Papers by Ankur Trigunayak
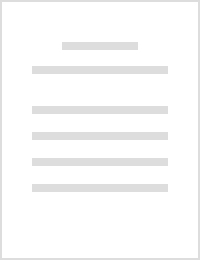
This paper discusses about development of testing methodology where fuze electronics is exposed t... more This paper discusses about development of testing methodology where fuze electronics is exposed to severe gun launch acceleration and softly recovered in decelerating setup so that survivability of fuze electronics can be tested against severe gun launch exclusively. An indoor facility based on ballistic compression concept has been developed. This consist of 40 mm smooth bore gun to launch the projectile and 33m long tube having slotted section, free air section, pressurised air section and incompressible water section separated by composite diaphragms. Parametric study was carried out in NASTRAN & AUTODYN using explicit analysis in Eulerian and Lagrangian domain to simulate supersonic projectile deceleration profile in compressed air column followed by water column. An ogive-nose cylindrical projectile was launched by gun in muzzle velocity range of 350 m/s to 800 m/s and successfully recovered in this designed soft recovery setup. Simulation results were found in correlation with experimental results.
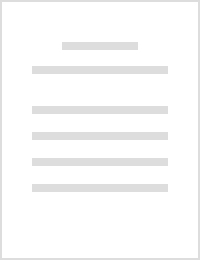
This paper discusses about development of testing methodology where fuze electronics is exposed t... more This paper discusses about development of testing methodology where fuze electronics is exposed to severe gun launch acceleration and softly recovered in decelerating setup so that survivability of fuze electronics can be tested against severe gun launch exclusively. An indoor facility based on ballistic compression concept has been developed. This consist of 40 mm smooth bore gun to launch the projectile and 33m long tube having slotted section, free air section, pressurised air section and incompressible water section separated by composite diaphragms. Parametric study was carried out in NASTRAN & AUTODYN using explicit analysis in Eulerian and Lagrangian domain to simulate supersonic projectile deceleration profile in compressed air column followed by water column. An ogive-nose cylindrical projectile was launched by gun in muzzle velocity range of 350 m/s to 800 m/s and successfully recovered in this designed soft recovery setup. Simulation results were found in correlation with...
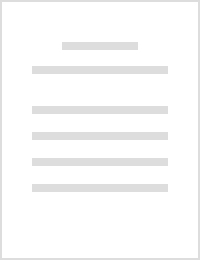
Procedia Engineering, 2017
Abstract This work demonstrates a methodology to analyze small time deformations in conico-cylind... more Abstract This work demonstrates a methodology to analyze small time deformations in conico-cylindrical, multi-material projectile containing explosive material during sub-ordnance velocity impact with the semi-infinite target as hard soil. A 3-Dimensional computational model is developed and analysed using explicit analysis in ANSYS AUTODYN Hydrocode for the Lagrangian domain. The problem was studied for two extreme cases by varying the angle of impact between 00 -150. Deformation and stress propagation patterns are studied in the projectile structure for impact with various targets like sand, concrete, and hard soil. To simulate this millisecond impact phenomenon, Mie-Gruneisen Shock-EOS was selected, strength model for the plastic deformation in ductile materials of the projectile was defined by Johnson –Cook Model and failure criteria defined for failure strain by J-C damage model. To define target as semi-infinite hard soil, compaction model was chosen. Pressure and energy variation with time at different points were observed and analysed for a critical condition for initiation of the explosion. This paper exhibits 3-D impact simulation methodology where deformation in projectile and target both considered for sub-ordnance velocity range impact.

AIP Advances
Polyurethane is a promising candidate for the potting of embedded electronics due to its shock ab... more Polyurethane is a promising candidate for the potting of embedded electronics due to its shock absorbing properties. This paper discusses the less known strain hardening and shock mitigation properties of 4,4 ′-methylenediphenyl diisocyanate based polyurethane under dynamic loading. This study is reported in a strain rate range of 1600-2900 s −1 under compression using a split-Hopkinson pressure bar (SHPB). The experimental stress-strain behavior of polyurethane was modeled with Hollomon's equation to analyze its hardening behavior in dynamic environments. Jointly, the incident, reflected, and transmitted strain signals of the SHPB are analyzed in time and frequency domains to understand the shock absorbing properties of polyurethane. Polyurethane was found to absorb more shock for more intense loading. It was observed to mitigate 81% of shock energy with frequencies up to 10 kHz.
Uploads
Papers by Ankur Trigunayak