Papers by Dragan Milutinovic

Original scientific paper This paper describes analytically and experimentally based compliance m... more Original scientific paper This paper describes analytically and experimentally based compliance modeling and identification of 5-axis vertical articulated machining robot. The conventional method for the calculation of Cartesian space compliance based on joint compliances and Jacobian matrix is expanded and used for experimental 5-axis machining robot. Analytical analysis was conducted for effects of compliances of each joint individually on Cartesian space robot compliance. Experimentally, the Cartesian space compliance is obtained by direct measurement of the absolute displacements evoked by static forces along 3-orthogonal directions at the tool tip in the robot workspace for the case of 3-axis machining. Analiza popustljivosti robota za obradu vertikalne zglobne konfiguracije Izvornoznanstveni članak U radu su predstavljeni analitičko i eksperimentalno modeliranje i identifikacija popustljivosti 5-osnog robota za obradu vertikalne zglobne konfiguracije. Konvencionalni pristup za određivanje popustljivosti robota u Kartezijevom prostoru, zasnovan na popustljivosti zglobova i Jakobijan matrici je proširen i upotrebljen za određivanje popustljivosti eksperimentalnog 5-osnog robota. Analitička analiza je provedena s ciljem definiranja utjecaja popustljivosti svakog zgloba pojedinačno na popustljivost robota u Kartezijevom prostoru. Popustljivost robota u Kartezijevom prostoru je eksperimentalno određena direktnim mjerenjem apsolutnih pomicanja vrha robota izazvanih statičkom silom u sva tri ortogonalna pravca u radnom prostoru za slučaj 3-osne obrade.
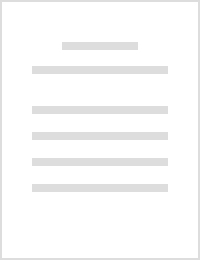
Sensitivity Analysis of Relationship Between Error Motions and Machined Shape Errors in Five-axis Machining Center - Peripheral Milling Using Square-End Mill as Test Case
Precision Engineering
Abstract Five-axis machine tools, consisting of three translational axes and two rotary axes, are... more Abstract Five-axis machine tools, consisting of three translational axes and two rotary axes, are increasingly being used for complex surface machining. This paper proposes a new sensitivity analysis method to elucidate the relationship between the tool trajectory error and the error motions of the feed axes. Based on the free-curve trajectory during simultaneous five-axis machining, a surface coordinate system is created for each tool center point, to define the tool trajectory and the trajectory errors. Then, a novel sensitivity coefficient is defined to investigate the relationship between the trajectory error and the error motions. It is shown that the proposed sensitivity analysis method can successfully determine whether the trajectory is sensitive to the error motions, based on sensitivity analyses performed during conic frustum machining and S-shaped machining tests. Moreover, the sensitivity analysis method can also predict the effects of the error motion source, such as the reversal errors. In the future, we intend to study other types of machining processes, such as ball-end milling, as well.
Tehnicki vjesnik - Technical Gazette
Robotic machining systems play an important role in modern manufacturing. The paper proposes the ... more Robotic machining systems play an important role in modern manufacturing. The paper proposes the application of virtual robots for off-line programming. The reconfigurable machining robot, programmed in G-code, which can be directly used by CNC machine tool programmers and operators, is presented. The subject of study are 5-and 6-DOF vertical articulated robots that can be configured to emulate vertical and horizontal 5-axis spindle tilting machine tools. The considered machining systems are supported by equivalent virtual robots in the CAD/CAM environment and control system. Several test workpieces were machined to demonstrate the effectiveness of the proposed architecture.
Mechanism for active Π-joint as an equivalent to the combination of revolute joint and proximal fixed-length link
Robotics and Computer-Integrated Manufacturing, 2015
ABSTRACT The Pa or Π-joint, as a planar parallelogram four-bar linkage, is of particular interest... more ABSTRACT The Pa or Π-joint, as a planar parallelogram four-bar linkage, is of particular interest and importance for parallel kinematic mechanisms. With the idea of replacing the combination of an active revolute joint and of a proximal fixed-length link with an active (powered and controlled) Π-joint, a new parallelogram-based one-degree-of-freedom (1-DOF) mechanism has been developed. The paper describes the structure of the mechanism, modeling approach and analysis as well as the developed active Π-joint laboratory prototype.

Tehnika, 2014
U ovom radu je predstavljen razvoj mini laboratorijske i edukacione stone troosne glodalice sa pa... more U ovom radu je predstavljen razvoj mini laboratorijske i edukacione stone troosne glodalice sa paralelnom kinematikom. Usvojeni su funkcionalni zahtevi i koncepcija mašine. Prikazan je opis primenjenog paralelnog mehanizma. Predstavljena je primenjena metodologija za konfigurisanje mini laboratorijske i edukacione stone troosne glodalice sa paralelnom kinematikom primenom IDEF0 dijagrama, sa detaljnom razradom aktivnosti koje se donose na realizaciju prototipa mašine. Verifikacija virtuelnog prototipa koncepcije mašine je izvršena simulacijom obrade na virtuelnoj mašini u CAD/CAM okruženju. U radu su pokazani neki od karakterističnih detalja pri realizaciji prototipa, kao i njegovog razvojnog ispitivanja. Ključne reči: konfigurisanje, virtuelni prototip, troosna glodalica sa paralelnom kinematikom This paper presents the development of mini laboratory and educational desktop 3 axis milling machine with parallel kinematic. Functional requirements and concept of this machine were adopted. Description of the applied parallel mechanism is shown in this paper. The presented methodology was used to configure mini laboratory and educational desktop 3 axis milling machine with parallel kinematic using IDEF0 diagrams, with detailed development activities who are made on the implementation of the prototype machine.Verification of the concept of virtual prototype is described using simulation on virtual machine in the CAD/CAM environment. The paper presents some of the most characteristic details in the implementation of the prototype, as well as his development testing.
This paper presents programming methods for parallel kinematics machine based on mini laboratory ... more This paper presents programming methods for parallel kinematics machine based on mini laboratory and desktop 3-axis parallel kinematic milling machine (PKMM). In this paper, a comparison between classical (G code) and new way of programming (STEP-NC) is given. Several test workpieces are machined in order to verify the programming system. The aim of the experiments was to test the capabilities of the developed control system prototype for mini laboratory and desktop 3-axis PKMM.
This paper describes analytically and experimentally based compliance modeling and identification... more This paper describes analytically and experimentally based compliance modeling and identification of 5-axis vertical articulated machining robot. The conventional method for the calculation of Cartesian space compliance based on joint compliances and Jacobian matrix is expanded and used for experimental 5-axis machining robot. Analytical analysis was conducted for effects of compliances of each joint individually on Cartesian space robot compliance. Experimentally, the Cartesian space compliance is obtained by direct measurement of the absolute displacements evoked by static forces along 3- orthogonal directions at the tool tip in the robot workspace for the case of 3-axis machining.
Pose Measurement of Parallel Kinematic Machines with Serial Link Measuring System
Advanced Manufacturing, 1999
ABSTRACT For higher accuracy of parallel kinematic robots and machine tools in particular, severa... more ABSTRACT For higher accuracy of parallel kinematic robots and machine tools in particular, several error models and compensation algorithms have been developed. The paper presents the approach for testing and control of Stewart platform-based machine tools and robots. The approach is based on serial link measuring system with six DOF in general, which may be used as an autonomous measuring device or in symbiosis with parallel kinematic machines to achieve Cartesian-based control schemes. Developed approach is demonstrated and verified on the example of developed planar parallel simulator with three DOF.
Strojniški vestnik – Journal of Mechanical Engineering, 2015
Configuring new machine tools is a complex task that involves the use of a large range of concept... more Configuring new machine tools is a complex task that involves the use of a large range of conceptions, methods, models, virtual prototypes and simulations. This paper presents a methodology for configuring a new machine tool to the level of a virtual prototype by using CAD configurator Pro/WEB.Link and a top-down approach. This methodology is explained via an example of the development of a minilaboratory and desktop 3-axis parallel kinematic milling machine (PKMM). The results are two variants of the virtual prototype and one real world prototype. The configured virtual prototypes are used for the verification of the machining program and programming system using machining simulation in the CAD/CAM environment. The mini-laboratory and desktop 3-axis PKMM has been verified by the successful machining of test workpieces.
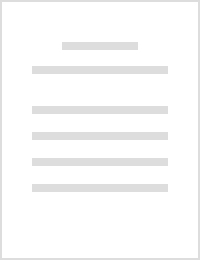
Mini Educational 3AXIS Parallel Kinematic Milling Machine
Parallel kinematic machines (PKM) are still R&D topic in many laboratories although many of them ... more Parallel kinematic machines (PKM) are still R&D topic in many laboratories although many of them unfortunately, have no PKM at all. Therefore the use of a low cost mini educational 3-axis parallel kinematic milling machine is suggested as a help in the proc- ess of acquiring basic experiences in the field of PKM. The developed mini educational 3-axis parallel kinematic milling machine is based on a newly developed 3-DOF spatial parallel mechanism. This paper describes the structure of machine, modelling approach, and control and programming system based on PC Linux platform. In order to contribute to acquiring practical experiences in modelling, design, control, program- ming and the use of PKM, functional simulator of parallel kinematic milling machine has been first developed /1/ and then a low-cost mini educational 3-axis parallel kinematic milling ma- chine is suggested. The developed mini educational 3-axis parallel kinematic milling machine is based on a newly developed 3-DOF ...
Robotics and Computer-Integrated Manufacturing, 1990
Based on the SCARA concept, accepted worldwide, this paper considers the possibility of realizing... more Based on the SCARA concept, accepted worldwide, this paper considers the possibility of realizing SCARA with a full circle working area. The basis of the approach is a mechanism with two eccentrically positioned rotating discs instead of two joined links. In this way, apart from a circular working area and some other advantages, the installation of several tools (hands) is also facilitated. This paper analyzes the advantages of the proposed solution and the possibilities of its realization.

Robotics and Computer-Integrated Manufacturing, 1987
A model-based vision system has been successfully implemented in a small computer environment. Th... more A model-based vision system has been successfully implemented in a small computer environment. This approach uses a basic solid modeling system to develop three-dimensional models of mechanical parts. From those models, two-dimensional projections are taken for every stable state of the object, with many orientations around the object's vertical axis for each stable state. These two-dimensional projections are treated as synthetic binary images, from which a variety of features may be measured and extracted. A similar procedure is used for a binary image of an object from a real scene, and features are also extracted for that image. A simple matching procedure uses the model-based feature sets to determine the real object's stable state position and orientation. This paper describes the system in detail and shows examples of its use.
Parallel structured milling machines with long X travel
Robotics and Computer-Integrated Manufacturing, 2008
The paper presents research and development results of one parallel structured milling machine wi... more The paper presents research and development results of one parallel structured milling machine with long X travel. The developed milling machine experimental prototype is based on a newly developed 3-DOF spatial parallel mechanism. In comparison with similar developed machines, it has several advantages such as: rather regular shape of the workspace similar to serial machines, greater stiffness by nature of
Robotics and Computer-Integrated Manufacturing, 1997
The paper presents the results of the research and the development of the universal adaptive comp... more The paper presents the results of the research and the development of the universal adaptive compliant device for customary assembly task robot configurations. The developed system is based on a newly developed SCARA robotic mechanism and combined properties of the SCARA concept and RCC devices. It successfully operates around its true compliance center, obtained under precisely determined conditions.
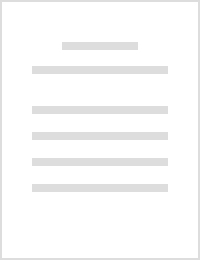
A method for off-line compensation of cutting force-induced errors in robotic machining by tool path modification
The International Journal of Advanced Manufacturing Technology, 2014
ABSTRACT Industrial robots are promising cost-effective and flexible alternatives for multi-axis ... more ABSTRACT Industrial robots are promising cost-effective and flexible alternatives for multi-axis milling applications in machining of complex parts of light materials with lower tolerances, having freeform surfaces. As it is well-known, the poor accuracy, stiffness, and the complexity of programming are the most important limiting factors for wider adoption of robotic machining in machine shops. The paper presents the developed method for off-line compensation of machining robot tool tip static displacements as a dominant part of cutting force-induced errors. The developed method is based on modification of programmed trajectory in G-code. Off-line modification of programmed trajectory is performed according to the predicted static tool tip displacements calculated based on developed robot compliance model and cutting forces predicted by mechanistic model. The obtained experimental results show the relevance of developed method since the machining errors could be significantly reduced. This allows the desired accuracy of robot machining to converge towards nominal specifications.
The International Journal of Advanced Manufacturing Technology, 2009
Parallel kinematic machines (PKM) are researchand-development topic in many laboratories although... more Parallel kinematic machines (PKM) are researchand-development topic in many laboratories although many of them, unfortunately, have no PKM at all. Therefore, the use of low cost but functional simulator of a 3-Axis parallel kinematic milling machine is suggested as a help to acquire the basic experiences in the PKM field. The idea is based on the possibility that the simulator could be driven and controlled by a conventional 3-Axis Computer Numerical Control machine tool (CNC). The paper describes the development procedure of a simulator including the selection of a corresponding parallel mechanism, kinematic modelling, and the programming algorithm. The functional simulator idea has been verified by successful making of some standardized test pieces of soft material, under full operational conditions.
A New 3-DOF Spatial Parallel Mechanism for Milling Machines with Long X Travel
CIRP Annals - Manufacturing Technology, 2005
It is well known that the shape and volume of the workspace are one of the greatest weaknesses of... more It is well known that the shape and volume of the workspace are one of the greatest weaknesses of parallel kinematic machine tools (PKM). Hexaglide and Triaglide mechanisms are examples where workspace extension is achieved by elongating one axis as a principal motion axis that is a common feature of all Cartesian machines. With the idea of principal axis of
Micro Scara Robot as Universal Adaptive Compliant Wrist
CIRP Annals - Manufacturing Technology, 1996
The newly developed robotic mechanism based on well-known SCARA concept uses two eccentrically po... more The newly developed robotic mechanism based on well-known SCARA concept uses two eccentrically positioned rotating discs instead of two joined links. The paper analyzes the capabilities and advantages of the use of this mechanism in the realization of micro SCARA robot as an additional adaptive compliant wrist to standard robot configurations for assembly tasks. The prototype of a universal passive adaptive compliant wrist was developed at this stage. The performance around its true compliance center obtained under precisely determined conditions proved successful.
The International Journal of Advanced Manufacturing Technology, 2011
Industrial robots represent a promising costeffective and flexible alternative for some machining... more Industrial robots represent a promising costeffective and flexible alternative for some machining applications. This paper describes the concept of reconfigurable robot multi-axis machining systems for machining the complex parts of light materials with lower tolerances having freeform surfaces. For the basic configuration of a five-axis robotic machining system, the robot modeling approach is shown in detail as well as the prototype of developed control system with programming in G-code. The experimental robotic machining system has been verified by successful machining of several test work pieces.
Uploads
Papers by Dragan Milutinovic