Papers by Jamshid Ghaboussi
CRC Press eBooks, May 11, 2018
CRC Press eBooks, May 11, 2018
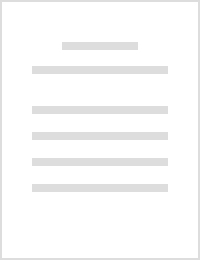
Ballast, typically comprising large sized aggregate particles with uniform gradation, is an essen... more Ballast, typically comprising large sized aggregate particles with uniform gradation, is an essential layer in the railroad track substructure. Functions of ballast include facilitating load distribution and drainage, maintaining track geometry and track stability, and providing track resilience and noise absorption. Throughout its service life, ballast goes through changes in gradation and particle shape properties due to aggregate breakdown/degradation. In United States freight lines, mineral aggregate breakdown/degradation has been reported as the main mechanism causing ballast fouling, which covers up to 76% of all the fouling cases. To investigate the effects of ballast aggregate breakdown and degradation on the mechanical behavior, a series of Los Angeles (LA) abrasion tests were performed to generate fouled materials caused by particle degradation under a controlled laboratory environment. In what follows, large-scale triaxial tests were performed on both clean and heavily fouled ballast specimens using a triaxial test device recently developed at the University of Illinois specifically for testing ballast size aggregate materials. The triaxial testing efforts also focused on (a) the effects of gradation considering those finer materials or fines, i.e. particles less than 9.5 mm (3/8 in.), generated through ballast degradation and (b) the effects of aggregate shape properties, such as angularity and flatness and elongation, for particles larger than 9.5 mm (3/8 in.). Accordingly, triaxial tests were also performed only on those aggregate particles still kept after the LA abrasion tests larger than 9.5 mm (3/8 in.) in size, which would constitute the skeleton of the fouled ballast layer in the field. The experimental study results indicated that ballast degradation did not necessarily result in significant strength loss from the monotonic compression tests on dry specimens. On the contrary, in most cases, the dry degraded ballast with or without fines yielded higher strength properties than those observed in the new ballast specimens. Smaller particles provided a “stabilizing” effect that caused a strengthening of the aggregate matrix and accordingly, fines served as a “stabilizer” to fill the voids and increase density in the ballast aggregate matrix.
CRC Press eBooks, Aug 1, 2008
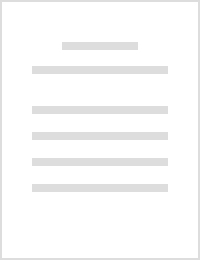
To date, material modelling has involved the development of mathematical models of material behav... more To date, material modelling has involved the development of mathematical models of material behaviour derived from human observation of, and reasoning with, experimental data. An alternative, discussed in this paper, is to use a computation and knowledge representation paradigm, called neural networks, developed by researchers in connectionism (a subfield of artificial intelligence) to model material behaviour. The main benefits of using a neural-network approach are that all behaviour can be represented within a unified environment of a neural network, and that the network is built directly from experimental data using the self-organising capabilities of the neural network. Such a modelling strategy has important implications for modelling the behaviour of modern, complex material, such as composites. In this paper, the behaviour of concrete in the state of plane stress under monotonic biaxial loading and compressive uniaxial cycle loading are modelled with a back=propagation neural network.
Routledge eBooks, Jun 23, 2021
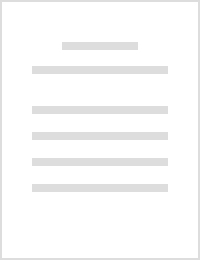
After a brief discussion of neural networks and their potential engineering applications, the aut... more After a brief discussion of neural networks and their potential engineering applications, the author's on-going research in application of neural networks in structural engineering will be discussed. A common task in most engineering problems is the development of mathematical models. Model development with neural networks is achieved through learning. A neural network learns the significant relationships directly from the data. In computational mechanics, neural networks are being used to develop models of material behavior in which neural networks learn the material behavior directly from the experimental results. The author's current research in this area, which will be discussed briefly, is aimed at development of methods for training of neural network material models from the results of structural tests. An other example of the learning replacing mathematical modeling is in the author's research on active control of structures which will also be briefly described. In this research neural networks are trained to learn to control the structure.
Journal of Engineering Mechanics-asce, May 1, 1992
Computing in Civil Engineering and Geographic Information Systems Symposium, 1992
SAE technical paper series, Apr 1, 1994
Neural networks are massively parallel computational models for knowledge representation and info... more Neural networks are massively parallel computational models for knowledge representation and information processing. The capabilities of neural networks, namely learning, noise tolerance, adaptivity, and parallel structure make them good candidates for application to a wide range of engineering problems including diagnostics problems. The general approach in developing neural network based diagnostic methods is described through a case study. The development
Journal of the Soil Mechanics and Foundations Division, Oct 1, 1973
Abstract: The objective of this paper is to present a method for dynamic stress analysis of satur... more Abstract: The objective of this paper is to present a method for dynamic stress analysis of saturated soil-structures subjected to earthquake loading. The soil is idealized as a fluid saturated porous solid. The coupled equations of motion of the finite element discretized ...
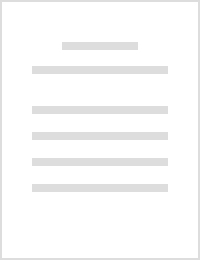
Elsevier eBooks, 1973
Publisher Summary This chapter introduces incompatible displacement modes at the element level in... more Publisher Summary This chapter introduces incompatible displacement modes at the element level in order to improve element accuracy. One of the main causes of inaccuracies in lower-order finite elements is their inability to represent certain simple stress gradients. The same basic method of introducing incompatible displacement modes in order to improve the bending properties can be used in three dimensions. The first eight are the standard compatible interpolation functions. The last three are incompatible and are associated with linear shear and normal strains. The nine incompatible modes are eliminated at the element stiffness level by static condensation. As the three-dimensional element degenerates to the same approximation as in the two-dimensional element, the same improvement in accuracy is obtained. This element has been found to be extremely effective in the analysis of massive three-dimensional structures subjected to bending. One element in the thickness direction of arch dams or thick pipe joints has been found to be adequate.
Journal of the Geotechnical Engineering Division, Feb 1, 1975
Journal of Civil Engineering and Management, Aug 31, 1999
Uploads
Papers by Jamshid Ghaboussi