Papers by Dr.G.Madhusudhan Reddy
Social Science Research Network, 2022
Friction stir processing (FSP) has emerged as an effective secondary processing technique to impr... more Friction stir processing (FSP) has emerged as an effective secondary processing technique to improve the microstructure and properties of aluminum matrix composites (AMCs). Al/(0-15wt.%) Al 3 Fe AMCs were prepared by adding pure iron powder to molten aluminum and subjected to FSP. The microstructural changes before and after FSP were studied using OM, SEM, EBSD and TEM. Cast composites exhibited coarse grains, segregation, pores and sharp-edged particles. The distribution of particles was rearranged into a homogeneous distribution after FSP. Casting defects such as pores were eliminated. The sharp edges of Al 3 Fe particles were removed and rounded into near spherical shape. The M

Defence Technology, Sep 1, 2015
The present work is aimed at studying the microstructure and pitting corrosion behaviour of shiel... more The present work is aimed at studying the microstructure and pitting corrosion behaviour of shielded metal arc welded high nitrogen steel made of Cromang-N electrode. Basis for selecting this electrode is to increase the solubility of nitrogen in weld metal due to high chromium and manganese content. Microscopic studies were carried out using optical microscopy (OM) and field emission scanning electron microscopy (FESEM). Energy back scattered diffraction (EBSD) method was used to determine the phase analysis, grain size and orientation image mapping. Potentio-dynamic polarization testing was carried out to study the pitting corrosion resistance in aerated 3.5% NaCl environment using a GillAC electrochemical system. The investigation results showed that the selected CreMneN type electrode resulted in a maximum reduction in delta-ferrite and improvement in pitting corrosion resistance of the weld zone was attributed to the coarse austenite grains owing to the reduction in active sites of the austenite/delta ferrite interface and the decrease in galvanic interaction between austenite and delta-ferrite.
Fusion Engineering and Design, Mar 1, 2021
Cu-ZrO 2 nanocomposites were produced by the thermochemical process followed by powder metallurgy... more Cu-ZrO 2 nanocomposites were produced by the thermochemical process followed by powder metallurgy technique. Microstructure development during fabrication process was investigated by X-ray diffraction, field emission scanning electron microscope and transmission electron microscope. The results show an improved distribution of zirconium dioxide (ZrO 2 ) nanoparticles (45 nm) in the copper matrix, which resulted in the improvement of mechanical properties of Cu-ZrO 2 composites. The nanocomposite with 9 wt-% ZrO 2 possesses the highest hardness (136.5 HV) and the superior compressive strength (413.5 MPa), resulting in an overall increase by 52 and 25%, respectively. The wear rate of the nanocomposites increased with increasing applied loads or sliding velocity.

Proceedings of the Institution of Mechanical Engineers, Part C: Journal of Mechanical Engineering Science, Nov 14, 2022
Friction stir processing (FSP) is a solid-state processing technique to enhance the surface prope... more Friction stir processing (FSP) is a solid-state processing technique to enhance the surface properties of the metallic materials. The present study aims to improve the surface mechanical and wear properties of Cu-0.18wt.%Zr alloy through FSP without deteriorating its electrical conductivity behavior. The Cu-Zr alloy was friction stir processed at a constant tool rotation speed of 600 rpm and by varying the tool travel speed from 50 to 200 mm/min. The specimens were extracted from the stir zone to characterize its microstructure, mechanical properties and wear behavior. It was observed that the average size of grains in stir zone decreased from 40.5 to 4.6 lm with the increase in tool travel speed, whereas hardness of the processed specimens increased from initial 70 to 99 Hv. The coefficient of friction was decreased from 0.4 to 0.07 (l) as travel speed increased. Consequently, the wear resistance of the processed samples increased with the travel speed. The change in electrical conductivity, as measured using eddy current technique, was noted to be insignificant in the processed specimens, i.e., it decreased to 77.4% IACS from its initial 78.2% IACS. Hence, the objective of improving the mechanical and wear resistance properties of Cu-Zr alloy was achieved without impairing the electrical conductivity by friction stir processing. The results suggest that friction stir processing can be effectively used to improve the wear behavior of highstrength and high-electrical conductivity alloys.
Materials Science Forum, 2006
The commercial 7xxx series Al alloys are based on medium strength Al-Zn-Mg and high strength Al-Z... more The commercial 7xxx series Al alloys are based on medium strength Al-Zn-Mg and high strength Al-Zn-Mg-Cu systems. The medium strength alloys are weldable, whilst the high strength alloys are nonweldable. On the other hand, the Cu-free, weldable alloys suffer from poor SCC resistance. It is the purpose of this article to provide quantitative data and microstructural analysis to demonstrate that small additions of either Ag or Sc to Al-Zn-Mg and Al-Zn-Mg-Cu alloys bring about very significant improvement in SCC resistance and weldability, respectively. The improvement in SCC resistance of the Cu-bearing alloys due to over aging and retrogression and reaging (RRA) is further discussed in light of a similar improvement in the SCC resistance of these alloys, when peak aged, due to Ag and Sc additions.
Advances in Materials and Processing Technologies, Jun 2, 2023
Materials Science Forum, 2002
All rights reserved. No part of contents of this paper may be reproduced or transmitted in any fo... more All rights reserved. No part of contents of this paper may be reproduced or transmitted in any form or by any means without the written permission of TTP, www.ttp.net. (ID: 66.249.66.204-27/04/11,07:45:41) ... Aluminium Alloys 2002 - ICAA8 doi:10.4028/www. ...
Social Science Research Network, 2022
Friction stir processing (FSP) has emerged as an effective secondary processing technique to impr... more Friction stir processing (FSP) has emerged as an effective secondary processing technique to improve the microstructure and properties of aluminum matrix composites (AMCs). Al/(0-15wt.%) Al 3 Fe AMCs were prepared by adding pure iron powder to molten aluminum and subjected to FSP. The microstructural changes before and after FSP were studied using OM, SEM, EBSD and TEM. Cast composites exhibited coarse grains, segregation, pores and sharp-edged particles. The distribution of particles was rearranged into a homogeneous distribution after FSP. Casting defects such as pores were eliminated. The sharp edges of Al 3 Fe particles were removed and rounded into near spherical shape. The M

Transactions of the Indian Institute of Metals, Mar 2, 2017
The influence of parent metal condition on the microstructure and mechanical properties of fricti... more The influence of parent metal condition on the microstructure and mechanical properties of friction welds of Ti6Al4V alloy has been investigated. Welds are observed to contain predominantly martensite. Stress relieving results in improvement in the strengths of a ? b and b treated parent metal and their welds. b welds are observed to contain coarser prior b grains. Studies reveal that welds of a ? b solution treated parent metal exhibit higher strength than all the other welds. In plain tensile tests, the location of failure is away from the welds in all the conditions, suggesting that the welds are stronger than their respective parent metals. Parent metal in a ? b and b solution treated conditions is observed to respond to stress relieving such that, hardness is improved after stress relieving. Stress relieving results in reduced ductility and improvement in the strength of the welds. Notch tensile strength of the welds is observed to be higher than their parent metals and stress relieving results in further improvement. The notch tensile ratio of the welds has been observed to be *1.4 in all the conditions indicating that the welds are not notch sensitive.
Trans Tech Publications Ltd. eBooks, Jul 15, 2006
The commercial 7xxx series Al alloys are based on medium strength Al-Zn-Mg and high strength Al-Z... more The commercial 7xxx series Al alloys are based on medium strength Al-Zn-Mg and high strength Al-Zn-Mg-Cu systems. The medium strength alloys are weldable, whilst the high strength alloys are nonweldable. On the other hand, the Cu-free, weldable alloys suffer from poor SCC resistance. It is the purpose of this article to provide quantitative data and microstructural analysis to demonstrate that small additions of either Ag or Sc to Al-Zn-Mg and Al-Zn-Mg-Cu alloys bring about very significant improvement in SCC resistance and weldability, respectively. The improvement in SCC resistance of the Cu-bearing alloys due to over aging and retrogression and reaging (RRA) is further discussed in light of a similar improvement in the SCC resistance of these alloys, when peak aged, due to Ag and Sc additions.

Transactions of the Indian Institute of Metals, Mar 4, 2019
Friction stir processing (FSP) is a solid-state processing technique to enhance the surface prope... more Friction stir processing (FSP) is a solid-state processing technique to enhance the surface properties of the metallic materials. The present study aims to improve the surface mechanical and wear properties of Cu-0.18wt.%Zr alloy through FSP without deteriorating its electrical conductivity behavior. The Cu-Zr alloy was friction stir processed at a constant tool rotation speed of 600 rpm and by varying the tool travel speed from 50 to 200 mm/min. The specimens were extracted from the stir zone to characterize its microstructure, mechanical properties and wear behavior. It was observed that the average size of grains in stir zone decreased from 40.5 to 4.6 lm with the increase in tool travel speed, whereas hardness of the processed specimens increased from initial 70 to 99 Hv. The coefficient of friction was decreased from 0.4 to 0.07 (l) as travel speed increased. Consequently, the wear resistance of the processed samples increased with the travel speed. The change in electrical conductivity, as measured using eddy current technique, was noted to be insignificant in the processed specimens, i.e., it decreased to 77.4% IACS from its initial 78.2% IACS. Hence, the objective of improving the mechanical and wear resistance properties of Cu-Zr alloy was achieved without impairing the electrical conductivity by friction stir processing. The results suggest that friction stir processing can be effectively used to improve the wear behavior of highstrength and high-electrical conductivity alloys.

Materials Letters, Apr 1, 2020
Friction stir processing (FSP) is a solid-state processing technique to enhance the surface prope... more Friction stir processing (FSP) is a solid-state processing technique to enhance the surface properties of the metallic materials. The present study aims to improve the surface mechanical and wear properties of Cu-0.18wt.%Zr alloy through FSP without deteriorating its electrical conductivity behavior. The Cu-Zr alloy was friction stir processed at a constant tool rotation speed of 600 rpm and by varying the tool travel speed from 50 to 200 mm/min. The specimens were extracted from the stir zone to characterize its microstructure, mechanical properties and wear behavior. It was observed that the average size of grains in stir zone decreased from 40.5 to 4.6 lm with the increase in tool travel speed, whereas hardness of the processed specimens increased from initial 70 to 99 Hv. The coefficient of friction was decreased from 0.4 to 0.07 (l) as travel speed increased. Consequently, the wear resistance of the processed samples increased with the travel speed. The change in electrical conductivity, as measured using eddy current technique, was noted to be insignificant in the processed specimens, i.e., it decreased to 77.4% IACS from its initial 78.2% IACS. Hence, the objective of improving the mechanical and wear resistance properties of Cu-Zr alloy was achieved without impairing the electrical conductivity by friction stir processing. The results suggest that friction stir processing can be effectively used to improve the wear behavior of highstrength and high-electrical conductivity alloys.
Surface Engineering, Mar 1, 2011
Present work pertains to investigation carried out on solid state surfacing of titanium alloy Ti-... more Present work pertains to investigation carried out on solid state surfacing of titanium alloy Ti-6Al-4V with AA2124SiCp metal matrix composite by friction surfacing. The coating was characterised by metallography and dry sliding wear. For the first time it was found that titanium alloy could be friction surfaced with metal matrix composites. The surface coating exhibited the wear properties to many-fold than that of the titanium substrate. Significant improvement in the wear resistance of titanium alloy may be attributed to the interdiffusion of elements and the formation of nanocrystalline layer of the alloy at the interface.
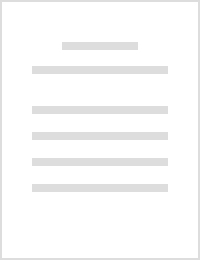
Lecture notes in mechanical engineering, 2020
The impulse excitation technique (IET) is one of the most reliable and non-destructive techniques... more The impulse excitation technique (IET) is one of the most reliable and non-destructive techniques to measure dynamic elastic properties of materials. It is also possible to measure the damping factor and the resonant frequency of materials using this technique. In the current study, IET is used to measure Young’s modulus, natural or resonant frequency (fr) and damping factor (Q−1) of friction stir processed pure metals with an intention to assess their vibration damping ability. Commercial pure aluminium (Al), copper (Cu) and magnesium (Mg) metals were subjected to single-pass friction stir processing employing 600 RPM of tool rotational speed and 60 mm/min of travel speed. The specimens for IET analysis and for microstructural observations were extracted from the stir zone of friction stir processed plates. The microstructure in the stir zone is severely refined by the friction stirring particularly the grain size of magnesium refined to 25.6 µm from its initial size of 780 µm. The measured Young’s modulus and natural frequency for the processed Al and Cu samples were interestingly lower than their as-received counterparts. But the damping ability of these metals significantly improved after processing. However, for magnesium, the observed trends in the properties before and after processing were quite opposite to the other two metals. The crystal defects created during the friction stirring could be a reason for the observed trends.
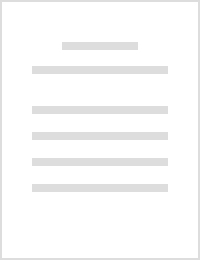
Materials Letters, Sep 1, 2021
Abstract An attempt is made here to understand the role of tool rotational speed on the damping c... more Abstract An attempt is made here to understand the role of tool rotational speed on the damping capacity of friction stir processed (FSP) commercial pure aluminium metal. The as-received metal plates were processed with a conical pin tool by keeping the tool traverse speed as constant and varying the rotational speed 600, 900 and 1200 rpm. Subsequently, samples extracted from the stir-zones were characterized for their microstructure, hardness, frequency-dependent and temperature-dependent damping capacities. The increase in rotational speed decreased the dislocation density and increased the average grain-size at the stir-zone, thus significantly influenced the damping capacity. The frequency-dependent damping capacity decreased with rotational speed owing to the reduction in dislocation density. High-temperature damping was significantly higher for the processed samples, but at the same time increase in rotational speed decreased the damping as there was an increase in grain size.
Advanced Materials Research, Sep 1, 2013
The present work compares the microstructure and mechanical properties of 1050 aluminum subjected... more The present work compares the microstructure and mechanical properties of 1050 aluminum subjected to constrained groove pressing (CGP) combined with cold rolling. Transmission electron microscopy observations showed that four passes of CGP refines the grain size to ~1.4 μm. Combining the CGP with cold rolling (rolling at a room temperature) brings about further reduction of the grain size and a significant improvement of the mechanical properties. It also changes the tensile deformation behavior of 1050 aluminum. The stress-strain curves of further cold rolled samples displayed a yield point phenomenon. A combination of high strength exceeding 300 MPa and good elongation to failure approaching 20% was obtained for 1050 aluminum after processing by 4 passes of CGP combined with subsequent 80% cold rolling.

Materials Today: Proceedings, 2020
The metallic materials are generally poor dampers of vibration as compared to polymeric materials... more The metallic materials are generally poor dampers of vibration as compared to polymeric materials. However, microstructure refinement was shown to be effective in enhancing the damping properties of metallic materials. In this study, the microstructure of commercial pure (CP) aluminium has been refined using friction stir processing (FSP) further its vibration-damping properties are evaluated using the dynamic mechanical analyser. The CP-aluminium was friction stir processed at 600 rpm and 60 mm/min to achieve fine microstructure. Electron backscattered diffraction (EBSD) and XRD analysis were employed to measure grain size and dislocation density of processed samples, respectively. The stir zone of processed specimens consists of fine and fully recrystallized grains. The results showed that the average grain size is approximately 10 mm after FSP. The hardness of the Al is decreased by 27% after FSP. The damping capacity was studied by the dynamic mechanical analyser (DMA) applying three-point bending mode. The damping capacity of processed specimens at room temperature was measured to be lesser than the as-received specimen. While increasing the temperature, beyond 130 °C, the damping capacity of processed specimens was measured to be better than the as-received sample. The decrease in damping capacity of processed samples at room temperature is due to the reduction of dislocation density while an increase of damping at high temperatures due to an increase in the grain boundary area.

Journal of Materials Engineering and Performance, Jul 5, 2018
Study of tribological characteristics of multi-pass shielding metal arc-welded (SMAW) Armox 500T ... more Study of tribological characteristics of multi-pass shielding metal arc-welded (SMAW) Armox 500T steel joints in comparison with its counterpart base metal was carried out. Series of dry sliding wear tests were carried out as a function of applied loads ranging from 30 to 120 N and sliding distances from 1000 to 6000 m at a constant sliding velocity using pin-on-disk tribometer. It was observed that specific wear rate and lost volume in SMAW joints significantly high compared to Armox 500T base metal in the range of loads and sliding distances considered in the present study. The scanning electron micrographs indicated that wear of Armox 500T base metal occurred due to micro-grooving and adhesion, on the other hand, micro-delamination was observed in SMAW joints. Microstructural investigations revealed that base metal exhibits superior tribological properties as compared to SMAW joints due to the formation of martensite lath in acicular form with coarse and fine precipitates.

Fusion Engineering and Design, Dec 1, 2020
A previously unknown mechanism of bistable behavior in lasers with single-mode cavities is propos... more A previously unknown mechanism of bistable behavior in lasers with single-mode cavities is proposed and analyzed. It is shown that if losses in a cavity exhibit nonmonotonic dependence on frequency, the equation for stationary lasing frequencies can have multiple solutions even in single-mode cavities. In such a case, a system can generate one of several lasing outputs characterized by different frequencies and intensities. All these potential lasing states are stable at the same pumping level, and the choice between them is determined by initial conditions. The latter can be, in principle, controlled by seeding pulses. This mechanism does not depend on such nonlinear effects responsible for most known types of bistability as saturable absorption or cross saturation. An example of a cavity structure, in which such a mechanism can be realized, is presented. Standard lasing equations fail to describe dynamical behavior of such systems; therefore a generalized approach treating dynamic of lasing frequency and intensity on equal footing is developed.
Uploads
Papers by Dr.G.Madhusudhan Reddy