Papers by Danial Ghodsiyeh
Mechanisms and Machine Science, 2016
In this work, a numerical lumped model is developed to simulate static characteristics of an exte... more In this work, a numerical lumped model is developed to simulate static characteristics of an externally pressurized grooved air pad. In addition, an experimental study is performed with one sample pad to evaluate the accuracy of the model.
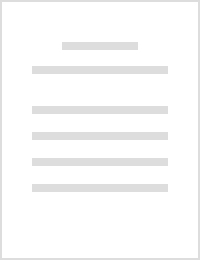
Aero-static thrust bearings offer some distinct advantages in comparison with contact bearings as... more Aero-static thrust bearings offer some distinct advantages in comparison with contact bearings as there is no contact between the moving and stationary parts, thus there is no wear, limited heat generation and long life can be achieved. Moreover, linear positioning control is not affected by the highly nonlinear friction forces, and high precision positioning or high speed can be achieved. The main drawbacks of aerostatic bearings are low stiffness and load capacity and sometimes poor damping in comparison to contact bearings, so that their application in some sectors, e.g. machine tools, is less popular. Active compensation methods can be used as a solution for this problem. Electronic control with piezo actuators give generally good results in both static and dynamic conditions but they are expensive do to use of many sensors and piezo actuators for each pad. In addition in this type of methods, special design is necessary for each air bearing and normal commercial air bearings ca...
The paper shows a prototype of diaphragm pneumatic valve used to increase the stiffness of air be... more The paper shows a prototype of diaphragm pneumatic valve used to increase the stiffness of air bearings. The elaborated numerical model used for the design of the valve and the experimental tests conducted on the prototype are presented and discussed

Indian Journal of Science and Technology
Wire-electro discharge machining (WEDM) has become an important non-traditional machining process... more Wire-electro discharge machining (WEDM) has become an important non-traditional machining process, as it provides an effective solution for producing components made of difficult-to-machine materials like titanium, zirconium, etc., and intricate shapes, which are not possible by conventional machining methods. Due to large number of process parameters and responses lots of researchers have attempted to model this process. This paper reviews the research trends in WEDM on relation between different process parameters , include pulse on time, pulse off time, servo voltage, peak current, dielectric flow rate, wire speed, wire tension on different process responses include material removal rate (MRR), surface roughness (Ra), sparking gap (Kerf width), wire lag (LAG) and wire wear ration (WWR) and surface integrity factors. Furthermore, different types of WEDM methods introduced and discussed. In addition the paper highlights different modelling and optimization methods and discussed their advantage and disadvantage. The final part of the paper includes some recommendations about the trends for future WEDM researches.
Journal of the Brazilian Society of Mechanical Sciences and Engineering

Sādhanā
This article presents the relationship of machining parameters containing pulse-on time (T on), p... more This article presents the relationship of machining parameters containing pulse-on time (T on), pulseoff time (T off), peak current (IP) and servo voltage (SV) on surface integrity characteristics, including white layer thickness (WLT), heat-affected zone (HAZ) and surface crack density (SCD) and also on material removal rate (MRR), after wire electric discharge machining of Ti-6Al-4V. Taguchi's method was utilized to design the experiments, and response surface methodology (RSM) was employed for developing the empirical models. Results indicated that T on and IP played a significant role on surface integrity characteristics. In addition, the microstructure of selected machined samples was analysed using a field emission scanning electron microscope (FESEM) and energy-dispersive X-ray (EDX) analysis. Accuracy of models was examined using residual analysis and confirmation runs. Finally, multi-response optimization of process parameters was obtained using desirability approach. Results can be used to improve the quality of the machined workpiece significantly to fulfil the requirements of the various industries. The novelty of this research is mainly investigation and multi-response optimization of all the surface integrity characteristics at the same time.

Research Journal of Applied Sciences, Engineering and Technology
Verifying the optimal cutting parameters in order to achieve high performance in various kinds of... more Verifying the optimal cutting parameters in order to achieve high performance in various kinds of machinery has always been a critical matter. This research aims to investigate the behavior of three control parameters according to Design of Experiment (DOE) method while WEDM of titanium alloy (Ti6Al4V) is being examined. The sample was cut by an electrode instrument made of brass wire of 0.25 mm diameter. Analysis of Variance (ANOVA) technique was used to find out the parameters affecting the Surface Roughness (SR), Material Removal Rate (MRR) and Sparking Gap (SG). Assumptions of ANOVA were discussed and carefully examined using analysis of residuals. This study has been established as a second-order mathematical model based on the Response Surface Methodology (RSM). The residual analysis and confirmation runs indicate that the proposed models could adequately describe the performance of the factors those are being investigated. The outcomes are particularly useful for scientists and engineers to determine which subset of the process variable can optimize the performance.
Tribology International, 2017
Abstract: Selection of optimal cutting parameters has always been a critical issue to achieve hig... more Abstract: Selection of optimal cutting parameters has always been a critical issue to achieve high-quality in the machining process. In this study Design of Experiment (DOE) method for selection of optimal cutting parameters during WEDM of titanium alloy (Ti6Al4V) is ...

Applied Mechanics and Materials, Feb 6, 2013
Drilling is a hole making process on machine components at the time of assembly work, which are i... more Drilling is a hole making process on machine components at the time of assembly work, which are identify everywhere. In precise applications, quality and accuracy play a wide role. Nowadays' industries suffer due to the cost incurred during deburring, especially in precise assemblies such as aerospace/aircraft body structures, marine works and automobile industries. Burrs produced during drilling causes dimensional errors, jamming of parts and misalignment. Therefore, deburring operation after drilling is often required. Now, reducing burr size is a serious topic. In this study experiments are conducted by choosing various input parameters selected from previous researchers. The effect of alteration of drill geometry on thrust force and burr size of drilled hole was investigated by the Taguchi design of experiments and found an optimum combination of the most significant input parameters from ANOVA to get optimum reduction in terms of burr size by design expert software. Drill thrust influences more on burr size. The clearance angle of the drill bit causes variation in thrust. The burr height is observed in this study. These output results are compared with the neural network software @easy NN plus. Finally, it is concluded that by increasing the number of nodes the computational cost increases and the error in nueral network decreases. Good agreement was shown between the predictive model results and the experimental responses.
Advanced Science Letters, 2013
Journal of the Brazilian Society of Mechanical Sciences and Engineering, 2013
Uploads
Papers by Danial Ghodsiyeh