Papers by Subir Kumar Saha
Techno-Societal 2016, 2017
[1993] Proceedings IEEE International Conference on Robotics and Automation
Automatic guided vehicles with omnidirectional wheels have three degrees of freedom (DOF), their ... more Automatic guided vehicles with omnidirectional wheels have three degrees of freedom (DOF), their full mobility being obtained by virtue of the free rollers around the periphery of the wheels. The choice of the orientation of the roller axes with respect to the wheel axis, along with the wheel orientations with respect to the platform, the number of wheels, etc., are design issues considered here. A design approach based on the isotropy of the underlying Jacobian matrices is reported in this paper.

Lecture Notes in Mechanical Engineering, 2016
Increasing number of universities are offering robotics courses at undergraduate and graduate lev... more Increasing number of universities are offering robotics courses at undergraduate and graduate level. Introductory courses on robot mechanics involve topics from matrix multiplication, coordinate transformations and multivariate equations. Often, the physical meaning of concepts in kinematics and dynamics are lost behind the complicated mathematics involved in them. Hence, it may be the case that some fundamental concepts in robot mechanics may not be very intuitive to teach or learn. In order to appreciate the same, robotics teaching/learning software can be integrated into the curriculum. In this paper, the use of RoboAnalyzer, a 3D model based software for teaching and learning a course in robot mechanics is discussed. An integrated coursework that involves virtual experiments and projects in robot mechanics using RoboAnalyzer is also proposed in the paper. The foreseen advantages of using RoboAnalyzer in classroom and laboratory sessions are also discussed.

Multibody System Dynamics, 2004
The selection of robot manipulator architecture, i.e. the determination of link lengths, their re... more The selection of robot manipulator architecture, i.e. the determination of link lengths, their relative orientations, types of joints, e.g. revolute or prismatic, etc., has been largely done so far by experience, intuition and at most based on the kinematic considerations like workspace, manipulability, etc. Dynamics is generally ignored at this stage even though it is widely used for control and simulation. This paper attempts to introduce a criterion based on the dynamics of a robot manipulator, namely, simplicity of the associated generalized inertia matrix (GIM). Since the GIM influences both the control and simulation algorithms significantly, its fast computation and / or making its shape diagonal will certainly enhance the speed, precision, and stability of the robots. Two measures of simplicity, the computation complexity of the GIM in terms of floating point operations and the computer CPU time of an algorithm where the GIM appears, e.g., the inverse dynamics algorithm, are used here to evaluate a robot arm. The proposed criterion is illustrated with two-link robot arms with revolute and prismatic joints and compared with the two commonly used criteria, namely, the workspace, and manipulability. Finally, an example is taken to select an arm from the two spatial robot architectures, RTX and Stanford.
Journal of Mechanical Design, 1994
This paper follows an accompanying one on the constrained minimization of cam profiles with trans... more This paper follows an accompanying one on the constrained minimization of cam profiles with translating flat-face followers. Here, the corresponding problem for oscillating flat-face followers is discussed. The unconstrained optimization of this type of cam mechanisms, aimed at the minimization of the area of the cam disk, has been reported elsewhere. In this paper we recognize that unconstrained cam-size minimization can lead to profiles with curvature discontinuities, i.e., cusps, which should be eliminated, for they give rise to inadmissibly large contact stresses. The conditions under which curvature discontinuities arise are derived. These conditions lead to a simple constrained minimization procedure, whose application is illustrated with a fully solved numerical example.
IEEE Transactions on Robotics, 2005
The paper presents the dimensional design of a class of parallel manipulators, namely, Hexaslides... more The paper presents the dimensional design of a class of parallel manipulators, namely, Hexaslides. The design of hexaslides is formulated as a multiobjective optimization problem considering workspace and dexterity as dual objectives. As the relative emphasis on workspace and dexterity varies depending on the application, a set of Pareto-optimal solutions is found. The present analysis is a useful tool for designers to select suitable hexaslide parameters for a given application, particularly, in machine tool applications.
This paper presents dynamics algorithms for multibody systems using the concept of Decoupled Natu... more This paper presents dynamics algorithms for multibody systems using the concept of Decoupled Natural Orthogonal Complement (DeNOC) matrices. For this, a multibody system is treated here as an open-loop serial-or tree-types. In fact, it is shown how the knowledge for a serial system can be extended to a tree-type system. The resulting equations are used to obtain recursive inverse and forward dynamics algorithms. The methodology is illustrated using a tree-type four Degree-Of-Freedom (DOF) robotic gripper and 100-DOF serial-type rope system. It will be shown how efficiency of the proposed algorithm will benefit as the DOF of a system becomes very large.

IUTAM Symposium on Intelligent Multibody Systems – Dynamics, Control, Simulation, 2019
This paper discusses a general procedure for creating a computer-aided design (CAD) model of an e... more This paper discusses a general procedure for creating a computer-aided design (CAD) model of an existing commercial sheep hair shearing device for simulation purpose. In this paper, simulation was carried out using the commercial software RecurDyn while the CAD models of the components of the device were created using SolidWorks software. Note that the mechanism in the device can be identified as an RCCR spatial four-bar linkage which was also modeled analytically from its kinematics point of view. The dynamic equations of motion were developed using the concept of the cut-joint approach and the Decoupled Natural Orthogonal Complement (DeNOC) matrices. The equations of motion were then used to simulate the mechanism in Matlab environment. The results were compared to those obtained using the CAD model in RecurDyn environment.
Proceedings of the Advances in Robotics on - AIR '17
Dynamic parameter identification is essential due to the model-based controller, accurate off-lin... more Dynamic parameter identification is essential due to the model-based controller, accurate off-line programming, and validation of simulation results. An identification method is proposed to estimate the torque required for a given trajectory using the concept of equimomental systems which is a dynamically equivalent system of point-masses for the first time. It is experimentally validated by estimating the base parameters and using it for torque reconstruction for a general trajectory on the KUKAiiwa manipulator in order to validate the model identified. Results for the estimated torque using identified model and the torque obtained from robot controller are in the close match.

2020 International Joint Conference on Neural Networks (IJCNN)
Modern robotic researches propose various machine vision methods for accomplishing robotic tasks.... more Modern robotic researches propose various machine vision methods for accomplishing robotic tasks. The recognition quality in these tasks is very important for successful performance. A large number of them use fiducial marker systems as a main element of algorithms. However, only a few researches are comparing standard marker systems. This paper is dedicated to the comparison of AprilTag and ArUco markers resistance to rotations in the presence of synthetic noise. Experiments were conducted in ROS/Gazebo virtual environment in order to provide a fair comparison of marker detection and recognition algorithms while eliminating external environment conditions that influence the algorithms' performance. The presented virtual environments allow collecting a significant amount of data by experiment process automation. Different levels of additive white Gaussian noise were applied to input sensory data in order to simulate the imperfection of real digital cameras. The main contribution of the paper is the systematic comparison of AprilTag and ArUco markers for rotation resistance in the presence of optical sensor noise.

Proceedings of the Advances in Robotics 2019
In this paper, we have performed the kinematic identification and repeatability analysis of LBR i... more In this paper, we have performed the kinematic identification and repeatability analysis of LBR iiwa 7 R800 (7 axis serial link robot) using monocular camera mounted at the end-effector of the robot. We started the process with the camera calibration process to identify intrinsic and extrinsic parameters of the camera used. In order to determine the pose of the end-effector using camera for repeatability analysis, we have used a 9x6 checkerboard for the repeatability experiment and for kinematic identification we have used ArUco markers. For repeatability analysis, we have used poses from ISO 9283 standards. Also we have used dispersion as a statistical means for quantifying the repeatability analysis. Subsequently, we have compared the results of kinematic identification with those from laser sensors and the theoretical CAD data sheet provided for the robot. Also in this paper, the algorithm has been introduced for measuring repeatability under force control mode and consequently, a single point repeatabilty has been evaluated.
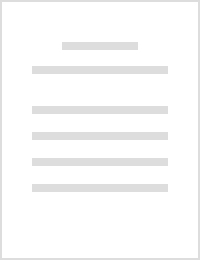
Dynamic model of an underwater robot is nonlinear in hydrodynamic parameters such as added mass, ... more Dynamic model of an underwater robot is nonlinear in hydrodynamic parameters such as added mass, damping, etc. The hydrodynamic coefficients vary with time and configuration of the robot. This paper presents a modeling technique for the Underwater Vehicle-Manipulator System (UVMS) using the DeNOC matrices. Furthermore, as a starting point, some simple hydrodynamic experiments were performed which are used to validate the hydrodynamic simulation in MATLAB environment. For these simulations, the hydrodynamic coefficients were considered to be constant throughout the simulation of the manipulators. Two experiments were performed. In the first experiment, free fall of one-link arm was considered, and in the second, free fall of a two-link manipulator was considered. The simulation results obtained were found in good agreement with the experimental results, even with the constant hydrodynamic coefficients, because of the simple structure of the experiments.
Design Science and Innovation, 2019
This paper emphasizes the failure analysis of comb of a sheep hair shearing device developed by I... more This paper emphasizes the failure analysis of comb of a sheep hair shearing device developed by IIT Delhi. This device is under development to provide a mechanized way to cut woollen fleece of the sheep to minimize the drudgery faced by shearers. After few trails of the device in the field, comb broke. Our purpose was to find the type and cause of the failure on the failed comb so that the quality of the product could be improved. To get the objective done, visual inspection and metallographic study were performed. For metallographic study, SEM (Scanning Electron Microscope) and EDS or EDX (Energy Dispersive Spectroscopy) were used. To avoid this failure, some corrections in the manufacturing process are suggested in this paper.
Design Science and Innovation, 2019
With the aim to reduce drudgery in operation and improve reliability, the design of a conventiona... more With the aim to reduce drudgery in operation and improve reliability, the design of a conventional feet-operated treadle pump have been modified into a solar-powered treadle pump which will be able to lift groundwater to suffice the irrigation needs during periods of scarce rainfall in an economic and environment friendly manner. Dynamic analysis has been performed for the proposed design after taking into account the hydraulic forces and frictional forces encountered while in operation. The results of dynamic simulation has helped us to design the various parts of it for proper functioning. The fabricated model has been tested to evaluate its discharge and efficiency.
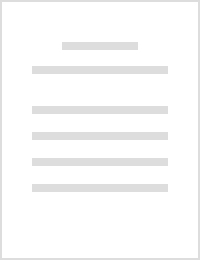
Design Science and Innovation, 2019
The field trials of sheep hair shearing machine indigenously developed at IIT Delhi [1] showed re... more The field trials of sheep hair shearing machine indigenously developed at IIT Delhi [1] showed relatively poor friction and wear characteristics compared to imported devices. Hardness and elastic modulus are the main mechanical properties that control friction and wear. To address these issues, steels of different grades were selected and heat treated to control the metallurgical properties. Hardness (H), elastic modulus (E), and tribological responses were recorded using micro-indentation and Tribometer study, respectively. Worn surfaces were analyzed using scanning electron microscope (SEM). The increase in hardness was associated with decreased wear rate as given by Archard equation. Further, H/E ratio is an important parameter to control the activation of wear mechanisms. Abrasive mode of wear seems to dominate to control the tribological behavior.
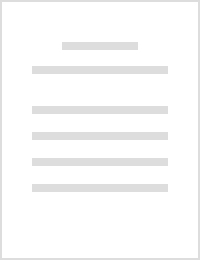
Robotics has become one of the important interdisciplinary course in engineering education. To de... more Robotics has become one of the important interdisciplinary course in engineering education. To describe the position and orientation of a robot, or any part of a robot, several methods are available. One of the commonly used methods is Homogenous Transformation Matrix (HTM), which consists of a Rotation matrix to represent the orientation and a Position vector to represent the position. The HTMs are extensively used in the forward and inverse kinematic formulations of the robots. However, teaching and learning of the concepts related to HTMs remain a challenge using conventional teaching tools. In this paper, a new module developed in RoboAnalyzer software is reported. It has an easy to use interface to visualize the position and orientation of one Coordinate frame with respect to another in a 3D environment. Also, various other useful features are present which help in effective understanding of the HTMs.
It is essential to know the dynamic parameters of the robot for its precise control and simulatio... more It is essential to know the dynamic parameters of the robot for its precise control and simulation. Philosophy of identification is based on finding the model using its input-output data. The identification equation of the manipulator is derived from Newton-Euler equations, using manipulator kinematic, i.e., geometric parameters and joint values as input and joint torque data as output. In this paper, the dynamic parameters are identified for the CAD model provided by the robot manufacturer in simulation. And experimentally for the installed seven degrees of freedom (DOF) robot KUKA-iiwaR800. The variation between the joint torques predicted from the estimated base parameters obtained using CAD model and actual robot are presented. The factors responsible for the variation are also highlighted.
2015 IEEE/RSJ International Conference on Intelligent Robots and Systems (IROS), 2015
Peg-in-tube assembly stands ahead of a more common benchmark task for industrial assembly, i.e., ... more Peg-in-tube assembly stands ahead of a more common benchmark task for industrial assembly, i.e., `pegin-hole'. The robot can easily be deceived to detect the actual hole while performing a `peg-in-tube' task as the tube has a surrounding pocket that cannot support the peg. The paper presents a thorough geometrical analysis of the `peg-in-tube' assembly process, and proposes a novel algorithm based on depth measurements of peg center to perform `peg-in-tube' task. The results are demonstrated on a KUKA KR5 Arc industrial robot with a chamferless cylindrical peg and a tube having a minimum clearance of 0.10 mm.
Proceedings, 1989 International Conference on Robotics and Automation, 1989
A systematic method for the kinematic and dynamic modeling of a two-degree-of-freedom (DOF) autom... more A systematic method for the kinematic and dynamic modeling of a two-degree-of-freedom (DOF) automatic guided vehicle (AGV) is presented. This type of methodology can be used to analyze, design, simulate, and control any kind of rolling robots. The concept of orthogonal complement is used to develop the dynamical equations of motion. The vehicle is analyzed for simulation purposes. Simulation results
Contents Contents Definition of Robot Definition of Robot • What is a robot? Robit (Check word)->... more Contents Contents Definition of Robot Definition of Robot • What is a robot? Robit (Check word)-> Work Robota (Slav word)-> Menial or slave labour Got publicity from the play Rossum's Rossum's Universal Robots (RUR) [1921] Universal Robots (RUR) [1921]
Uploads
Papers by Subir Kumar Saha