir processing (FSP) has emerged as a surface modification tool for surface/substrate grain refinement and homogenization of microstructure in biomaterial. In the pressent efforts, Mg-nHA composite surface on with 5-20 wt% HA on Mg substrate were fabricated by FSP for biodegradation and bioactivity study. The results of electrochemical measurement indic...
Advanced Engineering Materials
Journal of Magnesium and Alloys

Sensors
Corrosion in underground and submerged steel pipes is a global problem. Coatings serve as an impe... more Corrosion in underground and submerged steel pipes is a global problem. Coatings serve as an impermeable barrier or a sacrificial element to the transport of corrosive fluids. When this barrier fails, corrosion in the metal initiates. There is a critical need for sensors at the metal/coating interface as an early alert system. Current options utilize metal sensors, leading to accelerating corrosion. In this paper, a non-conductive sensor textile as a viable solution was investigated. For this purpose, non-woven Zinc (II) Oxide-Polyvinylidene Fluoride (ZnO-PVDF) nanocomposite fiber textiles were prepared in a range of weight fractions (1%, 3%, and 5% ZnO) and placed at the coating/steel interface. The properties of ZnO-PVDF nanocomposite meshes were characterized using scanning electron microscopy (SEM), X-ray diffraction (XRD), Fourier transform infrared (FTIR) and d33 meter. Electrochemical impedance spectroscopy (EIS) testing was performed during the immersion of the coated sample...
ACS Biomaterials Science & Engineering
Materials Science and Engineering: C
Uploads
Papers by Yee-Hsien (Thomas) Ho