Papers by S Kishore Kumar

Military aircraft engines employ afterburner system for increasing the thrust required during com... more Military aircraft engines employ afterburner system for increasing the thrust required during combat and takeoff flight conditions. V-gutter is employed for stabilisation of the flame during reheat. For fifth generation aero engine the gas temperature at the start of the afterburner is beyond the allowable material limits of the V-gutter so it is required to cool the V-gutter to obtain acceptable creep life. The design of cooling configuration for the given source pressure is worked out for different rib configurations to obtain the allowable metal temperature with minimum coolant mass flow.1D network analysis is used to estimate the cooling mass flow and metal temperature for design flight condition. CFD analysis is carried out for four cooling configurations with different rib orientations. Out of four configurations one configuration is selected for the best cooling configuration.
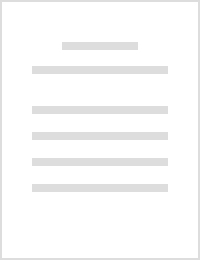
ASME 2013 Gas Turbine India Conference
3D NS analysis is routinely used in the design and analysis of modern turbine stages in the recen... more 3D NS analysis is routinely used in the design and analysis of modern turbine stages in the recent days. One of the key parameters which influence the results of the numerical analysis is the turbulence models. Thus the choice of the turbulence models plays an important role in the 3D NS analysis. In addition to the turbulence models, the grid resolution in the boundary layer also considerably influences the results of the analysis. The objective of the work is to study the choice of turbulence models, inlet free stream turbulence intensity, the eddy length scales and values of y+ on the performance of an axial flow turbine stage of a typical turbofan engine by using ANSYS CFX 3D NS code. The Reynolds Averaged Navier – Stokes (RANS) equations are solved. The governing equations are discretized using finite volume method. The solution algorithm is based on an implicit scheme coupled with multi-grid. Analyses are carried out using three different turbulence models namely k-ε, k-ω and ...

This paper focuses a detailed numerical prediction of non-reacting flow analysis in a practical 1... more This paper focuses a detailed numerical prediction of non-reacting flow analysis in a practical 1/3 scaled model gas turbine afterburner system. The analysis is performed using SIMPLE algorithm in a body-fitted multi-block grid using STAR-CD software. The turbulence is simulated using standard k-e model. The validation of software is carried out in a afterburner model by comparing axial, radial and circumferential velocities at various axial locations. The agreement between the prediction and experimental data are quite reasonable. The analysis is extended to the flow in a practical afterburner system. The afterburner system consists of an annular diffuser, a complex three-dimensional flame stabilizer, a liner with chute, screech and cooling rings holes and a convergent nozzle. The wall static pressures are compared with experimental data obtained from rig results for both core and bypass casing. The agreement between CFD prediction and experimental data are in close agreement. The ...
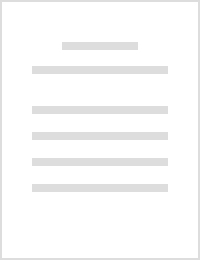
Military aero engines employ afterburner system for increasing the reheat thrust required during ... more Military aero engines employ afterburner system for increasing the reheat thrust required during combat and takeoff. During reheat the gas temperature in the afterburner is of the order of 2100K.The afterburner liner has to be cooled with the available bypass air to maintain metal temperature within allowable limits. The liner has cooling rings at the rear to cool the liner with tangential film cooling.This paper discusses the methodology of afterburner liner metal temperature prediction and comparison with measured metal temperature during aero engine testing at reheat condition. All the modes of heat transfer are considered for thermal analysis, radiation due to higher level of gas temperature during reheat, conduction due to presence of low conductivity thermal barrier coating and convection due to higher gas velocities are considered.At different steady state reheat conditions metal temperature are predicted and compared with measured data during aero engine testing. The predicted skin temperatures and measured temperatures are in good agreement. Empirical correlations are used for estimating the heat loads coming on the liner and adiabatic film temperature near screech holes and cooling rings. Metal temperature and thermal loads coming onto the liner are predicted with 1D code. The estimated thermal loads are applied on 3D FE model to obtain nodal temperature distribution. The thermal Analysis is carried using ANSYS software in which thermal barrier coating is also modeled.The parameters like gas temperature, thermal barrier coating thickness, coating conductivity, and coolant mass flow distribution are considered for carrying out a sensitivity analysis of liner metal temperature.Copyright © 2013 by ASME
The performance requirements of a gas turbine combustor are conflicting and non-linearly related ... more The performance requirements of a gas turbine combustor are conflicting and non-linearly related and hence, its design and development is a challenging task. Combustors of the earlier years were designed using a number of empirical relations supported by experiments. The designs, thus obtained were optimized by experimentally testing several variants of the combustor which were costly and time-consuming. Of late, Computational Fluid Dynamics (CFD) codes have become comprehensive, reliable and are being routinely used in the design and development of gas turbine combustors. In this paper, such efforts of several researchers utilizing CFD, in all stages of design and development viz., preliminary sizing to performance optimization, have been elucidated.
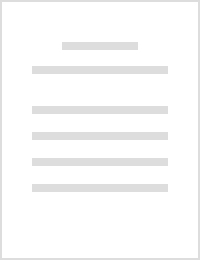
International Journal of Turbo & Jet-Engines, 2015
Effect of fuel spray cone angle in an aerogas turbine combustor has been studied using computatio... more Effect of fuel spray cone angle in an aerogas turbine combustor has been studied using computational fluid dynamics (CFD) and full-scale combustor testing. For CFD analysis, a 22.5° sector of an annular combustor is modeled and the governing equations are solved using the eddy dissipation combustion model in ANSYS CFX computational package. The analysis has been carried out at 125 kPa and 303 K inlet conditions for spray cone angles from 60° to 140°. The lean blowout limits are established by studying the behavior of combustion zone during transient engine operation from an initial steady-state condition. The computational study has been followed by testing the practical full-scale annular combustor in an aerothermal test facility. The experimental result is in a good agreement with the computational predictions. The lean blowout fuel–air ratio increases as the spray cone angle is decreased at constant operating pressure and temperature. At higher spray cone angle, the flame and hig...
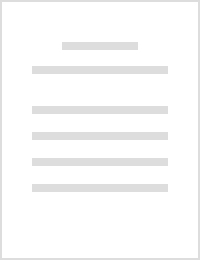
ASME 2014 Gas Turbine India Conference, 2014
Machines and beam like structures used in various industries require continuous monitoring for th... more Machines and beam like structures used in various industries require continuous monitoring for the fault identification for ensuring uninterrupted service. Different non-destructive techniques (NDT) are generally used for this purpose, but they are costly and time consuming. Vibration based methods can be useful to detect cracks in structures using various artificial intelligence (AI) techniques. The modal parameters from the dynamic response of the structure are used for the purpose. In the current analysis, the vibration characteristics of a glass fiber reinforced composite cracked cantilever beam having different crack locations and depths have been studied. Numerical and finite element methods have been used to extract the diagnostic indices (natural frequencies, mode shapes) from cracked and intact beam structure. An intelligent Genetic Algorithm (GA) based controller has been designed to automate the fault identification and location process. Single point crossover and in some...
International Journal of Turbo & Jet-Engines, 2014
Lean blow out characteristics in a swirl stabilized aero gas turbine combustor have been studied ... more Lean blow out characteristics in a swirl stabilized aero gas turbine combustor have been studied using computational fluid dynamics. For CFD analysis, a 22.5° sector of an annular combustor is modeled using unstructured tetrahedral meshes comprising 1.2 × 10
International Journal of Turbo & Jet-Engines, 2014
Combustion stability is examined in a swirl stabilized aero gas turbine combustor using computati... more Combustion stability is examined in a swirl stabilized aero gas turbine combustor using computational fluid dynamics. A 22.5° sector of an annular combustor is modeled for the study. Unstructured tetrahedral meshes comprising 1.2 × 10
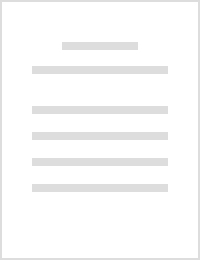
ASME 2012 Gas Turbine India Conference, 2012
ABSTRACT A parametric study is carried out for aerodynamic performance of turbines including geom... more ABSTRACT A parametric study is carried out for aerodynamic performance of turbines including geometrical requirements, thermal requirements, mechanical integrity and manufacturing requirements. Life cycle costs, product cycle time and weight are additional, possible criteria during the parametric study. Preliminary design plays an important role in reaching the final design of the turbine. Preliminary design steps calculate the mean dimensions of the machine. The main step in the aerodynamic design which is instrumental in providing desired performance is blade element profile generation. During the profile generation, in addition to aerodynamic performance, additional constraints for castability, structural requirements and thermal requirements need to be considered. Thus profile generation is a trade-off between contradicting requirements of aerodynamic performance, structural and thermal performance. Copyright © 2012 by ASME
ASME 2012 Gas Turbine India Conference, 2012
ABSTRACT Performance of intake duct with fixed inlet trajectory and different area distributions ... more ABSTRACT Performance of intake duct with fixed inlet trajectory and different area distributions have been analyzed using a commercial CFD (Computational Fluid Dynamics) software. The performance have been evaluated for fixed boundary conditions. The area distributions studied are defined by varying cross sectional area at different locations of intake duct by keeping the inlet and exit area same. The performance of the intake ducts are studied in terms of the pressure recovery coefficient, total pressure loss, pressure recovery factor and distortion coefficient in the present work. The motion caused by the change in centerline curvature is analyzed. The objective of the work is to derive a shape of the duct with minimum distortion of the flow and maximum pressure recovery. Copyright © 2012 by ASME .
Journal of Propulsion and Power, 1998

Journal of Aircraft, 1998
Conceptual design has critical leverage on the entire course of design process since it addresses... more Conceptual design has critical leverage on the entire course of design process since it addresses the issue of selecting the baseline design to optimally accomplish the specified set of requirements. Conceptual design software has been developed to determine the optimal engineairframe match over a given mission role, its multi-mission capabilities, and the size and weight of optimum engine cycle. Its capabilities are demonstrated over three combat mission applications. The results are presented to indicate the optimum designs over these missions, interaction effects of a few design variables and the future course of developments in propulsion system technology. The results also include a preliminary estimate of the impact of thrust vectored take off and landing and a variable capacity low pressure turbine on engine cycle selection and overall aircraft sizing. afterburner exit temperature W EMP empty weight W ENG,DP engine design point mass flow W F,msn fuel consumed over design mission W TO aircraft take off gross weight
International Journal for Numerical Methods in Fluids, 1988
Bulletin of Mathematical Biology, 1990
Uploads
Papers by S Kishore Kumar