Papers by Alankar Alankar

A continuum grain boundary model is developed that uses experimentally measured grain boundary en... more A continuum grain boundary model is developed that uses experimentally measured grain boundary energy data as a function of misorientation to simulate idealized grain boundary evolution in a 1-D grain array. The model uses a continuum representation of the misorientation in terms of spatial gradients of the orientation as a fundamental field. The grain boundary energy density employed is non-convex in this orientation gradient, based on physical grounds. A simple gradient descent dynamics of the energy is utilized for idealized microstructure evolution, which requires higher-order regularization of the energy density for the model to be well-set; the regularization is physically justified. Microstructure evolution is presented using two plausible energy density functions, both defined from the same experimental data: a `smooth' and a `cusp' energy density. Results of grain boundary equilibria and microstructure evolution representing grain reorientation in one space dimensio...
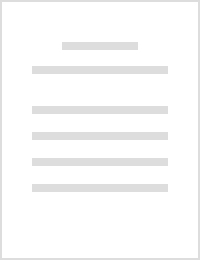
Accurate prediction of cladding mechanical behavior is a key aspect of modeling nuclear fuel beha... more Accurate prediction of cladding mechanical behavior is a key aspect of modeling nuclear fuel behavior, especially for conditions of pellet-cladding interaction (PCI), reactivity-initiated accidents (RIA), and loss of coolant accidents (LOCA). Current approaches to fuel performance modeling rely on empirical constitutive models for cladding creep, growth and plastic deformation, which are limited to the materials and conditions for which the models were developed. To improve upon this approach, a microstructurally-based zirconium alloy mechanical deformation analysis capability is being developed within the United States Department of Energy Consortium for Advanced Simulation of Light Water Reactors (CASL). Specifically, the viscoplastic self-consistent (VPSC) polycrystal plasticity modeling approach, developed by Lebensohn and Tomé, has been coupled with the BISON engineering scale fuel performance code to represent the mechanistic material processes controlling the deformation behavior of light water reactor (LWR) cladding. A critical component of VPSC is the representation of the crystallographic nature (defect and dislocation movement) and orientation of the grains within the matrix material and the ability to account for the role of texture on deformation. A future goal is for VPSC to obtain information on reaction rate kinetics from atomistic calculations to inform the defect and dislocation behavior models described in VPSC. The multiscale modeling of cladding deformation mechanisms allowed by VPSC far exceed the functionality of typical semi-empirical constitutive models employed in nuclear fuel behavior codes to model irradiation growth and creep, thermal creep, or plasticity. This paper describes the implementation of an interface between VPSC and BISON and provides initial results utilizing the coupled functionality.

Journal of Engineering Materials and Technology, 2012
In latent interactions of dislocations, junction formation is one of the most important phenomena... more In latent interactions of dislocations, junction formation is one of the most important phenomena that contribute to the evolution of strength. In this work, the latent hardening coefficients for pure aluminum are estimated using 3D multiscale dislocation dynamics program (MDDP). Three well-known junction configurations, namely, the Hirth lock, the glissile junction, and the Lomer lock, are studied using 3D discrete dislocation dynamics simulations. The evolution of strength is discussed as a function of the resolved shear stress (RSS) and the number of junctions for the three junctions investigated. Hirth lock and Lomer lock are found to be the weakest and strongest junctions, respectively. Collinear reaction of dislocations does not form a junction but causes a higher strength than a Lomer lock. Quantitative and qualitative results are compared with those found in the literature.
This chapter contains sections titled: Introduction Crystal Kinematics Constitutive Law Dislocati... more This chapter contains sections titled: Introduction Crystal Kinematics Constitutive Law Dislocation Density Based Framework Grain Boundary Effect Uniaxial Tensile Test Simulation Results and Concusions IntroductionCrystal KinematicsConstitutive LawDislocation Density Based FrameworkGrain Boundary EffectUniaxial Tensile TestSimulation Results and Concusions
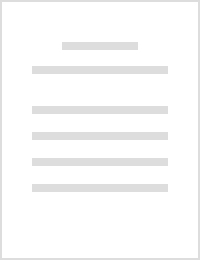
A crystal plasticity finite element model (CPFEM) for bcc single crystals.Incorporation of the di... more A crystal plasticity finite element model (CPFEM) for bcc single crystals.Incorporation of the different velocities of edge and screw dislocations.Effect of dislocation velocities on formability of electrodeposited α-iron sheet.Improved understanding of metal forming process based on dislocation theory.We present a single crystal plasticity model based on edge and screw dislocation densities for body centered cubic (bcc) crystals. In a bcc crystal screw dislocations experience high lattice friction due to their non-planar core. Hence, they have much slower velocity compared to edge dislocations. This phenomenon is modeled by accounting for the motion of screw dislocations via nucleation and expansion of kink-pairs. The model, embedded as a constitutive law into a crystal plasticity framework, is able to predict the crystallographic texture of a bcc polycrystal subjected to 70%, 80% and 90% thickness reduction. We perform a parametric study based on the velocities of edge and screw dislocations to analyze the effect on plastic anisotropy of electro-deposited pure iron with long needle-shaped grains having sharp crystallographic <1 1 1>//ND texture (ND: normal direction). The model shows a large change in the r-value (Lankford value, planar anisotropy ratio) for pure iron when the texture changes from random to <1 1 1>//ND. For different simulated cases where the crystallites have an orientation deviation of 1°, 3° and 5°, respectively, from the ideal <1 1 1>//ND axis, the simulations predict r-values between 4.0 and 7.0 which is in excellent agreement with data observed in experiments by Yoshinaga et al. (ISIJ Intern., 48 (2008) 667–670). For these specific orientations of grains, we also model the effect of long needle shaped grains via a procedure that excludes dislocation annihilation.
In this work microstructure evolution in a columnar polycrystal of pure aluminum is studied using... more In this work microstructure evolution in a columnar polycrystal of pure aluminum is studied using a microstructure sensitive crystal plasticity finite element model (CPFEM). In the model, based upon the kinematics of crystal deformation and dislocation interaction laws, dislocation generation and annihilation are modeled. Dislocation densities evolve in the form of closed loops and are tracked as state variables, leading to spatially inhomogeneous dislocation densities that show patterning in the dislocation structures. The hardening law is based on the strength of junctions between dislocations on specific slip systems. The CPFEM model is able to show the anisotropic hardening behavior of aluminum single crystals. The measures of accumulated plastic strain in the experiment and the simulation are compared with varying degrees of success.
We present a crystal plasticity model that incorporates cross-slip of screw dislocations explicit... more We present a crystal plasticity model that incorporates cross-slip of screw dislocations explicitly based on dislocation densities. The residence plane of screw dislocations is determined based on a probability function defined by activation energy and activation volume of cross-slip. This enables the redistribution of screw-dislocations and dislocation density patterning due to the effect of stacking fault energy. The formulation is employed for explaining the cross-slip phenomenon in aluminium during uniaxial tensile deformation of 100 single crystal and a single slip orientation of single crystal, and compare the results with experimental observations. The effect of cross-slip on the stress–strain evolution is seen using this explicit treatment of cross-slip.
The current work examines deformation at grain boundaries from an experimental viewpoint. The ori... more The current work examines deformation at grain boundaries from an experimental viewpoint. The orientation images of a pseudointernal surface during interrupted channel die deformations of a Cu bicrystal show the evolution of lattice orientation and crystallite fragmentation near the grain boundary. The experiments demonstrate that a region near the boundary is influenced strongly by neighboring grain deformation and lends support to the development of deformation models that include the effects of boundary character and nonlocal slip system interaction. Two crystal plasticity models of the experiment were implemented with a limited degree of success in modeling the observed behavior.

Materials Science and Engineering: A, Jan 1, 2010
Over the past decade thermomechanical models of the direct chill (DC) casting process have been d... more Over the past decade thermomechanical models of the direct chill (DC) casting process have been developed in an effort to mitigate casting defects such as hot tearing as well as to develop a more scientific understanding of the thermal stress and strains which develop during the casting process. A key input to these models is the constitutive behavior of the material in the solid state under thermomechanical conditions that are typical of those experienced during DC casting (strain rates from 1 × 10−1 s−1 to 1 × 10−5 s−1 and temperatures from solidus down to room temperature). This research work presents use of an empirical model (the extended Ludwik equation) to predict the high and low temperature constitutive behavior of aluminum alloys in the solid state under deformation conditions relevant for DC casting. The effect of temperature, strain and strain rate has been studied for three commercially important alloys, namely: AA3104, AA5182 and AA6111. Material parameters used in the constitutive equation were calculated based on experimental measurements using a Gleeble 3500. To validate the constitutive equations developed, complex thermomechanical history tests were performed using the Gleeble 3500 that more closely resemble those experienced by the material during industrial DC casting. These measurements were then compared to the material response based on an ABAQUS finite element (FE) simulation of the test which modeled the material behavior using tabular data and included the effects of temperature, strain and strain rate. When using a commercial FE package such as ABAQUS, it was found that strain softening needs to be considered in situations where the temperature is changing during the simulation. An empirical model was developed to account for strain softening which occurs during continuous cooling tests based on the measured work hardening parameter “n”.
Acta Materialia, Jan 1, 2011
A new constitutive plasticity model for prismatic slip in hexagonal α-titanium is developed. In t... more A new constitutive plasticity model for prismatic slip in hexagonal α-titanium is developed. In the concept pure edge and screw dislocation densities evolve on the {101¯0}〈12¯10〉 slip systems. The model considers that the screw dislocation segments have a spread out core, leading to a much higher velocity of edge compared with screw dislocations. This enables the model to describe the observed transition in strain hardening from stage I to stage II in single crystals oriented for prismatic slip. Good agreement is found between the experimentally observed and simulated stress–strain behavior.
Solid State Phenomena, Jan 1, 2010
Abstract A dislocation density based crystal plasticity finite element model (CPFEM) is developed... more Abstract A dislocation density based crystal plasticity finite element model (CPFEM) is developed for aluminum in which dislocation densities evolve on all octahedral slip systems. Based upon the kinematics of crystal deformation and dislocation interaction laws, dislocation generation and annihilation are modeled. The CPFEM model is calibrated for pure aluminum using experimental stress-strain curves of pure aluminum single crystal from literature. Crystallographic texture predictions in plane-strain compression of aluminum ...
Acta Materialia, Jan 1, 2009
A dislocation-density-based crystal plasticity finite-element model (CPFEM) is developed in which... more A dislocation-density-based crystal plasticity finite-element model (CPFEM) is developed in which different dislocation densities evolve. Based upon the kinematics of crystal deformation and dislocation interaction laws, dislocation generation and annihilation are modeled. The CPFEM model is calibrated for pure aluminum using experimental stress-strain curves of pure aluminum single crystal from the literature. Crystallographic texture predictions in plane-strain compression of aluminum are validated against experimental observations in the literature. The framework is implemented in ABAQUS with user interface UMAT subroutine.
Uploads
Papers by Alankar Alankar