Papers by ŞEMSETTİN TEMİZ
International Journal of Adhesion and Adhesives, 2017
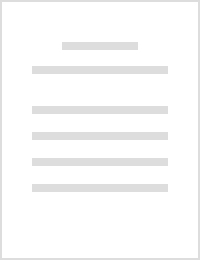
Journal of The Brazilian Society of Mechanical Sciences and Engineering, Dec 10, 2019
In this study, V and X welding grooves were opened to the forehead positions of the AA5182 and AA... more In this study, V and X welding grooves were opened to the forehead positions of the AA5182 and AA7075 aluminum alloy pairs and these alloy pairs were joined with tungsten inert gas (TIG) and metal inert gas (MIG) methods. Three different welding currents were used in joints. Gas flow rates of 12 and 17 l/min at the TIG welding and wire feed rates of 38 and 45 cm/min at MIG welding were selected. The effect of the welding grooves, welding current, gas flow rate and wire feed rate on microstructure and mechanical properties were investigated. Microstructures of welding zones were analyzed by an optical microscope and a scanning electron microscope (SEM). Vickers hardness of these zones was also measured. In addition, tensile and fatigue tests were carried out. Fracture mechanisms of failed specimens were conducted after the tensile tests were examined by using SEM. The highest hardness, tensile and fatigue strengths were obtained from the alloy pairs joined by opening X welding groove with TIG welding method. These values were 89 HV, 262.87 MPa, and 131.5 MPa, respectively. Similarly, the lowest tensile and fatigue strengths were obtained from the alloy pairs joined by opening V welding groove in the TIG welding method. These values were, respectively, 94.48 MPa and 19.1 MPa. However, the minimum hardness value was measured as 58 HV from the alloy pairs joined by opening V welding groove with MIG welding methods. In addition, it was observed on the fracture surfaces that the grain distributions and mechanisms differed depending on the welding methods, welding groove, and welding parameters.

DergiPark (Istanbul University), Aug 1, 2016
There is a considerable interest nanoparticles added structural adhesives, recently. Because, nan... more There is a considerable interest nanoparticles added structural adhesives, recently. Because, nanoparticles improve the mechanical properties of an adhesive and its joint. In this paper, the static strengths of adhesive joints incorporating Al2O3 nanoparticles (% 2 proportions in epoxy adhesive) were compared to those adhesive joints without nanoparticles. Experiments were performed 20 mm, 25 mm and 30 mm overlap lengths, respectively. DP460 epoxy adhesive, Al2O3 nanoparticles and St-37 plates were used for the single lap adhesive joints. The results of the experimental research revealed that average tensile failure load was decreased in the 20 mm and 30 mm overlap bonded joints with nanoparticlereinforced adhesive. However, average tensile failure load was increased (% 5 proportions) in the 25 mm overlap bonded joints with nanoparticle-reinforced adhesive. Moreover, the extension capacity in the joints was decreased in the joints with nanoparticle-reinforced adhesive.
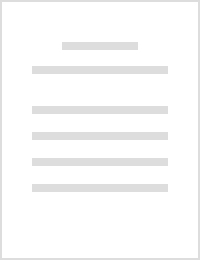
MP MATERIALPRUEFUNG - MP MATERIALS TESTING, May 4, 2023
The mechanical properties of bio-core sandwich composite structures fabricated in different confi... more The mechanical properties of bio-core sandwich composite structures fabricated in different configurations were investigated experimentally and numerically in this study. Balsa woods with thicknesses of 4, 6, 8, and 10 mm were used in the core element. Glass fiber/epoxy composites with 8 and 12 layers at [0°]2s, [0/90°]s, and [±45°]s fiber orientation zones were used on the bottom and top surfaces of the sandwich structure. The effects of external surface fiber arrangement variation, the number of layers, and core thickness increase on the flexural damage load of sandwich structures produced by the vacuum infusion method were investigated. For this purpose, a three-point bending test was applied to the sandwich specimens. Maximum damage load values were determined using the three-point bending test performed in accordance with ASTM C-393 standard. Experimental and numerical data were compared with the finite element model created in the ANSYS package program. As a result of the tests, the damaged specimens were visualized and the types of damage to the balsa wood and composite element were determined.
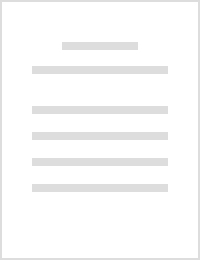
International journal of 3d printing technologies and digital industry, Sep 3, 2022
Today, 3D manufacturing technologies are shown as candidates to replace traditional manufacturing... more Today, 3D manufacturing technologies are shown as candidates to replace traditional manufacturing technologies. In this direction, many studies are carried out to reduce the disadvantages of 3D manufacturing technologies. The first few of these disadvantages are; high production cost, slow production speed, and lower strength values of the produced product compared to traditional methods. Increasing or decreasing the printing speed, which is one of the 3d production parameters, appears as a parameter that will directly affect the strength and production costs of the produced product. For this reason, it is important to determine the effects that may occur on the mechanical properties of the product produced by changing the printing speed in terms of choosing the printing speed according to the intended use of the product. In this study, the effect of desktop Fused Deposition Modelling (FDM) 3D printing speed on mechanical properties was investigated. Tensile test samples were produced using Polylactic Acid (PLA) material at seven different printing speeds using two different 3D printers operated without bed heating. The mass, hardness, surface roughness, and porosity values of the produced samples were determined. Fractured surfaces of the samples were analyzed using Scanning electron microscopy (SEM) images. The results show that an increase in the printing speed decreases the mass, the top surface hardness, and the tensile strength and increases the porosity, the arithmetic average roughness of the products produced with both 3D printers.
Mechanics Based Design of Structures and Machines, Nov 24, 2020
Temiz (2020): Mechanical characterization of composite pipe systems joined using different radii ... more Temiz (2020): Mechanical characterization of composite pipe systems joined using different radii pipes subject to internal pressure, Mechanics Based Design of Structures and Machines,

Gazi Üniversitesi Mühendislik-Mimarlık Fakültesi Dergisi, Nov 20, 2023
Score sandwich panel composite design and manufacturing were done Finite element modeling and... more Score sandwich panel composite design and manufacturing were done Finite element modeling and mechanical tests were performed in three-point bending Bending behaviors were compared Composite panel sandwiches can meet the needs of modern engineering applications with their core geometry and different material selection. This article investigates the deflection behavior of nine Score composite panel sandwich configurations against the damage load calculated due to the three-point bending test and finite element analysis, as can be seen in Figure A. Figure A. Score sandwich panel composite three-point bending ANSYS mechanical analysis and experimental test specimen Purpose: Core geometry and material selection in sandwich panel composite studies show themselves in the current literature. It is thought that the three-point bending behaviors with different geometric dimensions of the Score structure will contribute to the literature. Theory and Methods: The measurement taken for the three-point bending test dimensioning and the models created with the ANSYS mechanical finite element analysis program were applied. Physical experiments and numerical analysis data were compared. Results: Experimental studies and finite element analysis results are compatible. It stands out with its lower density than different core structures. Conclusion: When the damage loads are examined, it is seen that the damage loads and bending stiffness increase as the core thicknesses increase, which gradually reduces the deflection of the plates. This is because as the core materials' thickness increases, the resistance against bending causes less bending and deflection as the moment of inertia increases. As the radii of curvature of the S-shaped core material increase, the damage loads decrease. In the expression (1/=M/EI), the expression (M/EI) decreases as the radius of curvature increases; that is, failure deformations and failure stresses are reached with a lower bending moment and lower damage load. As a result of the analysis, the damage occurs on the core, and the regressions on the adhesive do not cause damage. This provides a broader spectrum for adhesive selection.

Uludağ üniversitesi mühendislik fakültesi dergisi, Dec 17, 2021
Öz: Erimiş yığma modellemesi (FDM), makul bir süre içinde karmaşık şekillere sahip işlevsel parça... more Öz: Erimiş yığma modellemesi (FDM), makul bir süre içinde karmaşık şekillere sahip işlevsel parçalar oluşturma yeteneği nedeniyle hızla büyüyen bir hızlı prototipleme teknolojisidir. FDM yöntemiyle üretim yapan 3 boyutlu yazıcılarla üretilen ürünlerin mekanik özelliklerinin belirlenmesi ve geliştirilmesi, bu imalat yönteminin kullanımının yaygınlaşması açısından büyük öneme sahiptir. Bu çalışmada; Ultimaker 2 Extended 3B yazıcı ile ABS ve PLA malzeme kullanılarak farklı renklerde ve farklı dolgu desenlerinde çekme test numuneleri üretilmiştir. Filament renginin ve dolgu deseninin mekanik özellikler üzerindeki etkileri deneysel olarak araştırılmıştır. Sonuç olarak, kullanılan filament renginin, 3 boyutlu yazıcı ile üretilen çekme numunelerinin mekanik özellikleri üzerinde kayda değer bir etkisinin olmadığı tespit edilmiştir. Kullanılan dolgu desenleri arasından en yüksek çekme mukavemeti değerlerinin "Concentric" dolgu deseniyle üretilen numunelerde olduğu belirlenmiştir.

Kahramanmaraş Sütçü İmam universitesi mühendislik bilimleri dergisi, Dec 3, 2021
3B yazıcı ile üretilen ürünlerin çeşitli parametrelere göre mekanik özelliklerinin tespit edilmes... more 3B yazıcı ile üretilen ürünlerin çeşitli parametrelere göre mekanik özelliklerinin tespit edilmesi, bu ürünlerin kullanılacakları yerlere göre üretim parametrelerinin seçilebilmesi açısından önem kazanmaktadır. Bu çalışmada; Ultimaker 2 Extended 3B yazıcıda ABS (Akrilonitril Bütadien Stiren) ve PLA (Polilaktik Asit) malzeme ile farklı tabla ve nozul sıcaklıkları kullanılarak çekme test numuneleri üretilmiştir. Tabla ve nozul sıcaklıklarının mekanik özellikler üzerindeki etkileri araştırılmıştır. Üretilen numunelerin kütleleri, sertlikleri, yüzey pürüzlülükleri ölçülmüş ve üretilen numunelere çekme testi yapılmıştır. 3B yazıcı ile üretilen çekme numunelerinin boyutlandırılmasında ASTM D638-14 standardı kullanılmıştır. Yapılan testler sonucunda ABS ve PLA malzemelerin her ikisinde de farklı tabla sıcaklıklarının kütle, sertlik, yüzey pürüzlülüğü, çekme dayanımı ve uzama bakımından çok fazla bir etkisinin olmadığı belirlenmiştir. Ayrıca ABS ve PLA malzemelerle üretilen çekme numunelerinde nozul sıcaklığının düşmesiyle kütle, üst yüzey sertlik ve çekme dayanımı değerlerinin azaldığı, aritmetik ortalama pürüzlülük değerlerinin arttığı, alt yüzey sertlik ve uzama değerlerinde ise kayda değer bir değişimin olmadığı tespit edilmiştir. Anahtar Kelimeler: 3 boyutlu (3B) yazıcı, eriyik yığma modelleme (EYM), çekme testi, sertlik ve pürüzlülük ölçümleri, yazdırma sıcaklığı.

Journal of The Faculty of Engineering and Architecture of Gazi University, Sep 12, 2021
Production with fused deposition modelling (FDM) method in 3D printer The effect of printing sp... more Production with fused deposition modelling (FDM) method in 3D printer The effect of printing speed on the mechanical properties of the manufactured product Imaging of breaking regions with scanning electron microscopy (SEM) In this study, tensile test specimens have been produced using ABS and PLA material at different printing speeds with Ultimaker 2 Extended 3d printer. The effect of printing speed on mechanical properties has been investigated. Masses, hardness and surface roughness of the produced samples have been measured, porosity values have been calculated and tensile test has been performed on the produced samples. After the tensile test, images have been taken by scanning electron microscopy (SEM) from the breaking regions of samples. Figure A. Stress-strain curves of samples produced at different printing speeds Purpose: This study has been carried out to determine the change in the mechanical properties of the products produced with the Ultimaker 2 Extended 3D printer, which produces with the Fused Deposition Modeling (FDM) method, with the printing speed. Theory and Methods: In this study, tensile test specimens have been produced at different printing speeds with FDM 3D printer. The effect of printing speed on mechanical properties has been investigated. The ASTM D638-14 standard has been used for sizing the tensile specimens. Tensile test has been applied to the produced samples, and after the tensile test, scanning electron microscopy (SEM) images have been taken from the breaking regions. Results: It has been determined that the tensile strength of the samples produced with PLA material are higher than the samples produced with ABS material, and the elongation at break values of the samples produced with ABS material are higher than the samples produced with PLA material. Conclusion: It has been determined that the mass, porosity, hardness, arithmetic average roughness and tensile strength values of the samples produced with ABS material did not change much with the increase in printing speed. However, it has been determined that the mass, hardness and tensile strength values decreased, and the porosity and arithmetic average roughness values increased of the samples produced with PLA material with the increase in printing speed.
Journal of Adhesion Science and Technology, 2005
Abstract: This paper presents an approach to predicting the failure and strength of joints bonded... more Abstract: This paper presents an approach to predicting the failure and strength of joints bonded with a film-type adhesive (FM 73) using non-linear finite element method. First, lap-shear tests on Single-Lap Joints (SLJs) with different adherend thicknesses and overlap ...

Çukurova Üniversitesi Mühendislik Fakültesi Dergisi, Jun 30, 2022
Honeycomb structures are frequently used in many constructions today. For this reason, the invest... more Honeycomb structures are frequently used in many constructions today. For this reason, the investigation of the mechanical properties of products produced from honeycomb structures is a current issue. In this study, the bending strengths of sandwich structures with honeycomb core produced with a threedimensional printer using ABS and PLA materials were experimentally investigated. In the experiments, the effect of the cell diameter change of the honeycomb core on the bending strength was investigated experimentally in the sandwich structures. For this purpose, experiments were carried out for three different cell diameters. A total of eighteen three-point bending tests were applied, with each experiment repeated three times. In addition, positioning equipment has been specially designed and produced to increase the reliability of the experiments. As a result of the experiments carried out, force-elongation curves were obtained. It has been determined that the samples produced from PLA material are more durable than ABS samples. In addition, it was determined that the samples with a cell diameter of 9 mm had the highest strength, while the samples with a cell diameter of 12 mm had the lowest strength for both materials.
El-cezeri, Sep 30, 2019
The vacuum infusion method is used in the production of ballistic composite materials, in the rep... more The vacuum infusion method is used in the production of ballistic composite materials, in the repair of aircraft parts and in the production of layered hybrid composite materials. In this study, production of hybrid composite materials including apricot kernel shell powder, hazelnut shell powder, walnut shell powder and graphene nanopowder added layer were made by vacuum infusion method. Layered hybrid composite samples with pure graphene nanopowder added and different shell powder added were produced. Then the produced hybrid composite samples were subjected to ballistic experiments. Due to the security, only the photographs of the ballistic test results were allowed to be shared.
Composites Part B-engineering, Dec 1, 2017
DergiPark (Istanbul University), Mar 18, 2014
Klasik çift takviyeli yapıştırma bağlantılarında dış yüzeye yapıştırılan yama özellikle hava araç... more Klasik çift takviyeli yapıştırma bağlantılarında dış yüzeye yapıştırılan yama özellikle hava araçlarında dış yüzeyde hava direncine sebep olmaktadır. Bu direnci ortadan kaldırmak için yamalar yapıştırılan parçanın içine gömülürler. Bu çalışmada çift takviyeli yamaları gömülü yapıştırma bağlantılarının dört nokta eğilme altındaki davranışı ve yapıştırma bağlantılarında parça kalınlığının etkisi sonlu elemanlar yöntemiyle (SEY) incelenmiştir. Üç farklı kalınlıktaki (4.8, 5.6 ve 6.4 mm) AA 2024-T3 alüminyum parça ve 0.4 mm kalınlık ve 15 mm bindirme uzunluğunda yay çeliği yama ile çift taraflı yapıştırılmışlardır. Yapıştırıcı olarak SBT 9244 kullanılmıştır. Parça kalınlığının gerilme dağılımı üzerinde önemli etkisi olduğu görülmüştür.

Research Square (Research Square), Nov 15, 2021
It is not possible to increase the surface quality of non-standard gears with curved involute too... more It is not possible to increase the surface quality of non-standard gears with curved involute tooth profile produced by 5-axis CNC milling method with standard gear grinding methods due to curved tooth profiles. In this study, the possibilities of increasing the surface quality of non-standard gears with curved involute tooth profile were investigated in order to expand their use in the industry. For this purpose, the target model was produced by using the mathematical parametric equations of the involute curve that forms the profile form of a tooth in the CAD environment. By using the target model, manufacturing codes were derived in the CAM environment, and gears with curved involute tooth profile were produced on a 5-axis CNC machine. Then these gears; The possibilities of increasing the tooth profile surface quality were investigated by applying four different methods, such as precision finishing, corunning in oil, co-running in oil with SiC added, and grinding on a 5-axis CNC machine with a finger grinding tip specially produced for gears. In the oil co-run method, considering the running-in stage for each method, the gears were tested with the help of the designed gearbox, at a revolution speed of 670 rpm, by turning a total of 150,000 turns in 6 periods of 25,000 turns. In the co-start method, the gears at the beginning of the test and at the end of each period; thermal records, noise analysis, photographic records, surface roughness values (Ra, Rz) were measured. In the cooperation methods applied to increase the surface quality, the tooth surface of the gears at the beginning of the test and at the end of each period; photographic records, surface roughness values (Ra, Rz) were measured, noise levels were measured during the test and thermal records were taken. Similarly, in precision machining and grinding methods, photographic recordings of the tooth surface were taken, surface roughness (Ra, Rz) was measured, micrographs were taken in SEM and analyzed after the process. As a result of the tests and analyzes carried out; It has been observed that the surface quality is the best in the process performed using a specially produced finger grinding tip and a CNC grinding machine.

Journal of The Faculty of Engineering and Architecture of Gazi University, Jan 12, 2023
Low-velocity impact test samples production with additive manufacturing (AM) method in 3D printer... more Low-velocity impact test samples production with additive manufacturing (AM) method in 3D printer Impact tests for polymer materials Effect of cell width and cell wall thickness on impact strength In this study, the low-velocity impact performances of sandwich composites in honeycomb geometry with three different cell widths and cell wall thicknesses but close surface areas were investigated. Three different cell width and cell wall thickness sizes of the core produced in the 3D printer and the cross-sectional views of the samples after the impact test are shown in Figure A. Figure A. Three honeycomb cell widths and cell wall thicknesses used in the study and cross-sectional views of the samples after the impact test Purpose: The main aim of this study is to reveal the effects of different cell widths with similar surface areas on the low-velocity impact behavior of 3D printed sandwich composite test specimens. Theory and Methods: The cores of the sandwich composites were produced using a 3D printer using the additive manufacturing method. The tests of the samples were carried out according to the ASTM D7766 impact test standard by bonding the cores with CFRP plates. Impact behavior of samples with different cell widths at impact energies of 30J, 40J, 60J, 80J and 100J were presented with graphics and figures. Results: In the impact tests, as the impact energy increased, the damage height in the samples increased. While the striker perforated the top surface at 60J impact energy and damaged the core, it only damaged the bottom surface at 80J impact energy. At 100J impact energy, it completely perforated the sample. Conclusion: The behavior of the test samples produced in the 3D printer against five different impacts was determined.
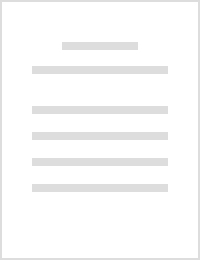
Polymers and Polymer Composites
The present study focuses on maximum compressive force of honeycomb structures produced from poly... more The present study focuses on maximum compressive force of honeycomb structures produced from polylactic acid (PLA) and acrylonitrile butadiene styrene filament using an Ultimaker hot plate 3D printer. A honeycomb structure with an equal surface area and three different cell sizes and wall thickness was designed. The samples were produced with a cell width (d) of 6 mm, 9 mm, 12 mm, a cell wall thickness (t) of 0.8 mm, 1.2 mm, 1.6 mm and a cell height (h) of 10 mm, 20 mm and 30 mm for each cell width, respectively. The produced samples were weighed in order to calculate their porosity percentages. During the compression test, the highest compressive force was obtained from the samples produced from PLA filament with a cell height of 10 mm, a width of 12 mm and a wall thickness of 1.6 mm. Similarly, a detailed finite elements analysis of three structures with different cell widths and thicknesses using ANSYS® software yielded results similar to the experimental study. ANSYS® results we...
MP MATERIALPRUEFUNG - MP MATERIALS TESTING, Nov 29, 2022
Uploads
Papers by ŞEMSETTİN TEMİZ