Papers by Rakesh K . Barik
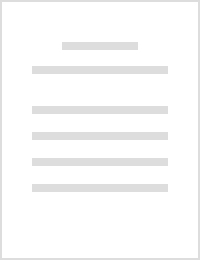
Materials Science and Engineering: A
The present work investigates the micro-mechanisms of cleavage fracture in a low carbon ferritic ... more The present work investigates the micro-mechanisms of cleavage fracture in a low carbon ferritic steel, subjected to Charpy impact test at low temperature. EBSD crack path analysis reveals {100} crystallographic plane as the predominant cleavage plane in ferrite, with occasional cracking along the secondary {110} cleavage plane. {110} cleavage cracking is particularly feasible when the {100} planes within a given grain exhibit significant twist angles with the preceding crack plane. Moreover, the fracture surface also exhibited numerous "tongue" like features that are intermittently aligned parallel to a common <110> crack front, as evidenced from the point EBSD analysis directly on the fracture surface. To illuminate the origin of such intermittent tongues, we performed molecular dynamics fracture simulation on a pure Fe single crystal, considering a (001) edge crack with a large [110] crack front. It was found that the development of intermittent tongues mainly originates from the intermittent nucleation of symmetric {112}<111> type twins across the entire crack front. Such intermittent twin nucleation results in a sinusoidal crack front, characterized by twin boundary cracking in one region and radial expansion of cleavage cracking in the adjacent regions, which can ultimately lead to the formation of tongues on the fracture surface. Finally, based on the simulation results and experimental observations, we propose a step by step mechanism that potentially explains the formation of intermittent tongues when a sufficiently large <110> straight crack front propagates along a {001} cleavage crack plane.

Materialia, 2023
Copper addition in austenitic stainless steel is known to provide good high-temperature strength ... more Copper addition in austenitic stainless steel is known to provide good high-temperature strength through precipitation strengthening. However, the mechanism of such strengthening and its overall contribution to strength in austenitic stainless steels have not been adequately investigated. The present work employs molecular dynamics (MD) simulation to investigate the interaction between an edge dislocation and copper precipitate in austenitic stainless steel. The mechanism controlling the strength was found to be trailing partial detachment for smaller precipitates up to a maximum radius of 3 nm, whereas leading partial detachment controls the strength for larger precipitate sizes, irrespective of the inter-precipitate spacing. Besides, modulus strengthening was identified as the primary strengthening contributor for the coherent Cu precipitate in the present alloy, which was subsequently aligned with the theoretical predictions by the existing Russell-Brown (R-B) model, adopting some modifications. The discrepancy between the simulation results and the original R-B model is attributed to the interaction between the two partial dislocations in presence of the precipitate. The modified R-B model was then used in combination with Thermo-calc and DICTRA predictions to estimate the strength of Cu-added austenitic stainless steel. However, the predictions overestimated the experimental data due to the model's inability to account for the random distribution of precipitates. To address this limitation, a subsequent discrete dislocation dynamics (DDD) simulation was conducted, incorporating a random distribution of Cu precipitates. Finally, the DDD simulation results demonstrated a good match with the experimental results, which can be further extended to other alloy systems as well.

Materials Science and Engineering: A, 2023
The present work investigates the micro-mechanisms of cleavage fracture in a low carbon ferritic ... more The present work investigates the micro-mechanisms of cleavage fracture in a low carbon ferritic steel, subjected to Charpy impact test at low temperature. EBSD crack path analysis reveals {100} crystallographic plane as the predominant cleavage plane in ferrite, with occasional cracking along the secondary {110} cleavage plane. {110} cleavage cracking is particularly feasible when the {100} planes within a given grain exhibit significant twist angles with the preceding crack plane. Moreover, the fracture surface also exhibited numerous "tongue" like features that are intermittently aligned parallel to a common <110> crack front, as evidenced from the point EBSD analysis directly on the fracture surface. To illuminate the origin of such intermittent tongues, we performed molecular dynamics fracture simulation on a pure Fe single crystal, considering a (001) edge crack with a large [110] crack front. It was found that the development of intermittent tongues mainly originates from the intermittent nucleation of symmetric {112}<111> type twins across the entire crack front. Such intermittent twin nucleation results in a sinusoidal crack front, characterized by twin boundary cracking in one region and radial expansion of cleavage cracking in the adjacent regions, which can ultimately lead to the formation of tongues on the fracture surface. Finally, based on the simulation results and experimental observations, we propose a step by step mechanism that potentially explains the formation of intermittent tongues when a sufficiently large <110> straight crack front propagates along a {001} cleavage crack plane.

Metals
The present study investigates the relative effect of B and N concentrations and the austenitizat... more The present study investigates the relative effect of B and N concentrations and the austenitization temperature on the microstructure and mechanical properties (tensile and Charpy impact) of modified 9Cr-1Mo (P91) steels. Initially, a B-free P91 steel (with 500 ppm N) and four different B-containing steels (25–100 ppm) with varying N concentrations (20–108 ppm) were hot-rolled, normalized from different austenitization temperatures (1000–1100 °C/1 h) and finally tempered at 760 °C for 1 h. A Charpy impact test shows that the ductile–brittle transition temperature (DBTT) of all the B-added steels decreases with an increase in the austenitization temperature, where the 100 ppm B steel offers the lowest DBTT (−85 °C). Similarly, the strength increases with the increase in the austenitization temperature (1100 °C), with a slight drop in ductility. The influence of precipitates on the microstructure and mechanical properties is explained considering the B enrichment at the precipitates ...
Materialia, 2023
This paper proposes the efficacy of martensite nano-twins in a medium carbon armor grade martensi... more This paper proposes the efficacy of martensite nano-twins in a medium carbon armor grade martensitic steel on the cleavage crack resistance at a local scale. Concurrent analyses through electron channeling contrast imaging and electron back scattered diffraction techniques reveal that fine twins of width less than 10 nm are ineffective in deflecting the crack, propagating in the {100} cleavage plane. Coarse twins, on the other hand, resist the crack propagation by deflecting the crack through stepwise crack path propagations, e.g., a combination of matrix-twin {100} cleavage cracking or a combination of matrix {100} and twin-matrix {112} interface cracking. The interfacial cracking along the {112} twin boundaries is attributed to the presence of carbon enriched clusters along the twin boundaries.

Computational Materials Science, 2023
Screw dislocation motion in bcc Fe plays an important role in establishing the strong temperature... more Screw dislocation motion in bcc Fe plays an important role in establishing the strong temperature and strain rate sensitivity of flow stress, which in turn promotes the ductile to brittle transition phenomenon in steel. Addition of solute atoms, possessing attractive interaction with screw dislocations, is believed to reduce the flow stress sensitivity of Fe. The present work intends to study the effect of Ni and Cu solute atom distribution on the screw dislocation motion in bcc Fe using molecular statics (MS) and molecular dynamics (MD) simulations. MS simulation results predict that the local distribution of Ni atoms around the screw dislocation greatly influences the Peierls stress of Fe at 0 K temperature, while Cu atom distribution has marginal effect. Moreover, the presence of Ni/Cu atoms ahead of the dislocation line helps to reduce the Peierls stress due to the dislocationsolute attractive interaction. MD simulation was performed on random Fe-Ni and Fe-Cu alloys to determine the effect of solute concentration on the temperature sensitivity of flow stress of Fe. The results showed that addition of Ni/Cu reduces the flow stress sensitivity of Fe by inducing solid solution softening effect at low temperature regime. Ni was found to be more effective than Cu in reducing the flow stress temperature sensitivity of Fe. The rationale behind the softening action of Ni and Cu is discussed in terms of changing the differential displacement plot and unstable stacking fault energy of Fe.

Materialia, 2022
Ductile to brittle transition (DBT) is a well-known phenomenon responsible for deteriorating the ... more Ductile to brittle transition (DBT) is a well-known phenomenon responsible for deteriorating the low temperature fracture toughness of ferritic steels. It is unambiguous to state that the transition phenomenon is a direct consequence of the strong temperature and strain rate sensitivity of flow stress, which in turn is regulated by the thermally activated motion of screw dislocation at the atomic scale. Due to very high Peierls stress, screw dislocation motion is accompanied by the nucleation and propagation of kink-pairs along the dislocation line. Thus, the activation energy required for kink-pair nucleation is an essential ingredient for correctly predicting the flow stress sensitivity and hence the ductile to brittle transition temperature (DBTT) of ferritic steel. However, experimental determination of kink-pair activation energy is rather tedious and there exists a strong discrepancy between atomistic simulation results (using Density Functional Theory and empirical potentials). Therefore, the present review is aimed at understanding the mechanism of screw dislocation motion in BCC Fe lattice and comparing the results obtained for kink-pair activation energy through experiments and simulations. The effect of different alloying elements on the overall flow stress sensitivity of Fe is also discussed with reference to the interaction of screw dislocation with solute atoms or clusters. Finally, the importance of screw dislocation on predicting the DBTT is explored to identify the present knowledge gaps and the future research directions.

Materials Science and Engineering: A, 2019
Achieving superior impact toughness in high-strength pearlitic steels is extremely desirable and ... more Achieving superior impact toughness in high-strength pearlitic steels is extremely desirable and challenging due to the brittle character of the intervening cementite lamellae. Besides the 'Hall-Petch' type lamellar strengthening, a systematic understanding of various micro-toughening mechanisms through cleavage cracking resistance is essential to develop an integrated microstructure for toughness improvement. In this study, both thermal as well as thermo mechanical processing routes were adopted to correlate the processing and microstructural parameters with the mechanical properties. The prime contribution of pearlite nodule size refinement towards improving the impact toughness is discussed in terms of frequent cleavage crack deflection at the nodule boundaries. Other microstructural parameters controlling the toughness are the pearlite morphology (lamellar or spheroidized), interlamellar spacing and the cementite lamellae orientation with the crack path. It appears that both spheroidized and fine lamellar pearlite are more effective crack arresters than their coarse lamellar pearlite counterparts. Besides, the variation of crack growth resistance with the pearlite lamellae orientation and the ferrite-cementite interface (habit) plane is also presented, relating to the mechanism of interface decohesion.

Metallurgical and Materials Transactions A, 2022
The present study fine tunes the processing route of a eutectoid steel to shape an optimum streng... more The present study fine tunes the processing route of a eutectoid steel to shape an optimum strength–toughness combination through appropriate microstructural design. A fully lamellar coarse pearlite microstructure leads to poor strength and toughness. Hot deformation prior to the isothermal treatment breaks down the lamellar pearlite to a spheroidized structure. Moreover, reducing the hot deformation temperature not only refines the pearlite nodule size but also increases the spheroidized pearlite fraction, which thereby improves the toughness of the steel. However, no proportionate increase in yield strength was obtained due to insignificant change in the interlamellar spacing. Remarkable refinement in lamellar spacing and increase in the spheroidization amount was ensured when the hot deformation was carried out just below the eutectoid temperature, owing to the strain-induced pearlite transformation. The presence of a mixed microstructure of fine lamellar pearlite along with spheroidized pearlite constituents simultaneously improves both the yield strength and toughness of the steel. Optimum strength–toughness combination was attained when the hot deformation strain (just below the eutectoid temperature) was increased up to 45 pct. Subsequent increase in strain creates deformation bands and traces of strain-induced bainite in the microstructure, which again deteriorates the tensile elongation of the steel.

Acta Materialia, 2021
The present paper focuses on the microstructure-based cleavage crack propagation in a Charpy impa... more The present paper focuses on the microstructure-based cleavage crack propagation in a Charpy impact tested fully pearlitic steel by correlating microstructure and crystallography with the overall fracture be- havior. The importance of pearlite lamellae orientation in providing preferred fracture paths is discussed, encompassing the mechanism of interface decohesion and stepwise crack propagation through a math- ematical model simulation. While the {100} cleavage cracking is well familiar in pearlitic steels, crack propagation along the {110} crystallographic planes can also prevail in some pearlite colonies or nodules. This is related to suppressing the crack tip dislocation emissions due to restricted slip transferability across the lamellae interfaces. Besides, the strain incompatibility due to large elastic modulus or Schmid factor mismatch across the pearlite nodule boundaries is responsible for triggering internodular cracking in the steel. Connecting the framework of fracture mechanics with the experimental observations, the mechanisms pertaining to different types of tear ridges formed within a pearlite colony are proposed. This certainly illuminates the role of lamellae orientation in the process of crystal bending and shearing at the tear ridges formed within the colonies or at the twist nodule boundaries.
Materials Today: Proceedings, 2020
In the present study, a mathematical model is proposed for the prediction of wear rate of Al-12.6... more In the present study, a mathematical model is proposed for the prediction of wear rate of Al-12.6Si alloybased composites reinforced with in situ TiB 2 (2, 3, 5 wt%) particles by halide salt reaction route. For deducing an empirical relationship for wear rate (pin-on-disc type wear), a multiple regression analysis has been performed to show its dependency on the TiB 2 content of composite and various wear test parameters. From the regression statistics, it is inferred that the wear rate is strongly dependent on the rotating speed of the disc but moderately on the TiB 2 content and applied normal load.

Materials Science & Engineering A, 2019
Achieving superior impact toughness in high-strength pearlitic steels is extremely desirable and ... more Achieving superior impact toughness in high-strength pearlitic steels is extremely desirable and challenging due to the brittle character of the intervening cementite lamellae. Besides the 'Hall-Petch' type lamellar strengthening, a systematic understanding of various micro-toughening mechanisms through cleavage cracking resistance is essential to develop an integrated microstructure for toughness improvement. In this study, both thermal as well as thermo mechanical processing routes were adopted to correlate the processing and microstructural parameters with the mechanical properties. The prime contribution of pearlite nodule size refinement towards improving the impact toughness is discussed in terms of frequent cleavage crack deflection at the nodule boundaries. Other microstructural parameters controlling the toughness are the pearlite morphology (lamellar or spheroidized), interlamellar spacing and the cementite lamellae orientation with the crack path. It appears that both spheroidized and fine lamellar pearlite are more effective crack arresters than their coarse lamellar pearlite counterparts. Besides, the variation of crack growth resistance with the pearlite lamellae orientation and the ferrite-cementite interface (habit) plane is also presented, relating to the mechanism of interface decohesion.
Uploads
Papers by Rakesh K . Barik