Papers by Agathoklis Krimpenis
“Optimizing the Optimization”: A Hybrid Evolutionary-Based Ai Scheme for Optimal Performance
Designs, May 28, 2024
This article is an open access article distributed under the terms and conditions of the Creative... more This article is an open access article distributed under the terms and conditions of the Creative Commons Attribution (CC BY

Machines
Hybrid Manufacturing technologies enable the manufacturability and high manufacturing efficiency ... more Hybrid Manufacturing technologies enable the manufacturability and high manufacturing efficiency of innovative part designs comprising high complexity features which could not otherwise be manufactured in a single or a small number of steps. This study proposes the design of an industrial-grade low-cost fully automated multi-axis hybrid Additive and Subtractive CNC machine for non-metallic parts. It combines operations of a six-axis CNC machining center with a six-axis extrusion 3D printer with automated tool head change for processing parts made of polymer and special 3D printing materials (e.g., carbon fiber reinforced filaments). The design process includes static, dynamic and harmonic response Finite Element Analysis to optimize its structural strength and at the same time to reduce machine component costs down to a few thousand euros for all included components and subsystems, thus making it viable for industrial purposes. In investigated loading scenarios, analysis results sho...
Springer International Publishing eBooks, 2023
The use of general descriptive names, registered names, trademarks, service marks, etc. in this p... more The use of general descriptive names, registered names, trademarks, service marks, etc. in this publication does not imply, even in the absence of a specific statement, that such names are exempt from the relevant protective laws and regulations and therefore free for general use.
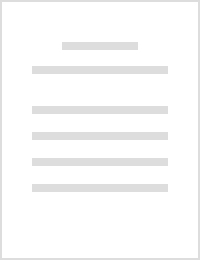
Design and analysis of a desktop multi-axis hybrid milling-filament extrusion CNC machine tool for non-metallic materials
Additive Manufacturing has unlocked the ability to introduce new concepts for parts of very high ... more Additive Manufacturing has unlocked the ability to introduce new concepts for parts of very high complexity to the industrial landscape, which could not be manufactured with traditional manufacturing processes in a single or in a small number of steps. However, surface quality of 3D printed parts and process repeatability are low to medium, at least in an industrial context. This study proposes a new design of a fully automated multi-axis hybrid Additive and Subtractive Computerized Numerical Control machine tool for non-metallic parts, which can overcome the drawbacks of both Additive and Subtractive Numerical Manufacturing. It combines the operation a 5-axis CNC machining center with a 5-axis extrusion 3D printer with automated tool head change, which is able to make parts made of polymer and special 3D printing materials (eg. carbon fiber reinforced filaments) of high complexity which require minimal post-processing to produce the final product in the shortest possible time. The ...
Application of Hybrid Manufacturing processes in microfabrication
Journal of Manufacturing Processes
Βελτιστοποίηση κατεργασιών εκχόνδρισης σε κέντρα κατεργασιών CNC για γλυπτές επιφάνειες πολύπλοκης μορφολογίας με μεθόδους τεχνητής νοημοσύνης
Statistical and Computational Techniques in Manufacturing, 2012
The use of general descriptive names, registered names, trademarks, service marks, etc. in this p... more The use of general descriptive names, registered names, trademarks, service marks, etc. in this publication does not imply, even in the absence of a specific statement, that such names are exempt from the relevant protective laws and regulations and therefore free for general use. While the advice and information in this book are believed to be true and accurate at the date of publication, neither the authors nor the editors nor the publisher can accept any legal responsibility for any errors or omissions that may be made. The publisher makes no warranty, express or implied, with respect to the material contained herein.
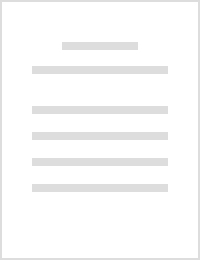
Rough milling optimisation for parts with sculptured surfaces using genetic algorithms in a Stackelberg game
Journal of Intelligent Manufacturing, 2009
ABSTRACT In rough milling of sculptured surface parts, decisions on process parameters concern fe... more ABSTRACT In rough milling of sculptured surface parts, decisions on process parameters concern feedrate, spindle speed, cutting speed, width of cut, raster pattern angle and number of machining slices of variable thickness. In this paper three rough milling objectives are considered: minimum machining time, maximum removed material and maximum uniformity of the remaining volume at the end of roughing. Owing to the complexity of the modelled problem and the large number of parameters, typical genetic algorithms cannot achieve global optima without defining case-dependent constraints. Therefore, to achieve generality, a hierarchical game similar to a Stackelberg game is implemented in which a typical Genetic Algorithm functions as the leader and micro-Genetic Algorithms as followers. In this game, one of the leader’s parameters is responsible for creating a follower’s population and for triggering the optimisation. After properly weighing the three objectives, the follower performs single-objective optimization in steps and feeds the leader back with the objective values as they appear prior to weighing. Micro-Genetic Algorithm (follower) chromosome consists of the distribution of machining slice thickness, while the typical Genetic Algorithm (leader) consists of the milling parameters. The methodology is tested on sculptured surface parts with different properties, and a representative case is presented here.
The International Journal of Advanced Manufacturing Technology, 2005
Product manufacturing on CNC milling machine tools involves a number of machining parameters and ... more Product manufacturing on CNC milling machine tools involves a number of machining parameters and tool geometries. In the case of sculptured or free-form surfaces the number of these parameters can be significantly large and vary according to surface complexity. Minimising the number of parameters is carried out through statistical elimination. Design of experiments (DoE) along with the respective statistical analysis of variance (ANOVA) constitutes a low-cost useful tool in determining suboptimum values for all parameters involved in each milling strategy as well as the most significant of those parameters. DoE was implemented for a particular sculptured surface assessing a variety of roughing and finishing strategies of a CAM simulation software.

The International Journal of Advanced Manufacturing Technology, 2014
Micromachining operations are mainly restricted to precision machining of two-dimensional micropa... more Micromachining operations are mainly restricted to precision machining of two-dimensional microparts, usually performed on microelectrical discharge machining or microlaser computer numerical control (CNC) machine tools. However, micromilling can fully exploit computer-aided design/computer-aided manufacturing (CAM) software abilities, in order to achieve more complex three-dimensional micropart geometries. After fully defining the micromilling process parameters and related constraints, optimization methodologies, such as genetic algorithms, can be coupled with CAM software, thus obtaining optimal process parameters with very small calculation cost. In this study, CNC micromilling process is systematically presented, along with respective micromilling tools and the necessary industrial equipment for the processes. Genetic algorithm code was developed in Visual Basic, which optimizes the process and ultimately yields optimal parameter values, including all process particulars. Two test cases were presented, and results were discussed in terms of micropart quality, production time, and calculation cost.

Models and Techniques, 2012
Extracting CNC machining data on-or off-line demands thorough and careful planning. Exploitation ... more Extracting CNC machining data on-or off-line demands thorough and careful planning. Exploitation of this data can be carried out by statistical methods, in order to obtain the most influential parameters along with their respective level of significance. However, significance of machining parameters varies according to the posed Quality Characteristics at each machining phase. In actual experiments, measuring devices and assemblies are used, and data is recorded in computer archives. To shorten the production time and cost, machining processes are planned on CAM software, especially when complex part geometries, such as sculptured surfaces, are involved. Hence, planning machining experiments using CAM software modules is an efficient approach for experimentation on the actual CNC machine tools. Data extraction and statistical analysis methodologies are presented along with respective machining experimental examples.
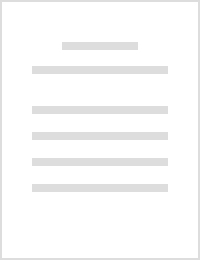
Initialisation improvement in engineering feedforward ANN models
Any feedforward artificial neural network (ANN) training procedure begins with the initialisation... more Any feedforward artificial neural network (ANN) training procedure begins with the initialisation of the connection weights ’ values. These initial values are generally selected in a random or quasi-random way in order to increase training speed. Nevertheless, it is common practice to initialize the same ANN architecture in a repetitive way in order for satisfactory training results to be achieved. This is due to the fact that the error function may have many local extrema and the training algorithm can get trapped in any one of them depending on its starting point based on the particular initialisation of weights. This paper proposes a systematic way for weight initialisation that is based on performing multiple linear regression on the training data. Experimental data from a metal cutting process were used for ANN model building to demonstrate an improvement on both training speed and achieved training error regardless of the selected architecture.

Sculptured surface parts machining is a demanding task even though commercially available CAM sof... more Sculptured surface parts machining is a demanding task even though commercially available CAM software offers a variety of possible strategies and a number of machining planning functions. However, process optimization routines are seldom embedded in CAM software. The present work aims at proposing an optimization method that computes optimal process parameter values for sculptured surface rough machining. The objectives are minimum machining time and maximum material removal, subject to technological constraints imposed by the rough machining process. Optimization is based on multi- objective evolutionary algorithms (EAs), assisted by surrogate evaluation models. In addition, a two-player Nash game optimization was programmed and tested. Software was developed for the interaction between the Application Program Interface (API) of a given CAM system and the optimization tool as well as for the calculation of objective function values. The proposed optimization process was applied to...
HydraX, a 3D printed robotic arm for Hybrid Manufacturing. Part I: Custom Design, Manufacturing and Assembly
Procedia Manufacturing
Balancing multiple criteria in formulation of weighted, single-objective genetic algorithm optimization for CNC machining problems
Advances in Manufacturing
3D parametric design and CNC manufacturing of custom solid wood electric guitars using CAD/CAM technology
Wood Material Science & Engineering
On Systematic CAD/CAM Modeling of Blow Molds for Plastic Bottles
Solid State Phenomena
Flexible Integration of Shape and Functional Modelling of Machine Tool Spindles in a Design/Optimisation Framework
Materials Forming, Machining and Tribology, 2014

The present work deals with the parametric 3D modeling of manufacturing systems and cells, as wel... more The present work deals with the parametric 3D modeling of manufacturing systems and cells, as well as with factory layout issues. Main focus is given on the flexibility of shop-floor production, the shop-floor arrangement and the unobstructed material flow through suitably detailed functional-moving manufacturing systems' 3D models that comprise of CNC machine tools, robots and conveyor belts. Parametric 3D modeling enables the rapid creation of parts, assemblies and systems with an intuitive, model-centric way. Association among design parameters offers flexibility and allows components to be changed and updated according to both product development and production needs. Visualization of production floor performance, material flow simulation, off-line scheduling and virtual machine positioning are some of the major benefits of this concept, while at the same time idle times may be drastically reduced through off-line processes supervision. Different layout scenarios are presented and discussed in terms of performance and efficiency.
Uploads
Papers by Agathoklis Krimpenis